Packaging plays a crucial role in product storage, transportation and delivery. It is an important step towards ensuring the safety and quality of products as they make their way through the supply chain. Packaging also gives your product a personality – the face of your product speaks to the customer, even before they have interacted with it.
Therefore, a well-thought-out packaging strategy is essential to the success of a product. Product packaging starts with understanding the three different levels of packaging – Primary Packaging, Secondary Packaging, and Tertiary Packaging.
Each level has its own unique set of functions, significance, and array of types. This article will delve into the intricacies of these three levels of packaging solutions, exploring their various types and importance in the product supply chain. We will also compare the three types of packaging and shed light on key factors that influence the selection of suitable packaging type for a product.
But first, let’s understand why the different levels of packaging are important.
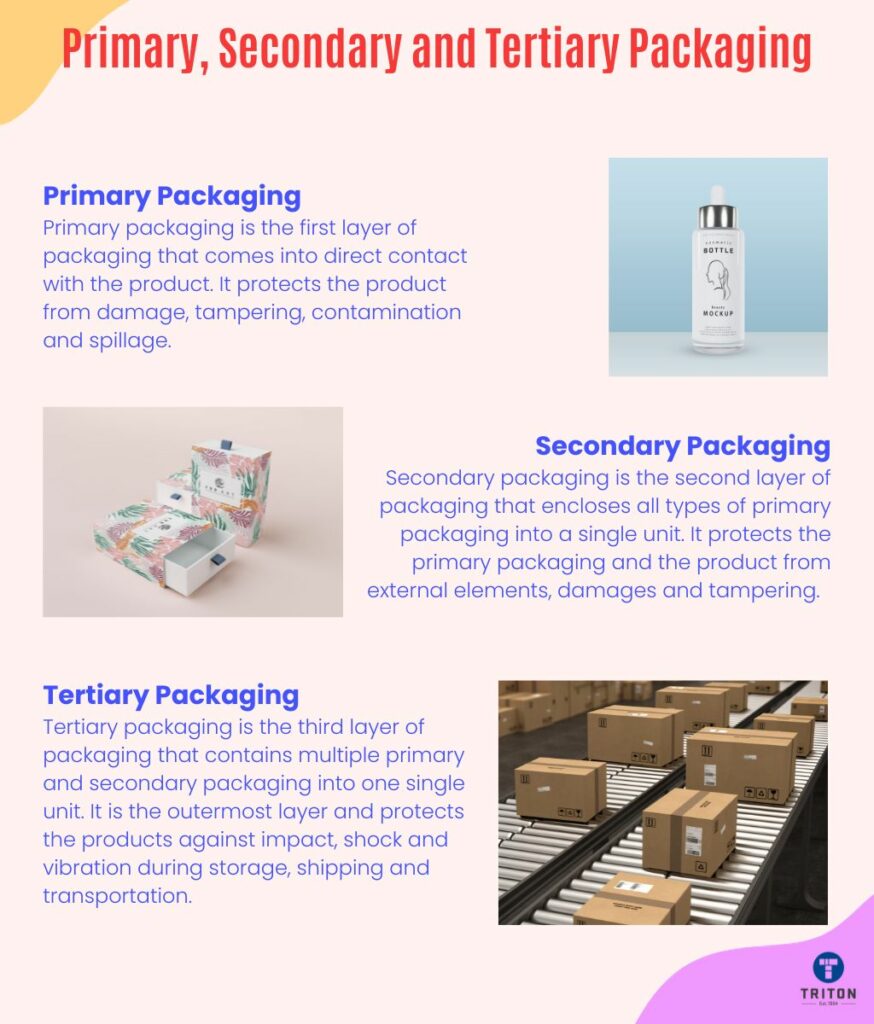
Why are Different Levels of Packaging Important?
The different levels of packaging are essential for various reasons.
Primarily, it provides maximum safety and protection to products during transit from the point of manufacture till it reaches its customer. It also reduces the risk of damages due to the handling and movement of products between locations.
Apart from the safety reasons, here is why the three levels of packaging are important for a product.
Compliance
Packaging is highly regulated, and various laws and regulations are implemented worldwide. Countries and industries have different requirements regarding packaging materials, sizes, labelling and product information. The three levels of packaging ensure that these regulations and standards are met with ease.
For example, the Food Standards Australia New Zealand (FSANZ) mandates that food package labelling should list food allergens if used as an ingredient, additive, or processing aid, even if the amount is minuscule. Our guide on understanding allergen labelling compliance will help you navigate the complexity of this regulation. Bartender Software will also assist in developing labels for your packaging that assist in meeting compliance requirements.
Branding & Promotion
Packaging is a great way to communicate your product’s identity and values. It is the first thing that customers interact with and is an effective way to attract attention to your product.
Packaging is also used as a powerful marketing tool to differentiate the product from competitors. For instance, FMCG (Fast-Moving Consumer Goods products) brands can create hype around their products by having attractive packaging or limited edition ones during special occasions like Christmas or Chinese New Year.
The three levels of packaging provide ample scope and opportunities to showcase the unique features of your product, strengthen its identity, and communicate its values to customers.
Cost Savings
The three levels of packaging also provide economic benefits.
Secondary and tertiary packaging, in particular, helps to bundle multiple units into one bigger unit, which makes it more economical to transport them in bulk rather than individually. This reduces the overall shipping costs and ensures that products reach their destination securely, allowing businesses to increase their profits.
Ease of Handling
Lastly, the three levels of packaging make it easy to handle and manoeuvre different types of products.
For instance, secondary packaging such as boxes or cartons makes it easier to move multiple items at once without picking them up separately. It also helps with inventory management by allowing for better organisation and tracking of products during transit.
Now that we have understood why the different levels of packaging are important let’s explore each one in more detail.
What is Primary Packaging? - The First Line of Contact
The primary packaging is the first layer of packaging that encloses the product. This type of packaging comes into direct contact with the product and is designed to protect it from damage, tampering, contamination and spillage. It serves as a barrier against external elements such as moisture, light, and dust and helps ensure that products remain sterile until they are opened for consumption.
The most common types of primary packaging materials are.
- Plastic
- Metal
- Glass
- Paper
- Cardboard
Some examples of primary packaging are plastic bottles, cans, jars, boxes, blister packs, clamshells, pouches and sachets.
The primary packaging is also called retail packaging, as it is the packaging customers see when purchasing a product.
Types of Primary Packaging
The primary packaging can be further classified into three types.
- Flexible Primary Packaging
- Rigid Primary Packaging
- Semi-Rigid Primary Packaging
Flexible Packaging
Flexible packaging is a type of primary packaging that can easily mould around a material or change shape when filled with a product. This type of packaging is often made from materials like paper, plastic (cellophane), aluminium foil, or a combination of these. Primary packaging allows manufacturers to add resealable closures or handles to make them more convenient for consumers.
Flexible packaging is a popular choice in the food and beverage industry and personal care products due to its lightweight, ease of storage, and excellent barrier properties, capable of protecting contents from moisture and gases.
Some examples of flexible packaging include bags, pouches, shrink films, and sachets.
Rigid Packaging
Rigid packaging, as the same suggests, is a packaging type that maintains its shape regardless of the content inside. This type of packaging is usually made from materials such as glass, metal, and hard plastic and is often used to contain liquids, powders, and solids.
Manufacturers prefer rigid packaging for its excellent protection against impacts, leakage and tampering. It is often used in beverage, medical, pharmaceutical and electronics industries.
Some examples of rigid packaging include aerosol cans, bottles, jars, boxes, cases and trays.
Semi-Rigid Packaging
Semi-rigid packaging is a combination of both rigid and flexible packaging. This type of packaging has the flexibility to change shapes but maintains its structure. It is usually made from foam, cardboard, paperboard or fibreboard and has a flexible portion that can be pressed to adapt the product’s shape.
Semi-rigid packaging is often used for products like eggs and alcohol bottles that require extra protection from impacts and the ability to absorb shock and vibration during transportation.
Why is Primary Packaging Important?
Primary packaging is important for the following reasons.
#1 Product Safety
The primary packaging is the first line of defence for a product. It is responsible for protecting the contents from tampering, damage, contamination & spoilage from external elements such as dirt, dust, moisture, light and temperature.
The primary packaging plays an important role in ensuring that the product remains in perfect condition until it reaches the customer. A defective primary packaging can lead to product spoilage and damage, resulting in loss of product and product recalls.
#2 Product Branding & Promotion
The primary packaging is the first thing customers interact with when it comes to a product. Therefore, it is an effective way to attract attention and communicate the product and the brand’s identity and values.
The primary packaging should use unique designs and attractive colours to showcase product features and create a memorable first impression. This helps to increase brand awareness and trust, differentiate from competitors, and promote sales.
#3 Share Information
The primary packaging contains essential information about the product, such as ingredients used, potential allergens, instructions for use, nutrition labels, expiration and manufacturing dates, safety warnings and barcodes.
This information helps to ensure that customers know what they are buying and allows them to determine if it suits their needs. It also allows manufacturers to comply with legal requirements that most countries have regarding product labelling.
What is Secondary Packaging? - Grouping and Protection
The secondary packaging is the second layer of packaging that encases the primary packaging. It is used to contain and protect multiple products packed together in a single unit. Like primary packaging, secondary packaging also helps to safeguard the product from damage, contamination and tampering and assists with product identification and inventory management.
The most common types of secondary packaging materials are.
- Bubble wraps
- Plastic
- Corrugated cardboard
- Corrugated fibreboards
- Foam
Some examples of secondary packaging are cartons, plastic containers, shrink-wrapped bundles of primary packaging, paperboard trays and bags.
The retail packaging industry and a local grocery store often use primary or secondary packaging to showcase and distribute individual units to consumers.
Types of Secondary Packaging
The secondary packaging can be further classified into four types.
- Reinforcement and Interior padding
- Wrapping
- Boxes
- Container
Reinforcement and Interior Padding
Reinforcement and interior padding are secondary packaging that provides extra protection for fragile primary packages like glass and bottles. This type of packaging is usually made from materials such as bubble wrap, polystyrene foam, paperboard, air cushions and corrugated fibreboard.
The reinforcement and interior padding are used to fill any gaps between the products in order to reduce movement within the package. It also helps to protect the product from shocks, vibrations, abrasion or pressure during transportation & handling.
Wrapping
Wrapping consists of stretch wrap and shrink wrap. This type of packaging is used to secure multiple products into one unit and to protect them during transportation.
Stretch wrapping uses elastic tensioning material such as plastic film or banding materials, whereas shrink wrapping uses heat-shrinkable plastics. Apart from stretch and shrink wraps, paper, fabric, and metal foil are also used for wrapping products.
Wrapping is commonly used in the food and beverage industry to bundle multiple items like cans, bottles and jars together for convenience and cost savings.
Boxes
Boxes are secondary packaging primarily used to enclose one or more products into a single unit. They are usually made from corrugated cardboard or paperboard and have flaps and closures for easy opening & closure. Boxes can be customised to fit the exact size and dimensions of the product.
Boxes provide superior protection for the products compared to wrapping materials as they absorb more shocks, vibrations and impacts. They also come with additional features such as dividers and partitions to provide separate spaces for storing different product accessories.
Boxes are often used in the retail industry to transport products from warehouses to stores and as a means for customers to carry their purchases home. They are also common for products that need extra protection from impacts and shocks, such as glassware and electronics.
Containers
Containers are large secondary packaging used to transport and store products. These containers are usually made from plastics, metals or wood and can come in various sizes and shapes, such as drums, bags, barrels, boxes and buckets.
Containers are a popular choice for bulk shipments of goods that require further processing or storage at the destination point. They provide extra product protection against impact, shock, moisture, temperature fluctuations and other external elements.
Containers are commonly used to store hazardous materials, food & beverages, chemicals and industrial raw materials.
Why is Secondary Packaging Important?
Secondary packaging is essential for several reasons, such as.
#1 Protection & Quality Preservation
The secondary packaging helps to protect products from external elements, damages, contamination and tampering during storage, transportation & handling. This ensures that products remain in perfect condition until they reach their destination.
#2 Facilitating Transportation & Storage
The secondary packaging is mostly designed in such a way that it can be stacked on top of each other without damaging the product. This helps conserve storage space and facilitates easy and cost-effective transportation.
#3 Brand Awareness & Promotion
The secondary packaging serves as an additional layer for branding the product. Brands can use this space to provide information about their products and services, which helps to create brand awareness and promote sales.
What is Tertiary Packaging? - Bulk Handling and Transport
The tertiary packaging, also called bulk packaging or transit packaging, is the third layer of packaging that secures multiple primary and secondary packaging or groups of products into one single unit. It serves as an outermost protective layer and is used when products need to be transported in larger quantities and distances.
Some examples of tertiary packaging are.
- Wooden crates
- Pallets
- Slip sheets
- Plastic Collapsible Containers (PCCs)
- Shipping container
Tertiary packaging is made from very strong materials such as wood, hard plastic, and metals like aluminium and steel as they need to withstand severe impacts and store large volumes of products.
Types of Tertiary Packaging
Tertiary packaging can be divided into four categories.
- Large containers
- Pallets
- Crates
- Gaylord boxes
Large Containers
Large containers are huge boxes made from metals or wood used to store and transport large volumes of products. Examples of large containers are shipping containers, tanks and boxes. These types of packaging are mostly used when transporting goods overseas and in the automotive industry.
Pallets
Pallets are flat transport structures designed to store and move products with the help of forklifts, pallet jacks or automated conveyor systems. They are usually made from a mixture of hardwoods (oak) and softwoods (southern yellow pine).
Pallets are mostly used in supermarkets, warehouses and factories for stocking up large quantities of goods.
Crates
Crates are rigid boxes or cases that come with a lid or a cover. These are made from wood, plastic or metal and usually have a handle at the top or side for easy carrying. Crates come in different sizes and shapes and are easily stackable on top of each other.
Crates have stronger walls compared to boxes and are mostly used to transport fragile items like glassware, artwork and sensitive electronic components.
Gaylord Boxes
Gaylord boxes, also known as bulk boxes, are large corrugated cardboard or fiberboard containers with a flat bottom and an open top. These boxes come with lids that can be sealed shut to secure the contents.
The word ‘Gaylord’ is derived from the name of a company, Gaylord Container Corporation, that originally manufactured these boxes.
Gaylord boxes are generally used for storing, moving and shipping hazardous chemicals, hazardous waste, industrial products and dangerous goods. The use of Gaylord boxes is highly regulated in some countries.
Why is Tertiary Packaging Important?
Tertiary packaging is important for the following reasons.
#1 Protection
The tertiary packaging provides additional protection to products against impact, shock and vibration during storage, shipping and transportation. It also helps to keep the products safe from tampering or pilferage.
In short, tertiary packaging ensures the product remains in perfect condition until it reaches its final destination.
#2 Easy Handling & Storage
The tertiary packaging helps consolidate multiple packages into one unit, making it easier to handle and store. Similar to secondary packaging, tertiary packages are also designed to be stalked on top of each other. This helps to save storage space and make the handling process more efficient.
The use of tertiary packaging also significantly reduces manual labour involved in handling large volumes of products as it can be moved easily using forklifts, pallet jacks or automated conveyor systems.
#3 Cost-effective Bulk Shipping
The tertiary packaging allows large quantities of goods to be transported in bulk, which is more cost-effective and time-saving. This is because shipping large volumes of goods at once reduces cost per unit and helps to reduce overhead costs associated with transportation & handling.
Primary Packaging vs Secondary Packaging vs Tertiary Packaging - What's the Difference?
Here is a table that illustrates the difference between primary, secondary and tertiary packaging.
Packaging Level | Description | Example |
---|---|---|
Primary Packaging
| The first layer of defence;
In direct contact with the product;
Opened by consumers only;
Provides protection against external environmental elements;
Also called retail packaging
| Soda cans,
Bag of chips,
Milk cartoons,
Jam jars
|
Secondary Packaging
| The second layer of defence;
In direct contact with the primary packaging;
Can be opened by consumers and sellers both;
Protects against damages, contamination and tempering
| Cardboard box,
Shrink-wrapped PET bottles,
Paperboard trays,
Big jute bags
|
Tertiary Packaging
| The third layer of defence;
In direct contact with the secondary packaging;
Opened by sellers only;
Provides protection against impact, shock and vibration during handling, shipping, transportation and storage of products;
Aids in easy and safe transportation/shipping;
Also called bulk packaging or transit packaging
| Wood crates,
Pallets,
Shipping containers,
Drums
|
Factors to Consider When Choosing Packaging for Product
From a business perspective, each level of packaging plays a pivotal role in ensuring the product reaches the consumer in optimal condition. Therefore, it’s important to identify the right kind of packaging that meets the needs of the product and its intended purpose.
Here are some essential factors to consider when determining the correct type of packaging for a product.
#1 Product Nature & Properties
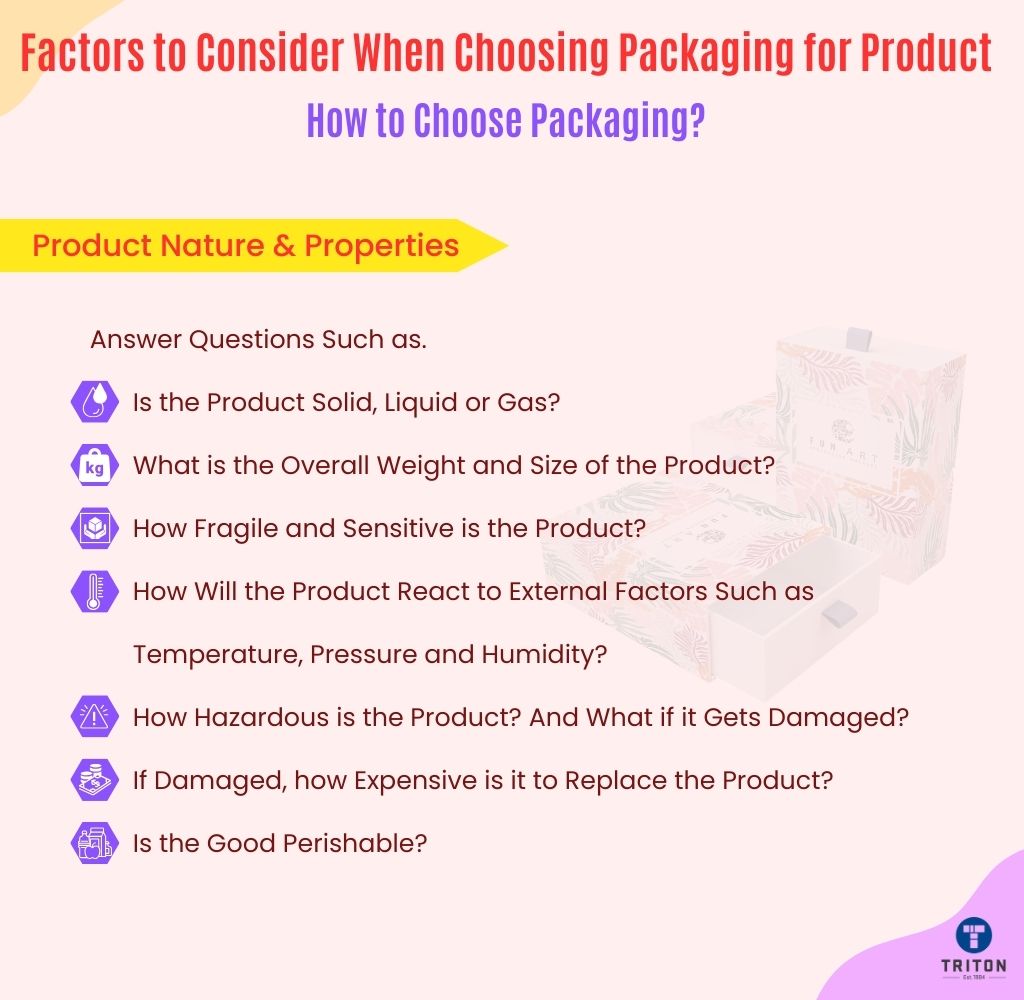
The first and foremost thing to consider when selecting packaging for a product is its nature and properties. This includes asking questions such as.
- Is the product solid, liquid or gas?
- What is the overall weight and size of the product?
- How fragile and sensitive is the product?
- How will the product react to external factors such as temperature, pressure and humidity?
- How hazardous is the product? And what if it gets damaged?
- If damaged, how expensive is it to replace the product?
- Is the good perishable?
Answering these questions will help to determine the primary, secondary or tertiary packaging that is best suited and can provide adequate protection to your products.
For example, for fragile products like glassware, it would be wise to opt for semi-rigid primary packaging along with cushioning materials such as foam, bubble wrap or air pillows as secondary packaging to add extra cushioning protection.
#2 Product Quantity
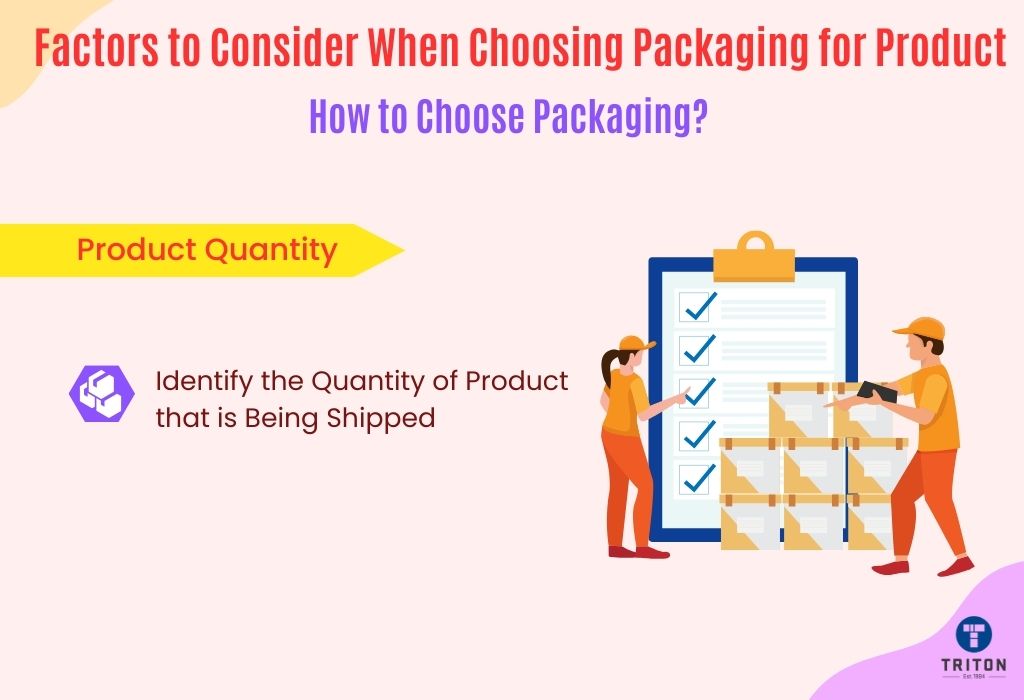
The quantity of product plays a crucial role when it comes to selecting the right packaging type.
For example, if your products are in large quantities or ordered in bulk orders, then it would be wise to opt for tertiary packaging such as pallets or Gaylord boxes, which can help to move more goods at once and save costs on transportation and handling.
On the other hand, if you want to ship a small number of goods, then secondary packaging like cardboard boxes, shrink-wraps or bags would be more efficient and cost-effective.
#3 Shipping and Logistics Considerations
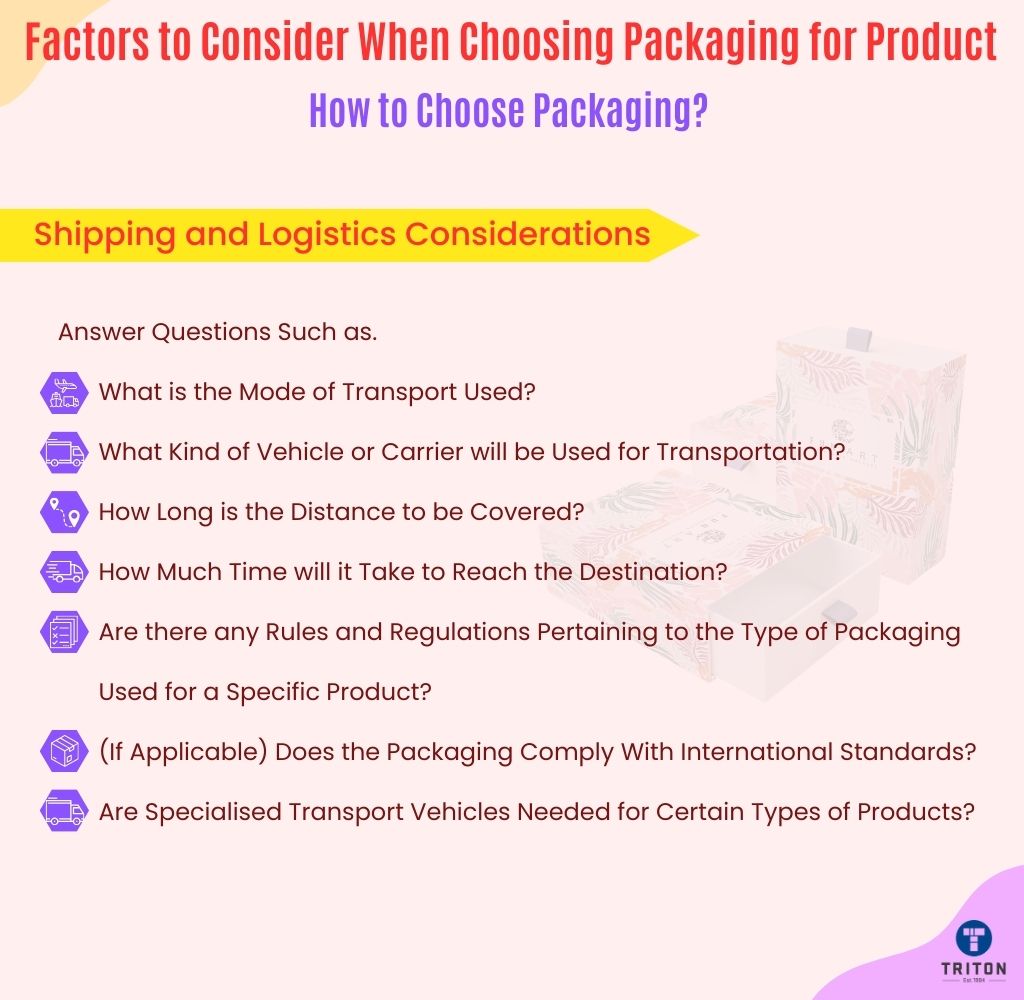
When selecting a type of packaging, it’s important to consider shipping and logistics requirements. This includes factors such as.
- The mode of transport, i.e. road, sea or air transportation
- What kind of vehicle or carrier will be used for transportation?
- How long is the distance to be covered?
- How much time will it take to reach the destination?
- Are there any rules and regulations pertaining to the type of packaging used for a specific product? And (if applicable) does the packaging comply with international standards?
- Are specialised transport vehicles needed for certain types of products?
Answering these questions will help to determine the type of packaging that can provide optimal protection to your products during transportation and keep them undamaged until they reach the final destination.
#3 Storage, Distribution and Supply Chain Needs
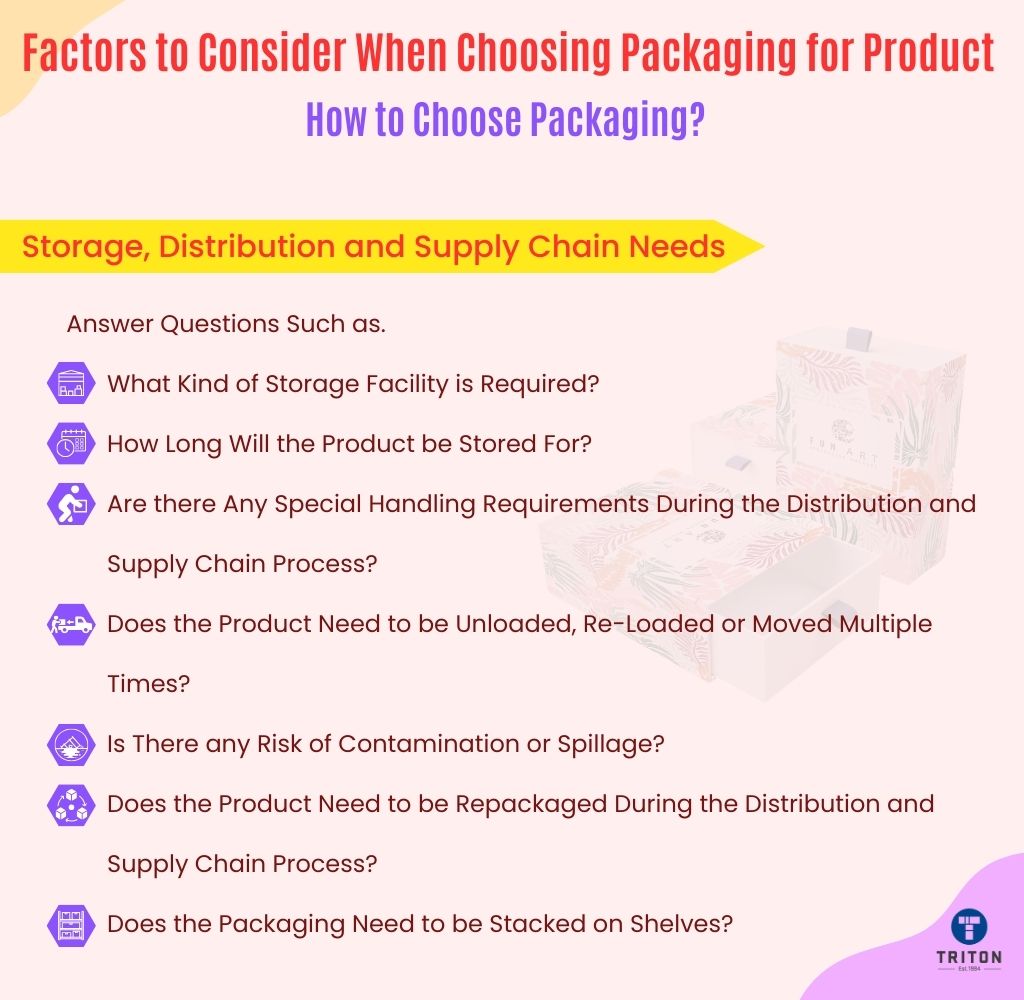
Apart from shipping and logistics, the storage, distribution process, overall supply chain strategy and the end user also dictate the type of packaging used.
Questions to consider in this regard are.
- What kind of storage facility is required?
- How long will the product be stored for?
- Are there any special handling requirements during the distribution and supply chain process?
- Does the product need to be unloaded, re-loaded or moved multiple times?
- Is there any risk of contamination or spillage?
- Does the product need to be repackaged during the distribution and supply chain process?
- Does the packaging need to be stacked on shelves?
For instance, if the product needs to be stored in a cold-storage facility, then using packaging materials with insulation properties would be optimal to maintain the temperature of the product. Similarly, if there is a risk of contamination or spoilage during transportation, opting for leak-proof and tamper-proof packaging would help reduce such risks.
Answering these questions will help to identify the type of packaging that best meets the packaging needs of a product and its supply chain.
#4 Hazards & Risks
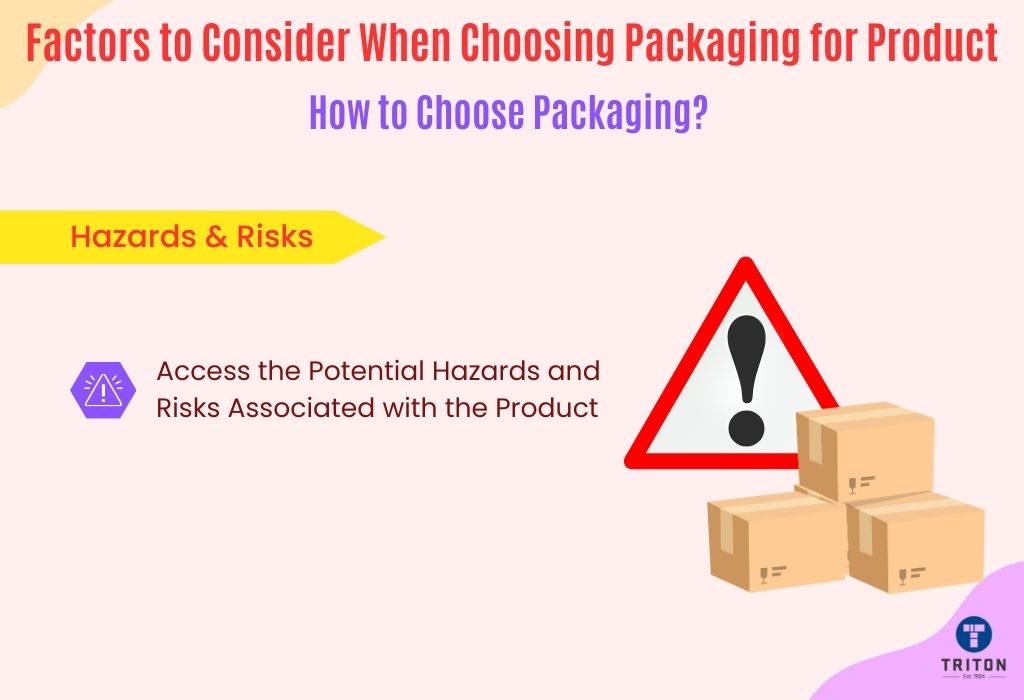
It’s important to assess the potential hazards and risks associated with the product to determine the type of packaging that can provide adequate protection.
For instance, if the product is hazardous or flammable, extra care must be taken to ensure it is appropriately packed in air-tight and fire-resistant packaging. Similarly, if the product contains sharp edges or corners, it would be wise to use cushioning materials such as foam or bubble wrap around the product to reduce the risk of injury and ensure safe handling.
Moreover, if you need to ship hazardous materials and dangerous goods like chemicals and explosives, then it’s important to abide by the regulations set out by various local and international government authorities.
Particularly for hazardous chemicals, the United Nations developed the Globally Harmonized System of Classification and Labelling of Chemicals (GHS). If you deal with hazardous chemicals, it is important to understand the GHS requirements and comply with them when packaging and transporting such products. The following articles will help you to comply with GHS regulations.
#5 Cost & Budget
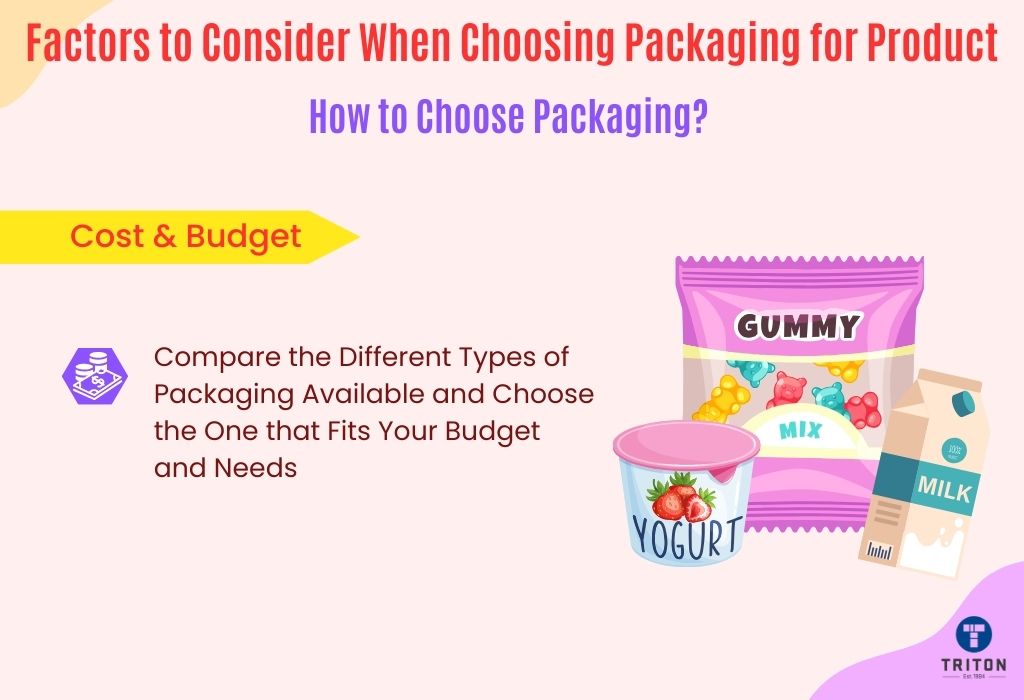
The cost of packaging is another important factor to consider when selecting the right type of product packaging. Different types of packaging come with different price points depending on the material used, size and shape.
It’s wise to make a thorough comparison between available options and analyse and weigh the benefits and drawbacks of using a particular type. This way, you can make an informed decision and select the type of packaging that offers optimal product protection without compromising on budget constraints.
#6 Environmental Considerations and Sustainability
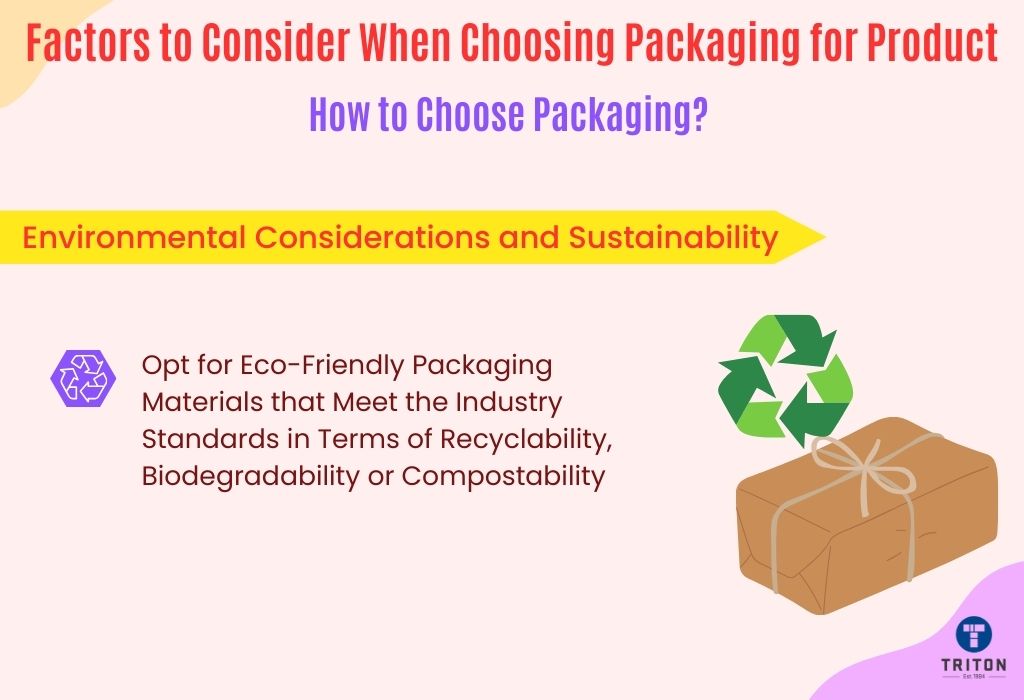
Sustainability is not an option but a necessity today. Therefore, it’s important to consider the environmental impact of packaging when selecting it.
It’s essential to opt for eco-friendly packaging materials like paper pulp, bioplastics, jute bags and cardboard that meet the industry standards in terms of recyclability, biodegradability or compostability. If possible, avoid using non-biodegradable materials like plastics, polythene and styrofoam, as these have a negative environmental impact.
The Takeaway
Packaging may seem like a small aspect of the overall product life cycle; however, it plays a crucial role in the product distribution and supply chain process. Understanding the differences between primary, secondary, and tertiary packaging can guide you in choosing the most effective and efficient packaging solution for your products.
As we’ve discussed, numerous factors should be considered when selecting the most efficient packaging type for products. These include the product’s characteristics & quantity, shipping & logistics needs, storage requirements, distribution needs, potential hazards and risks, and the cost associated with the packaging itself.
Importantly, the choice of packaging should address functional requirements and align with your commitment to sustainability, reflecting your brand’s responsibility towards our environment.
We hope this article was useful.
Thanks for reading!