Store Location
Choose Your Store
You are currently in the Australian store. If you are located in New Zealand please select the correct store below.
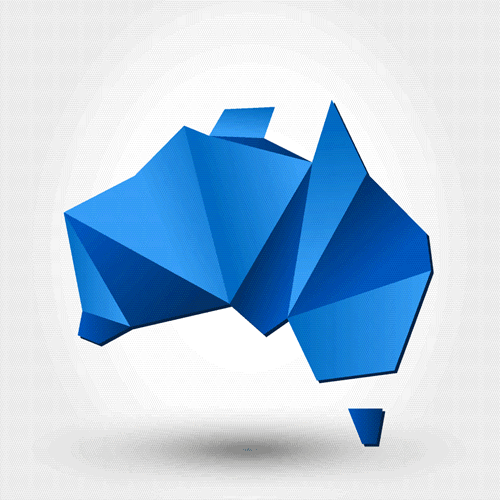
You are currently in the Australian store. If you are located in New Zealand please select the correct store below.
Label rewinders and unwinders are practical devices used to manage label rolls during printing processes. Unwinders supply blank labels into printers, maintaining consistent tension, while rewinders collect printed labels for storage or application.
These tools help streamline label handling by reducing manual effort and improving accuracy in high-volume operations. Commonly used in industries such as manufacturing, logistics, and retail, rewinders and unwinders support efficient workflows and consistent label quality.
By automating roll handling, they help minimise waste and maintain steady production, making them a useful addition to environments requiring precise label management.
Label rewinders are devices designed to automatically wind printed labels onto a roll as they exit a printer. This automation ensures that labels are neatly collected, facilitating easier handling, storage, and subsequent application.
By maintaining consistent tension and alignment, label rewinders help prevent issues such as misalignment or damage, therefore enhancing the efficiency and quality of the labelling process.
Label unwinders are designed to efficiently feed large rolls of blank labels into printers, ensuring a consistent and smooth supply during the printing process. They prevent issues such as misfeeds or jams by maintaining proper tension and alignment.
Utilising an external unwinder allows businesses to use larger label rolls than those typically accepted inside the printer, thereby reducing the cost per label and saving time by minimising roll changes.
A label unwinder is particularly helpful in high-volume production, improving workflow efficiency and reducing manual intervention.
Label rewinders and unwinders offer features required for efficient label handling and seamless integration with printing systems.
control ensures smooth and consistent label feeding or rewinding by maintaining optimal tension thTension roughout the process. This feature prevents misalignment, tearing, or wrinkling of labels, resulting in high-quality output and reduced wastage, especially in high-spoperationseed.
Label rewinders and unwinders are designed to integrate seamlessly with a variety of printers and label applicators.
This compatibility ensures flexibility in different workflows, allowing businesses to adapt their equipment to diverse label printing and application needs.
These devices can accommodate a wide range of roll sizes, offering flexibility for various applications.
Whether handling small rolls for retail or large rolls for industrial use, their adjustable capacity supports efficient operations across different requirements.
Built with robust materials, label rewinders and unwinders are engineered for demanding industrial environments.
They can withstand prolonged use, heavy workloads, and exposure to challenging conditions, ensuring reliability and longevity in high-volume applications.
Adjustable core holders allow rewinders and unwinders to support various core diameters, offering versatility for different roll specifications.
This feature simplifies setup and ensures a secure fit, reducing downtime and improving operational efficiency.
Label alignment mechanisms ensure that labels are wound accurately onto rolls without misalignment or overlapping. This feature improves the quality of label rolls, making them easier to handle during application and reducing waste caused by unevenly wound labels.
Direction control allows users to select between clockwise and counterclockwise winding, offering flexibility for different printer setups and operational requirements.
This feature ensures compatibility with various label roll orientations and simplifies workflow adjustments.
Direction control allows users to select between clockwise and counterclockwise winding, offering flexibility for different printer setups and operational requirements.
This feature ensures compatibility with various label roll orientations and simplifies workflow adjustments.
Variable speed control ensures the rewinder operates in sync with the printer’s output speed. This feature prevents tension imbalances and ensures smooth, uninterrupted operation, regardless of the printer’s production rate.
A smooth feeding mechanism ensures a consistent supply of labels to the printer by maintaining steady tension and alignment. This prevents common issues like label misfeeds, wrinkles, or tearing, which can disrupt the printing process.
The mechanism ensures high print quality and reduces material waste, making it essential for uninterrupted operations.
Quick-loading systems allow users to replace label rolls efficiently, minimising downtime during high-volume production.
These systems often include intuitive designs, such as easy-access spindles or quick-lock mechanisms, making roll changes faster and hassle-free, ensuring continuity in demanding workflows.
Adjustable height features allow label unwinders to be positioned correctly with printers of varying sizes and configurations.
This flexibility ensures proper alignment between the unwinder and the printer reducing the risk of label misalignment and ensuring smooth feeding regardless of the printer model.
Some advanced label unwinders come equipped with sensors that detect the presence and position of labels. These sensors help maintain precise feeding by ensuring that labels are correctly aligned before entering the printer.
This feature reduces errors and improves overall efficiency, especially in automated or high-speed setups.
Motorised unwinders offer automated control over label tension and feed rate, making them ideal for high-speed printing environments. The motor ensures consistent feeding regardless of roll size or printer output speed, reducing manual intervention.
This advanced feature is particularly beneficial for industrial settings where precision and efficiency are critical.
Label rewinders and unwinders serve diverse industries by streamlining label management. This section highlights their key applications across manufacturing, logistics, retail, food, and pharmaceuticals.
Label rewinders and unwinders optimise manufacturing processes by enabling precise printing and organisation of product, component, and packaging labels. They simplify inventory management by producing and rewinding large batches of labels for easy storage and application.
Additionally, they assist in quality control by efficiently creating and organising batch labels and inspection tags, ensuring smooth workflows and consistent quality in production.
In logistics, label rewinders and unwinders improve efficiency by supporting bulk printing and rewinding of shipping labels for quick application. They streamline the production of barcode labels for tracking and inventory management, ensuring they are ready for immediate use.
These devices enable clear identification by producing and organising labels for pallet and bulk shipments, aiding in seamless supply chain operations.
Label rewinders and unwinders enhance retail and e-commerce operations by facilitating the bulk printing and organisation of price tags and product labels. They support the efficient production of promotional labels for sales and marketing updates.
Additionally, these devices streamline order fulfilment by enabling fast printing and application of labels for e-commerce packages, improving processing speed and accuracy.
In the food and beverage industry, label rewinders and unwinders ensure compliance and efficiency by enabling the printing of ingredient lists and nutritional labels. They streamline the production of expiration date labels for perishable goods, improving inventory management and ensuring safety.
For breweries, these devices simplify the organisation and application of labels for bottles and cans, supporting effective branding and product identification.
In the food and beverage industry, label rewinders and unwinders ensure compliance and efficiency by enabling the printing of ingredient lists and nutritional labels. They streamline the production of expiration date labels for perishable goods, improving inventory management and ensuring safety.
For breweries, these devices simplify the organisation and application of labels for bottles and cans, supporting effective branding and product identification.
Choosing the right label rewinder or unwinder requires careful consideration of your specific needs. Start by assessing label volume, sizes, materials, and your printer’s output speed to ensure compatibility.
Look for essential features like adjustable tension control, variable speed, bi-directional operation, core adapters, and label counters for efficient handling. Ensure the equipment aligns with your printer model, label materials, and available workspace.
Prioritise durability with robust construction, reliable motors, and a good warranty. When evaluating costs, factor in productivity gains, reduced waste, and long-term maintenance to balance upfront expenses with operational efficiency.
Regular maintenance ensures the longevity and efficiency of label rewinders and unwinders. Following a structured schedule and best practices can prevent breakdowns and optimise performance.
Develop a maintenance routine with daily, weekly, monthly, and annual tasks. This includes daily cleaning, weekly lubrication checks, monthly alignment adjustments, and annual inspections with part replacements. Maintain a detailed logbook for all activities to track performance and interventions.
Regularly clean the machine, focusing on areas like rollers and cutting sections, to remove dust, debris, and adhesive residue. Use non-abrasive solutions and lubricate moving parts like bearings and gears according to manufacturer recommendations. Address any signs of inadequate lubrication, such as unusual noises or resistance.
Regularly clean the machine, focusing on areas like rollers and cutting sections, to remove dust, debris, and adhesive residue. Use non-abrasive solutions and lubricate moving parts like bearings and gears according to manufacturer recommendations. Address any signs of inadequate lubrication, such as unusual noises or resistance.
Regularly inspect blades for sharpness and replace or sharpen them if worn, nicked, or chipped. Ensure proper blade holder alignment to maintain clean cuts and prevent label damage.
Every three months, inspect electrical wiring and connections for wear. Check bearings and belts monthly for tension and condition. Conduct vibration analyses to identify potential issues early and prevent equipment failure.
Keep sensors clean using compressed air before loading new media rolls. Check calibration regularly to ensure optimal performance and make adjustments as needed.
Perform periodic tests, such as roll structure and winding quality checks, to identify and address issues early. Pause tests can also help detect any underlying printing or rewinding inconsistencies.
In harsher environments, increase the frequency of cleaning and inspections. Maintain optimal temperature and humidity levels in the workspace to minimise environmental impact on performance.
Advancements in label rewinders and unwinders have introduced smart features like automation and feedback sensors, which adjust tension and speed for consistent label quality while reducing manual intervention.
Energy-efficient designs incorporate power-saving components, lowering operational costs and environmental impact. Noise reduction technology, including improved motor designs and sound-dampening materials, ensures quieter operation for noise-sensitive environments.
Additionally, manufacturers offer customisable options, allowing businesses to tailor equipment to specific needs, such as label sizes, materials, and production speeds, enhancing adaptability and efficiency in various applications.
Label rewinders and unwinders help in automating label handling, reducing waste, and maintaining consistent quality, making them essential across industries such as manufacturing, logistics, and healthcare. With advancements like smart sensors and energy-efficient designs, these devices now offer enhanced performance and adaptability.
To maximise their benefits, it is crucial to assess factors like label volume, material, and printer compatibility while prioritising features such as tension control and variable speed.
Regular maintenance ensures long-term reliability, and investing in equipment tailored to your needs can significantly streamline and optimise labelling operations.
Melbourne
Brisbane
Phone 1300 558 438
Live Chat – Widget below
Melbourne
Brisbane
Phone 1300 558 438
Live Chat – Widget below