Shrink sleeve label applicators put shrink sleeve labels on products or packaging. The market for these machines is set to hit $2.5 billion by 2030, growing at 6.5% each year.
For business owners, managers, and packaging pros, understanding these applicators is key. It helps you boost efficiency, keep product quality up, and stay ahead in the market.
This guide breaks down the main types of shrink-sleeve label applicators, giving you the info you need to make smart choices for your packaging process.
Let’s dive into each type to see what they offer and where they might fall short.
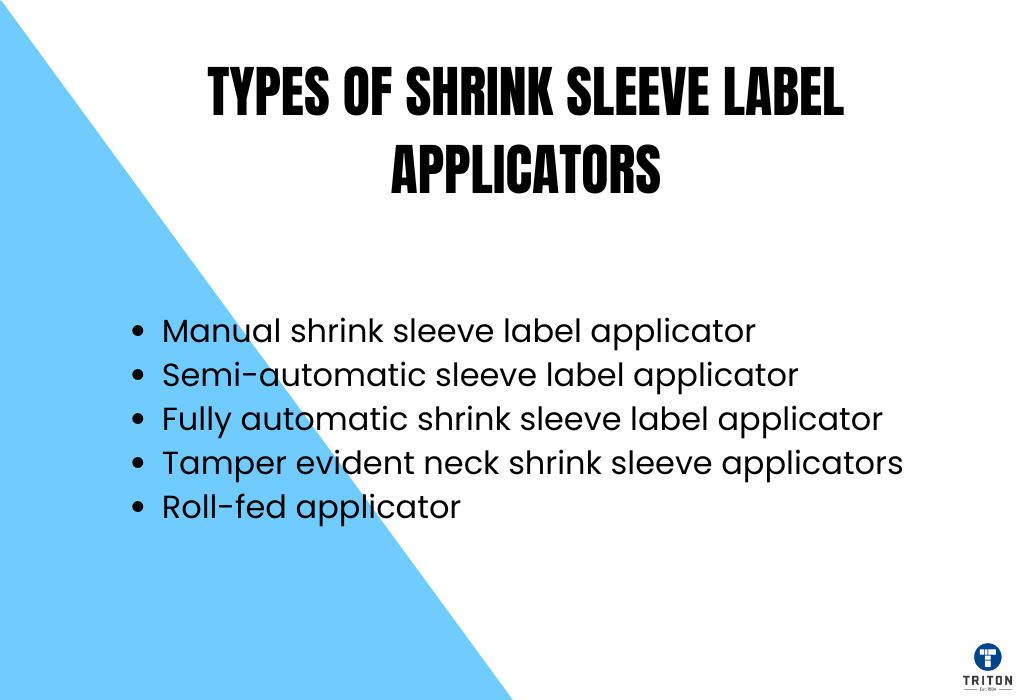
Manual Shrink Sleeve Label Applicators
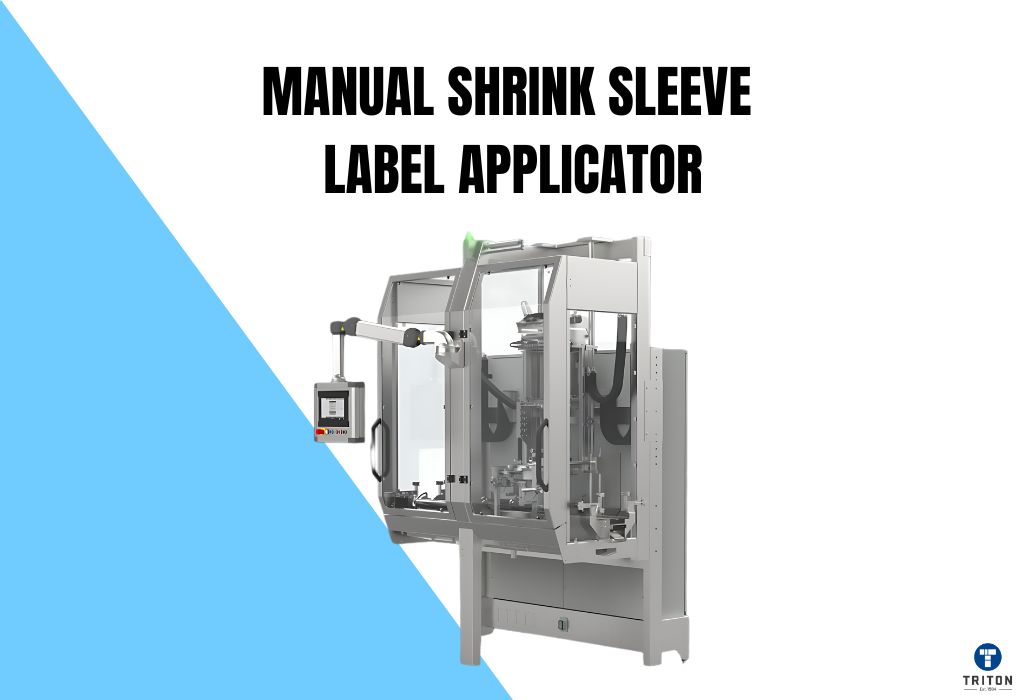
Manual shrink sleeve label applicators let operators apply shrink sleeves by hand. They can label up to 200 bottles an hour. The labelling speed depends on product shape, film thickness, and label length.
- These applicators use heat and tension to wrap the sleeve around the product to create a seamless finish.
- They come with safety features, including emergency stops and motion detectors.
These machines aren’t just basic tools; they’ve kept up with industry trends. One such trend is downgauging, which uses thinner films to save on materials and costs. This shift has led to a need for more precise cutting systems and better control.
Recent upgrades, like SMART human-machine interface (HMI) technology, have taken these applicators a step closer to Industry 4.0. HMI tech gives real-time data and insights into system performance.
Main Components
- Sleeve Dispenser: Holds sleeve roll, ensures smooth feeding.
- Sleeve Cutter: Cuts sleeve to size.
- Applicator Head: Positions sleeve onto the container.
- Heat Tool: Provides temporary shrinkage or wrinkle smoothing (heat gun, wand).
- Stand: Offers stability and ergonomic benefits (height adjustment, foot pedal).
How Does a Manual Shrink Sleeve Label Applicator Work?
- Setup
- The manual shrink sleeve label applicator is placed on a stable work surface.
- A roll of shrink sleeves is fed onto the sleeve feed mechanism.
- The label positioning system is adjusted to match the size and shape of the product.
- Feeding the Sleeve
- The Shrink sleeve is pulled from the roll and fed through the sleeve feed mechanism.
- Sleeve alignment and smooth movement of the roll are ensured.
- Cutting the Sleeve
- The shrink sleeve is cut to the required length with the cutting mechanism.
- Ensure the cut is clean and precise to avoid issues during the shrinking process.
- Positioning the Sleeve
- The product is placed on the label positioning system.
- The sleeve is slid onto the product.
- Shrinking the Sleeve
- A heat tunnel or heat gun is used to apply heat to the sleeve.
- The product is rotated if necessary to ensure even heat distribution and good shrinkage.
- The heat shrink process is monitored to avoid overheating and damaging the sleeve or product.
- Final Adjustment
- The shrunk label is inspected for quality control.
- If required, temperature and positioning adjustments are made.
Technical Specification of a Generic Manual Shrink Sleeve Label Applicator
Feature | Specification |
---|---|
Container Diameter Range | 1 – 5 inches |
Container Height Range | Up to 10 inches |
Labelling Speed | 100 – 200 containers per hour |
Training Requirement | Minimal |
Maintenance Requirement | Low |
Label Material | Heat-sensitive shrink sleeves |
Application Process | Manual application with a heat gun |
Heat Source | Heat gun or heat tunnel. |
Weight | 5 – 20 lbs |
Machine Dimensions | Approximately 12 x 10 x 8 inches (varies by model) |
Power Requirement | Standard electrical outlet |
Material Compatibility | Plastic, glass, metal containers |
Suitable for | Small businesses, start-ups, trial runs |
Operator Skill Level | Basic (minimal technical knowledge needed) |
Usage Environment | Indoor, dry, and clean conditions |
Label Alignment | Manual positioning for precision |
Semi-Automatic Shrink Sleeve Label Applicators
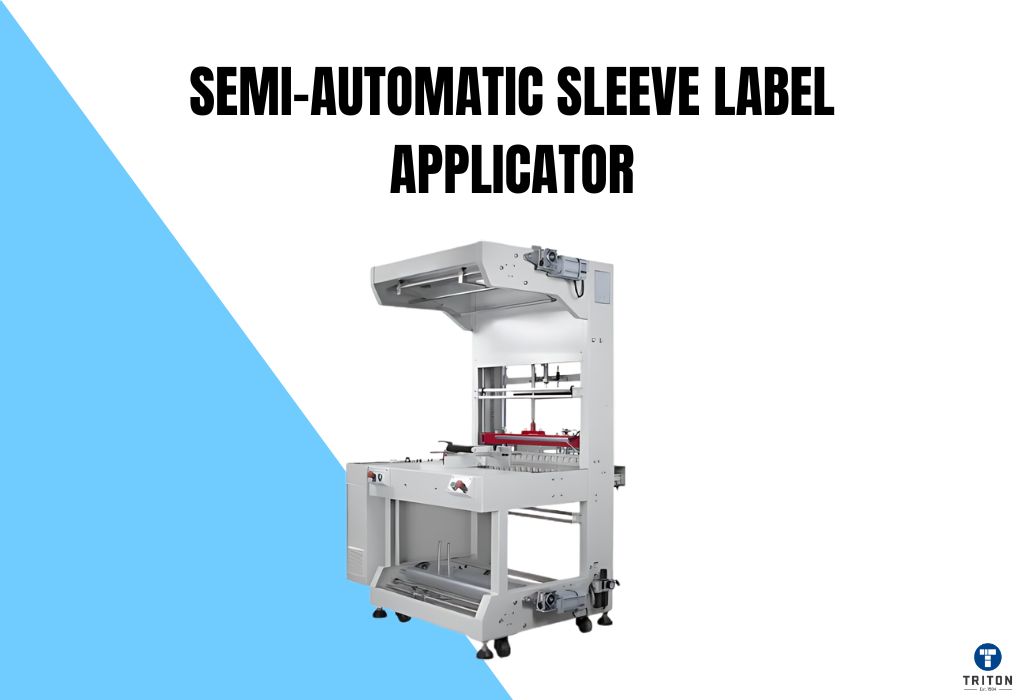
Semi-automatic shrink sleeve label applicators are designed for medium to high-volume production. These machines can label up to 1,000 bottles per hour. They use a mix of heat and tension to apply labels. Most semi-automatic shrink sleeve labellers have adjustable guides and rollers to maintain product alignment.
The latest models with PLC (Programmable Logic Controller) can do full-body sleeves and tamper-evident bands. Some models can label up to 400 containers per minute (24,000 containers per hour) and offer quick changeovers for different container shapes and sizes.
What is the Difference Between Semi-Automatic & Fully Automatic Label Applicators? Semi-automatic shrink sleeve label applicators need an operator to place containers on the conveyor and align sleeves. They’re suitable for medium-volume production and can be adjusted for different container sizes within 30 minutes to a few hours. Fully automatic applicators manage the entire process automatically. Their labelling speeds are higher and have better precision and finish. They are used in large-scale operations. |
Main Components
- Heavy-Duty Framework
- Constructed from robust materials for industrial environments.
- Engineered to support the weight and stress of continuous operation.
- Automated Sleeve Dispenser
- Includes a motorised system to feed shrink-sleeves automatically.
- Equipped with sensors to detect sleeve presence and ensure proper feeding.
- Programmable Cutter
- Utilises electronic controls to cut sleeves to precise lengths.
- Allows for different cut lengths to be set based on product dimensions.
- Precision Alignment System
- Automated alignment ensures the sleeve is perfectly positioned around the product.
- Uses advanced sensor technology to detect and adjust the position.
- Integrated Heat Source
- Typically, a heat tunnel or a series of heat guns that uniformly apply heat.
- Designed to provide consistent and controlled shrinking of the sleeve.
How Does a Semi-Automatic Shrink Sleeve Label Applicator Work?
- System Setup
- The shrink sleeve roll is loaded into the automated sleeve dispenser.
- The programmable cutter is configured for the required sleeve length.
- Feeding
- The automated sleeve dispenser is activated to begin feeding the shrink sleeves.
- Sensors ensure each sleeve is fed smoothly into the application area.
- Precision Cutting
- The programmable cutter automatically cuts the sleeves to the set length.
- Ensure that the cut sleeves are of consistent length for uniform application.
- Product Placement
- Products are manually fed into the alignment conveyor.
- The system adjusts the sleeve correctly with the product.
- Heat Application
- The product, now fitted with a sleeve, is conveyed through the integrated heat source.
- The heat source uniformly applies heat to shrink the sleeve around the product.
- Inspection and Adjustment
- Machine vision system inspects products
- If needed, adjustments are made to the process parameters
Technical Specifications of Generic Semi-Automatic Shrink Sleeve Label Applicators
Lorem ipsum dolor sit amet, consectetur adipiscing elit. Ut elit tellus, luctus nec ullamcorper mattis, pulvinar dapibus leo.
Feature | Specification |
---|---|
Container Diameter Range | 0.5 – 7 Inches |
Container Height Range | Up to 15 inches |
Speed of Manufacturing | Typically around 1000 Containers |
Training Requirement | Moderate |
Maintenance Requirement | Moderate |
Label Material | Heat-sensitive shrink sleeves
|
Application Process | Semi-automatic application with heat gun or heat tunnel |
Heat Source | Integrated heat tunnel or heat gun
|
Suitable for | Small to medium-sized businesses, expanding operations |
Operator Skill Level | Intermediate
|
Weight | Typically, around 500 kg |
Machine Dimensions | 1020*830*1980 mm Varies by model |
Power Requirement | 110v/220v single phase+380v 3phase |
Material Compatibility | Plastic, glass, metal containers
|
Label Alignment | Semi-automatic positioning for precision
|
Usage Environment | Indoor, dry, and clean conditions
|
Fully Automatic Shrink Sleeve Label Applicators
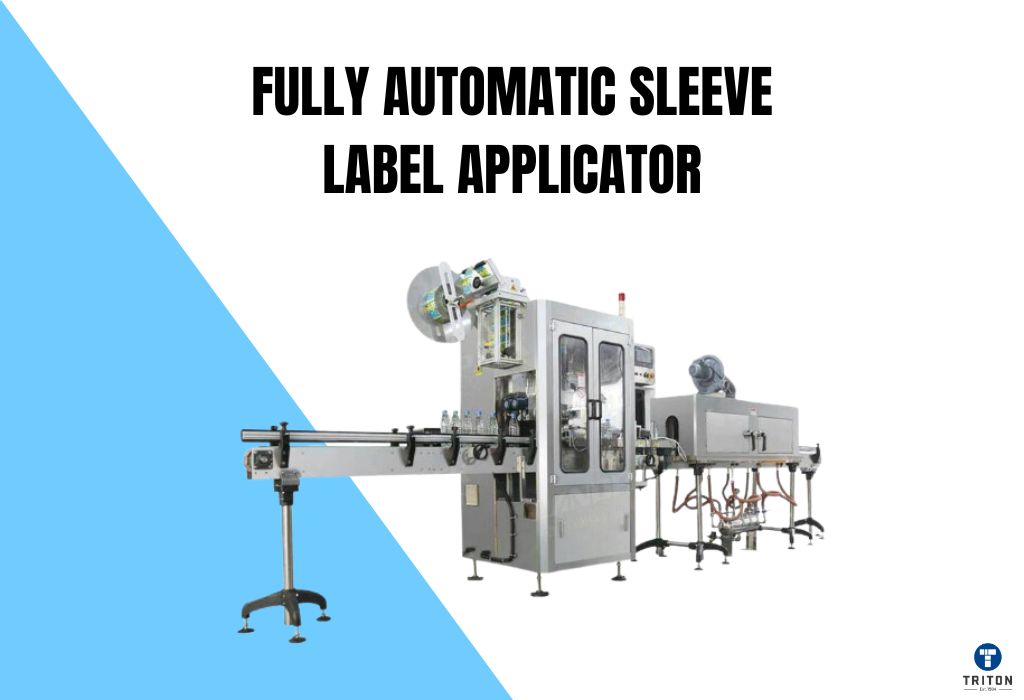
Fully automatic shrink sleeve label applicators are used in high-speed industrial scale production lines to automate the entire labelling process. These machines can process hundreds or even thousands of containers per minute.
Recent advancements in these applicators include downgauging, which involves using thinner films for sleeves, and automatic film splicing and print registration, which have been integrated to improve accuracy and reduce interruptions during operation.
IoT and Industry 4.0 have brought a new level of intelligence to fully automatic shrink sleeve label applicators. With IoT, these machines can now collect and analyse performance data in real-time, enabling predictive maintenance and reducing the risk of unexpected downtime. This data-driven approach allows on-the-fly adjustments for optimal machine performance and minimises material waste.
Industry 4.0 integration connects these applicators to other equipment on the production line, creating a fully automated and interconnected system (including digital twins).
Main Components
- Product Infeed System: This can be a conveyor belt, in-feed screw, or starwheel that positions and transports containers throughout the labelling process.
- Sleeve Unwind and Registration System: This section houses a roll of shrink sleeve material, unwinds it smoothly with a tensioning mechanism, and ensures precise registration for accurate cutting.
- Sleeve Former (Mandrel): This contoured form shapes the sleeve into a 3D cone that easily slides onto the container.
- Sleeve Cutter: A rotary cutter or similar mechanism precisely cuts the sleeve to the desired length based on container size.
- Sleeve Applicator Head: This head uses compressed air or mechanical arms to grab and place the pre-cut sleeve onto the container.
- Shrink Tunnel: This enclosed chamber uses hot air to shrink the label securely onto the container’s shape.
- Conveyor Outfeed System: This transports the labelled containers out of the machine for further processing or packaging.
- Control System: The brain of the operation, a PLC (Programmable Logic Controller) along with a Human-Machine Interface (HMI) touchscreen, allows for setting parameters, monitoring performance, and making adjustments for different container sizes and labels.
- Safety Systems: Light curtains, emergency stops, and safety guards ensure operator safety during operation.
How do Automatic Shrink Sleeve Label Applicators Work?
- Pre-Operational Setup
- Sleeve rolls are loaded into the automated loading system.
- Parameters are configured using the centralised control system.
- Automatic Sleeve Unwinding
- The automated sleeve loading system continuously unwinds the sleeves.
- Sensors monitor the sleeve roll and ensure consistent feed into the cutting unit.
- High-Speed Cutting
- The high-speed cutting unit precisely cuts sleeves to the programmed lengths.
- The system automatically adjusts for different lengths.
- Product Entry and Handling
- Products are fed into the system via conveyor belts or robotic handlers.
- The handling system ensures a steady flow of products entering the alignment and placement area.
- Dynamic Alignment and Placement
- Real-time adjustments are made using cameras and sensors for perfect sleeve placement.
- The alignment system adapts to different product shapes and sizes on the fly.
- Heat Shrink Process
- Products pass through the comprehensive heat shrink tunnel, where multi-zone heaters apply controlled heat.
- The sleeve shrinks uniformly around the product, conforming to its shape.
- Quality Inspection
- Vision systems inspect each product for proper sleeve application.
- Products with misapplied or defective sleeves are automatically rejected.
- Operational Adjustment and Monitoring
- Operators can monitor and adjust settings via the centralised control system.
- The system allows for quick recipe changes, facilitating fast transitions between different product batches
Technical Specifications of Generic Fully Automatic Shrink Sleeve Label Applicators
Feature | Specification |
---|---|
Container Diameter Range | 0.5 – 8 inches |
Container Height Range | Up to 18 inches |
Labelling Speed | 400 containers per minute to 1000 containers per minute |
Training Requirement | High |
Maintenance Requirement | High (requires regular maintenance by trained technicians) |
Label Material | Heat-sensitive shrink sleeves |
Application Process | Fully automated application with integrated heat tunnel |
Heat Source | Built-in heat tunnel, infrared heater, steam
|
Suitable for | Large-scale manufacturing, high-volume production lines |
Operator Skill Level | Advanced (requires technical expertise)
|
Weight | Typically 1,000 kg (varies by model)
|
Machine Dimensions | Typically 2500 x 1500 x 2200 mm
|
Power Requirement | 220V/380V three-phase power |
Material Compatibility | Plastic, glass, metal containers
|
Label Alignment | Automated positioning for high precision
|
Usage Environment | Industrial settings, requiring controlled conditions
|
Tamper-Evident Neck Shrink Sleeve Applicators
These machines apply shrink sleeves to container necks to provide clear tamper indication. These applicators use sleeves made from polyethylene terephthalate glycol (PETG) or polyvinyl chloride (PVC) for their sturdiness and uniform shrinking properties.
These applicators have throughputs ranging from 100 to 300 units per minute.
Components of Tamper-Evident Neck Shrink Sleeve Applicators
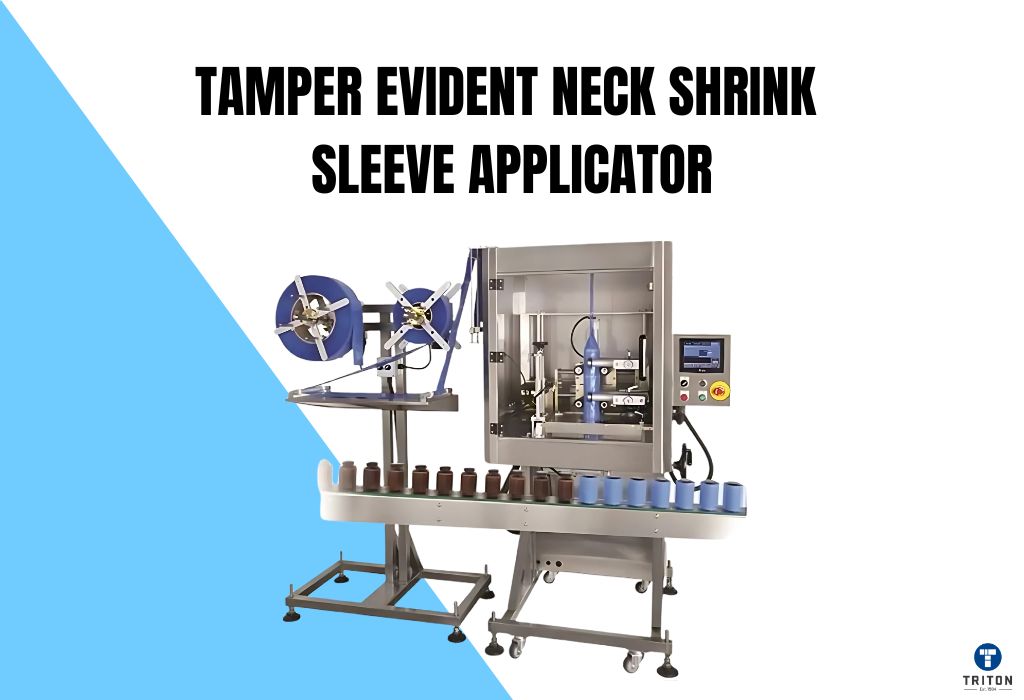
Main Components
- Stainless Steel Frame: The main base frame of the applicator is made of sturdy stainless steel pipes, providing a robust and durable structure.
- Stainless Steel Coverings: The machine is fully enclosed in high-quality stainless steel 304 panels, ensuring a hygienic and corrosion-resistant design.
- Precision Bearings: The applicator utilises SKF, Nachi, or equivalent high-quality bearings for smooth and reliable operation.
- Stainless Steel Guide Rods and Pins: Critical moving parts are made of stainless steel 304 for enhanced durability and corrosion resistance.
Sleeve Handling Components
- Film Unwinding Unit: The sleeve material is unwound and controlled by a motor-driven system.
- Sleeve Feeder: Two motors with up-down assemblies precisely feed the sleeve material into the applicator.
- Sleeve Pitching Unit: A dedicated motor controls the pitching (spacing) of the sleeve material.
- Sleeve Pusher Unit: Two motors with up-down assemblies push the sleeve onto the container neck.
- Sleeve Cutting Unit: A blade-based system accurately cuts the sleeve to the desired length.
Automation and Control
- Servo Motors: Servo motors are used for precise control and positioning of various components.
- Digital PLC with HMI: A digital programmable logic controller (PLC) with a human-machine interface (HMI) provides advanced control and monitoring capabilities.
- Bottle Sensors: Sensors detect the presence of bottles to ensure accurate sleeve application.
- Eye Mark Sensor: For printed sleeves, an eye mark sensor ensures precise cutting alignment.
Performance Specifications
- Production Speed: 30 to 400 bottles per minute, depending on bottle size, sleeve length, and material.
- Sleeve Thickness: Minimum 40 microns.
- Sleeve Applying Area: Tamper-evident neck sleeving.
- Accuracy: Sleeve application within ±1.5 mm of the target position.
Technical Specifications of Generic Tamper-Evident Neck Shrink Sleeve Applicators
Feature | Specification |
---|---|
Container Diameter Range | 0.5 – 5 Inches |
Container Height Range | Up to 12 inches |
Speed of Manufacturing | Up to 300 containers per minute (varies by model) |
Training Requirement | Moderate to high (requires specialised training) |
Maintenance Requirement | Moderate to high (requires regular and specialised maintenance) |
Label Material | Heat-sensitive tamper-evident shrink sleeves
|
Application Process | Fully automated application with integrated heat tunnel |
Heat Source | Built-in heat tunnel or infrared heater
|
Suitable for | Large-scale manufacturing, high-volume production lines |
Operator Skill Level | Intermediate to advanced (requires technical expertise)
|
Weight | Typically 800 kg (varies by model) |
Machine Dimensions | Approximately 2000 x 1200 x 1800 mm (varies by model) |
Power Requirement | 220V/380V three-phase power
|
Material Compatibility | Plastic, glass, metal containers
|
Label Alignment | Automated positioning for high-precision
|
Shrink Sleeve Applicators with Tunnel Sleeve Labellers
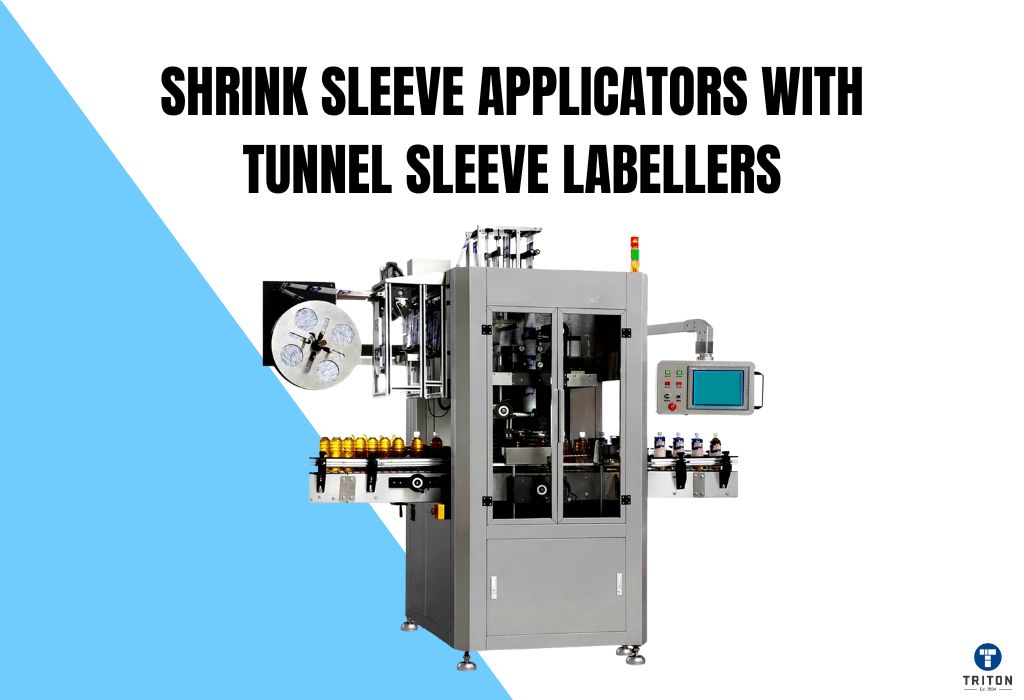
Shrink sleeve applicators with tunnel sleeve labellers are used in packaging to apply shrink sleeves to containers for a tight fit. This process improves the product’s visual appeal and security.
These applicators use sensors and vision systems to detect and correct misalignments in real time, which increases accuracy and reduces waste.
These applicators can handle various container shapes and sizes and are used in food & beverage, pharmaceutical, and cosmetic industries for consistent, tamper-evident packaging.
Their heat tunnels use steam or electric heat to shrink the sleeves to the container’s shape, ensuring an airtight, tamper-evident seal.
Main Components
Applicator Section:
- Sleeve Dispenser: Holds the roll of shrink sleeve material and ensures smooth feeding through tension control mechanisms and guide rails.
- Sleeve Former (Mandrel): The contoured form of the mandrel shapes the sleeve into a cone for easy placement onto the container.
- Sleeve Cutter: Precisely cuts the sleeve to the desired length based on container size (rotary cutter, guillotine cutter).
- Sleeve Applicator Head: Uses compressed air or mechanical arms to grab and place the pre-cut sleeve onto the container.
- Control System: Manages applicator functions like speed, tension, and cutting parameters.
Shrink Tunnel Section:
- Heat Chamber: Enclosed chamber where hot air shrinks the label securely onto the container’s shape.
- Conveyor System: Transports containers through the heat chamber for uniform shrinkage.
- Airflow System: Circulates hot air within the chamber, ensuring even heat distribution.
- Temperature Controls: Regulate the temperature within the heat chamber for optimal shrinking based on sleeve material.
Additional:
- Safety Features: Light curtains, emergency stops, and safety guards protect operators during operation.
- Tunnel Design: Options include steam tunnels (for 360° heat) or electric hot air tunnels (more energy-efficient).
How do Tunnel Sleeve Labellers Work?
- System Setup
- Position the shrink sleeve applicator and tunnel sleeve labeller on the production line.
- Load the roll of shrink sleeves into the automatic sleeve feeding system.
- Configure settings on the integrated control system based on product and sleeve specifications.
- Automatic Sleeve Feeding
- The motorised roll holder unwinds the shrink sleeves.
- Sensors ensure a continuous and smooth feed of sleeves into the cutting mechanism.
- Precision Sleeve Cutting
- The cutting mechanism slices sleeves to the required lengths with precision.
- Automated adjustments allow for different sleeve lengths as needed.
- Product Transport
- Products are conveyed through the system on adjustable guide conveyors.
- Ensures consistent spacing and alignment for the sleeve application.
- Accurate Sleeve Application
- The sleeve application unit positions the cut sleeve accurately onto each product.
- Uses a vacuum, static electricity, or mechanical arms for precise placement.
- Heat Shrink Process
- Products with applied sleeves enter the heat shrink tunnel.
- Multi-zone heating elements apply uniform heat, causing the sleeves to shrink tightly around the products.
- Conveyor speed and temperature are adjustable for different product requirements.
- Inspection and Quality Control
- Products are inspected after the shrinking process to ensure proper sleeve application.
- Any defective or misapplied sleeves are automatically identified and rejected.
- Operational Monitoring and Adjustment
- Operators monitor the process via the PLC and HMI control system.
- Adjustments to speed, heat, and sleeve application settings can be made as necessary.
Feature | Specification |
---|---|
Container Diameter Range | 0.5 – 8 Inches |
Container Height Range | Up to 18 inches |
Speed of Manufacturing | Up to 400 containers per minute (varies by model) |
Training Requirement | High (requires specialised training)
|
Maintenance Requirement | High (requires regular and specialised maintenance) |
Label Material | Heat-sensitive shrink sleeves |
Application Process | Fully automated application with integrated heat tunnel |
Heat Source | Built-in heat tunnel or infrared heater
|
Suitable for | Large-scale manufacturing, high-volume production lines |
Operator Skill Level | Advanced (requires technical expertise)
|
Weight | Typically, around 1,000 kg |
Machine Dimensions | Typically 2500 x 1500 x 2200 mm
|
Power Requirement | 220V/380V three-phase power |
Material Compatibility | Plastic, glass, metal containers
|
Label Alignment | Automated positioning for high precision
|
Usage Environment | Industrial settings, requiring controlled conditions
|
Heat Tunnel Specifications | Adjustable temperature settings, conveyor speed control |
Heat Tunnel Dimensions | Typically 3000 x 1000 x 1500 mm (varies by model) |
Roll-Fed Applicators
Roll-fed applicators are used for high-volume production. They feed shrink-sleeve material from a roll, cut it, and apply it to products in one motion. These applicators use servo-controlled systems and cutting mechanisms.
They operate with PLC (Programmable Logic Controller) technology for smooth operation and have HMI (Human-Machine Interface) control panels for easy adjustments.
Roll-fed applicators are used in industries like beverages, pharmaceuticals, and household products, where efficiency and speed are crucial.
Market Trends and Future of Shrink Sleeve Label Applicators
The future of shrink sleeve label applicators is shaped by significant technological advancements and market growth. One notable trend is the increasing integration of smart sensors and automation, which enhances the efficiency and precision of these machines.
The market is also witnessing increased adoption of shrink-sleeve label applicators across various industries, including food and beverage, pharmaceuticals, and cosmetics. These sectors benefit from the applicators’ ability to handle diverse container shapes and sizes with high precision, thereby improving product aesthetics and security.
Conclusion
Whether you run a small business, a mid-sized company, or a large-scale manufacturing operation, knowing the different types of shrink sleeve label applicators—manual, semi-automatic, fully automatic, tamper-evident neck, and those with tunnel sleeve labellers—helps in choosing the right equipment for your packaging needs.
Selecting the appropriate shrink sleeve label applicator can enhance productivity, ensure precise labelling, and strengthen your product’s market presence.
FAQs
What is a shrink-sleeve label applicator?
A shrink sleeve label applicator is a machine designed to apply shrink sleeve labels onto containers. The labels shrink and conform to the shape of the container when heat is applied, providing a seamless and attractive finish.
What are the different types of shrink-sleeve label applicators?
There are several types of shrink sleeve label applicators, including manual, semi-automatic, fully automatic, tamper-evident neck, and tunnel sleeve labellers. Each type is suited for different scales of operation and levels of automation.
What is the role of heat tunnels in shrink-sleeve label applicators?
Heat tunnels are used to apply heat uniformly to shrink sleeve labels, ensuring they conform tightly to the container. They can be powered by steam or electric heat and are integrated into semi-automatic and fully automatic applicators.
How do tamper-evident neck shrink sleeve applicators enhance product security?
Tamper-evident neck shrink sleeve applicators apply shrink sleeves to the neck area of containers, creating a visible indication if the product has been tampered with.
What factors should I consider when choosing a shrink-sleeve label applicator?
When choosing a shrink sleeve label applicator, consider factors such as your production volume, the types of containers you use, the level of automation you need, and your budget.