A load cell is a transducer that converts force (or weight) into an electrical signal. This property makes load cells useful for applications like weighing scales, material testing equipment, medical devices, aerospace & defence technology and more.
Weight vs Mass: Simply put, mass is the amount of matter in an object and doesn’t change regardless of location. Weight is the force exerted by gravity on that mass, so it can vary depending on where you are (like Earth vs. the Moon). Think of mass as the “stuff” in something, and weight as how heavy that “stuff” feels due to gravity pulling on it. Are Weight and Force the Same Thing? Not really. Weight is a specific type of force – the gravitational force that acts on an object’s mass. So, while weight is a force, not all forces are weight; there are other types of forces like friction, tension, and centrifugal etc. |
Inside the load cell, there are specially designed areas that bend when a force is applied. Attached to these areas are small metal strips called strain gauges.
When the load cell bends, the strain gauges also bend, creating a tiny electrical signal.
The global load cell market was valued at $165.2 billion in 2022 and is projected to reach $227.0 billion by 2031, growing at a rate of 3.7% annually. This growth is driven by the increasing adoption of automation, advancements in digital technologies, and the need for precise measurement.
How Load Cells Work
Load cells work by converting mechanical force into an electrical signal. Here’s how they work:
Role of Strain Gauge
When a force is applied to an object, it can cause it to bend, stretch or compress. This change in shape is called deformation.
The amount an object deforms depends on its size, material, and the force applied. The term “strain” refers to how much an object deforms compared to its original size.
Strain gauges measure this deformation. They are made of a thin, resistive foil pattern attached to a flexible backing material. When the object with a strain gauge deforms, the strain gauge deforms in the same way.
As the strain gauge stretches, its electrical resistance increases, and when it compresses, the resistance decreases. By measuring this change in resistance, we can determine how much the object has stretched or compressed.
This change in resistance is used to determine the weight or force applied on the strain gauge.
Wheatstone Bridge
The wheatstone bridge is what converts the change in resistance into an electrical signal. The wheatstone bridge has four strain gauges
When no force or weight is applied to the load cell, the bridge is balanced. In other words all four strain gauges have the same resistance.
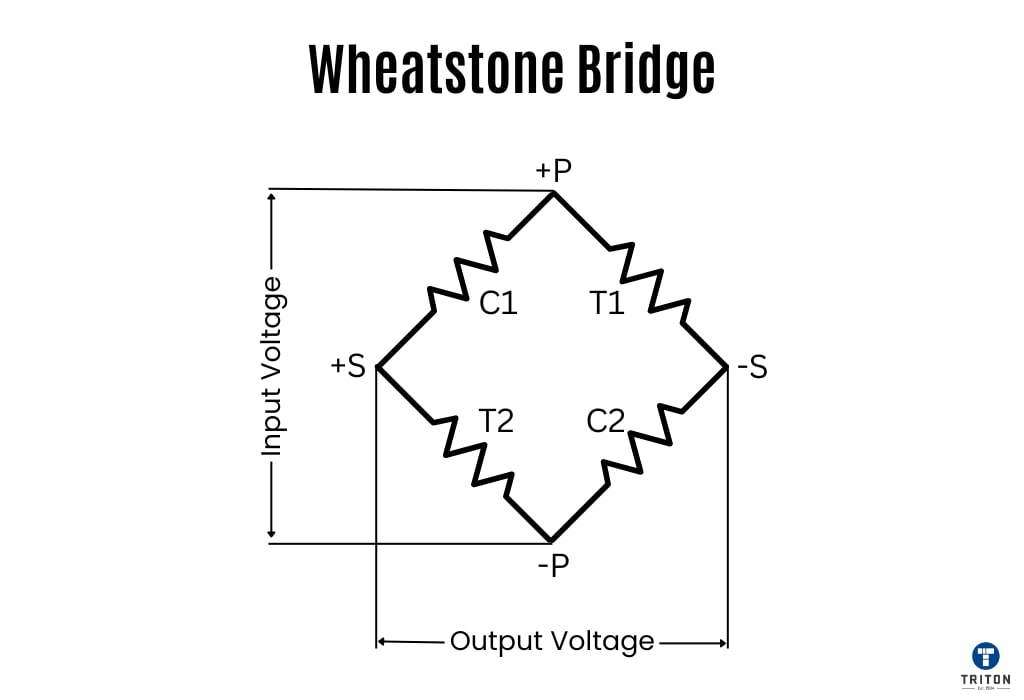
When a force is applied, the strain gauges deform: two gauges stretch, and two compress. This deformation changes their resistance, unbalancing the bridge and creating an output voltage proportional to the applied load.
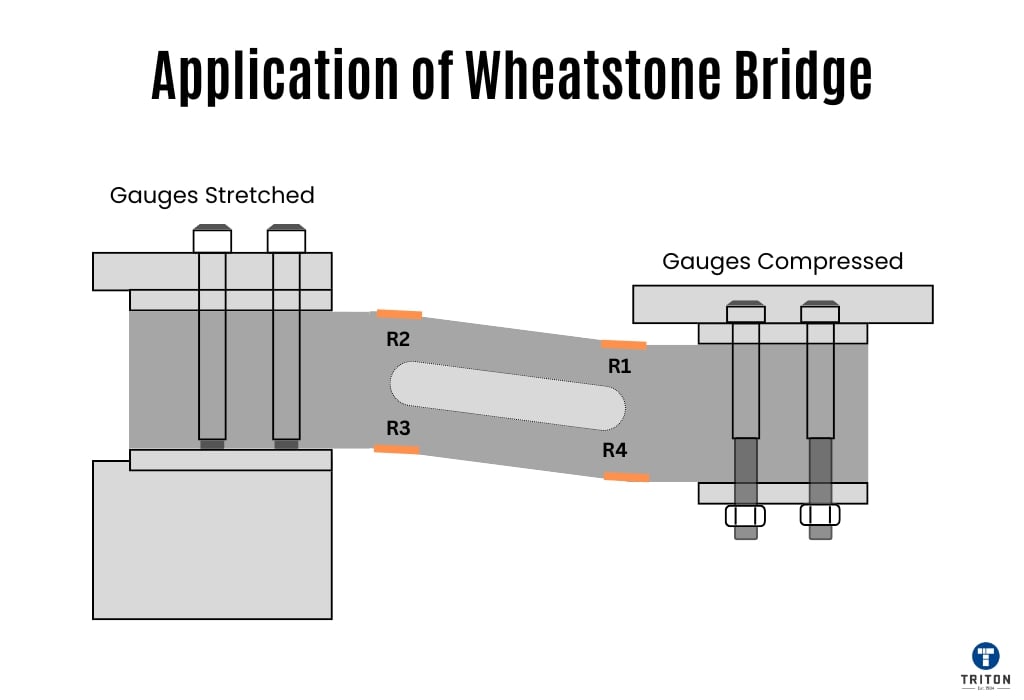
The output voltage is sent through signal wires to a device that converts it into a readable force value, like pounds, kilograms, or newtons.
Factors such as temperature and wire length can affect resistance and cause errors. Load cells add extra resistance to the bridge to compensate for these effects and ensure precision.
Types of Load Cells
Load cells come in different types, each with unique operating principles and suitable applications. Here are some common types:
Strain Gauge Load Cells:
Strain gauge load cells are the most widely used. They work by measuring the change in electrical resistance of strain gauges attached to the load cell structure.
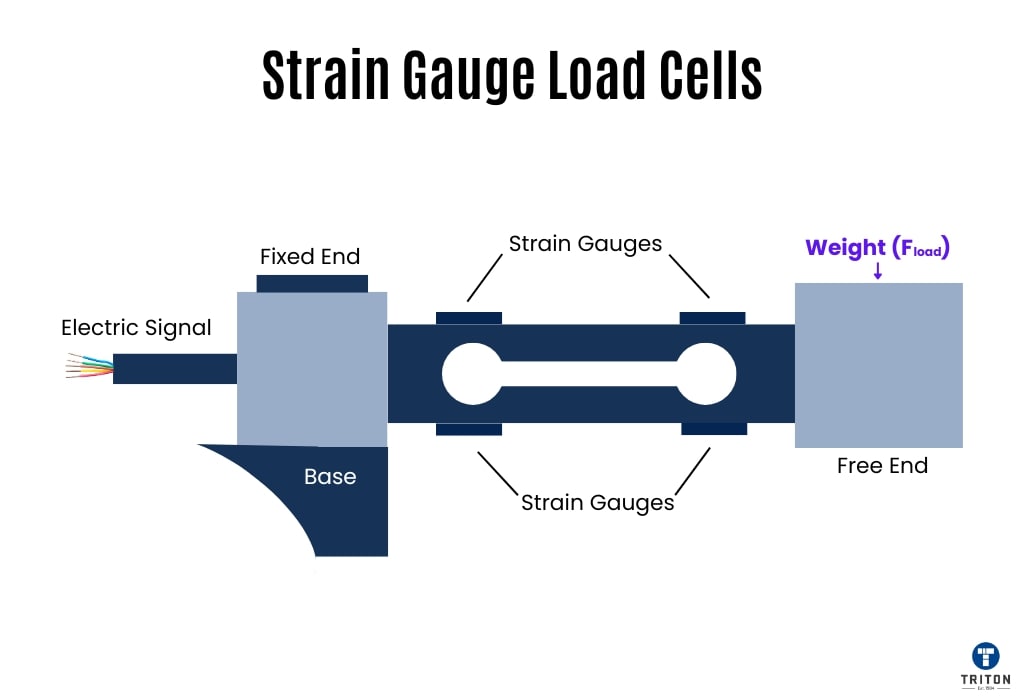
When a force is applied, the strain gauges deform, altering their resistance. This change is then converted into an electrical signal that indicates the force applied.
The capacities of strain gauge load cells typically range from one kilogram to more than 50,000 kilograms. These load cells can precisely track sudden changes in force or weight because of their fast response time which comes around 1-10 milliseconds.
Hydraulic Load Cells
Hydraulic load cells use a fluid-filled chamber to measure force. When a load is applied, it changes the pressure in the fluid. This pressure change is then measured by a pressure gauge or a transducer, which converts the pressure into an electrical signal that can be read and interpreted.
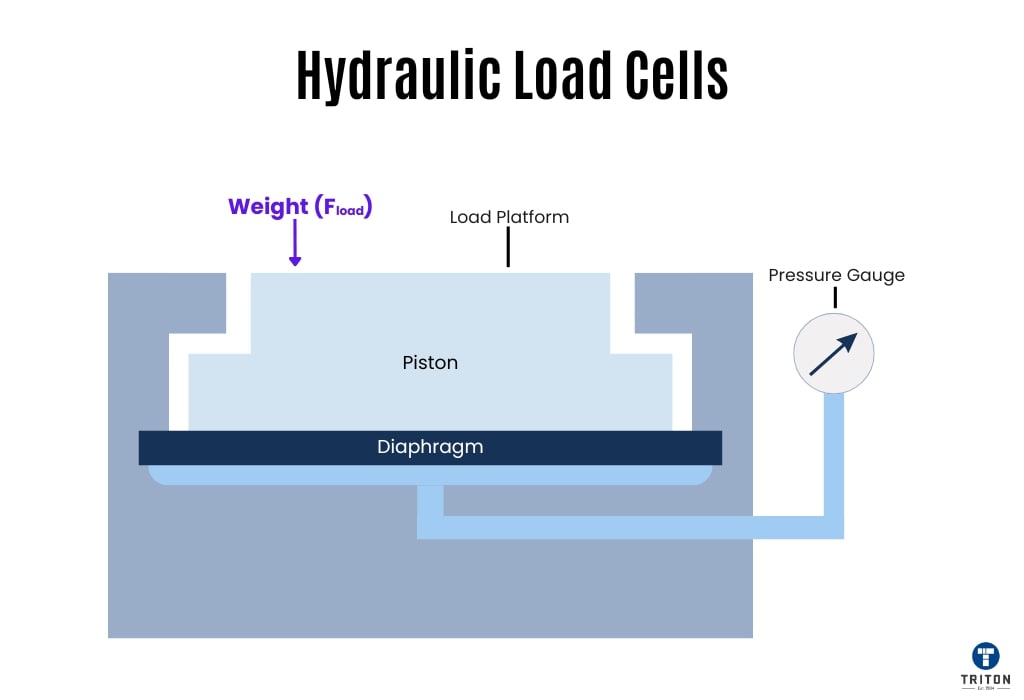
These load cells can measure weights ranging from 1 ton up to 1,000 tons can be measured by these load cells. Custom-made hydraulic load cells can handle weight up to 10,000 tons.
Hydraulic load cells respond slower than other types, like strain gauge and piezoelectric load cells. This is because the fluid takes time to move and stabilise, causing a delay in the system’s response to changes in pressure.
This type of load cell is especially useful in environments where electrical power is impractical or hazardous, such as chemical plants and mining operations.
Hydraulic load cells have an accuracy of 0.25% to 1.0% of full-scale output. Their resolution is about 0.02%, making them suitable for precise measurements in various industrial applications.
Accuracy vs Resolution: Accuracy is how close the load cell’s reading is to the true weight, like knowing your exact weight on a scale. Resolution is the smallest weight change the load cell can detect, like noticing the difference if you add or remove a small item, such as your mobile phone. So, accuracy ensures the reading is correct, while resolution ensures small changes in weight are noticeable. |
They are robust and can handle extreme conditions, ensuring reliable performance over time.
Pneumatic Load Cells:
Pneumatic load cells, similar to hydraulic ones, use air pressure instead of fluid. The load applied to the cell compresses the fluid, and this compression changes the fluid’s pressure. This pressure change is then measured by a pressure gauge or a transducer, which converts the pressure into an electrical signal.
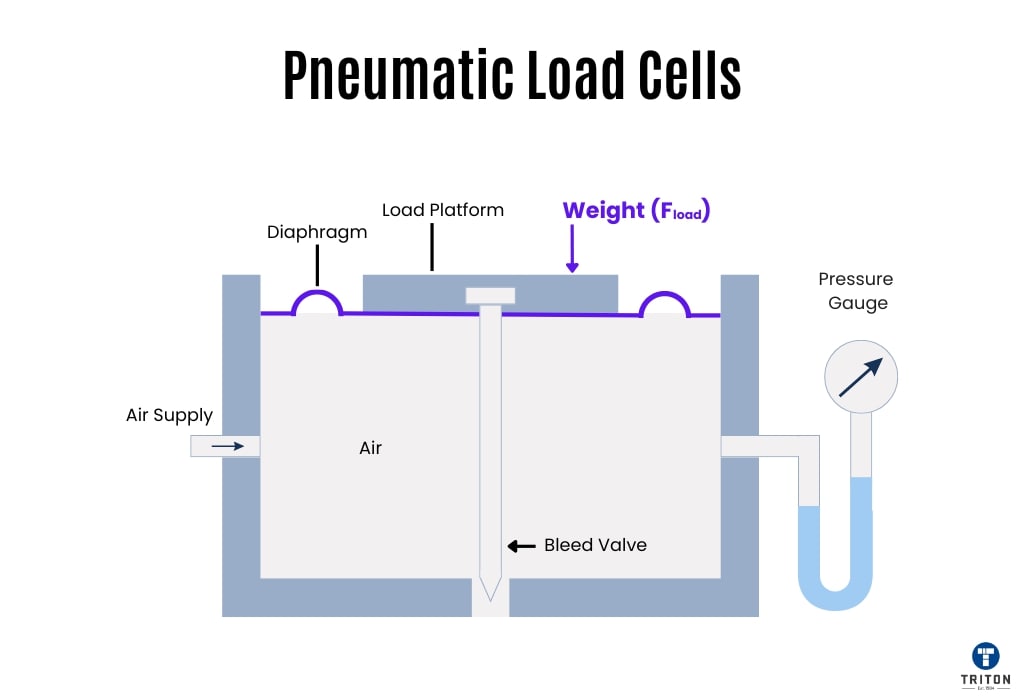
Pneumatic load cells work on the same principle as hydraulic ones, but they use air pressure instead of fluid. The load applied to the cell compresses the air, changing its pressure. A pressure gauge or transducer then measures this pressure change and converts it into an electrical signal.
Because pneumatic load cells use compressed air, there’s no risk of contamination if the diaphragm ruptures. This makes them ideal for industries like pharmaceuticals and food processing.
The capacity of pneumatic load cells can range from 1 kilogram to over 200 tons and they are accurate within 0.5% to 1% of full scale.
Capacitive Load Cells:
A capacitive load cell consists of two parallel conductive plates separated by a dielectric (insulating material). When a force is applied, the distance between these plates changes, altering the capacitance.
Then, this change in capacitance is measured and converted into an electrical signal.
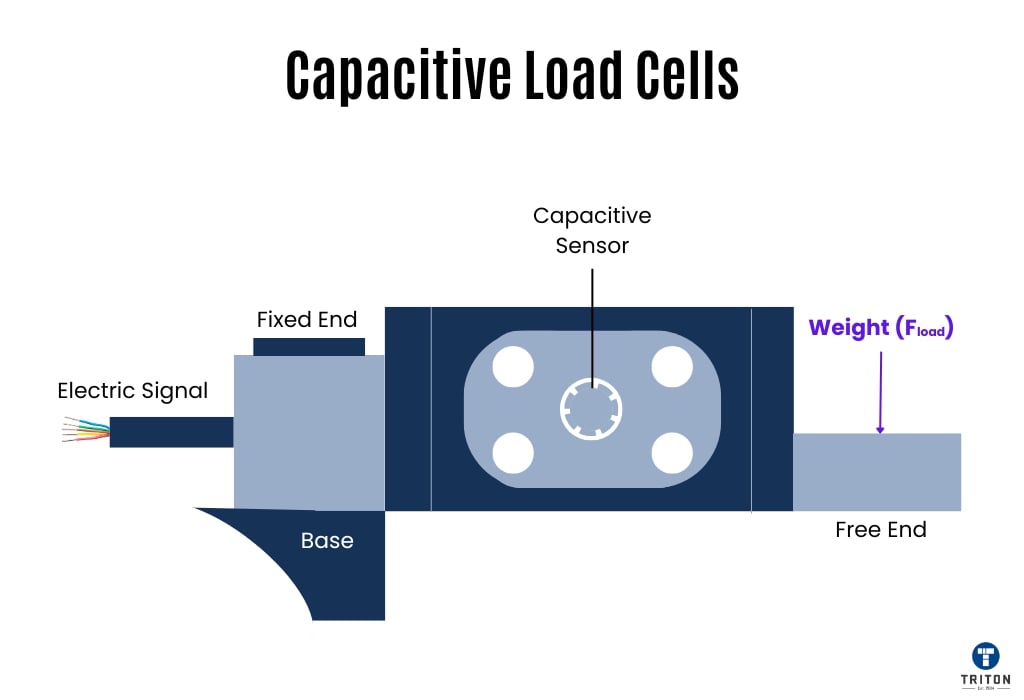
Capacitive load cells have a wide measurement range from several grams to about 10 tons. They have a very fast response time, typically in the range of milliseconds. For example, some capacitive load cells can respond in just 3 to 5 milliseconds.
Capacitive load cells have high accuracy, often within 0.1% to 0.025% of full scale, making them perfect for tasks that need high precision, like lab tests and small industrial processes. They can detect tiny changes in force, which is why they are great for delicate measurements.
Piezoelectric Load Cells:
Piezoelectric load cells work by using the piezoelectric effect. These load cells contain materials like quartz or special ceramics.
When a force is applied, these materials deform. The deformation of the piezoelectric material creates an electric charge that is measured by electrodes attached to the material. This charge is then converted into an electrical signal.
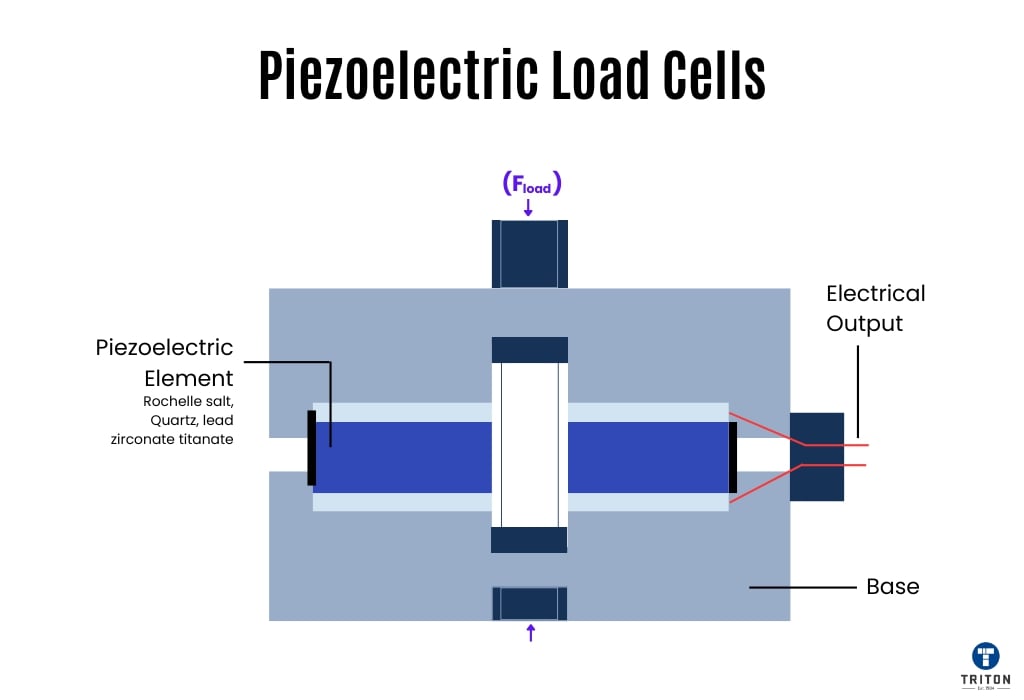
Piezoelectric load cells are capable of handling capacities ranging from as low as a few grams to 10 tons.
Piezoelectric load cells have high accuracy, typically within 0.1% to 0.5% of full scale. They also have fast response times as quick as 1 millisecond and high natural frequencies, which makes them ideal for measuring forces that change quickly, such as in impact tests, vibration monitoring, and car crash tests.
Other Types of Load Cells
Inductive and Reluctance Load Cells
Inductive load cells work by using a coil with a magnetic core. When a load or a force is applied, the magnetic core moves inside the coil, which changes the coil’s electrical properties (inductance). This change creates a signal that can be measured to find out how much load is applied.
Reluctance load cells, on the other hand, operate based on the principle of magnetic reluctance.
In these load cells, the load causes a change in the magnetic circuit’s reluctance, which in turn alters the magnetic field. This change in the magnetic field is detected by a sensor and converted into an electrical signal.
Inductive and reluctance load cells are commonly used in industrial automation, robotics, automotive testing and many other manufacturing processes.
These load cells have error rates of less than 0.1% of the full-scale output.
Magnetostrictive Load cells
Magnetostrictive load cells use special materials that change shape when exposed to a magnetic field. These load cells have a coil and a magnetostrictive material.
When a load is applied, the material changes its magnetic properties. This change affects the coil’s electrical signal, which can be measured to determine the load.
These load cells are durable making them suitable for weight and force measurement in strip mills and rolling mills.
Applications of Load Cells
Load cells measure force and weight accurately, which helps in ensuring quality, safety, and efficiency in different jobs. They are crucial in many areas, from improving product quality in factories to making sure buildings and bridges are strong. Here are some key ways they are used:
Component Life cycle testing:
Load cells help test how long a component will last under stress.
During tests:
- Load cells are attached to the component.
- They measure the component’s deformation when force is applied.
- This process repeats to simulate use.
Example: When testing a car’s suspension arm:
- Load cells measure the suspension arm’s response to forces that mimic a vehicle’s weight and movement.
- This predicts how the part will perform over time.
This testing is necessary in industries like automotive and aerospace, where component failure could cause problems. It ensures parts meet standards before use in vehicles or aircraft.
Structural Testing
Structural testing is a process where engineers use load cells to measure the strength and stability of structures like buildings and bridges.
During testing:
- Load cells are attached to key points of the structure.
- They measure the structure’s deformation under applied forces.
- Tests simulate real-world loads, including static and dynamic forces.
This process allows engineers to:
- Quantify the structure’s load-bearing capacity
- Identify stress concentrations and potential failure points
- Verify compliance with building codes and standards
- Analyse structural behaviour under various load conditions
Load cell data gives insights for optimising structural design, selecting appropriate materials, and refining construction techniques. This ensures structures can withstand anticipated loads throughout their intended lifespan while maintaining safety and performance standards.
Press Force Measurement in Industrial Presses
Industrial presses are machines that apply force to materials for shaping, cutting, or joining. Load cells are used to measure this force.
In press force measurement:
- Load cells are installed on the press structure.
- They measure the force applied during each press cycle.
- This data is recorded and analysed.
Example: In a hydraulic press forming metal parts, load cells measure the force needed to shape the metal.
Benefits of using load cells in presses:
- Ensures consistent product quality
- Prevents press overload
- Allows precise control of applied force
- Reduces material waste
- Extends press lifespan
Manufacturers use this force data to:
- Monitor press performance
- Adjust press settings as needed
- Schedule maintenance
- Improve production efficiency
This information is crucial for maintaining product quality and preserving press functionality over time.
Weight Measurement Systems
Load cells measure weight in everyday and industrial uses.
Everyday applications:
- Household scales use load cells to measure body weight.
- When a person steps on a scale, the load cell converts weight to an electrical signal.
- The scale processes this signal and displays the weight.
Industrial applications:
- Weighing heavy items like shipping containers and raw materials.
- Measuring manufactured goods for quality control.
Other uses:
- Agriculture: Weighing livestock and crops for resource management.
- Retail: Ensuring accuracy of checkout scales for correct pricing.
Load cells provide precision in industries and integrate into daily life. They convert physical force to electrical signals, allowing accurate weight measurement across various fields.
Selecting the Right Load Cell for Your Needs
Selecting the right load cell is essential for achieving accurate and reliable measurements in your specific application. It’s not just about picking a device; it’s about ensuring optimal performance and precision. Here are the key factors to consider to make the best choice:
Load Capacity
Selecting the right load cell capacity is crucial for accurate measurements. Start by determining the maximum load the cell needs to measure, including potential overloads.
Then, choose a load cell with a capacity slightly higher than this maximum load to prevent overloading.
To account for unexpected variations, incorporate a safety margin, typically 20-30% above the maximum load. Consulting with experts like Triton can provide tailored advice, ensuring you select a load cell that offers optimal performance and reliability for your needs.
Environmental Conditions
When choosing a load cell, it’s important to consider the environment it will be used in. Temperature changes can affect accuracy, so select a load cell that works well within your temperature range.
- In humid or wet conditions, use waterproof or sealed load cells to prevent moisture damage.
- For environments with chemicals, choose corrosion-resistant materials like stainless steel.
- Dusty areas need load cells with protective covers to keep out particles.
- Electrical interference can also affect performance, so ensure proper shielding is in place.
The Bottom Line
In conclusion, load cells are essential for precise weight measurement across various industries. Their accuracy and reliability ensure quality and safety in numerous applications. To enhance your weighing systems, check out the top-quality options at Triton Store’s checkweighing systems and manual weigh labelling solutions.