Temperature-sensitive labels are a cost-effective solution for monitoring temperature in a wide range of applications from manufacturing to logistics.
Temperature sensitive labels use chemicals that change colour at specific temperatures.
These labels are typically used to track the temperature of products like vaccines, medicines, electronic components, industrial equipment and perishable goods by showing if the temperature has stayed within the safe range.
They change when the temperature goes above or below a certain point, helping users to assess if the product is still safe.
Unlike electronic temperature sensors, they don’t require a power source, are unaffected by electrical interference, offering a straightforward, reliable way to track temperature.
How Do Temperature Labels Work?
Let’s see how a typical temperature-sensitive label works.
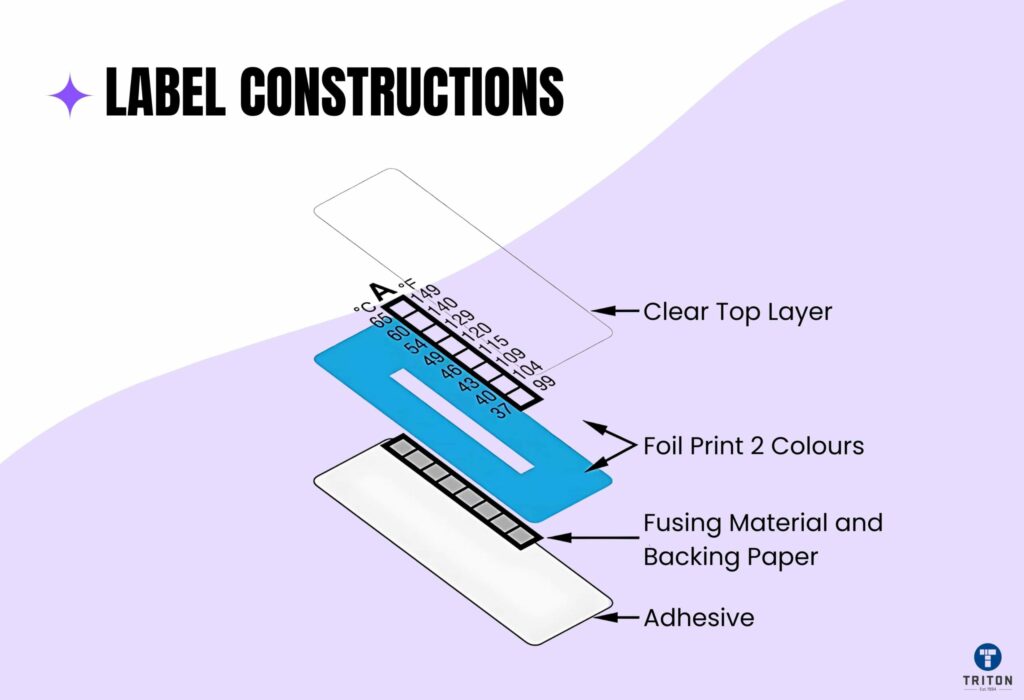
Capillary Action
The simplest temperature-sensitive labels contain two fluids—one clear and one coloured—inside a tiny capillary tube. When the temperature crosses a pre-engineered threshold, the clear fluid expands, pushing the coloured fluid forward and triggering a permanent colour change.
The clear fluid is often a volatile organic compound (VOC) such as isopropanol or hexane. These fluids have predictable expansion properties.
There are other types of temperature sensitive labels that use phase-change indicators, leuco dyes, and, liquid crystals, and organic crystals.
Phase Change Indicators
These indicators work by using a material that changes state from solid to liquid or liquid to solid, to show that a specific temperature has been reached. Materials used in phase change indicators have precise melting/solidifying points under a wide range of pressure. Some materials used in phase change indicators are paraffin waxes, fatty acids, fatty alcohol & easters, diols and dinitriles, and salt hydrates.
Types of Phase Change Melting (Endothermic Phase Change Indicators): This occurs when the material absorbs heat from the environment and changes from a solid state to a liquid. This is the most common mechanism for phase change indicators. Solidification (Exothermic Phase Change Indicators): The phase change material goes from liquid to solid, for indicators designed to detect a temperature drop below a specific temperature. |
Leuco Dyes
Leuco dyes work by shifting between two forms—a coloured form and a leuco (colourless) form. This change is driven by a reversible redox reaction that occurs at a specific temperature.
Leuco dyes are combined with other substances such as weak acids and solvents, which help control the temperature at which this colour transition occurs.
The colour changes because the molecular structure of the dye changes with temperature.
For instance, at one temperature, the dye absorbs visible light, giving it a distinct colour. When exposed to a temperature change, the molecular structure is altered, preventing it from absorbing light in the same way, and thus the dye becomes colourless or a different colour.
This transition is reversible, meaning that once the temperature drops or rises back to its original state, the colour returns to its previous form.
Leuco dyes are preferred for many applications because they can be finely tuned to activate at specific temperature points, providing a reliable visual indicator. The dyes themselves are typically non-toxic and can be safely used in consumer products.
Leuco dyes typically contain spirolactones, fluorans, or crystal violet lactones as the main colouring agents.
The Leuco Dye Family
Crystal Violet Lactone (CVL) | One of the most common leuco dyes | Changes from colourless to blue when heated |
Fluoran dyes | A family of leuco dyes with various colour changes | Examples include: a) 2-Anilino-6-dibutyl amino-3-methyl-fluoran (changes to orange) b) 3-Diethylamino-6-methyl-7-anilinofluoran (changes to red) |
Spiropyrans | Often used in combination with other dyes | Can switch between colourless and coloured forms with temperature changes |
Rhodamine B Lactam | Changes from colourless to pink/red when heated | |
Bisphenol A | Often used as a developer in combination with other leuco dyes | Helps stabilise the colour change |
These dyes are used in combination with other compounds like developers and solvents to create a thermochromic system. The exact formulation depends on the desired colour change, activation temperature, and application requirements.
Liquid Crystals
Liquid crystals behave both like liquids and crystals. They can flow like liquids but maintain some molecular order like crystals.
The molecular structure of liquid crystals changes with temperature, affecting how they interact with light. As temperature changes, the liquid crystals realign, causing them to reflect different wavelengths of light, resulting in visible colour changes.
Some liquid crystals used in temperature sensitive labels are cholesteryl esters, cyanobiphenyls, azoxybenzenes, Schiff bases, and terphenyls.
Liquid crystals are used in mixtures to achieve specific temperature ranges and colour play. The exact composition depends on the desired temperature sensitivity and colour change characteristics.
Key differences from leuco dyes
- Colour range: Liquid crystals typically display a range of colours as temperature changes, while leuco dyes usually switch between two states.
- Reversibility: Liquid crystal colour changes are more easily reversible than those of leuco dyes.
- Precision: Liquid crystals provide more precise temperature readings over a narrow range.
Now let’s look at reversible temperature labels and time-temperature indicators.
Reversible Temperature Labels
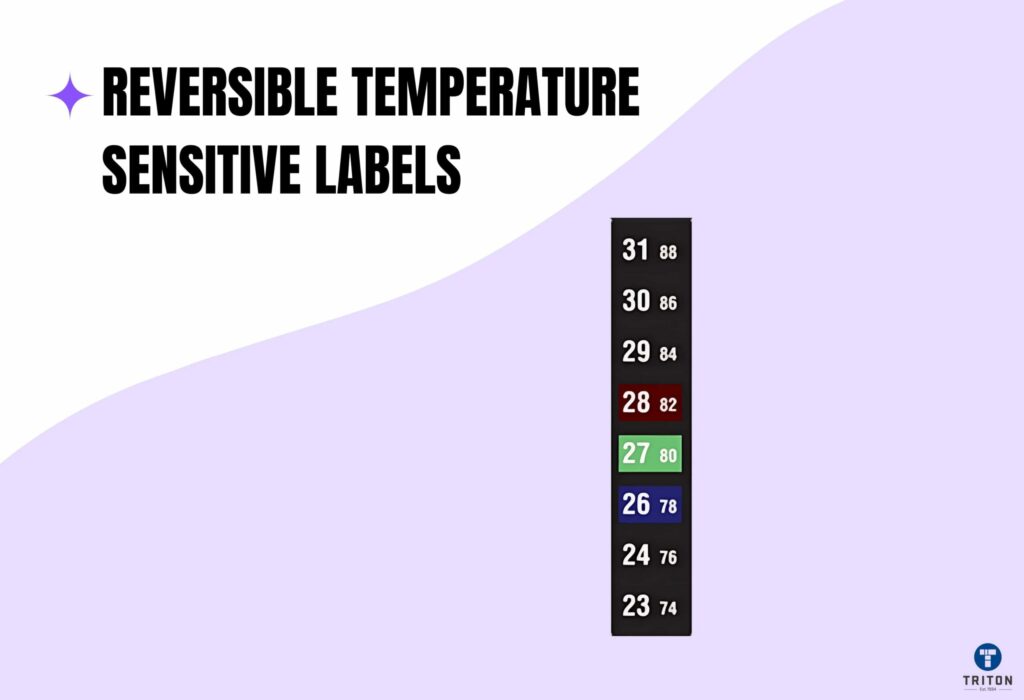
Reversible temperature labels are clever tools that change colour to show the current temperature of a product or environment. These labels use a special type of material called cholesteric liquid crystals, which have a unique property: they reflect different colours depending on their temperature.
Here’s how they work:
- At temperatures below 20°C, the liquid crystals reflect blue light
- Between 20°C and 25°C, the colour shifts through green
- At temperatures above 25°C, the crystals reflect red light
These temperature ranges can be adjusted during manufacturing to suit different applications. For example, a label designed for cold chain monitoring might use these ranges:
- Blue: below 2°C
- Green: 2°C to 8°C (ideal storage temperature for many pharmaceuticals)
- Red: above 8°C
The exact temperature ranges can be customised based on the specific needs of the product or process being monitored. Manufacturers can fine-tune the liquid crystal composition to create labels that are sensitive to different temperature brackets.
The beauty of these labels is their reusability. When the temperature drops, the label returns to its original colour, ready to be used again. This makes them a cost-effective option for ongoing temperature monitoring in manufacturing and logistics.
However, these labels only show the current temperature. They don’t keep a record of past temperature exposures, which might be a limitation for some applications.
While reversible temperature labels are quite accurate within their designed temperature range, they do have some limitations. Exposure to temperatures above 122°C for long periods can damage the liquid crystals, affecting the label’s performance. Also, these labels have a shelf life of about 18 to 24 months.
Time-Temperature Indicators (TTIs)
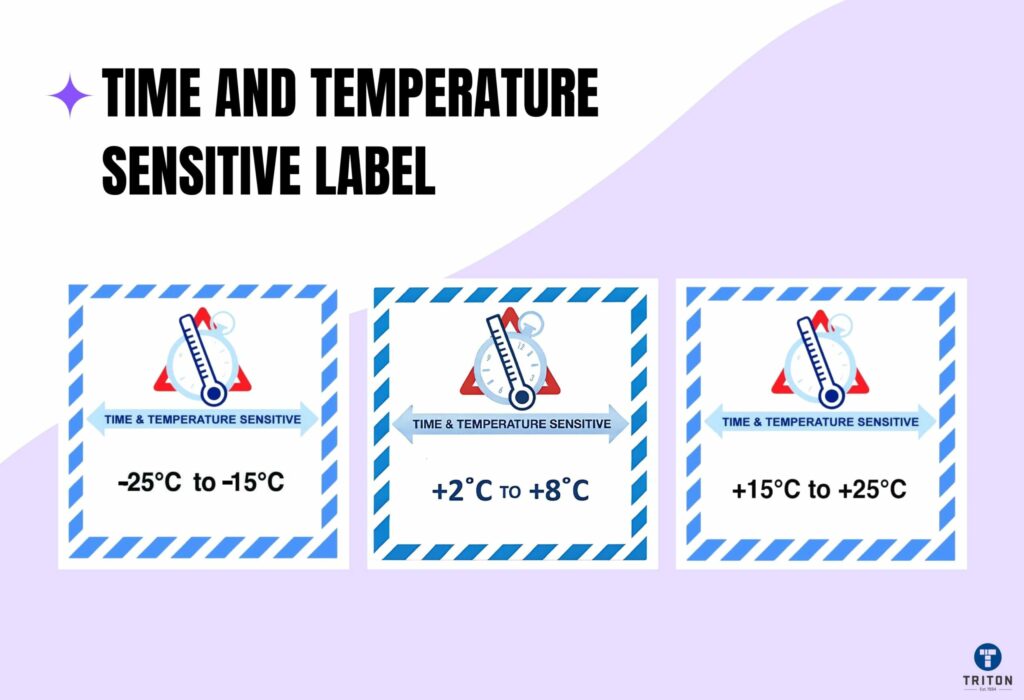
Time-Temperature Indicators (TTIs) are labels used to monitor the combined effects of time and temperature on a product. These labels change colour to provide a visual record of whether a product has been exposed to temperatures outside its safe range for too long.
TTIs work through a chemical reaction that is sensitive to both time and temperature. When the product is stored at safe temperatures, the reaction occurs slowly, and the label remains unchanged.
However, if the product is exposed to high temperatures for a certain duration, the reaction speeds up, causing a visible colour change. This colour shift indicates that the product may no longer be safe or of acceptable quality.
These labels are commonly used in industries like food and pharmaceuticals. For example, a TTI on a food package might turn from white to blue if the product has been exposed to unsafe temperatures beyond a certain duration during transport or storage.
Time-Temperature Indicators (TTIs) rely on irreversible chemical reactions, often involving oxidation, polymerisation, or enzymatic reactions.
Types of Temperature-sensitive labels
Temperature-sensitive labels fall under a broader category of devices, which include both reversible and non-reversible indicators.
Irreversible Temperature Indicator Labels
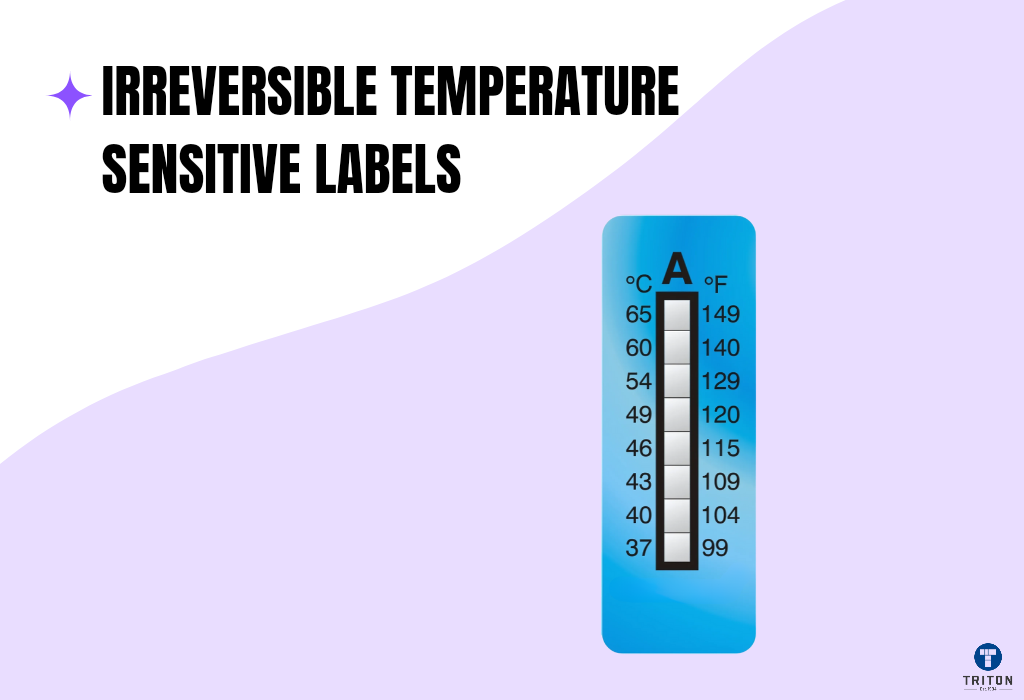
- Multiple Level Labels: These labels permanently change colour when different pre-set temperature thresholds are exceeded. They help monitor gradual increases in temperature, with each level indicating that a specific temperature point has been crossed.
- Time-Temperature Indicators (TTIs): TTIs track both time and temperature exposure, providing a record when products are exposed to unsuitable conditions for too long.
- Cold Mark Indicators: ColdMark labels activate when temperatures fall below a specific threshold.
- Warm Mark Indicators: WarmMark labels change colour when products experience temperatures above a certain limit.
Reversible Temperature Indicator Labels
- Dual Temperature Indicators: These labels monitor both high and low temperature limits (sometimes a range. )Unlike single-use indicators, they can be reset and reused. Dual temperature indicators are useful for products that need protection from both overcooling and overheating.
Why Choose Temperature-sensitive labels over electronic devices?
Here are reasons to choose temperature-sensitive labels over electronic devices:
- Direct Surface Temperature Reading: Fusible indicators provide accurate surface temperature readings as they are applied directly to the surface.
- Instant Feedback: The small mass of the material allows for rapid response, avoiding delays and preventing heat conduction errors.
- Simple and Cost-Effective: These indicators require minimal effort, training, and no advanced equipment, making them an economical choice. Temperature-sensitive labels typically cost around $67-70 for a pack of 10, while electronic monitors range from $18 to $100+ depending on features and the level of data tracking needed
- No Heat Loss: Unlike probes, fusible indicators do not conduct heat away from the surface, ensuring accurate results.
Use Cases for Temperature Labels
Here are the use cases for temperature-sensitive labels:
- Medications and Vaccines: Temperature labels ensure that sensitive products, like mRNA vaccines, are stored and transported at the correct temperatures, such as cold storage down to -80°C.
- Consumer Products: Labels track temperature exposure for perishable goods, like frozen foods, indicating if they have thawed or reached unsafe temperatures during shipping.
- Industrial Equipment: Temperature labels monitor the operating temperature of machinery, helping to maintain optimal performance and prevent overheating in environments where built-in gauges are unavailable.
Conclusion
Temperature-sensitive labels offer a reliable, affordable solution for monitoring temperature changes across industries. Their accuracy ensures the safety of vaccines, medications, and goods. Both irreversible and reversible options provide versatile, cost-effective alternatives to electronic devices.