Offset and digital printing are two widely used methods in modern printing, each suited to different needs. The choice between them depends on factors such as print volume, cost, and customisation requirements.
Offset printing, a time-tested technique, involves transferring ink from plates to a rubber blanket before applying it to the print surface. This method is ideal for high-volume projects where consistent quality and cost-efficiency are required.
Digital printing, on the other hand, prints directly from digital files without the need for plates. It excels in quick turnaround times and allows for customisation, such as variable data printing, making it ideal for smaller runs and personalised outputs.
Understanding the strengths and limitations of each method is key to selecting the right approach for your printing needs. The following sections will explore these methods in detail to guide your decision.
What is Offset Printing
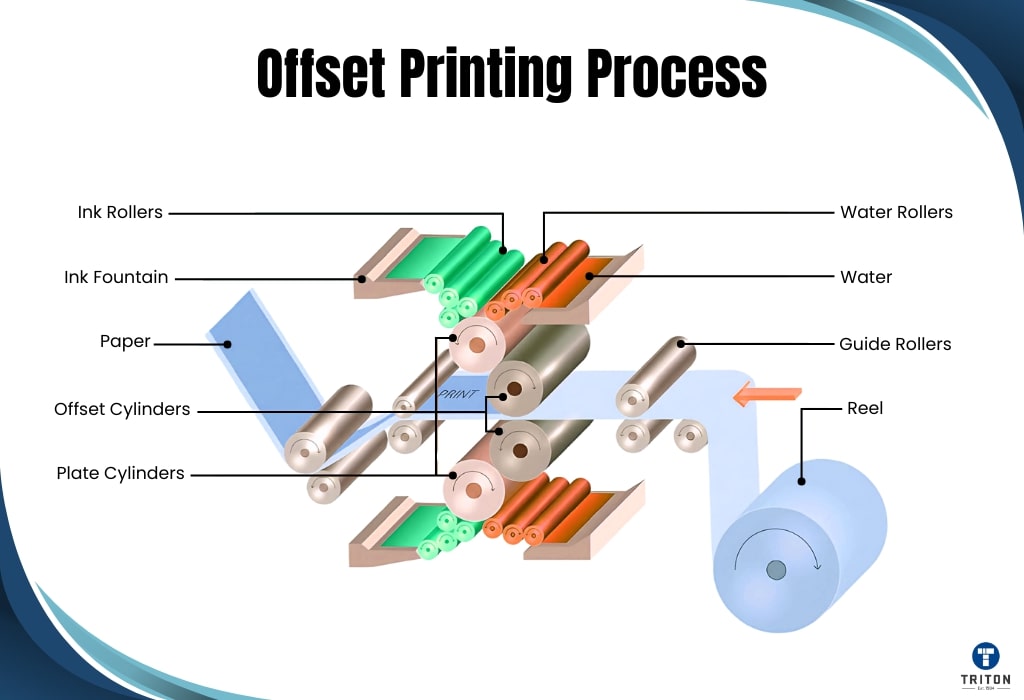
Offset printing, also known as offset lithography, is a commercial printing method that is cost-efficient and produces detailed prints in large volumes. The global offset printing press market was valued at USD 26.85 billion in 2022 and is projected to grow to USD 34.81 billion by 2030, with a compound annual growth rate (CAGR) of 3.3%.
This method operates on the principle of oil and water repulsion, using metal plates to transfer ink to image areas while repelling it from non-image areas. The process relies on three cylinders that work together:
- Plate cylinder: Holds the metal plate with the image.
- Offset blanket cylinder: Transfers the ink from the plate.
- Impression cylinder: Presses the paper against the blanket.
Ink is first applied to the plate, transferred to a rubber blanket, and then pressed onto the paper. The rubber blanket ensures uniform transfer and reduces wear on the plates, making this process reliable for consistent output in large volumes. Offset presses can produce up to 120,000 pages per hour, making them suitable for high-volume applications.
There are two main types of offset printing presses:
- Sheet-fed presses: Handle individual sheets of paper and are used for smaller runs and a variety of paper types, such as brochures and business cards.
- Web presses: Use large rolls of paper and are typically employed for high-volume jobs, such as newspapers and magazines. Web presses often include inline finishing options like cutting and folding.
The market is led by companies such as Heidelberg, Koenig & Bauer, and Komori. Europe leads the market with 47% of global usage, followed by Japan and North America. Europe’s dominance can be attributed to advanced printing technologies and widespread adoption in key industries.
Offset printing supports materials such as paper, cloth, and wood, making it versatile for different applications. Environmental advancements, such as recycled-content paper and eco-friendly inks, have further enhanced its relevance. It remains an important method for large-scale production where efficiency and consistent results are essential.
What is Digital Printing
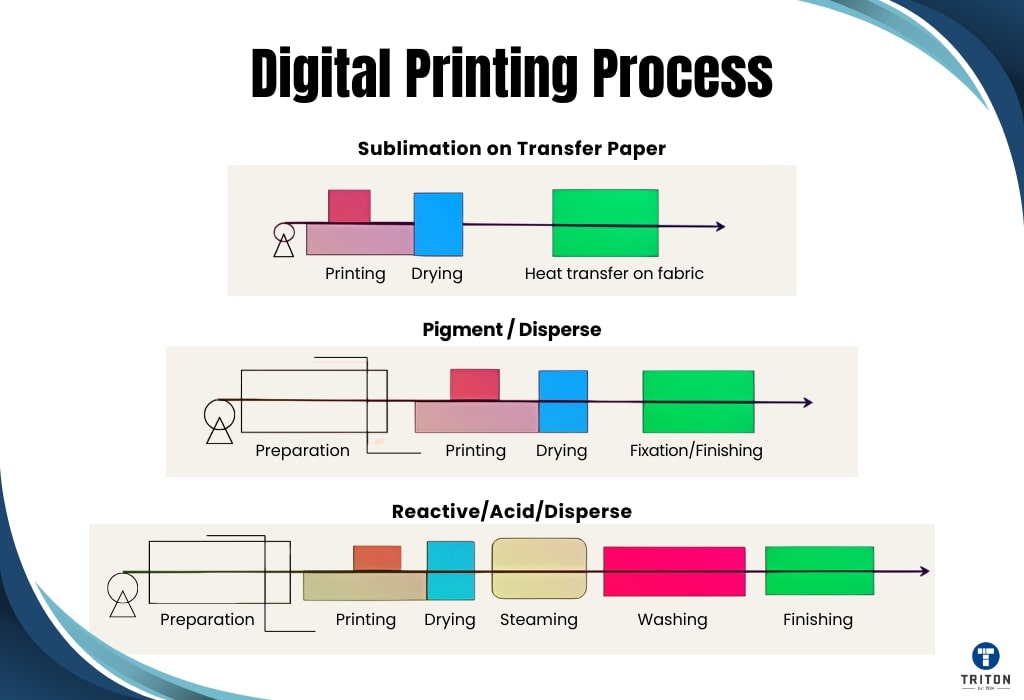
Digital printing is a modern printing method that transfers digital-based images directly onto various media substrates without the need for plates. The global digital printing market was valued at USD 28.19 billion in 2023 and is estimated to be USD 30.22 billion in 2024. It is projected to grow to USD 45.93 billion by 2029, with a compound annual growth rate (CAGR) of 6.36%. This growth reflects the rising demand for customisation and fast turnaround times in the printing industry.
Digital printing directly transfers digital files, such as PDFs, onto materials like paper, fabric, and canvas. Unlike traditional offset printing, it does not require plates, allowing for faster setup and greater flexibility. The process starts by converting the digital file into a raster image, or bitmap, made up of tiny pixels, ensuring precise ink or toner placement.
The process typically involves three steps:
- File preparation: Creating or importing a digital design file.
- Printing: Using inkjet or laser technology to apply colours and patterns to the substrate.
- Finishing: Completing the product with processes like cutting, binding, or laminating.
There are two main types of digital printing technologies:
- Inkjet printing: Propels fine droplets of ink onto the printing surface for high-resolution images and versatile material handling.
- Laser printing: Uses a laser beam to attract toner to specific areas, fusing it onto the material with heat. This method is fast and ideal for high-volume printing.
Digital presses operate at speeds of 15–50 feet per minute and are best suited for smaller print runs, typically around 10,000 items. These machines are favoured for their ability to handle diverse projects efficiently, including on-demand printing.
The market is dominated by companies like HP Inc., Canon, Epson, Xerox, and Ricoh. North America holds the largest market share, while the Asia Pacific region is experiencing the fastest growth, driven by increased adoption in sectors like packaging and textiles.
Digital printing supports a wide range of materials, including paper, fabric, plastic, and ceramics. It is particularly effective for applications requiring short print runs, rapid production, and personalisation. This makes it a popular choice in commercial printing, packaging, textiles, and e-commerce, where customised products are in high demand.
Recent advancements in digital printing include improved colour accuracy, faster print speeds, and integration with technologies like artificial intelligence and machine learning, which optimise production processes. Digital printing provides several advantages, such as cost-effectiveness for small print runs, quick turnaround times, and easy customisation, ensuring its continued importance in the evolving printing landscape.
Digital printing’s key strengths include its ability to produce high-resolution images and handle a variety of materials. Its flexibility and speed make it suitable for industries ranging from marketing and publishing to textiles and packaging, where meeting tight deadlines and delivering personalised outputs are essential.
Offset Printing vs Digital Printing Technology
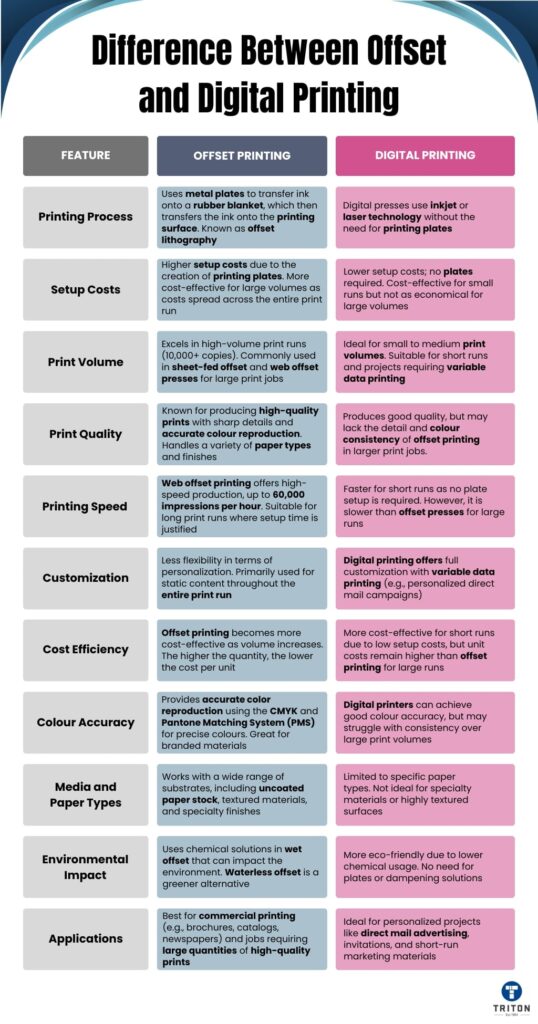
Feature | Offset Printing (Offset Lithography) | Digital Printing |
---|---|---|
Printing Process | Uses metal plates to transfer ink onto a rubber blanket, which then transfers the ink onto the printing surface. Known as offset lithography. | Digital presses use inkjet or laser technology without the need for printing plates.
|
Setup Costs | Higher setup costs due to the creation of printing plates. More cost-effective for large volumes as costs spread across the entire print run. | Lower setup costs; no plates required. Cost-effective for small runs but not as economical for large volumes. |
Print Volume | Excels in high-volume print runs (10,000+ copies). Commonly used in sheet-fed offset and web offset presses for large print jobs. | Ideal for small to medium print volumes. Suitable for short runs and projects requiring variable data printing. |
Print Quality | Known for producing high-quality prints with sharp details and accurate color reproduction. Handles a variety of paper types and finishes. | Produces good quality, but may lack the detail and color consistency of offset printing in larger print jobs.
|
Printing Speed | Web offset printing offers high-speed production, up to 60,000 impressions per hour. Suitable for long print runs where setup time is justified. | Faster for short runs as no plate setup is required. However, it is slower than offset presses for large runs. |
Customization | Less flexibility in terms of personalization. Primarily used for static content throughout the entire print run. | Digital printing offers full customization with variable data printing (e.g., personalized direct mail campaigns). |
Cost Efficiency | Offset printing becomes more cost-effective as volume increases. The higher the quantity, the lower the cost per unit. | More cost-effective for short runs due to low setup costs, but unit costs remain higher than offset printing for large runs. |
Color Accuracy | Provides accurate color reproduction using the CMYK and Pantone Matching System (PMS) for precise colors. Great for branded materials. | Digital printers can achieve good color accuracy, but may struggle with consistency over large print volumes. |
Media and Paper Types | Works with a wide range of substrates, including uncoated paper stock, textured materials, and specialty finishes. | Limited to specific paper types. Not ideal for specialty materials or highly textured surfaces. |
Environmental Impact | Uses chemical solutions in wet offset that can impact the environment. Waterless offset is a greener alternative. | More eco-friendly due to lower chemical usage. No need for plates or dampening solutions.
|
Applications | Best for commercial printing (e.g., brochures, catalogs, newspapers) and jobs requiring large quantities of high-quality prints. | Ideal for personalized projects like direct mail advertising, invitations, and short-run marketing materials. |
Environmental Impact
Offset printing traditionally generates higher waste due to the need for printing plates and initial paper wastage during setup. Historically, the process has also relied on chemical-based inks and cleaning solutions.
Advancements in modern offset printing have reduced its environmental footprint. The adoption of vegetable oil-based inks and recycling systems for ink and water has mitigated some of the waste and chemical usage.
Offset printing’s efficiency in high-volume jobs can reduce overall material waste when economies of scale are considered.
Digital printing eliminates the need for plates, significantly reducing material and paper waste. The process uses less energy during setup and production, particularly for smaller print runs, where no plates are created and initial waste is minimised.
Digital printing uses eco-friendly toners and water-based inks, which are less harmful to the environment and significantly reduce volatile organic compound (VOC) emissions.
Water-based inks eliminate petroleum-based solvents and chemicals, contributing to lower air pollution. Digital printing generates less waste compared to traditional methods, particularly through its ability to support on-demand printing and smaller print runs.
This reduces overproduction, further limiting waste and energy consumption. Additionally, digital printing is more energy-efficient than traditional offset printing, requiring less energy throughout the printing process.
For small print runs, digital printing tends to have a lower environmental impact due to its reduced waste, minimal energy consumption, and reliance on eco-friendly materials. On the other hand, offset printing can be more sustainable for large-scale projects, as the efficiency of high-volume production can offset the initial waste and energy use. Both methods, however, require careful management of resources and materials to maximise sustainability.
Recent advancements in both technologies have aimed to further reduce environmental impacts. These include the use of vegetable oil-based and water-based inks, improved recycling systems, and reduced emissions of VOCs. With these improvements, both offset and digital printing have become more sustainable options for various printing needs. However, the choice of method should align with the scale and requirements of the specific project to minimise the environmental footprint.
Offset printing is best for high-volume, cost-efficient jobs, while digital printing offers speed, flexibility, and personalisation for smaller runs. The choice depends on your print volume, turnaround time, and customisation needs.
Both methods have reduced environmental impacts with modern advancements. Offset suits large-scale projects, and digital is ideal for on-demand printing with minimal waste.
For reliable, tailored printing solutions, visit Triton Store.