In the industrial and packaging sectors, the demand for durable labels like polyester and polypropylene is rising as businesses seek solutions that withstand harsh conditions.
This is reflected in global market trends.
While the packaging labels market was valued at USD 53.92 billion in 2024 and is growing at a 4.5% CAGR, the industrial labels market, covering heavy-duty and safety labels, is expanding faster. It is expected to grow from USD 28.65 billion in 2023 to USD 48.5 billion by 2033 (5.5% CAGR).
This article compares polyester and polypropylene labels, their strengths, applications, and which suits specific industrial needs.
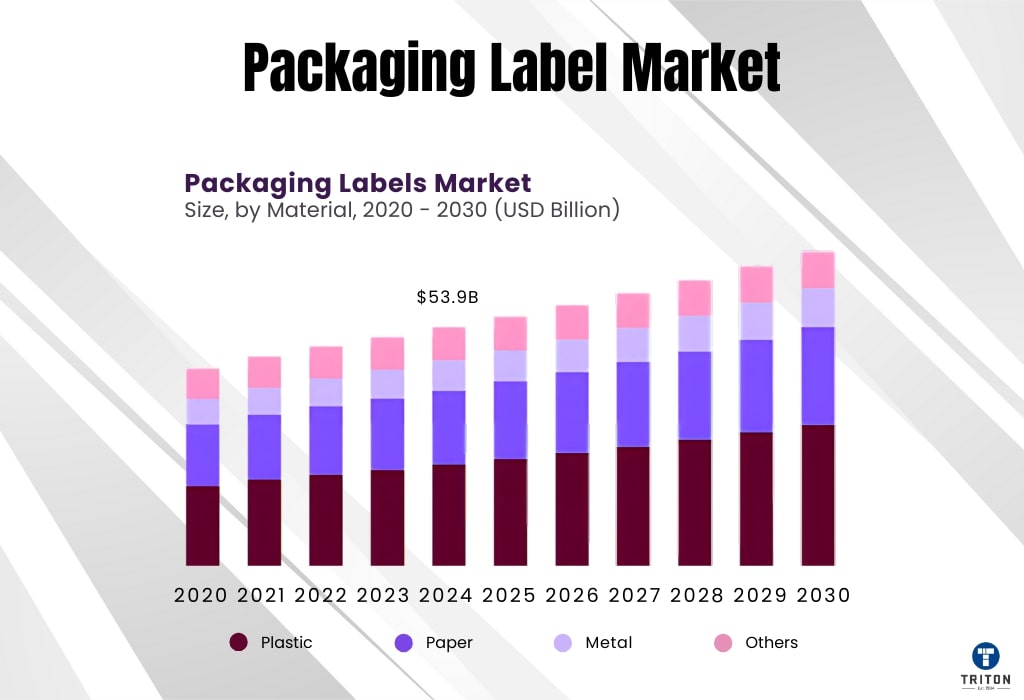
Types of Polyester & Polypropylene Labels
Not all polypropylene and polyester labels are the same. Each type is designed for specific applications based on durability, appearance, and functionality.
Types of Polyester (PET) Label
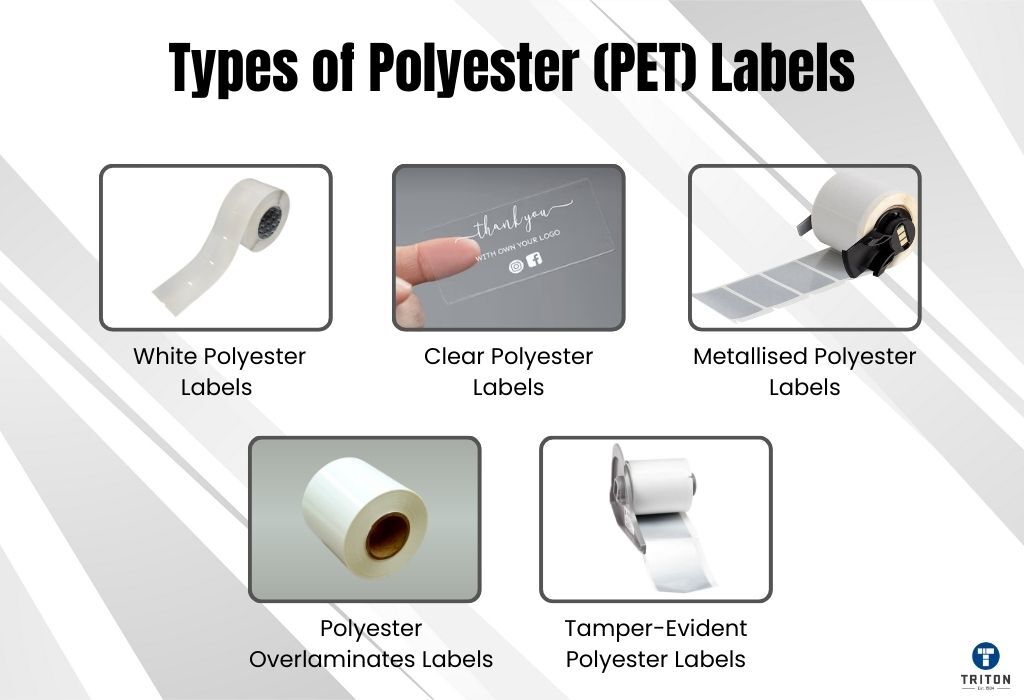
White Polyester
White polyester is the most common PET label. It is a white, opaque film available in gloss or matte finishes. It is used for asset tags, equipment labels, and rating plates. Due to its tear strength, heat resistance, and chemical durability, a 2-mil white PET label with permanent acrylic adhesive is standard for industrial labels.
Clear Polyester
This transparent PET film creates a “no-label” look or serves as a protective overlaminate. Clear PET labels do not yellow over time, so they are used as window decals or protective coatings on printed labels.
Metallic Polyester
Metalised silver, chrome, or gold PET labels provide a durable, metallic finish. Matte silver PET is common for nameplates, serial number labels, and rating plates. These labels mimic metal plates but are more flexible and cost-effective.
Tamper-Evident Polyester
When removed, this PET film leaves behind a VOID pattern or fractures. It is used for security seals, warranty protection, and calibration stickers.
Polyester Overlaminates
These are clear PET films with adhesive, used to protect labels from abrasion, chemicals, and UV exposure. A 1-2 mil PET overlaminate can significantly extend the label lifespan.
Types of Polypropylene (PP) Labels
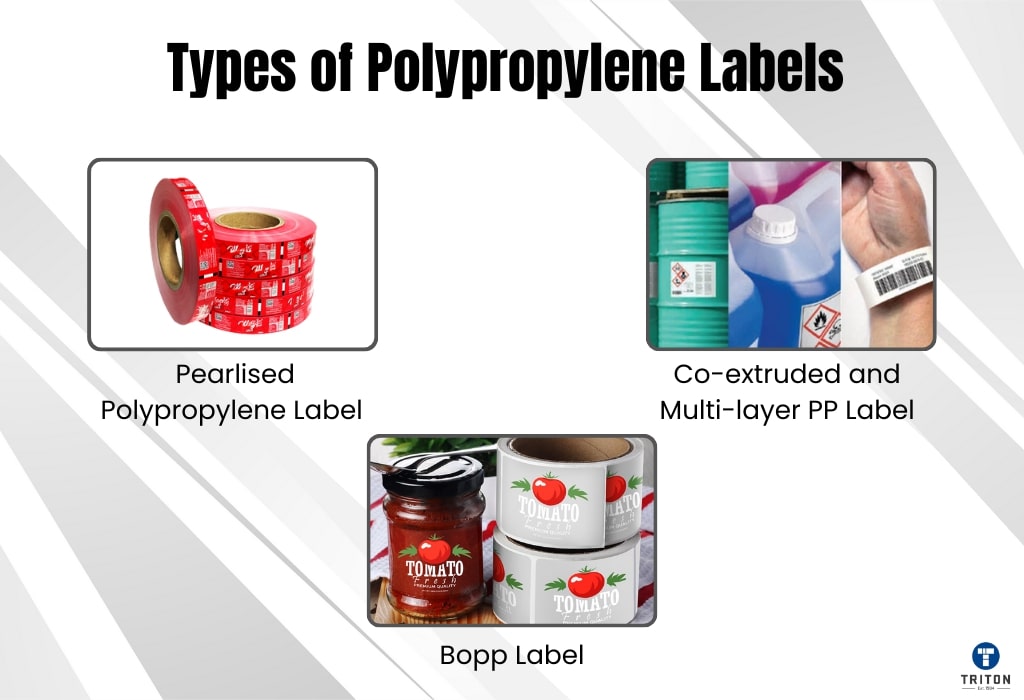
BOPP (Biaxially Oriented PP)
This is the standard PP label film. It comes in white, clear, or metallised finishes.
- White BOPP is used for food packaging and cosmetics.
- Clear BOPP creates a seamless “no-label” effect on beverage bottles.
- Metallised BOPP provides a shiny chrome look at a lower cost than metallic PET.
Pearlised Polypropylene
This shimmering, opaque BOPP is common in wrap-around labels for water and soda bottles. It is lightweight and moisture-resistant, making it ideal for refrigerated products.
Co-extruded and Multi-layer PP
Some PP films are engineered for greater durability. For example, Kimdura® labels are made of PP-based synthetic paper, which is known for its chemical and moisture resistance. These labels are tear-resistant and ideal for outdoor use.
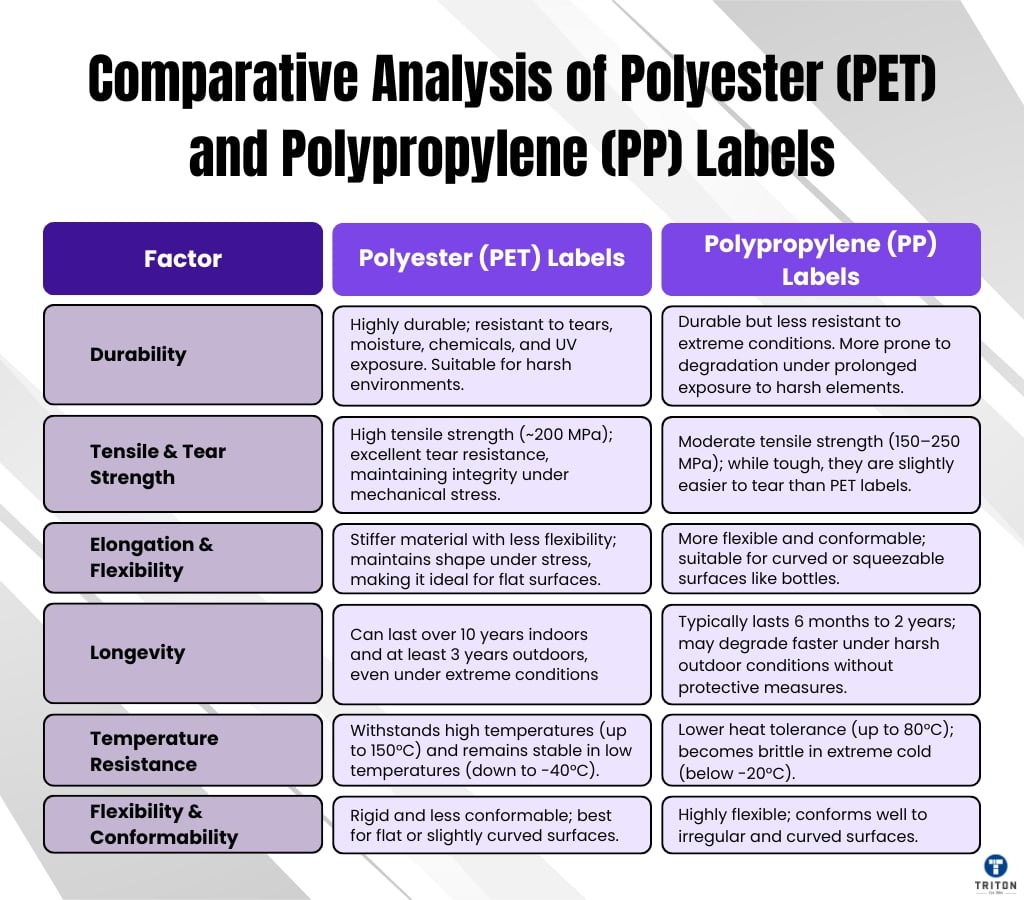
Durability
Durability determines how well a label withstands physical stress, environmental exposure, and long-term use.
Tensile & Tear Strength
Polyester labels are strong and highly tear-resistant. For example, biaxially oriented PET (BOPET) labels have a tensile strength of about 200 MPa in both machine and transverse directions.
In contrast, biaxially-oriented polypropylene (BOPP) has a tensile strength of 150–250 MPa in one direction but less in the other.
PET is more uniformly resistant to tension.
Both label materials resist tearing unless nicked, but PET labels have a higher initial tear resistance.
A 2 mil polyester facestock will not tear unless damaged, while polypropylene is tough but slightly easier to tear. This makes PET label the preferred choice for labels that must remain intact under mechanical stress, such as industrial equipment tags, asset labels, and safety markings. PP, while durable, is better suited for applications where flexibility is needed, such as food packaging and squeeze bottles.
Elongation & Flexibility
Polyester is a stiff material that resists stretching. It has a tensile modulus of about 4.5 GPa and can extend to roughly 100% of its original length before breaking. In contrast, polypropylene (PP) is more flexible. In one direction, it can stretch up to 150%, while in the other, its stretch is only about 50-100%.
Theoretically, PP will elongate slightly under force, whereas polyester maintains its shape. PET labels’ rigidity makes them reliable for applications like barcode and tracking labels, where precise printing and scanning over time depend on dimensional stability. Meanwhile, PP’s flexibility makes it ideal for labels that need to conform to curved or squeezable surfaces.
Abrasion Resistance
Polyester labels are highly resistant to scratches, scuffs, and friction, which makes them ideal for harsh environments.
For example, in a busy warehouse where shipping containers are frequently slid across rough concrete floors, polyester labels maintain their print clarity even after repeated abrasion. While polypropylene labels also resist scratches, they are less durable under high-abrasion conditions, leading to faster wear and reduced readability over time.
Longevity
Polyester labels offer exceptional longevity indoors and outdoors, maintaining legibility under harsh conditions such as rain, sunlight, and temperature extremes. This makes them ideal for applications like rating plates on industrial machinery or asset tracking on utility poles.
In contrast, polypropylene labels have a more moderate lifespan and may begin to degrade under harsh outdoor conditions without protection.
Below is a table summarising the durability characteristics:
Material | Indoor Durability | Outdoor Durability |
---|---|---|
Polyester | Very Long | Long |
Polypropylene | Medium | Short |
Print Quality
Both PET and PP labels support high-quality printing, but they differ in ink adhesion and print durability.
Ink Adhesion and Absorption
PET and PP provide smooth surfaces for high-resolution printing, but their ink adhesion differs. PET ensures sharp images and crisp barcodes, especially with resin-based thermal transfer ribbons. It also maintains accuracy under temperature and humidity changes, making it ideal for fine details. Most commercial PP labels come pre-treated for flexographic, digital, and thermal transfer printing.
What Does Higher Surface Energy Mean?Higher surface energy means that a material’s surface has a greater tendency to attract and bond with liquids like ink. In this context, PET’s higher surface energy allows ink to spread and stick better, resulting in sharper images and more durable prints. |
Unlike paper, PET and PP do not absorb ink; instead, ink dries or cures on the surface. PET’s higher surface energy improves ink adhesion, especially when coated, while PP requires treatment or a topcoat for strong anchorage. Properly coated, both perform well, but PET offers better adhesion for UV and solvent-based inks.
In digital printing (e.g., HP Indigo, inkjet), special PET and PP grades exist. However, uncoated PP can cause ink streaking unless a matte finish or primer is used. PET generally delivers more consistent digital printing results when top-coated. This makes PET the better choice for barcode labels, asset tags, and industrial applications where ink durability is critical, while PP works well for short-term packaging labels.
Printing Technologies and Print Clarity
PET and PP are compatible with flexography, UV inkjet, thermal transfer, and laser printing, but their heat resistance differs. PET withstands higher temperatures, making it ideal for laser printing and high-heat curing processes without warping. PP, with lower heat resistance, may deform under extreme temperatures, limiting its suitability for laser printing.
For thermal transfer printing, PET pairs best with resin ribbons for durable, smudge-proof prints, while PP works with wax-resin ribbons, making it more prone to scuffing unless coated or laminated. PET’s rigidity ensures high-resolution prints (600+ DPI) with sharp details, making it ideal for barcode labels and critical tracking applications.
PP, though slightly more flexible, still delivers clear prints and performs well in retail barcoding, especially for short product life cycles and branding applications. This means PET is ideal for labels requiring long-term scan accuracy and resistance to environmental stress, while PP is more suitable for consumer product labels where visual appeal is the priority.
Cost
The cost difference between polyester (PET) and polypropylene (PP) labels is significant. PP is a budget-friendly material, while PET is a premium choice. Below, we break down the key cost factors.
Raw Material Cost
Polypropylene is one of the cheapest plastics, widely used in packaging and films. Its large-scale production keeps costs low. Polyester is also mass-produced, but the type used for labels is more specialised and expensive.
BOPP labels are about three times the cost of paper labels, while PET labels can cost up to ten times more. This means a $0.01 paper label might cost $0.03 in PP and $0.10 in PET. In simple terms, PET can be about three times the price of PP for the same label size. From a raw material perspective, PET is one of the most expensive label films, while PP is among the most affordable.
Production and Conversion Costs
Both PET and PP labels use the same printing and die-cutting equipment. However, PET is a tougher, stiffer material that can dull cutting blades faster. Its rigidity means that if the die-cutting equipment isn’t specifically adjusted for PET, the material may not feed smoothly through the machinery, leading to misaligned cuts or jams.
PP has a lower melting point, making it easier to heat-seal in packaging processes. Another cost advantage is its lower density (0.90 g/cc vs. PET’s ~1.4 g/cc), which means more labels per kilogram of material. For the same thickness, PP produces 35-40% more label area per unit weight compared to PET.
Total Cost of Ownership
While PET labels cost more upfront, they can be more cost-effective in the long run. PET lasts longer, reducing the need for reprints and replacements. For example, PP labels on outdoor equipment might fade or peel within a year, requiring frequent replacement. A PET label could last 5+ years, reducing re-labelling costs and preventing errors from missing or unreadable labels.
These things make PP the economical choice for high-volume, short-term labelling applications like food and beverage packaging. At the same time, PET is preferred for high-durability needs such as industrial equipment tags, asset tracking labels, safety markings, chemical drum labels, and outdoor-rated signage.
Environmental Impact
Both PET and PP are petroleum-based plastics that do not biodegrade. However, their environmental impact varies based on recyclability, lifespan, and carbon footprint.
Carbon Footprint
Both PET and PP rely on fossil fuels and energy-intensive production, with raw material processing contributing most to their carbon footprints. PP has a lower density and melting point (~166°C vs. PET’s ~260°C), requiring less energy to process and yielding more labels per kilogram, reducing overall material use. This efficiency gives PP a lower carbon footprint per label.
However, PET’s higher recycling rates, especially with recycled PET (rPET), help offset its impact. If not recycled, both materials may be incinerated for energy recovery, though this emits CO₂.
PET and PP are chemically stable, non-toxic, and free from plasticisers, halogens, and hazardous substances. They comply with RoHS and REACH regulations, ensuring no heavy metals or restricted chemicals above 0.1%. While they do not off-gas under normal conditions, improper burning releases CO₂ and hydrocarbons, highlighting the need for controlled disposal and recycling.
This makes PET Labels the preferred choice for long-term, high-durability labelling in regulated industries, including medical devices, hazardous chemical containers, and outdoor industrial signage. PP labels, with their lower carbon footprint and high-yield production, remain the better option for cost-sensitive, short-life applications such as retail packaging, disposable food labels, and consumer goods. |
Chemical and Oil Resistance
PET and PP resist oils, but PET performs better in extreme conditions. Its aromatic polymer structure resists nonpolar hydrocarbons like engine oil and machine grease, preventing softening or swelling. PP is hydrophobic and repels oils well, but it may degrade under prolonged exposure to heavy or hot oils. For industrial applications, PET is the better choice for high-temperature or continuous oil exposure.
PET also excels in solvent resistance, withstanding acetone, toluene, MEK, and industrial degreasers while maintaining print clarity. PP resists milder solvents like alcohols but softens or distorts under strong solvents. PET is preferred for lab and industrial environments where solvent exposure is frequent, while PP is suitable for moderate conditions.
Both materials resist acids and bases, but PET remains more stable in highly aggressive environments. It withstands strong acids (sulfuric acid) and bases (sodium hydroxide) with minimal degradation. PP resists dilute acids and bases but breaks down under concentrated or high-temperature exposure. PET labels meet BS 5609 certification, ensuring durability in corrosive environments.
Temperature Resistance
Labels often face high heat, extreme cold, and rapid temperature changes. Polyester (PET) provides superior temperature resistance, while polypropylene (PP) works only in moderate conditions.
High and Low Temperature
PET labels excel in both high- and low-temperature conditions. With a melting point of 250-260°C PET remains stable up to 150°C, shrinking only 1–3% at this temperature. Speciality PET labels can endure brief exposure to 149°C without losing integrity. In industrial settings, PET withstands heat from engines, electronics, and lighting fixtures, where PP would deform or detach. Some PET labels even survive solder reflow (~260°C) in PCB applications, though polyimide is preferred for extreme heat.
PP has a much lower heat tolerance, melting at 160-166°C but softening well before that. BOPP labels typically withstand up to 80°C, but beyond 100°C, they warp or become brittle. Most PP labels are rated for a maximum of 70-80°C, making them unsuitable for high-heat applications.
In cold conditions, PET remains flexible to -40°C and does not crack easily unless sharply flexed. PP, with a glass transition temperature of ~-20°C, becomes brittle below this point. Standard PP labels function between -20°C and -29°C but may crack or delaminate at extreme cold (-40°C). At deep freeze levels (-80°C), PP shatters, while PET or polyimide labels are preferred. For freezer applications below -20°C, PET is the better choice.
Thermal Cycling, Dimensional Stability, and Flammability
PET maintains stability under temperature fluctuations, expanding minimally and staying flat when exposed to cycles of heat and cold. It resists warping, ensuring labels remain intact and legible even in environments shifting from -10°C at night to 60°C during operation. PP, however, expands and contracts more, causing wrinkling, peeling, or curling over time. It shrinks by 3-5% at 120°C, making it less reliable in fluctuating conditions.
Neither PET nor PP is naturally flame-resistant. Both burn or melt in a fire, but PET chars and shrinks slightly, while PP melts and produces flaming droplets. PET has a higher limiting oxygen index (LOI), making it slightly less flammable. However, for fire-resistant applications, polyimide or flame-retardant polyester is required, as standard PET and PP labels are combustible.
This makes PET labels the preferred choice for high-temperature applications such as engine components, industrial machinery, and electronics, where labels must endure extreme heat without warping or detaching. PP labels, with their lower heat tolerance, are better suited for moderate-temperature environments like food packaging, refrigerated storage, and general consumer labelling. |
Flexibility
Flexibility determines how well a label conforms to curves, bends, and squeezes without lifting or cracking.
Material Stiffness and Conformability
PET is about 80% stiffer than PP, with Young’s modulus of ~4,500 N/mm² compared to PP’s ~2,500 N/mm². This rigidity makes PET ideal for flat or gently curved surfaces like equipment plates, large pipes, and electronics but less suitable for curved or flexible surfaces. PP, being more flexible, wraps smoothly around curved bottles and semi-squeezable containers like shampoo bottles, reducing the risk of lifting. PET does not stretch, so on flexing surfaces, it may bubble or detach. PP labels remain thinner for flexibility, while PET labels often include protective overlaminates, further increasing stiffness.
Bending and Tear Resistance
PP handles repeated bending better than PET, making it ideal for applications requiring movement, such as power cords. PET, being stiffer, can develop stress cracks when sharply folded. Some speciality PET labels use micro-cuts or ultra-thin layers for flexibility, but PP remains superior in bending resistance.
At the same thickness, PP is always more flexible. PP labels (50-100 µm) conform well to curved surfaces, while PET labels (50 µm) remain relatively rigid. Cast PP or polyethylene facestocks offer extreme conformability for wrapping around wires or vials. PP stretches slightly before tearing, making it more ductile, while PET resists stretching but snaps under high tension.
This makes PET labels ideal for flat or gently curved surfaces like equipment plates and electronics, ensuring stability and durability. PP labels, with greater flexibility, are better suited for curved bottles, semi-squeezable containers, and applications requiring repeated bending. |
UV Resistance (Resistance to Sunlight/UV Degradation)
Exposure to ultraviolet (UV) light from the sun can degrade plastics, causing brittleness, discolouration, and loss of strength.
Polypropylene and UV Degradation
Unstabilised PP degrades rapidly under UV exposure due to its carbon-hydrogen backbone, which is prone to oxidation. This leads to cracking, chalking, and embrittlement. Studies show that PP fibres lose ~70% of their tensile strength within six days of high-intensity UV exposure. Standard PP without UV stabilisers can become brittle within months, often yellowing or flaking off.
For this reason, PP labels are mainly recommended for indoor or short-term outdoor use. When used outdoors, UV stabilisers like HALS (hindered amine light stabilisers) or UV absorbers (e.g., titanium dioxide) help slow degradation, though PP’s UV resistance remains lower than PET. Some premium PP films are designed for extended outdoor use, lasting up to five years – comparable to vinyl labels. However, most standard PP labels degrade within 1-2 years in direct sunlight before becoming brittle.
Polyester and UV Resistance
PET’s aromatic polymer structure absorbs less UV radiation, making it more UV-resistant than PP. Studies show PET retains ~67% of its strength after 12 months of sun exposure, lasting years before degrading. Unlike PP, PET resists yellowing and embrittlement, with many labels rated “UV-stable” for outdoor use. This durability makes PET ideal for solar panel tags, electrical boxes, and asset labels.
PET label’s UV resistance makes them the preferred choice for long-term outdoor applications like solar panel tags, electrical boxes, and asset labels, where UV resistance is critical. PP labels, while suitable for indoor and short-term outdoor use, require stabilisers for extended exposure and degrade faster under sunlight. |
Water Resistance
Both PET and PP are waterproof and highly resistant to moisture. PP is fully hydrophobic, absorbing less than 0.1% water even after days of immersion. PET, due to its slightly polar ester groups, absorbs around 0.5%, but this minimal difference does not impact labelling performance. In extreme humidity-sensitive applications, PET may undergo slight dimensional changes, which are negligible for most uses.
PP labels are commonly used in wet environments, such as bath and body products, as they remain intact despite splashes or condensation. PET labels, however, are preferred for marine and outdoor applications due to their superior resistance to prolonged moisture exposure, salt spray, and fluctuating temperatures.
PET also meets BS 5609 certification, which requires surviving three months of saltwater immersion, while PP typically fails due to adhesive breakdown or film degradation.
Under high heat and humidity, PET can undergo hydrolysis, where its ester bonds weaken over long periods (e.g., months at 60°C and 90% humidity), leading to brittleness or hazing. Special hydrolysis-resistant PET grades exist for applications like dishwashers or autoclaves. PP does not hydrolyse but may develop environmental stress cracks when exposed to detergents in wet conditions. Despite this, PET is more resistant to detergent-related stress cracking.
For wet environments, adhesive selection is crucial, as failure is usually due to adhesive breakdown rather than film degradation. PET and PP labels with strong acrylic adhesives maintain adhesion in rain and washing, ensuring durability even in submerged conditions.
Regulatory Compliance
Industrial labels must meet strict regulatory and safety standards. Below are key standards and label materials
Australia & New Zealand Regulations (Safe Work Australia, AS/NZS 3808)
In Australia and New Zealand, regulatory standards mandate that labels withstand harsh environmental conditions. Guidelines from Safe Work Australia and AS/NZS 3808 favour PET labels for their excellent weather resistance, high UV stability, and durability under moisture and temperature extremes. These properties make PET ideal for outdoor applications such as industrial asset tracking and signage where long-term legibility is critical.
ISO Standards (International)
ISO 28219 sets durability requirements for product labels, ensuring resistance to abrasion, humidity, and heat. PET meets these standards due to its superior durability. ISO 2230, which governs equipment storage labelling, also favours PET for long-term stability.
UL Standards (USA, Globally Recognized)
UL 969 certifies appliance labels, safety signs, and equipment, testing resistance to extreme temperatures, moisture, chemicals, and UV exposure. PP labels are mainly UL-approved for indoor use.
RoHS & REACH (EU Regulations)
Both PET and PP comply with RoHS, excluding hazardous substances like lead and cadmium. They also meet REACH standards, as their base polymers contain no restricted chemicals.
Regional Labeling Standards
- USA (OSHA 29 CFR 1910.1200): Hazard labels must remain legible; PET is preferred for durability.
- Canada (WHMIS 2015, HPR): PET is commonly used for chemical containers and outdoor signs.
- UK/EU (CLP, BS 5609): PET meets BS 5609 certification for 90-day saltwater immersion.
- Australia/New Zealand (Safe Work Australia, AS/NZS 3808): PET is favoured for weather-resistant labels, especially in high UV conditions.
Use Cases and Applications
Durable Asset & Equipment Labels
PET labels are essential in manufacturing, mining, oil & gas, and automotive industries, where labels must withstand heat, chemicals, abrasion, and UV exposure. They are used for machinery nameplates, serial tags, and rating plates. Automotive under-hood labels endure up to 150°C, resisting oil and grime. Electronics rely on PET for power supplies, hard drives, and circuit boards. Laboratories use PET barcode labels for chemical resistance, while outdoor applications, such as utility poles and telecom boxes, require PET for long-term weather durability.
Barcode Accuracy & Asset Tracking
PET is preferred for warehouse rack labels and asset tags due to dimensional stability. Retro-reflective PET labels enable long-range barcode scanning. Equipment tracking labels on tools and computers require PET for durability. Calibration stickers also use PET to ensure readability over time.
Cost-Effective Packaging & Consumer Labels
PP dominates food, beverage, and cosmetic packaging due to its affordability and moisture resistance. BOPP labels provide a glossy finish, with most Coca-Cola and Pepsi labels using clear BOPP for a seamless look. Shampoo, lotion, and sauce bottles use PP for oil and refrigeration resistance.
Medical & Pharmaceutical Labels
PP is widely used for medical and pharmaceutical labels, including those on medicine bottles, IV bags, and blood bags, due to its flexibility and chemical resistance. PET is chosen for reagent bottles requiring higher chemical durability.
Short-Term Durable Labels
PP is suitable for temporary labels, such as warehouse pallet tags and work-in-process labels, where short-term durability is needed at a lower cost.
Case Studies
Here are two company examples highlighting their best-use scenarios. These scenarios compare the real-world performance and cost-effectiveness of PET and PP labels.
Industrial Rack Labeling
A Las Vegas warehouse required durable barcode labels for 67,500 racks and 350,000 shelves. ASG Services installed PET labels for long-term scan reliability, resisting forklift contact, UV exposure, and temperature shifts. While PP labels were cheaper initially, PET’s abrasion resistance and stability prevented frequent replacements, reducing costs over time.
Beverage Labels
Major brands like Coca-Cola and Pepsi use BOPP labels for water and soda bottles due to their water resistance, durability, and cost-effectiveness. Unlike paper labels, these labels withstand ice buckets, refrigeration, and frequent handling without peeling or weakening. A 500 mL bottle typically features clear or pearlised BOPP, providing flexibility and vibrant printing for brand visibility. PET labels would outlast the product’s short lifecycle, increasing costs unnecessarily.
Conclusion
Choosing the right material depends on lifecycle demands, environmental exposure, and budget. Understanding these differences enables businesses to select the most effective labelling solution for their requirements. With the information and data provided here, professionals can make an informed decision or specification that meets their operational needs and industry standards.