Warehouse labels are integral components of an efficient inventory and storage management system. These labels serve as visual and scannable identifiers and provide essential information about the contents, location, and handling of items within a warehouse.
Moreover, warehouse labels are pivotal in streamlining operations, reducing errors, and ensuring quick access to goods. From simple paper tags to sophisticated barcode or RFID-enabled labels, these tools facilitate seamless tracking, picking, and inventory control.
This blog post delves deep into the art and science of choosing the right warehouse labels. From probing questions guiding your initial decisions to factors influencing your final choice, we’ll embark on a comprehensive journey to demystify the world of warehouse labelling.
So, let’s get started.
Questions to Ask Before Choosing Warehouse Labels
Navigating the myriad options available for warehouse labelling can be a daunting task. The right label can streamline operations, enhance efficiency, and reduce costly errors. In contrast, an ill-suited choice can lead to the opposite.
Before diving into the selection process, you must understand your warehouse’s unique needs and challenges.
In this section, we present pivotal questions to guide your decision-making, ensuring that the labels you choose align seamlessly with your operational demands and long-term goals.
- What specific environments (e.g., indoor, outdoor, cold storage) will the labels be exposed to?
- How long do I expect the labels to last before they need replacement?
- Do the labels have to be permanent or removable?
- Will the labels need to withstand specific conditions such as UV exposure, moisture, or chemical contact?
- What type of information will the labels need to convey, and how detailed should they be?
- Will the labels be used with specific scanning technologies like barcodes or QR codes, and what is the expected scanning range?
- How frequently might I need to update or change the labels?
- Do I require labels with special adhesive qualities, such as those that can be easily repositioned or those that leave no residue upon removal?
- What is the size and shape of the surfaces where the labels will be applied?
- Will the labels need to comply with any industry-specific regulations or standards?
Factors to Consider When Choosing Warehouse Labels
Let’s delve into the crucial factors you should consider when selecting warehouse labels, ensuring your choice aligns perfectly with your operational needs and goals.
Location of Labels
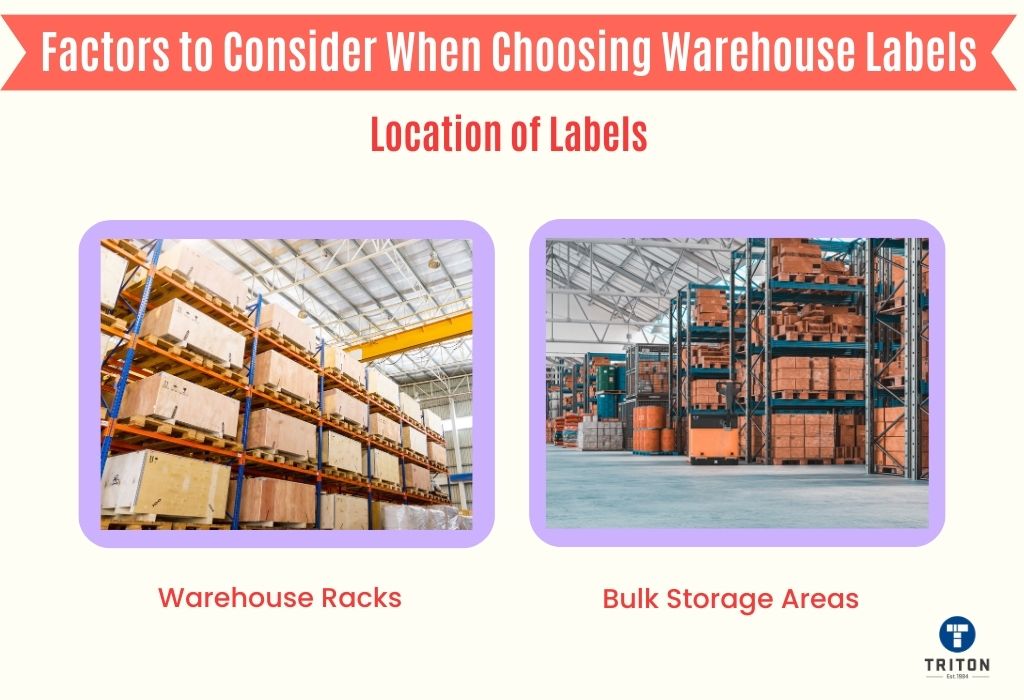
In the vast expanse of a warehouse, the strategic placement of labels is not just a matter of convenience but a critical component in optimising operations.
The location of labels significantly impacts the efficiency of inventory management, product retrieval, and overall workflow through quick identification of products, efficient space utilisation, and reduced errors in product management.
There are two main storage systems (based on location) that can be found in a warehouse –
- Warehouse racks
- Bulk storage areas
Warehouse Racks
Warehouse racks are storage solutions for storing, organising, and managing inventory. These racks are made of metal, wood, or other materials designed to hold goods in an organised manner, maximising the warehouse’s storage capacity.
Warehouse racks come in variations like single-level racks and multi-level racks. Both have different labelling requirements as follows –
- Single-level rack labels – Appropriate for racks where items are stored at one consistent level.
- Multi-level rack labels – Designed for racks that house items across multiple tiers, making it easier to identify multiple racks with a single glance.
Bulk Storage Areas
Bulk storage spaces are where large quantities of products, often in pallets or containers, are stored. To facilitate efficient inventory management and quick identification in these areas, it’s crucial to have clearly visible labelling systems in place.
This is where bulk storage labels like container labels, pallet labels, floor labels, and hanging signs come into play. However, these labels must be prominently displayed, ensuring they’re visible even from a distance.
Check out our comprehensive guide to types of warehouse labels to learn more about the different types of warehouse labels like pallet labels, floor labels, tote/bin labels, etc.
Container Labels
Container labels are designed to provide detailed information at a glance, ensuring swift identification. They often incorporate barcodes or QR codes, allowing for quick scanning and inventory management.
The adhesive used in these labels is chosen to withstand the conditions typical of container storage, ensuring longevity and readability.
Barcode and QR codes are two different technologies that are often confused and used interchangeably. Check out our article on barcode vs. QR code to learn the differences.
Pallet Labels
Pallet labels are attachable labels that are affixed to pallets used in storage and shipping. These labels contain essential information that helps in the identification, tracking, and management of the goods stored on the pallet.
Pallet labels are designed to endure the rigorous wear and tear associated with the pallets’ constant movement. But durability isn’t their only feature. These labels are also designed to provide a wealth of information, from the contents of the pallet to batch numbers, expiry dates, and more.
The placement of pallet labels is strategic, ensuring they’re easily scannable even when the pallet is stacked.
Floor Labels
A warehouse floor bears the brunt of foot traffic, machinery movement, and the weight of stored goods. Floor labels, therefore, are made from materials (like vinyl) that can resist abrasion, fading, and the impact of heavy objects.
Beyond durability, floor labels are crucial role in guiding warehouse personnel, demarcating zones, and aiding in the quick location of goods. Their design often incorporates high-contrast colours and large fonts to ensure visibility.
Hanging Signs
In warehouses with high ceilings and multi-tiered storage, hanging signs are indispensable.
Suspended from the ceiling, hanging signs serve as navigational aids, guiding staff to specific aisles or sections. They’re especially vital for items stored at great heights, ensuring that even products out of arm’s reach are easily identifiable.
Hanging signs often incorporate retro-reflective properties to be visible from a distance and readable under various lighting conditions.
Scanning Range
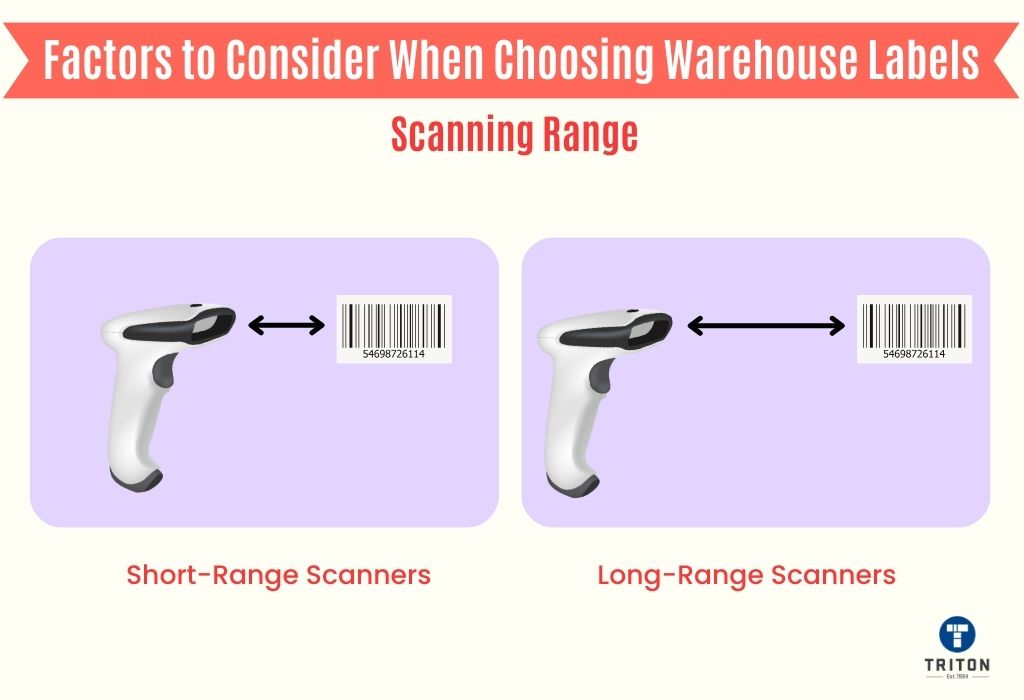
The efficiency of warehouse operations often hinges on the speed and accuracy of scanning.
The scanning range, determined by the types of barcode scanners and the placement of labels, helps ensure accuracy, reducing the physical strain on the warehouse employees, and efficient movement of products.
Choosing the right barcode scanner can be confusing, given the variety of types and models available in the market. Our guide on how to choose a barcode scanner will come in handy.
Short-Range Scanners (3-15 feet)
Label | Range (in feet) | Range (in centimetres) |
---|---|---|
Pallet labels
| 3 – 8 ft | 91.4 – 243.84 cm |
Floor labels
| 5 – 8 ft | 152.4 – 243.84 cm |
Rack level label | 5 – 10 ft
| 243.84 – 304.8 cm |
Multi-level rack label
| 10 ft
| 304.8 cm
|
Rack level 2 label
| 10 – 15 ft
| 304.8 – 457.2 cm
|
Short-range scanning labels are designed for close-quarters scanning. They are particularly effective for items stored at eye level or on the lower racks.
Given the range of short-range scanning labels, they are best suited for warehouses where the majority of goods are easily accessible and don’t require extended scanning capabilities.
The advantage of short-range scanners lies in their precision at close distances, ensuring that the right item is identified without interference from neighbouring labels.
Labels on one- or two-level racks, which are within arm’s reach, are best paired with short-range scanners.
Long-Range Scanners (up to 50 feet)
Label | Range (in feet) | Range (in centimetres) |
---|---|---|
Rack level 3 labels | 15 – 20 ft
| 457.2 – 609.6 cm |
Rack level 4 labels
| 20 – 30 ft
| 609.6 – 914.4 cm
|
Hanging sign
| 20 – 50 ft
| 609.6 – 1524 cm
|
For warehouses with tall storage racks or items stored at elevated levels, long-range scanning labels become indispensable.
Long-range scanning labels can accurately be read from significant distances, ensuring that even items placed at great heights are easily identifiable. This eliminates the need for manual retrieval or closer inspection, thereby speeding up the inventory management process.
Labels on higher rack levels, hanging signs, or those in hard-to-reach areas necessitate long-range scanning solutions. This ensures that the scanning process remains efficient, even when physical access to items is limited.
When it comes to barcode scanners, there’s no shortage of options out there. But at Triton, we’re proud to offer a selection of reliable, truly top-of-the-line barcode scanners created by well-known brands like Zebra and Honeywell.
Our barcode reader range includes the latest models of mobile terminals, general barcode scanners, rugged barcode scanners, fixed scanners & sensors, wireless barcode scanners, 2D barcode scanners and Bluetooth barcode scanners.
With sturdy materials and advanced features, you can count on our scanners to perform reliably for years on end. And, to make sure you’re always up and running, we also carry a full line of scanner accessories and spare parts.
So whatever your scanning needs may be, Triton has you covered. Shop our selection today to see the difference for yourself!
Environment of Storage
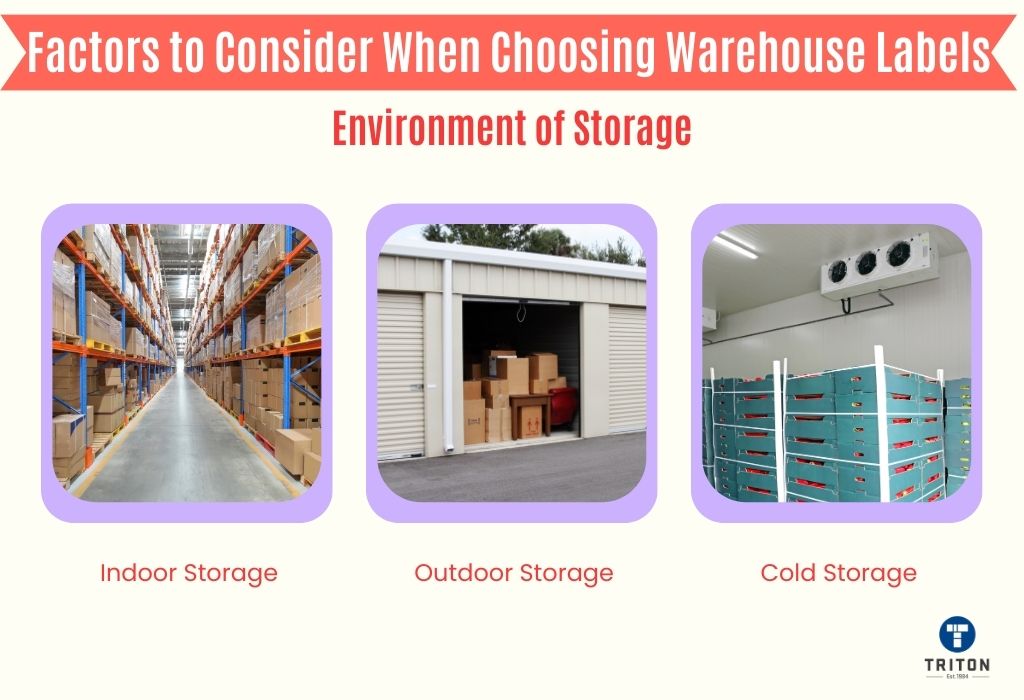
The environment (humid, cold, or hot) within which warehouse labels operate is a critical determinant of the labels’ design, material, and adhesive properties. Different storage conditions demand labels tailored to withstand specific challenges, ensuring longevity, readability, and adherence.
Following are the three types of storage environments and their specific requirements –
Indoor Storage
For indoor warehouses, labels must be durable to withstand routine wear and tear.
Indoor labels are usually made from materials (like polyester or paper) that can endure the usual indoor conditions, such as dust, humidity variations, and regular handling. Polyester labels also provide a balance between strong adherence and the possibility of repositioning if needed.
While indoor labels might not need to withstand extreme conditions, their durability in a controlled environment is paramount to ensure consistent operations.
Outdoor Storage
Warehouses or sections of warehouses exposed to nature’s elements require labels with different properties. These labels must be weather-resistant and capable of withstanding challenges like UV rays, rain, snow, and temperature fluctuations.
Often made of materials (like polypropylene) that repel water and resist fading, outdoor labels ensure that even when exposed to the outdoors, the information remains clear and accessible. These are weather-resistant labels with specialised adhesives ensuring longevity and readability, even when exposed to challenging outdoor conditions.
Cold Storage
Storing items in freezers or cold storage areas presents unique challenges. Labels in such cold environments must be specially made to endure extremely cold temperatures. This pertains to the label material and the adhesive, which must remain sticky and effective even in the cold.
Additionally, cold storage labels should resist moisture buildup, which is common in cold storage areas, ensuring that they don’t peel off or become unreadable due to frost.
A few examples of cold storage labels are – freezer-grade paper labels, cold temperature adhesive labels, etc. These labels are highly adhesives designed to remain sticky and effective, ensuring the label stays affixed and legible, even in freezing conditions.
Material of the Labels
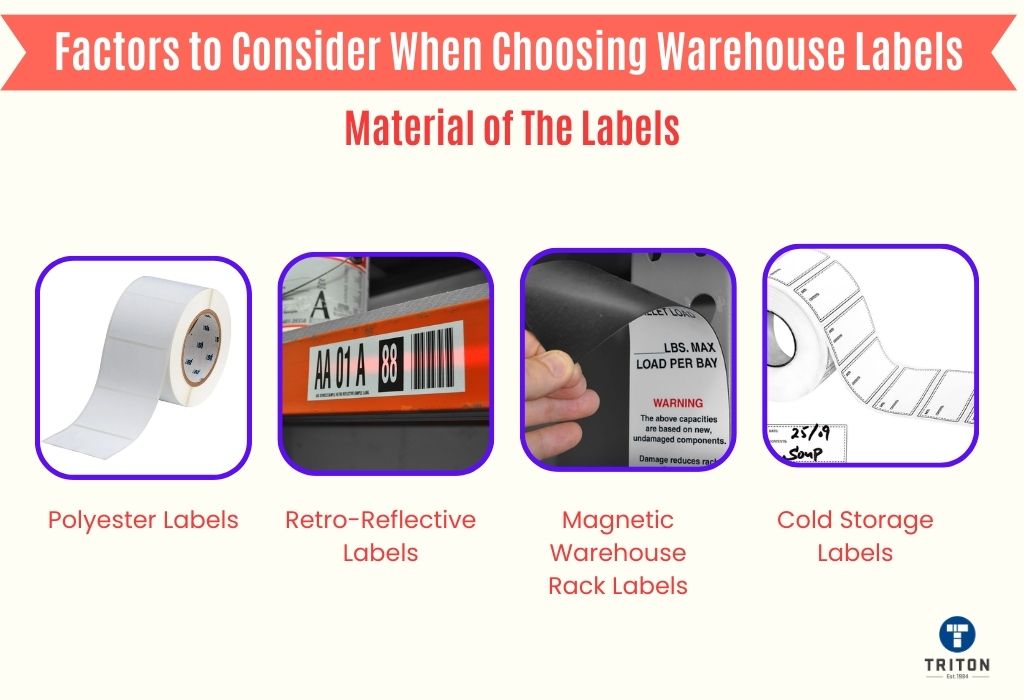
The material determines not only the label’s durability but also its applicability in various environments. Here’s a deep dive into the materials commonly used for warehouse labels and their properties:
Polyester Labels
Polyester labels are durable, water-resistant adhesive tags made from synthetic polymer materials. These labels are renowned for their ability to withstand environmental challenges like dust, moisture, etc.
Polyester labels are among the most versatile labels used in standard warehousing environments and are particularly favoured for their durability.
Polyester labels are the go-to choice for assets and inventory stored at eye level or on the first and second rack levels. They can withstand a warehouse’s general wear and tear and are resistant to moisture and chemicals.
Retro-Reflective Labels
Retro-reflective labels are specialised labels designed to reflect light back to its source, regardless of the angle at which the light hits the label. They are made using tiny glass beads or prismatic structures that bounce light back towards their origin. This property makes them highly visible even from a maximum distance of 50 feet.
Retro-reflective labels are designed for locations harder to reach with standard scanners, such as the third or fourth-level racks.
Magnetic Warehouse Rack Labels
Magnetic warehouse rack labels are labels designed with magnetic backing. This allows them to be easily attached to metal surfaces, such as the metal beams or uprights of warehouse racks, without the need for adhesive.
Magnetic labels offer a flexible solution for warehouses that frequently change their inventory or layout. These labels can be easily relocated, ensuring the labelling system remains accurate even as the warehouse setup evolves.
Cold Storage Labels
Cold storage labels are specially designed adhesive labels that can withstand the extreme temperatures and conditions commonly found in cold storage environments. These environments include refrigerators, freezers, and cold storage warehouses where temperatures range from slightly above freezing to below zero.
Cold storage labels have special, all-temperature adhesive properties, ensuring they remain affixed and legible even in sub-zero conditions.
Tips to Implement an Effective Labelling System
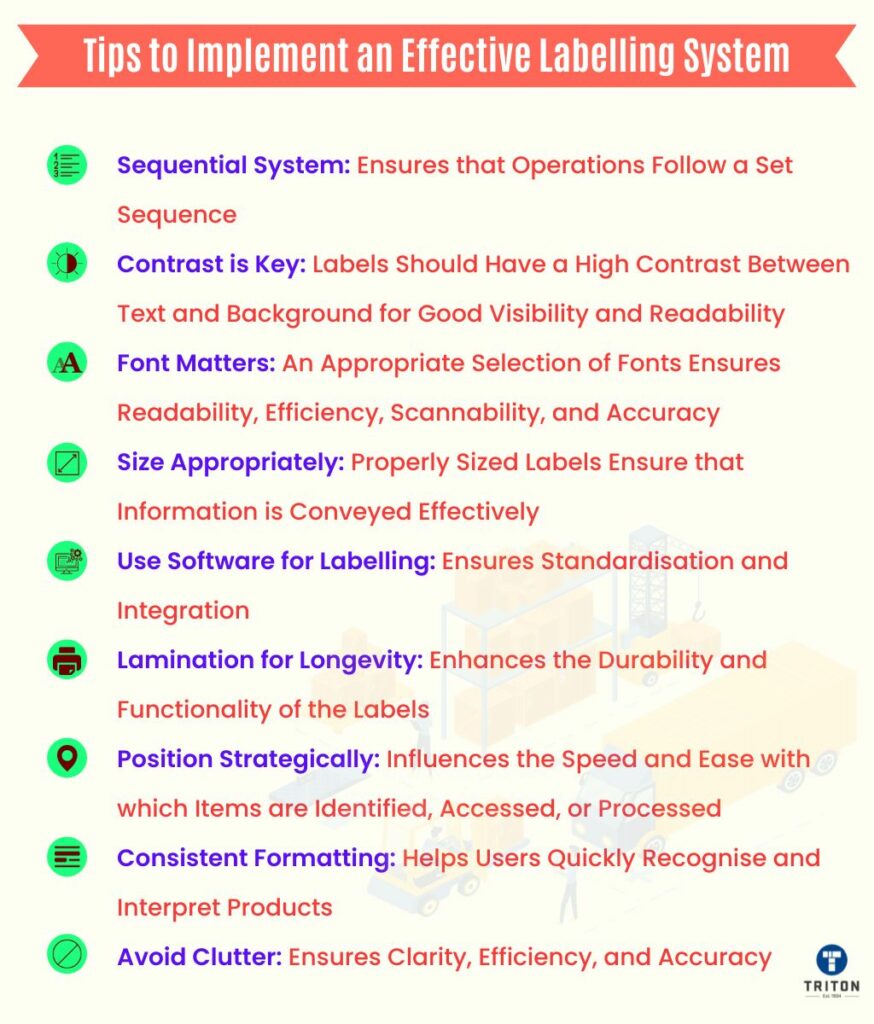
The efficiency of a warehouse rack labelling system hinges on the clarity and legibility of the labels. Here are some tips to guarantee that your labels stand out and are effortlessly decipherable:
Sequential System
At the heart of an organised warehouse is a well-thought-out sequential system.
A sequential system refers to a method of organising and executing tasks in a specific, predetermined order. This system ensures that operations follow a set sequence, which can help streamline processes, reduce errors, and improve efficiency. A sequential system includes the picking process, inventory replenishment, order of operations, batch processing, and zone picking.
By numbering aisles, racks, shelves, and bins in a logical sequence, you pave the way for intuitive navigation. This systematic approach reduces the time employees spend searching for items, leading to faster retrieval and reduced errors.
Contrast is Key
Labels should have a high contrast between text and background. This contrast is crucial for several reasons:
- Visibility: High contrast ensures that the text stands out clearly against its background, making it easier to spot and read, especially from a distance.
- Readability: The human eye can distinguish high-contrast combinations more efficiently, reducing the time and effort required to read the label.
- Scanner Compatibility: Many barcode scanners and optical devices work best with high-contrast labels. The difference in reflectivity between the dark and light areas helps the scanner detect and interpret the barcode accurately.
- Reduction of Errors: Mistakes are costly in environments like warehouses or stores. High contrast labels reduce the chances of misreading, ensuring that items are correctly identified, picked, and shipped.
Black text on a white background or white text on a black background is a classic combination that ensures readability from a distance.
Some other colours that you can consider for your labels are – red (warning labels), blue (general identification labels), green (safety information), etc.
Avoid using the same colours (e.g. light blue and dark blue) on warehouse labels, as it can lead to confusion, inefficiencies, and even costly mistakes.
Font Matters
Font choice in warehouse labels is crucial for various reasons, primarily revolving around readability, efficiency, scannability, and accuracy in operations.
When selecting fonts for optimal readability and clarity, Sans Serif fonts are often the top choice due to their clean lines devoid of additional embellishments. Notable examples of such fonts include Arial and Helvetica.
On the other hand, while decorative fonts like Comic Sans or Brush Script bring a unique flair, they can compromise readability, especially in a warehouse setting where quick information retrieval is paramount.
Additionally, in situations where alignment is crucial, fixed-width or monospace fonts, such as Courier New, are beneficial. These fonts allocate equal space for each character, ensuring a consistent and neat presentation.
Size Appropriately
Label size isn’t just a matter of aesthetics; it’s a critical component that directly impacts operational efficiency.
Properly sized labels ensure that information is conveyed effectively, reducing errors and streamlining processes.
Recommendations
- Modular Sizing: Adopt a modular approach to label sizing, where standard sizes are defined based on the type of item (pallet, bin, box) and the information content.
- Test and Iterate: Before finalising a size, it’s beneficial to run tests in real operational conditions. This can help identify any visibility or scanning issues that might not be apparent in design mock-ups.
- Integrate with Software: Modern Warehouse Management Systems (WMS) often have label printing integrations such as Triton Stock Scan, a leading solution designed for food manufacturers and cold storage environments. Ensure that the label sizes are optimised for the software’s output, reducing the need for manual adjustments.
Use Software for Labelling
Using labelling software in warehouse operations is of paramount importance for a multitude of reasons.
Firstly, it ensures standardisation across all labelling processes. This uniformity is crucial as it reduces confusion and ensures that every employee, regardless of tenure or experience, can interpret label information quickly and accurately.
Integration with Warehouse Management Systems (WMS) is another significant advantage. Modern labelling software can seamlessly synchronise with a WMS, allowing for automatic data transfer like product details, stock levels, and location to labels. This integration minimises manual input, thereby reducing the potential for human errors.
Hence, to achieve seamless inventory management, the use of specialised labelling software can be a game-changer, ensuring both consistency and precision in the creation and printing of labels.
One prime example that stands out in this regard is Seagull Scientific’s BarTender Software. This top-tier software specialises in the design, printing, and automation of labels, barcodes, and RFID tags. Not only does it offer a high degree of accuracy, but it’s also scalable to meet the needs of businesses of all sizes.
At Triton, we are proud to offer a comprehensive range of BarTender Software editions. Our selection includes the Starter Edition, Professional Edition, Automation Edition, Enterprise Edition, and the latest addition to the BarTender family, BarTender Cloud.
By providing various options, we empower you to choose the best-suited version for your label printing tasks, ensuring that you can maximise the potential of your software. Partner with Triton to enhance your label printing experience, and let us help you find the ideal fit.
Lamination for Longevity
Laminating labels significantly enhances their durability and functionality by providing a protective layer against environmental factors like moisture, dust, and chemicals. This ensures that the labels remain legible and intact over time, even in high-traffic or frequently-handled situations.
Additionally, laminated labels are UV-resistant, making them suitable for outdoor or sunlit areas.
Beyond durability, lamination also improves the aesthetic quality of labels, offering a polished and professional look that can positively impact brand perception.
Position Strategically
The strategic placement of labels has a profound impact on the efficiency and accuracy of inventory management, as well as on overall safety.
To optimise visibility and readability, labels should be positioned at eye level or natural angles for viewing. This minimises the time workers or customers spend searching for information, thereby expediting decision-making and task execution.
In addition to enhancing efficiency, well-placed labels can significantly reduce errors.
Labels should never be haphazardly placed or obscured by other items. In settings like warehouses, where precision is crucial, poorly placed labels can lead to costly mistakes such as mis-shipments or inventory discrepancies. Therefore, labels should be placed in a consistent, standardised location on each pallet or container to avoid confusion.
Strategically positioned labels also serve a vital role in enhancing safety. For example, labels marking hazardous areas should be prominently displayed at multiple vantage points to ensure maximum visibility. Similarly, labels providing essential instructions or safety guidelines should be placed where they are most likely to be seen and read, such as near control panels or entry and exit points.
Consistent Formatting
When every label adheres to a uniform format, it creates a predictable pattern that users can quickly recognise and interpret. This predictability reduces cognitive load, allowing workers, customers, or users to process information faster and more accurately.
Avoid Clutter
Avoiding clutter on labels is essential for ensuring clarity, efficiency, and accuracy in any environment where quick information retrieval is crucial.
A cluttered label containing excessive details or disorganised content can be difficult to decipher, leading to delays and potential misinterpretations. Especially in fast-paced settings like warehouses or retail stores, users rely on labels to provide immediate and clear insights.
When a label is cluttered, it increases the cognitive load on the user, forcing them to sift through extraneous information to find what they need. This not only slows down processes but also heightens the risk of errors.
Regular Maintenance
Regular maintenance of labels is vital for maintaining operational efficiency and accuracy.
Labels exposed to wear and tear, especially in challenging environments, can become illegible, leading to errors in tasks like inventory management or order fulfilment. In precision-dependent settings like warehouses, degraded labels can result in mistakes, raising operational costs and affecting customer satisfaction.
Furthermore, outdated or unreadable labels can convey incorrect information, potentially causing inefficiencies or safety hazards.
Why are Warehouse Labels Important?
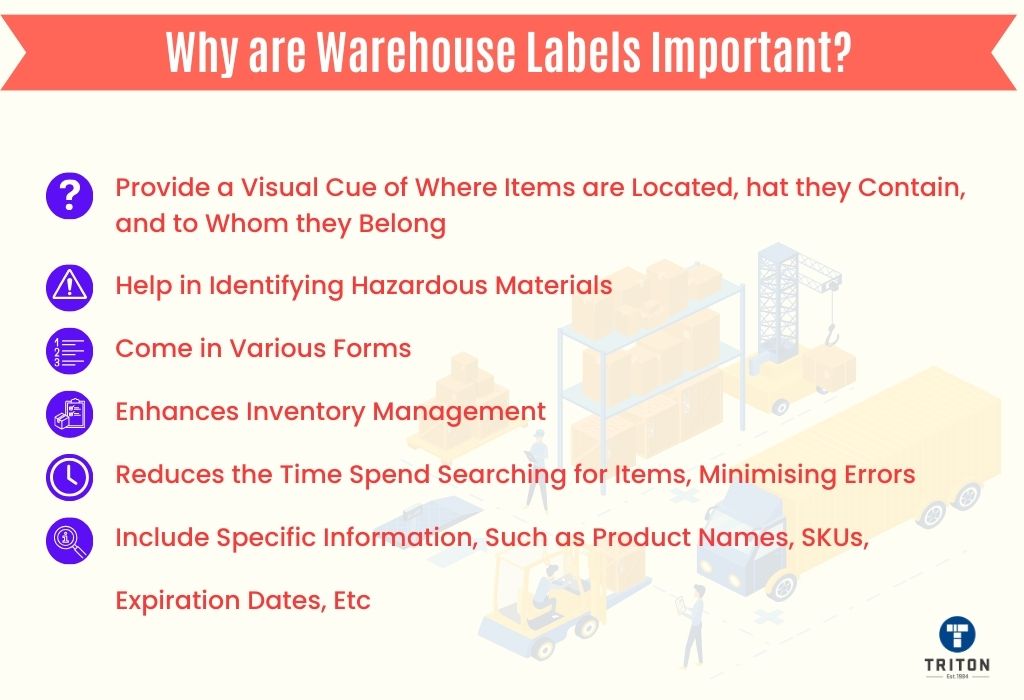
Warehouse labels are an integral part of an efficient warehouse management system. They serve as visual indicators that guide employees, streamline processes, and enhance the overall organisation of the warehouse. Here’s a deeper dive into their purpose:
- Visual Indicators: Labels provide a visual cue of where items are located, what they contain, and to whom they belong. This clarity is essential for quick and efficient operations, ensuring employees can locate items without unnecessary delays.
- Safety and Compliance: Labels are not just about organisation. They also play a crucial role in safety. They help identify hazardous materials, ensuring that the warehouse complies with safety regulations.
- Diverse Forms for Different Needs: Warehouse labels come in various forms, including barcodes, QR codes, stickers, and magnetic signs. The choice of label depends on the warehouse’s size and the nature of the items stored.
- Improved Inventory Management: An effective labelling system enhances inventory management. Labels facilitate tracking inventory levels, reducing stock shortages, and ensuring accuracy in inventory counts.
- Increased Productivity: Clear and organised labelling significantly boosts productivity. It reduces the time employees spend searching for items, minimising errors, especially in large warehouses where small mistakes can lead to substantial disruptions.
- Customisation: Modern warehouse labels can be tailored to include specific information, such as product names, SKUs, expiration dates, and more. This customisation ensures that employees have all the necessary information at their fingertips, eliminating the need to refer to external systems or databases.
- Streamlined Processes: Labels play a pivotal role in streamlining various warehouse processes, from stocking and picking to packing. Quick access to information via labels can expedite these operations and reduce errors.
Frequently Asked Questions
How to Perform Effective Warehouse Labelling?
To achieve effective warehouse labelling, follow these steps:
- Determine the Rack Types: Different racks, like tall pallet racks or smaller bin racks, require different label sizes based on accessibility and visibility requirements.
- Prepare the Racks: Clean the racks to ensure proper label adhesion. This includes removing dirt, grease, or rust. Repainting might be necessary for worn-out racks, and a protective layer can enhance label longevity.
- Select Suitable Labels: Choose labels based on the warehouse’s environmental conditions. For instance, cold storage areas need labels resilient to low temperatures, while sun-exposed areas require UV-resistant labels.
How to Print Warehouse Labels?
Here’s a step-by-step guide to ensure you get the best results when printing warehouse labels:
- Invest in a High-Resolution Printer: The foundation of clear labels lies in the printer’s resolution. Opt for a printer with a resolution of at least 203 DPI. This ensures that both text and barcodes are sharp, facilitating easy reading and accurate scanning.
- Select the Appropriate Label Material: Warehouses can vary significantly in terms of environmental conditions. Whether it’s a humid environment, cold storage, or an area exposed to sunlight, the label material should be chosen accordingly to withstand these conditions.
- Prioritise Printer Maintenance: Like any other machine, printers perform best when they’re well-maintained. Regular check-ups can prevent common issues like smudging or fading, ensuring each label is printed to perfection.
- Opt for High-Quality Thermal Consumables: High-quality thermal paper and thermal ribbons for warehouse labels ensure durability, readability, and efficiency, reducing long-term costs and enhancing operational workflow.
- Always Conduct a Test Print: Before proceeding with bulk printing, always print a sample. This preliminary step can help identify design discrepancies or print quality issues, saving time and resources in the long run.
When it comes to labelling your warehouse, the quality of the printer you use makes all the difference. That’s why thermal printers have become the go-to option for professionals in this field. These advanced printing machines use heat to produce sharp and clear images, perfect for barcodes and other important labels. Not only are they reliable and cost-effective, but they also print at lightning-fast speeds.
That’s why Triton offers a selection of top-of-the-line thermal printers from major brands such as Zebra, Honeywell, and TSC, as well as coloured label printers from OKI. Our vast inventory includes various thermal printer models such as desktop label printers, industrial label printers, direct thermal printers, thermal transfer printers, and barcode label printers. Our printer range is chosen with care, ensuring you can tackle any printing job with ease and efficiency.
So why wait? Shop with us today!
Conclusion
Choosing the right warehouse labels is more than a mere operational decision. It’s a strategic move that significantly influences efficiency, accuracy, and productivity.
As we’ve explored, factors such as the label’s location, material, adhesive quality, and the environment it’s exposed to play pivotal roles in determining its effectiveness.
By understanding these intricacies and aligning them with the specific needs of your warehouse, you can ensure a streamlined inventory management process, reduced errors, and enhanced operational flow.
Remember, in the vast ecosystem of a warehouse, every label serves as a beacon, guiding processes and ensuring order amidst the hustle and bustle. So, invest time in making the right choice, and your warehouse operations will thank you for it!