Did you know the global packaging market is projected to reach USD 1.18 trillion by 2025?
From protecting products to enhancing brand appeal, packaging materials play an important role in every industry.
But that is not the most fascinating aspect.
The most amazing part about packaging is the variety of materials used in modern applications. From lightweight plastics and sturdy metals to biodegradable paper and innovative composites, the choices are as diverse as the industries they serve.
Let’s explore them all in this article.
Corrugated Cardboard
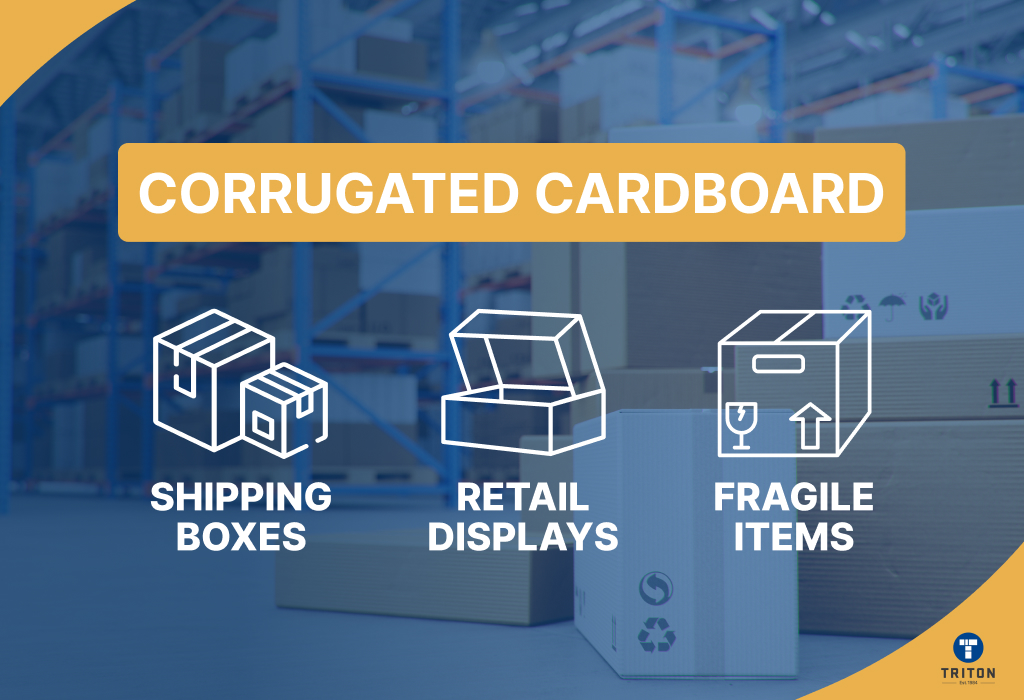
Corrugated cardboard is a popular packaging. It is strong, lightweight, and eco-friendly. Corrugated cardboard is constructed from kraft paper or recycled paper.
It has three layers: an outer liner, an inner liner, and a fluted middle layer. The middle layer, also known as the “flute,” is sandwiched between the liners and provides cushioning and rigidity, making it ideal for protecting items during transit.
Kraft paper, which is usually made from wood pulp, is strong, durable, and resistant to tearing. These properties make it the ideal base material.
The three layers are bonded with biodegradable starch-based or eco-friendly adhesives.
Use Case
- Shipping Boxes: Commonly used for shipping, it’s lightweight yet sturdy enough to protect items like electronics, clothing, and books.
- Retail Displays: Often used for point-of-sale displays in retail due to its structural strength and ease of customisation.
- Fragile Items: Ideal for packaging fragile products such as glassware and ceramics due to its cushioning properties.
Advantages
- Strong and Durable: Withstands impact and protects items well during transport.
- Lightweight: Reduces shipping costs due to its low weight.
- Eco-Friendly: Biodegradable and recyclable, supporting sustainable practices.
- Customisable: Easy to cut, fold and shape which makes it ideal for creating boxes of different shapes and sizes.
Disadvantages
- Sensitive to Moisture: Loses strength if exposed to moisture, making it less suitable for damp conditions.
- Not Reusable: Prone to tearing or deformation.
- Simple Appearance: May not offer the luxury aesthetic some brands require for high-end products.
Paperboard
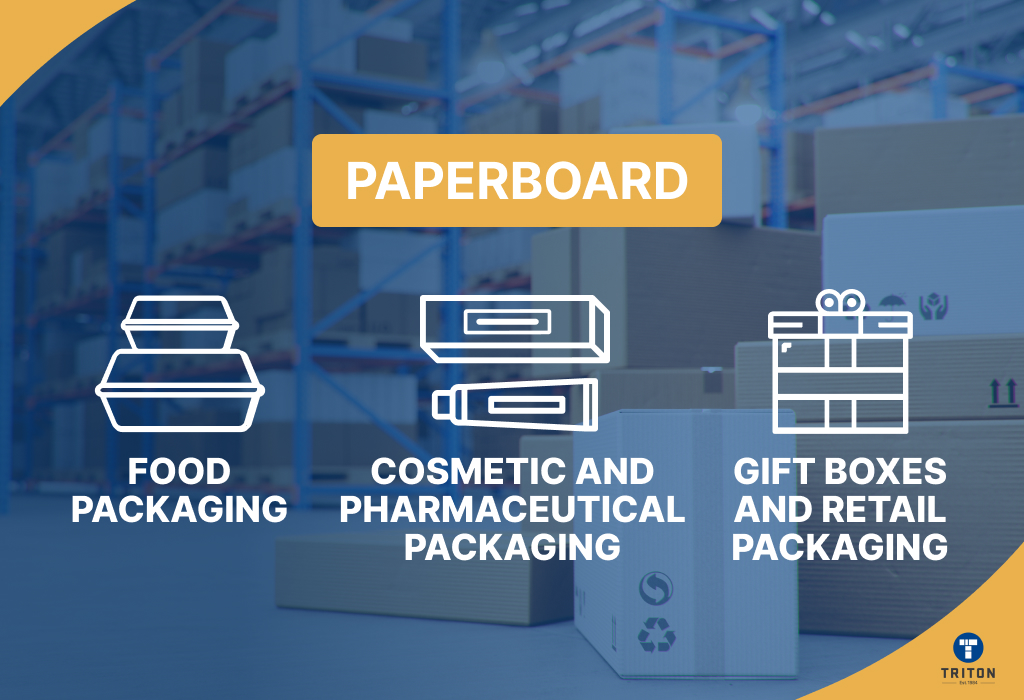
Paperboard is lightweight and versatile. It’s a go-to for retail packaging. It has a smooth surface, which is easy to print on and customise, making it ideal for branding.
Paperboard is made from processed paper pulp. It balances durability with being light and affordable. It’s not as sturdy as corrugated cardboard. However, it works well for items that aren’t too heavy or fragile.
Use Cases
- Food Packaging: Frequently used for cereal boxes, snack packaging, and frozen food cartons
- Cosmetic and Pharmaceutical Packaging: Ideal for small boxes that protect products while allowing for high-quality printing to display brand details.
- Gift Boxes and Retail Packaging: Often used for retail boxes to enhance the appeal of the products.
Advantages
- Lightweight: Easy to handle and adds minimal weight to products, therefore reduces shipping costs.
- Customisable: It has a smooth surface which can handle high-quality printing. This makes it excellent for branded packaging.
- Recyclable: Commonly recyclable, supporting eco-friendly practices and reducing environmental impact.
Disadvantages
- Not Durable: Not as strong as other materials; unsuitable for heavy or delicate items.
- Sensitive to Moisture: Can weaken or warp when exposed to moisture, making it less ideal for wet conditions.
- No Impact Protection: Needs additional cushioning for products that require impact protection.
Cardboard Cartons
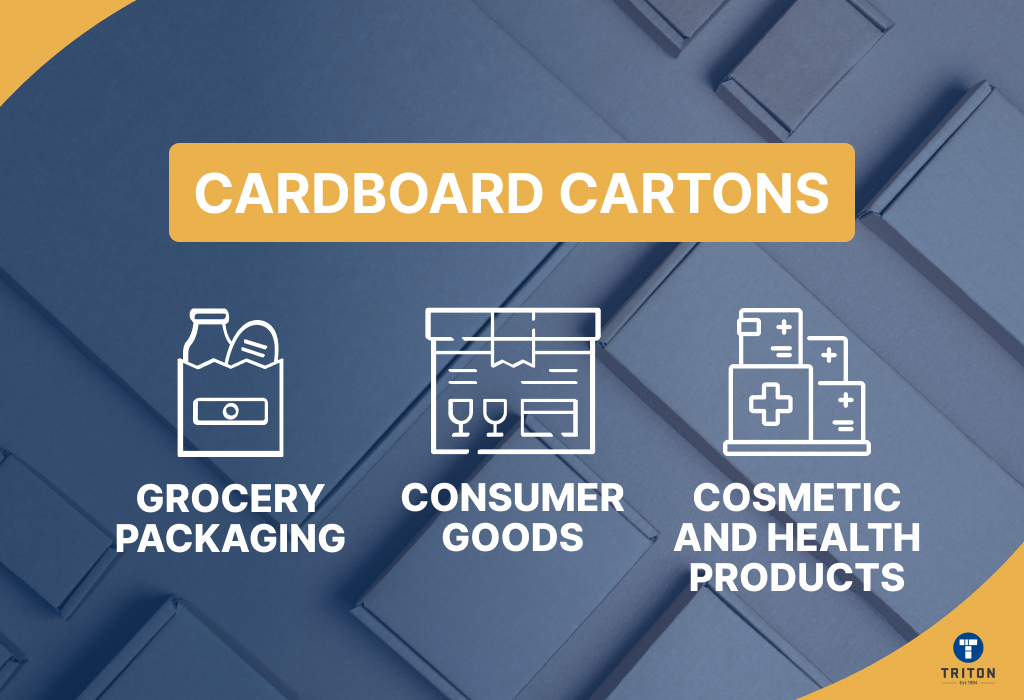
Cardboard cartons are made from solid paperboard. These are used in retail and consumer packaging. Unlike corrugated boxes, which have a fluted inner layer, cardboard cartons consist of a single, sturdy sheet of compressed paper pulp.
This makes them lightweight, sleek, and easy to work with.
These cartons are easily customisable, and are usually printed with branding and product information.
Cardboard cartons are cost-effective and environmentally friendly. They are often made from recycled materials and are fully recyclable themselves.
Use Cases
- Grocery Packaging: Suitable for items like cereal, dry snacks, and other pantry goods where moderate protection and easy storage are needed.
- Consumer Goods: Often used for packaging electronics accessories, books, and small gadgets, where a cost-effective, lightweight solution is ideal.
- Cosmetic and Health Products: Ideal for beauty products, toothpastes, and small pharmaceuticals.
Advantages
- Lightweight: Reduces shipping weight, transportation costs. Easier to handle.
- Affordable: A cost-effective option for high-volume use, especially for everyday consumer goods.
- Environmentally Friendly: Usually recyclable and often made from recycled content, making it a sustainable choice.
- Brand-Friendly: Smooth surface is great for high-quality printing, allowing brands to stand out on shelves.
Disadvantages
- Low Strength: Not suitable for heavy or very delicate items, as it doesn’t offer strong structural support.
- Sensitive to Moisture: Cardboard cartons can weaken if exposed to water, limiting their use in humid environments.
- Low Protection: Offers little cushioning, making it less effective for items requiring extra shock absorption.
Parchment Paper
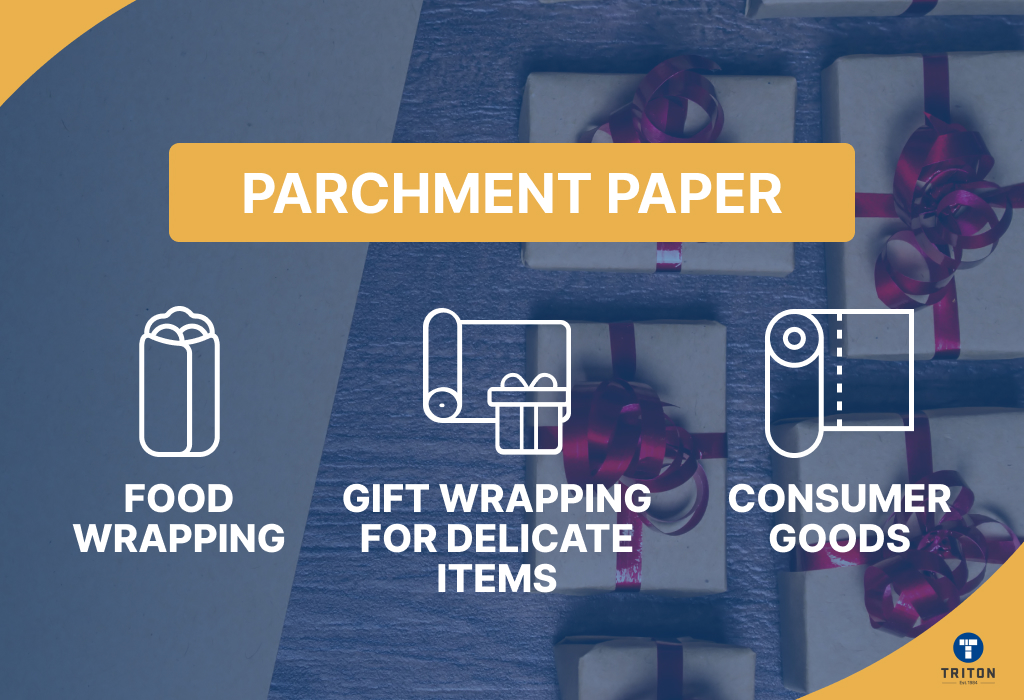
Parchment paper, also known as baking paper, is a cellulose-based paper treated to enhance its non-stick, grease-resistant, and heat-resistant properties.
The paper passes through a sulfuric acid bath (parchmentisation), which gelatinises the surface, creating a durable, smooth, and heat-resistant material ideal for culinary applications. In the food industry, parchment paper is indispensable for tasks such as baking, roasting, and steaming, and packaging as it prevents sticking.
Parchment paper can withstand temperatures up to 216–232°C (420–450°F.)
Parchment paper is compostable and biodegradable, aligning with sustainable practices in both industrial and household kitchens.
Use Cases
- Food Wrapping: Commonly used for bakery items, sandwiches, and cheeses, as it helps maintain freshness and prevents sticking.
- Baking and Cooking: Ideal for lining baking trays and pans to prevent food from sticking and to reduce the need for added oils.
- Gift Wrapping for Delicate Items: Occasionally used for wrapping fragile, oil-sensitive items like candles and soaps, as it provides a moisture barrier.
Advantages
- Heat Resistant: Can withstand high temperatures, making it suitable for baking and reheating.
- Non-Stick Surface: Prevents food from sticking, reducing cleanup time and the need for oils.
- Greaseproof and Moisture-Resistant: Keeps food fresh by providing a barrier against moisture.
- Biodegradable: Often compostable, which aligns with eco-friendly practices.
Disadvantages
- Limited Strength: Not suitable for heavy-duty packaging or items that require significant protection.
- Single-Use: Typically not reusable after exposure to high heat or grease.
- Limited Customization: Unlike some packaging materials, it’s less suitable for branding or printing.
Wet-Strength Paper
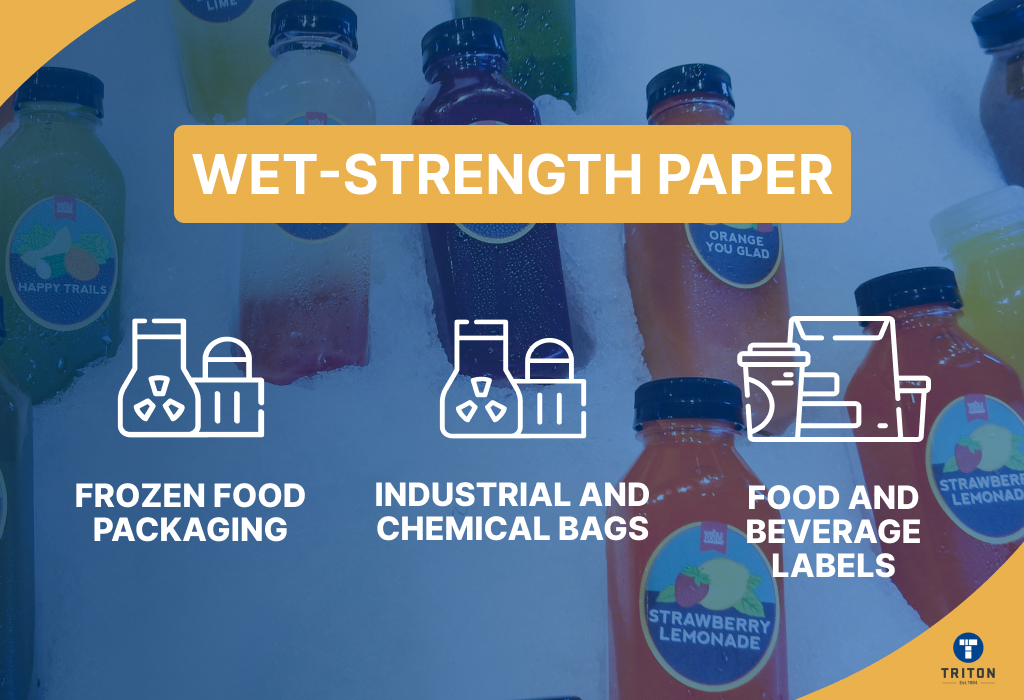
Wet-strength paper is engineered to maintain its integrity when exposed to moisture, which makes it ideal for applications like liquid packaging, outdoor materials, and food containers. This resilience is achieved by incorporating wet-strength resins, such as polyamide-epichlorohydrin (PAE), during production, which form covalent bonds with cellulose fibres, enhancing durability even in wet conditions.
Use Cases
- Food and Beverage Labels: Commonly used for labels on bottles and cans, particularly those stored in refrigeration or wet conditions.
- Frozen Food Packaging: Ideal for frozen foods needing moisture-resistant packaging to maintain integrity in low-temperature environments.
- Industrial and Chemical Bags: Often used to package moisture-sensitive chemicals, fertilisers, and similar products.
Advantages
- Water Resistance: Retains strength and structure when exposed to moisture, making it suitable for damp or humid settings.
- Durable: Provides higher tear and wear resistance compared to standard paper.
- Eco-Friendly Options: Many versions are recyclable and compostable, aligning with sustainable practices.
- Versatile: Available in different thicknesses and finishes to suit various packaging needs.
Disadvantages
- Higher Cost: More expensive than standard paper due to the additional water-resistant treatments.
- Limited Print Quality: Not easy to print on.
- Not Completely Waterproof: While moisture-resistant, it may not withstand prolonged water exposure without extra coatings.
Laminated Pouches
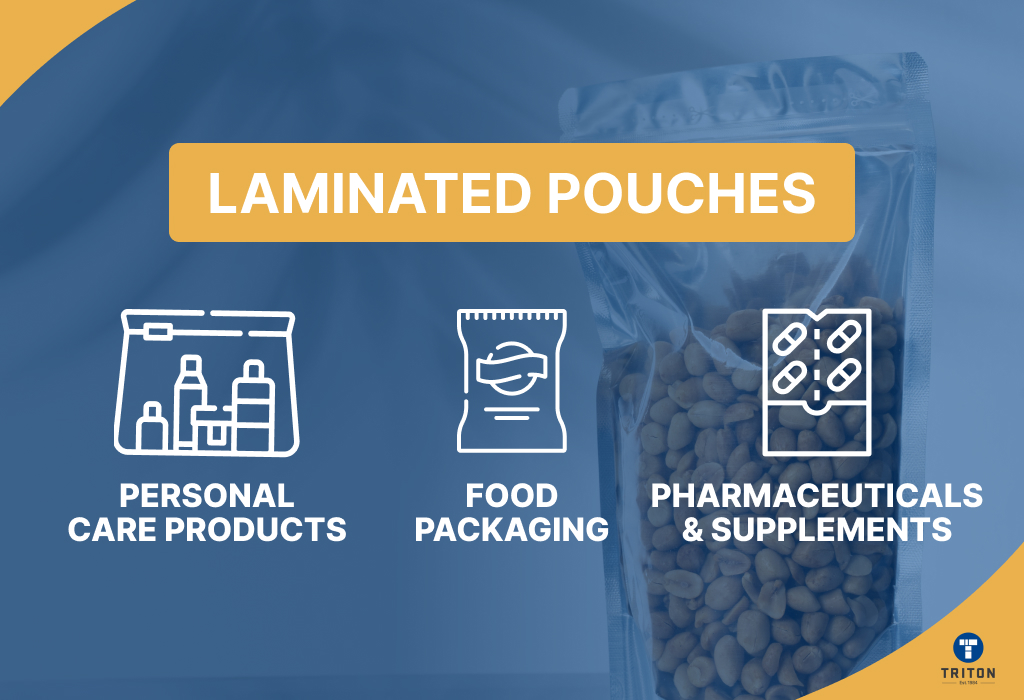
Laminated pouches are flexible packaging solutions made by layering multiple materials, typically plastic, aluminium, and sometimes paper, to create a durable, protective pouch. These layers combine to offer excellent resistance to moisture, air, and light. freshness and quality of products.
The outer layer (typically polyester or BOPP) provides strength, printability, and protection against external elements.
The middle layer (typically aluminium or EVOH) acts as a high-barrier shield against moisture, oxygen, and light.
The inner Layer (typically polyethylene or cast polypropylene) ensures heat-sealability and compatibility with the product being packed.
Laminated Pouches preserve product quality, extend shelf life, and enhance consumer convenience.
Laminated pouches are customisable, and are available in a number of form factors like resealable zippers, spouts, and more.
Use Cases
- Food Packaging: Commonly used for snacks, coffee, spices, and pet food, as they provide an airtight seal to keep contents fresh.
- Pharmaceuticals and Supplements: Often used for single-use doses and vitamin packaging to protect from moisture and contamination.
- Personal Care Products: Ideal for products like face masks and travel-sized cosmetics, providing a lightweight, leak-proof option.
Advantages
- Barrier Protection: Offers strong resistance to moisture, air, and light, keeping products fresh for extended periods.
- Lightweight and Space-Saving: Flexible design reduces storage and shipping costs.
- Customisable Features: Can include resealable zippers, spouts, and a variety of finishes to enhance user convenience and brand appeal.
- Extended Shelf Life: Helps to preserve perishable items, reducing waste.
Disadvantages:
- Non-Biodegradable: Often challenging to recycle due to mixed material layers, contributing to landfill waste.
- Higher Cost: More expensive than simple paper or plastic packaging, especially with added features like resealable zippers.
- Complex Disposal: Multi-layer structure can complicate recycling, limiting eco-friendliness.
Plastic Containers
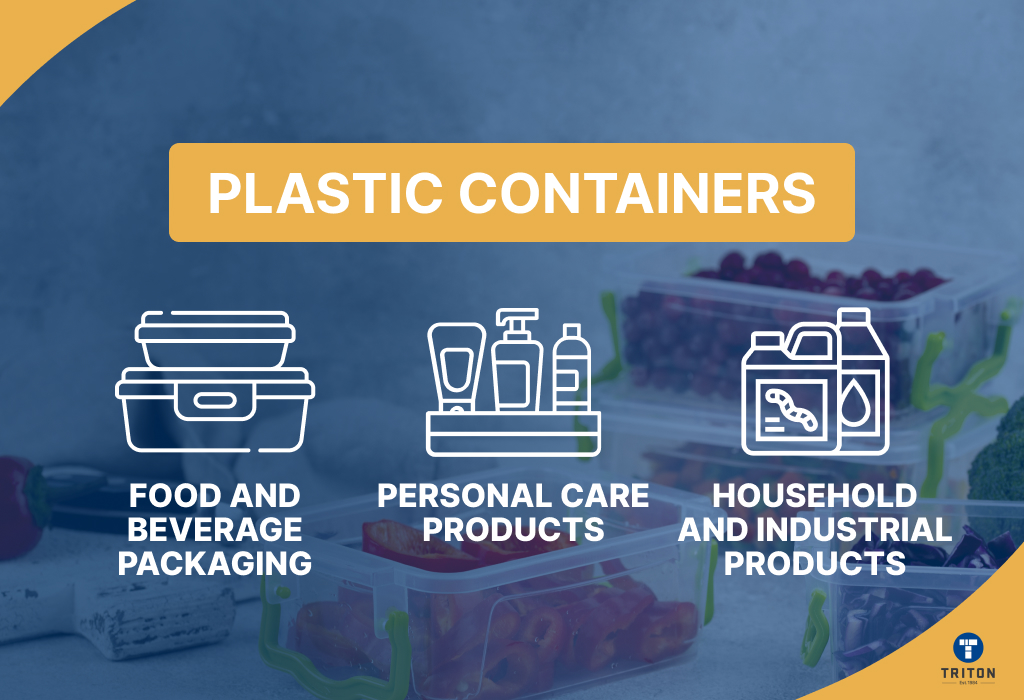
Plastic containers are a cornerstone of modern packaging. They are made from materials like PET, HDPE, and PP.
Plastic containers are lightweight, strong, and resistant to moisture, chemicals, and impact.
Their versatility makes them perfect for packaging everything from drinks and medicines to household cleaners and personal care products.
They can be moulded into almost any shape and they also support high-quality printing and labelling, boosting brand visibility.
Many plastic containers are recyclable, addressing sustainability goals, but recycling rates vary, and plastic waste remains a challenge. Innovations like biodegradable plastics and better recycling technologies aim to make plastic packaging more eco-friendly in the future.
Use Cases
- Food and Beverage Packaging: Common for items like bottled water, juices, yoghurt, and condiments, as they provide an airtight seal to preserve freshness.
- Personal Care Products: Frequently used for shampoos, lotions, and cosmetics, offering a leak-proof and durable solution.
- Household and Industrial Products: Ideal for detergents, cleaners, and chemicals due to their chemical resistance and secure sealing.
Advantages
- Durable and Lightweight: Strong enough to protect contents, yet light, reducing shipping and handling costs.
- Moisture and Leak Resistance: Prevents contamination and leakage, especially in food and liquid products.
- Customisable: Can be moulded into various shapes, sizes, and designs to align with branding and functional needs.
- Reusable and Sealable: Often designed for multiple uses, particularly with secure, resealable lids.
Disadvantages
- Environmental Impact: Non-biodegradable and challenging to recycle, contributing to landfill and ocean waste.
- Potential for Chemical Leaching: Some plastics, especially if reused or heated, may leach chemicals into products, raising safety concerns.
- Higher Production Emissions: Plastic production can be resource-intensive and generate significant emissions.
Thermoformed Packaging
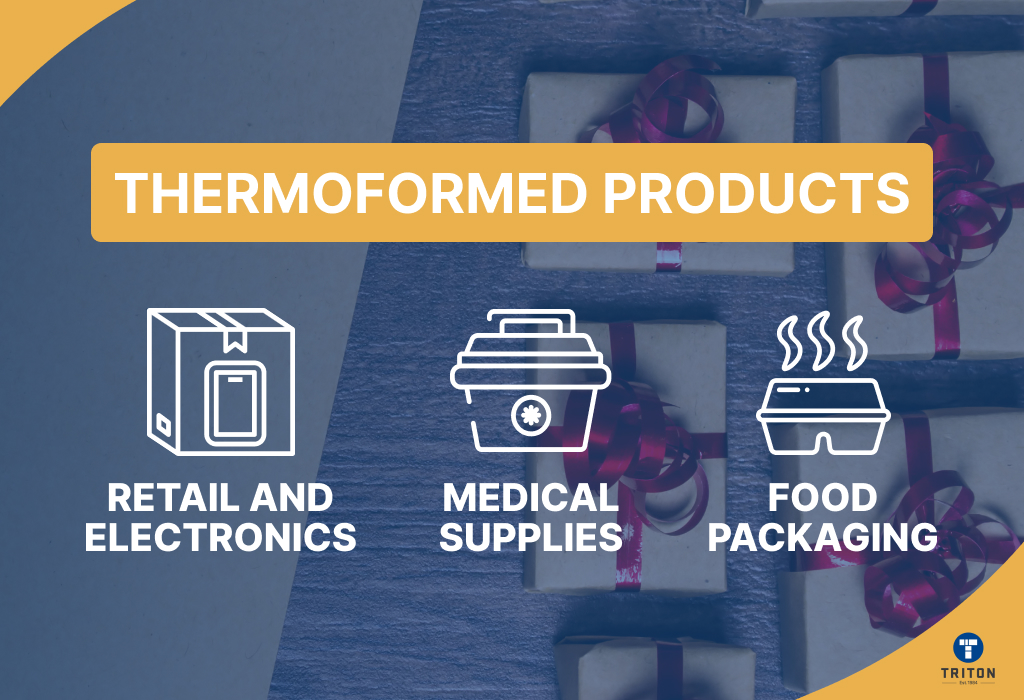
Thermoformed packaging is created by heating plastic sheets until pliable and then molding them into specific shapes using. This versatile packaging process is widely used across industries, including medical, packaging, and consumer goods.
Common materials used in thermoforming include polyethene terephthalate (PET), known for its strength and clarity, making it a preferred choice for food packaging applications; polyvinyl chloride (PVC), valued for its excellent clarity and often used in blister packs and clamshell packaging; and polypropylene (PP), recognised for its durability and heat resistance, which suits a variety of packaging requirements.
Use Cases
- Food Packaging: Widely used for produce trays, meat containers, and baked goods packaging due to their form-fitting design and transparency.
- Retail and Electronics: Ideal for clamshell packaging, blister packs, and trays, which protect items while allowing visibility for retail display.
- Medical Supplies: Used to package medical devices, syringes, and tools, providing a sterile barrier that’s also secure and easy to handle.
Advantages
- Customisable Shape: Can be moulded to specific product shapes, offering a secure fit and minimising movement during transport.
- Visibility: Clear plastic options enhance product visibility, making them suitable for retail display.
- Durable and Lightweight: Offers strong protection without adding much weight, making it cost-effective for shipping.
- Cost-Efficient: Thermoforming is relatively affordable for high-volume production, reducing per-unit packaging costs.
Disadvantages
- Environmental Impact: Thermoformed plastics are often difficult to recycle and may contribute to waste.
- Limited Reusability: Typically designed for single use, reducing their sustainability.
- Potential for Cracking: Some thermoformed plastics can be brittle, risking cracks or breaks if mishandled.
Tin Cans
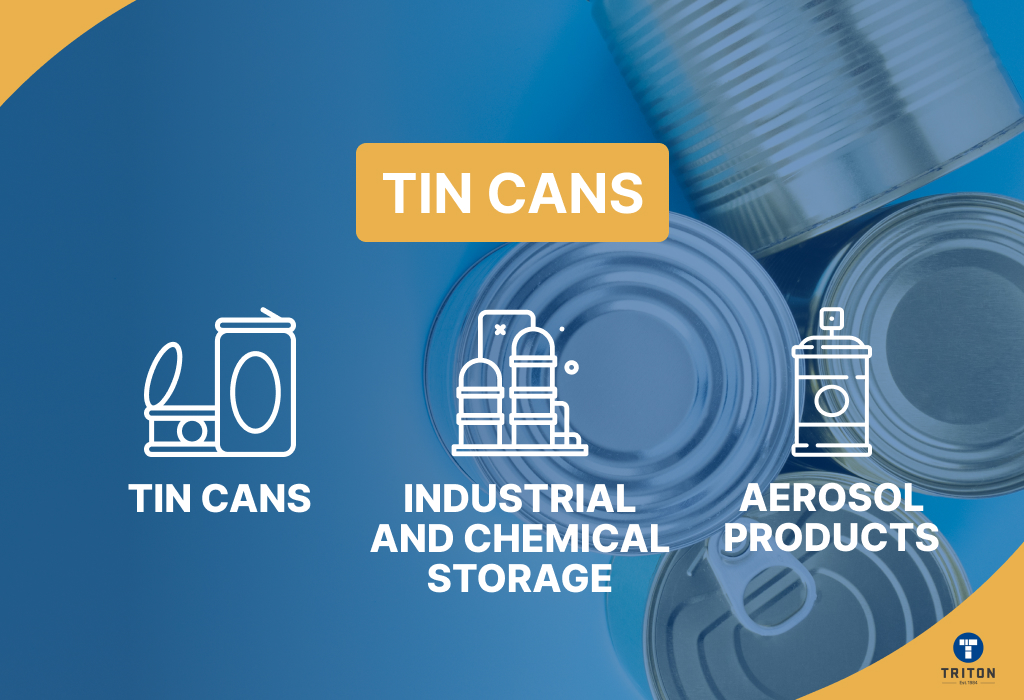
Tin packaging is made from tinplate which is a thin layer of tin coated onto steel. It is a durable and versatile option widely used across industries.
Its journey began in the early 19th century when British merchant Peter Durand secured a patent for tin-plated iron cans in 1810. This breakthrough changed how food was stored and transported, particularly for military and naval operations, and became the cornerstone of modern packaging technology.
Tin offers excellent protection against physical damage, air, and moisture, making it ideal for packaging food, beverages, and cosmetics. Its structure shields products from damage, air, and moisture, extending their shelf life while maintaining integrity.
Tin packaging is also valued for its metallic appearance, which adds a premium touch to products.
However, tin packaging is not suitable for acidic contents and is more costly than alternatives like plastic or paper.
Use Cases
- Food and Beverage Packaging: Commonly used for canned vegetables, soups, pet food, and soft drinks, as they preserve contents without the need for refrigeration.
- Aerosol Products: Suitable for products like spray paints, deodorants, and air fresheners, as they can withstand pressurisation.
- Industrial and Chemical Storage: Used for packaging paint, solvents, and chemicals, as they offer a secure, non-reactive barrier.
Advantages
- Long Shelf Life: Airtight seal and durability provide a long shelf life, preserving freshness without refrigeration.
- Excellent Barrier Properties: Blocks light, air, and contaminants, protecting products from spoilage.
- Recyclable: Tin cans are highly recyclable and can be repurposed multiple times, reducing environmental impact.
- Tamper-Resistant: Provides a secure barrier that helps prevent tampering, ensuring product safety.
Disadvantages
- Higher Production Cost: High energy and material cost.
- Heavy and Bulky: Adds weight, which increases shipping costs and handling challenges.
- Limited Design Flexibility: Shape and size options are more restricted (often cylindrical) compared to flexible packaging solutions.
Shrink Wrap
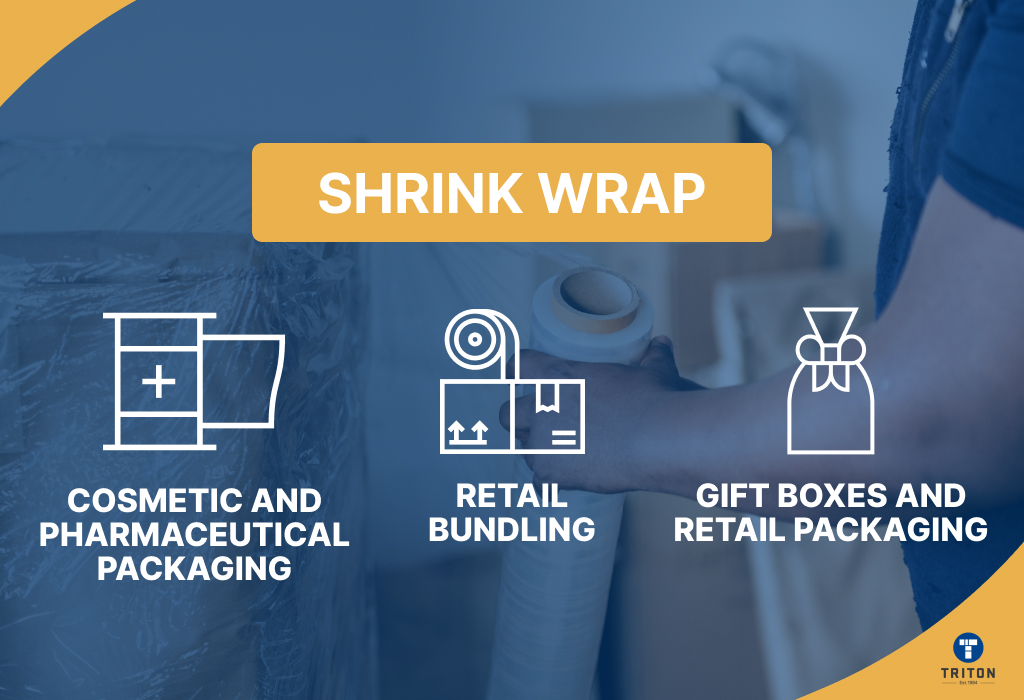
Shrink wrap, also known as shrink film, is a polymer plastic material that contracts when heat is applied, forming a tight seal around the encased item. This process involves wrapping the film around the product and then applying heat using a heat gun or by passing the package through a heat tunnel, causing the film to conform closely to the product’s shape.
The four common shrink wrap materials are: Polyolefin (POF), Polyvinyl Chloride (PVC), Polyethylene (PE), and Polypropylene (PP).
POF is strong and flexible, handling irregular shapes without tearing. PVC is lightweight and cost-effective but less popular now due to environmental concerns. PE is heavier and used to stabilise large loads, such as pallets of goods. PP is both clear and durable, making it the go-to choice for packaging items where visibility is important, such as retail products.
Use Cases
- Retail Bundling: Shrink wrap consolidates multiple items, such as beverage multipacks or canned goods into a single, manageable unit.
- Pallet Wrapping: It secures products on pallets during storage and transport, preventing items from movement and fall.
- Food Packaging: Commonly used for fresh produce, meat, and bakery items, shrink wrap offers a clear, protective layer that helps prevent contamination and retain freshness.
Advantages
- Protective Barrier: Shrink wrap prevents exposure to moisture, dust, and dirt, protecting items during handling and storage.
- Tamper-Evident: The material provides clear signs if packaging has been opened, helping deter tampering and ensuring product safety.
- Lightweight and Space-Saving: Shrink wrap adds negligible weight and bulk to packages and can be stored in compact rolls, saving space.
- Product Visibility: The transparent material allows consumers to view the product directly, which is beneficial for retail displays.
Disadvantages
- Single-Use and Non-Biodegradable: Designed for single use, shrink wrap contributes significantly to plastic waste and poses challenges for sustainable disposal.
- Limited Durability: The material tears or punctures easily, especially when used with heavy or sharp-edged items, making it less effective in such scenarios.
- Recycling Challenges :Shrink wrap is difficult to recycle due to its composition and is often mixed with materials like labels, adhesives, or residues from the products it encases, which complicates the recycling process.
Cling Film
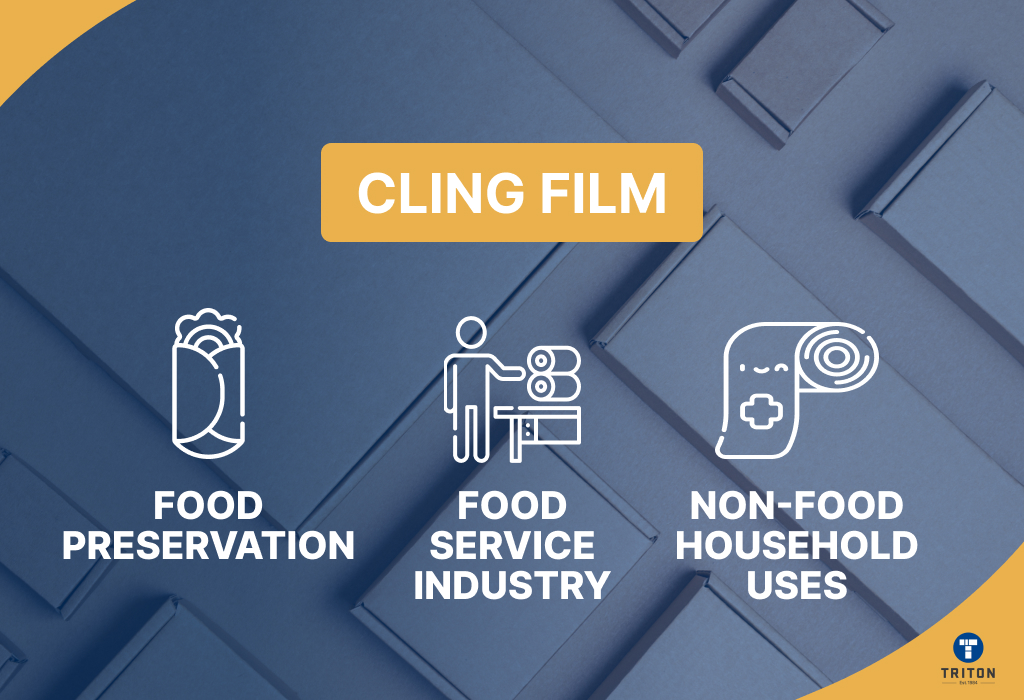
Cling film, often referred to as plastic wrap, is a thin, transparent sheet of plastic that clings tightly to surfaces and to itself when pressed. This self-sealing property makes it highly effective for covering food containers and wrapping items securely without the need for adhesives or fasteners.
It was invented in 1933 when Ralph Wiley, a Dow Chemical lab worker, accidentally discovered polyvinylidene chloride (PVDC), which later became the primary material in Saran Wrap.
Initially, cling films were made from PVDC due to its excellent barrier properties against moisture and gases. However, environmental concerns and production costs led to the adoption of materials like low-density polyethylene (LDPE) and polyvinyl chloride (PVC).
Use Cases
- Food Preservation: Used to cover and protect food in refrigerators, preventing contamination and slowing spoilage.
- Food Service Industry: Wrap prepared ingredients and meals for hygiene and maintaining quality.
- Household Storage: Sometimes used to wrap non-food items to protect them from dust and moisture during storage.
Advantages
- Effective Barrier: Forms a tight seal that blocks air, moisture, and odours, keeping items fresh.
- Flexible and Transparent: Easily wraps around items of various shapes and sizes, while allowing contents to remain visible.
- Lightweight and Practical: Simple to use and adds little weight, making it ideal for temporary storage.
- Affordable: A cost-effective solution for preserving food at home or in commercial settings.
Disadvantages
- Environmental Concerns: Designed for single use, it adds to plastic waste and contributes to pollution.
- Temperature Limitations: Unsuitable for high-heat applications, as it can melt or release harmful chemicals.
- Recycling Issues: Recycling is challenging due to its thinness and contamination from food residues, limiting eco-friendly disposal options.
Plastic Crates
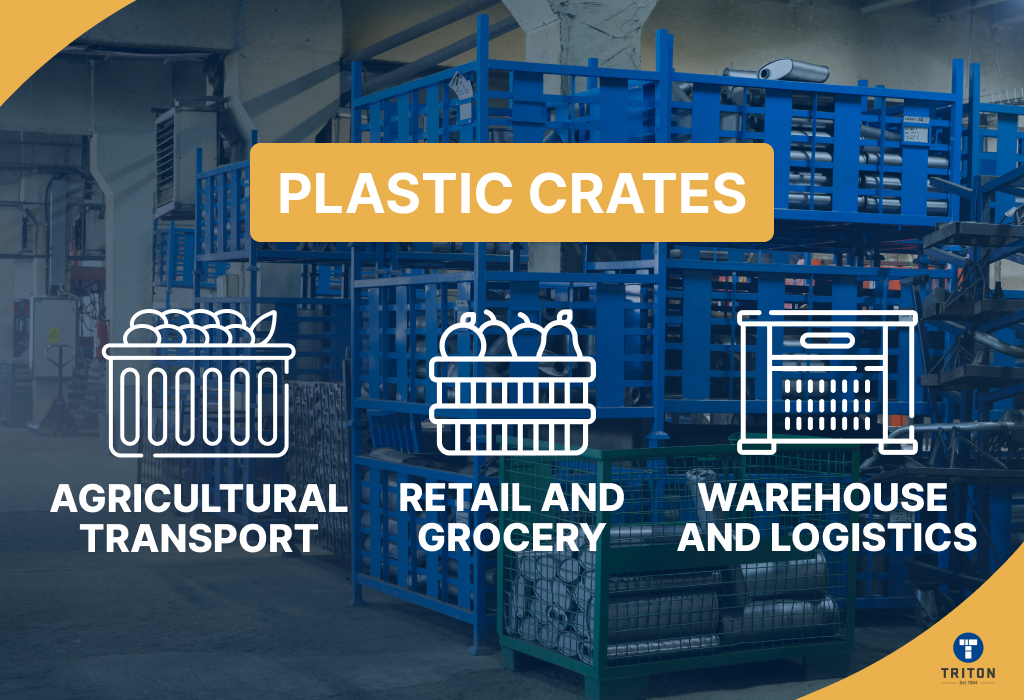
Plastic crates are durable, reusable containers widely used for transporting and storing various goods. Made from high-density polyethylene (HDPE) or polypropylene (PP), they offer a lightweight yet robust solution that can withstand heavy loads and rough handling. Plastic crates are valued for their long lifespan, stackability, and resistance to moisture, making them ideal for industries such as agriculture, food distribution, and retail. Their reusability and ability to be sanitised easily make them a more sustainable option compared to single-use packaging.
Use Cases
- Agricultural Transport: Commonly used for transporting fresh produce from farms to markets, as they provide ventilation and durability.
- Warehouse and Logistics: Ideal for storing and moving items in warehouses and during shipping, as they can withstand stacking and heavy handling.
- Retail and Grocery: Used to store and display goods like fruits, vegetables, and dairy, ensuring easy access and organised storage.
Advantages
- Durable and Long-Lasting: Designed to withstand repeated use, heavy loads, and rough conditions, making them highly cost-effective over time.
- Stackable and Space-Efficient: Easily stackable, allowing for efficient storage and transport, maximising space usage.
- Moisture and Chemical Resistant: Resistant to water and many chemicals, making them ideal for perishable goods and harsh environments.
- Easy to Clean: Can be sanitised, which is crucial in industries like food and pharmaceuticals where hygiene is important.
Disadvantages
- Higher Initial Cost: More expensive upfront than single-use packaging options, though costs balance out with long-term use.
- Bulkier than Foldable Options: While stackable, they take up space even when empty, unlike foldable crates.
- Non-Biodegradable: Made from plastic, which doesn’t decompose easily, leading to environmental impact if not recycled properly.
Plastic Trays
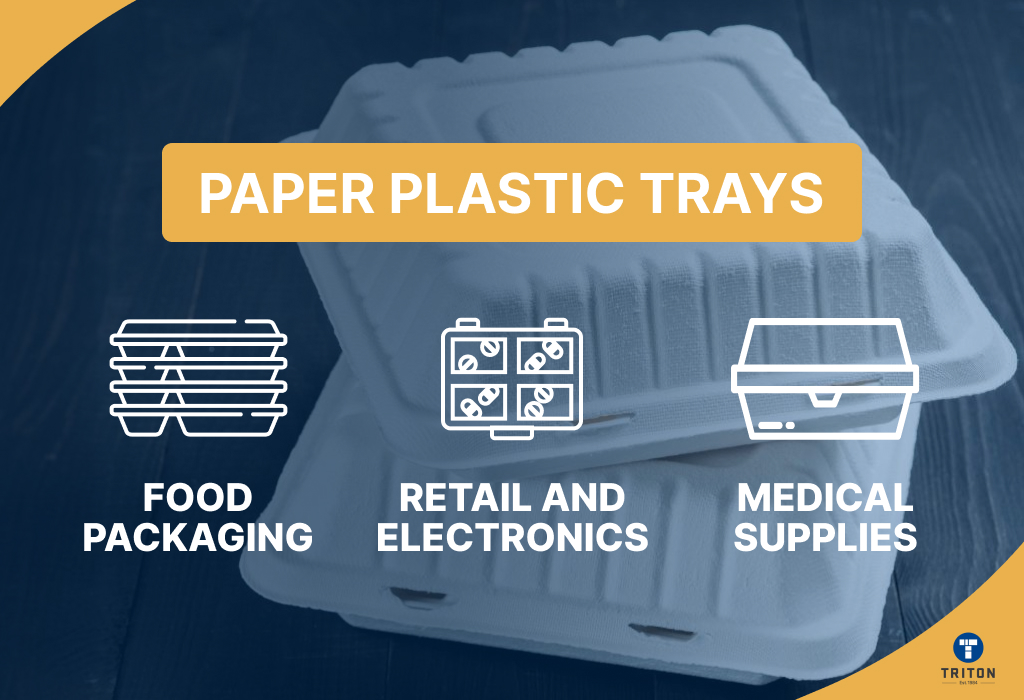
Plastic trays became popular during the mid-20th century as industries sought affordable and practical packaging solutions to improve the storage, transportation, and presentation of perishable foods, retail products, and medical supplies. Advances in polymer technology made trays lightweight, strong, and adaptable.
These trays are made from various materials, each suited to specific purposes. Polyethylene Terephthalate (PET) is strong, transparent, and recyclable. Polypropylene (PP) resists heat and chemicals, making it suitable for microwaveable containers. Polystyrene (PS) is lightweight and affordable, often used for disposable trays. Polylactic Acid (PLA), derived from renewable resources, is biodegradable and gaining traction as an eco-friendly choice.
Plastic trays are used in food packaging to preserve freshness and protect items such as meats, fruits, and ready-to-eat meals. In healthcare, they ensure the organised storage and sterility of medical instruments. In retail, they secure and display products effectively, improving presentation and accessibility.
Plastic trays are often not recycled due to the use of black plastics, which cannot be detected by recycling systems, and economic barriers tied to their lightweight design. Food contamination, though removable, adds complexity. Solutions include using recyclable materials, improving consumer practices, and adopting compostable or biodegradable alternatives.
Use Cases
- Food Packaging: Used for fresh produce, meats, and bakery items to protect and organise products for grocery displays.
- Medical Supplies: Organises and packages syringes, vials, and surgical tools in sterile conditions.
- Retail and Electronics: Secures and displays items like jewellery, tools, and electronics while maintaining visibility.
Advantages
- Lightweight: Easy to transport and handle, suitable for storage and display.
- Customisable Design: Includes compartments to separate items for better organisation and protection.
- Transparent: Allows consumers to see contents without opening the package.
- Moisture Resistant: Prevents contamination and protects perishable or sterile items.
Disadvantages
- Environmental Impact: Single-use design contributes to plastic waste.
- Weak Structure: Unsuitable for heavy or large items due to limited strength.
- Recycling Issues: Difficult to recycle when combined with other materials or contaminated with food residues.
EPS Trays
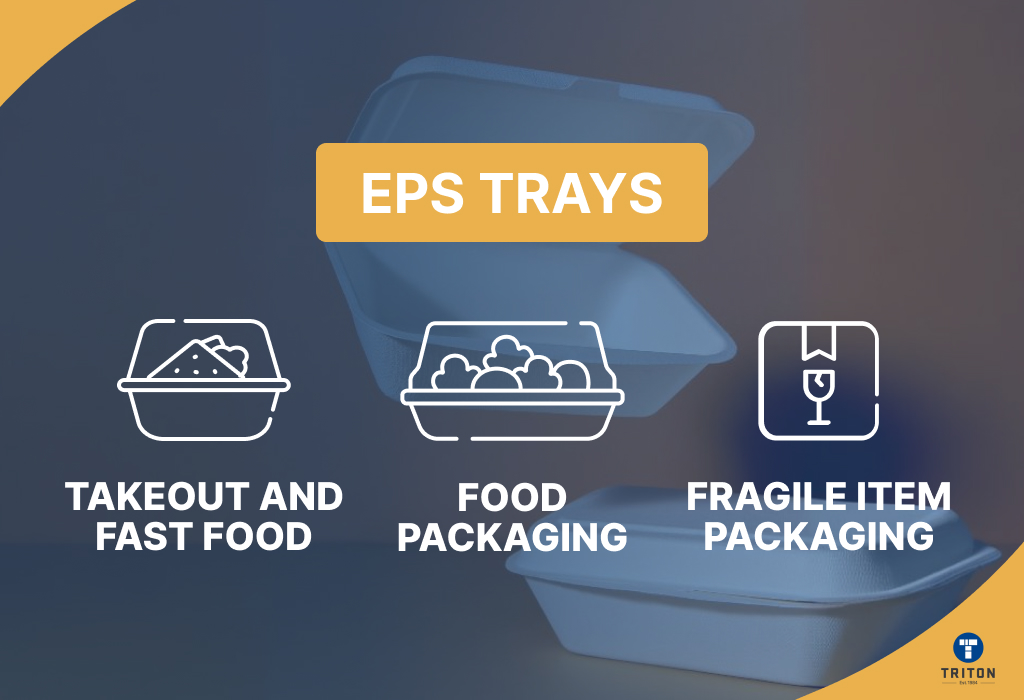
Expanded Polystyrene (EPS) is made from polystyrene, a polymer derived from petroleum or natural gas. Polystyrene beads, infused with a blowing agent like pentane, are expanded using steam, increasing their size by up to 50 times. The expanded beads are stabilised and moulded into solid forms by reheating, causing the beads to fuse into a closed-cell foam structure. EPS is 98% air, making it lightweight, thermally insulating, and resistant to moisture. Its properties make it ideal for protective packaging and insulation.
Use Cases
- Food Packaging: Commonly used for meat, poultry, and produce, as EPS trays help maintain freshness and reduce moisture build-up.
- Takeout and Fast Food: Frequently used in the food service industry for packaging takeout meals due to their insulation and lightweight design.
- Fragile Item Packaging: Ideal for packaging and cushioning electronics or delicate products, as the foam structure provides shock absorption.
Advantages
- Thermal Insulation: The closed-cell structure of EPS provides effective temperature regulation, keeping perishable items like meats, seafood, and dairy products fresh during storage and transit.
- Lightweight Design: EPS trays are made of 98% air, making them easy to handle and transport. This reduces shipping costs and energy consumption during distribution.
- Cost-Effectiveness: EPS trays are inexpensive to produce, providing an affordable solution for large-scale packaging needs across industries like food, healthcare, and consumer goods.
- Impact Protection: EPS absorbs shocks and protects fragile items from damage during transportation, making it ideal for shipping delicate goods.
- Moisture Resistance: The closed-cell foam resists water and moisture, preventing contamination and maintaining the integrity of food and other items.
- Customisation: EPS trays can be moulded into various shapes and sizes, including designs with compartments to separate and organise items effectively.
- Hygiene and Safety: EPS is chemically inert and does not react with food or other materials, ensuring safety for packaged goods.
Disadvantages
- Environmental Impact: EPS is non-biodegradable and can persist in the environment for hundreds of years. It contributes significantly to plastic waste and often ends up in landfills or oceans, harming ecosystems.
- Recycling Challenges: While EPS is technically recyclable, its low density and high air content make collection, transportation, and processing costly. Contamination from food residues further complicates recycling efforts.
- Energy-Intensive Production: EPS production relies on petroleum-based materials, which are finite resources, and the manufacturing process consumes energy, contributing to greenhouse gas emissions.
- Weak Structural Integrity: EPS trays are prone to cracking and breaking under pressure or when used to hold heavy or sharp items. This limits their application to lightweight goods.
- Flammability: EPS is flammable and, when ignited, releases toxic gases, posing safety risks. Flame retardants can be added but may raise additional health and environmental concerns.
- Regulatory Restrictions: Some governments and municipalities have banned or restricted EPS use due to its environmental drawbacks, reducing its availability and limiting its adoption in certain regions.
Retort Pouches
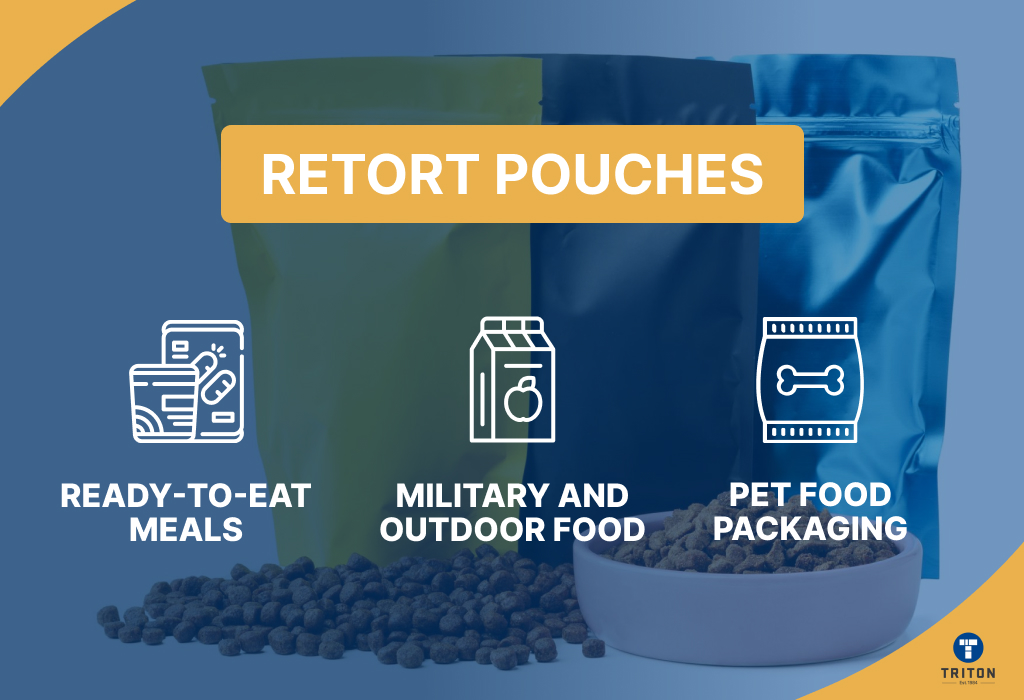
Retort pouches were first developed in the 1960s as an innovative solution for food preservation, combining the benefits of traditional canning with the convenience of flexible packaging. The technology gained traction with the introduction of “Bon Curry” in Japan in 1968, marking the first commercial retort pouch food product. By the 1970s, advancements led by the U.S. Army and packaging companies improved the design and durability of these pouches, establishing them as a reliable alternative to cans.
Modern retort pouches are made from laminated layers of materials, including polyester for strength, nylon for puncture resistance, aluminium foil for barrier protection, and polypropylene for sealing. This combination creates a durable, lightweight, and thermally stable package which can withstand high-temperature sterilisation processes.
These pouches are primarily used in the food industry for ready-to-eat meals, sauces, soups, and baby foods. They are also essential in military rations, space programs, and pet food packaging due to their ability to preserve contents for long periods without refrigeration.
Retort pouches have grown in popularity due to their efficiency, versatility, and contribution to reducing packaging waste compared to traditional cans.
Use Cases
- Food Preservation: Retort pouches are used for packaging ready-to-eat meals, sauces, soups, and baby foods. Their airtight, multilayered design allows for thermal sterilisation, ensuring extended shelf life without refrigeration.
- Military and Emergency Rations: Retort pouches are ideal for packaging meals for military personnel and emergency supplies. Their lightweight and durable nature makes them easy to transport and store, even in challenging conditions.
- Pet Food Packaging: Retort pouches are used to package wet pet foods, ensuring freshness and preserving nutritional value. Their flexible design also makes dispensing easier for consumers.
Advantages
- Extended Shelf Life: Retort pouches use thermal sterilisation to preserve food for long periods without refrigeration.
- Lightweight Design: Pouches are lighter than cans, reducing transportation costs and storage space requirements.
- Flexible Packaging: The material allows for compact, customisable designs, making them suitable for various products.
- Efficient Heat Transfer: The thin, laminated structure enables faster and more uniform heat processing compared to rigid packaging.
- Reduced Material Usage: Pouches use less material than traditional cans, lowering production costs and reducing packaging waste.
Disadvantages
- Recycling Challenges: The multilayered composition, combining plastics and aluminium, makes retort pouches difficult to recycle.
- Limited Structural Integrity: Pouches are prone to punctures and damage during handling compared to rigid packaging.
- High Production Costs: The complex manufacturing process and specialised materials result in higher production costs than some traditional packaging options.
Paper-Foil Laminate
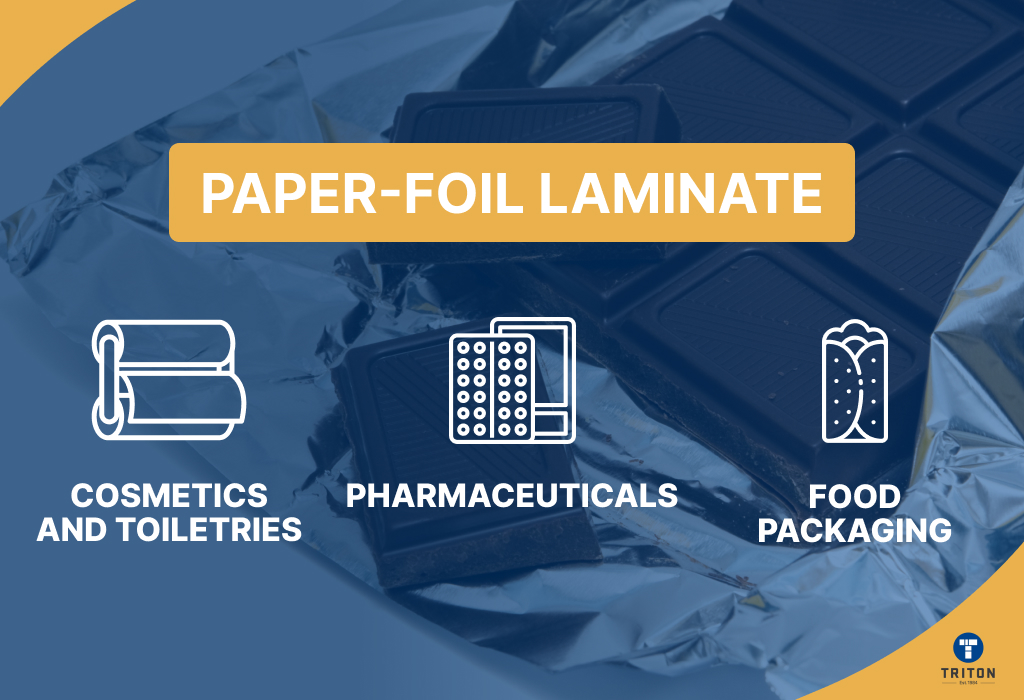
The integration of aluminium foil into packaging began in the early 20th century. In 1926, the U.S. Foil Company, which became Reynolds Metals Company, started producing aluminium foil for packaging applications. This innovation led to the development of laminated materials, combining the barrier properties of aluminium foil with the structural benefits of paper.
Paper-foil laminate packaging consists of layers of paper and aluminium foil bonded together. The paper provides strength and printability, while the aluminium foil offers a barrier against moisture, light, and gases. The lamination process typically involves adhesive bonding, where a thin layer of adhesive is applied between the paper and foil layers to ensure a uniform and durable bond.
What Does Paper-Foil Laminate Replace?Paper-foil laminate replaces waxed paper, plastic wraps, and plain aluminium foil. It provides stronger barriers against moisture and air than waxed paper, is more durable than plastic wraps, and adds a printable surface to aluminium foil. This makes it suitable for packaging that requires both protection and clear product information. |
Use Cases
- Food Packaging: Paper-foil laminate is used to wrap products like butter, chocolate, and baked goods. The foil layer keeps the items fresh by protecting them from moisture, light, and air.
- Pharmaceutical Packaging: The material is used in blister packs and sachets to keep medicines safe from environmental factors, ensuring their quality and effectiveness.
- Insulation Materials: Paper-foil laminate is applied in building insulation to improve thermal efficiency by acting as a barrier against heat loss and moisture.
Advantages
- Barrier Protection: The aluminium layer effectively blocks moisture, oxygen, and light, preserving the quality and shelf life of packaged products.
- Print Compatibility: The paper layer provides a surface for printing product details, branding, and instructions.
- Lightweight: The material is lighter than many alternatives, reducing transportation costs and energy use.
Disadvantages
- Recycling Difficulty: The combination of paper and aluminium makes it challenging to separate and recycle.
- Production Costs: Manufacturing the laminated structure is more expensive than single-material packaging.
- Environmental Impact: Aluminium production is energy-intensive, increasing the overall carbon footprint of the material.
Composite Cans
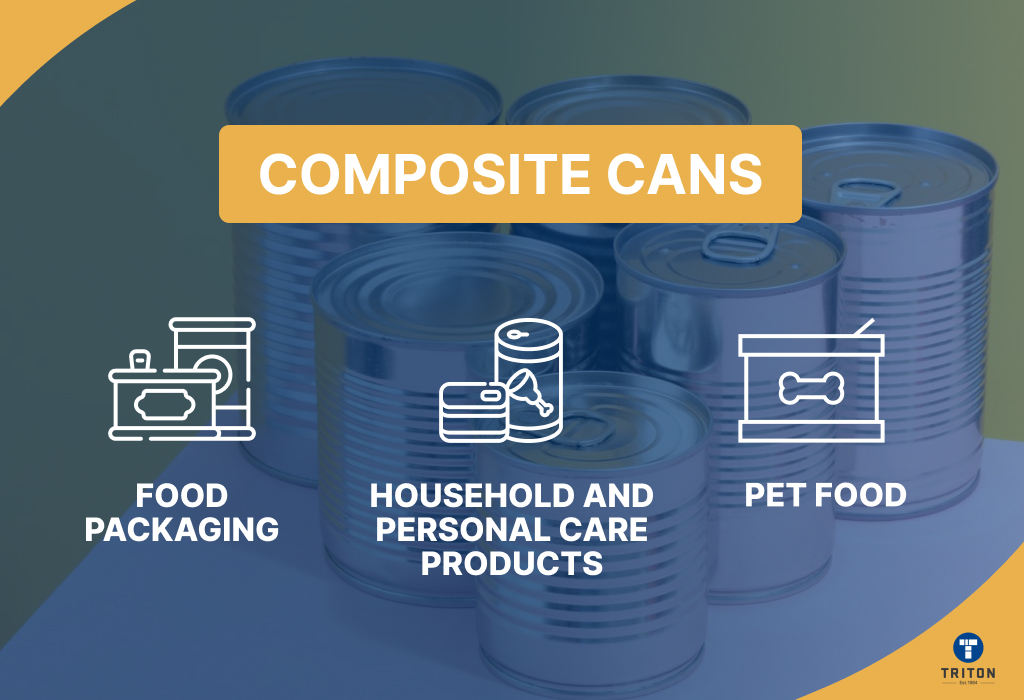
Composite cans are multilayered cylinders made of paperboard, aluminium foil, and plastic. Developed in the early 20th century as lightweight alternatives to metal cans, they initially stored dry goods like flour and snacks. Advances in materials later introduced moisture-resistant plastics and oxygen-blocking aluminium foil, expanding their use to liquids, powders, and perishables.
Modern designs prioritise sustainability, incorporating recyclable materials and reducing plastic content. Modern manufacturing allows composite cans to be made in customisable shapes, resealable lids, and tamper-evident features.
Today, they serve diverse industries like food, cosmetics and pharmaceuticals balancing functionality with eco-friendly innovation.
Composite cans use layered paperboard, foil, and plastic to provide rigidity, resist moisture, and extend shelf life. Their lightweight design lowers shipping costs. Manufacturers adapt these cans to consumer demands, focusing on functional performance and sustainable materials.
Use Cases
- Food Packaging: Commonly used for snacks, powdered beverages, coffee, tea, and spices.
- Household and Personal Care Products:Includes detergents, cleaning agents, cosmetics, and small hardware.
Advantages
- Barrier Protection: Multi-layer structure with aluminum foil and plastic liners.
- Lightweight and Durable: Lighter than metal cans while maintaining strength.
- Customisable and Brand-Friendly: Supports high-quality printing for branding.
- Eco-Friendly Options Available: Some use recyclable paperboard and aluminium.
Disadvantages
- Recycling Challenges: Mixed materials complicate separation for recycling.
- Higher Cost: Production complexity increases expenses.
- Limited Puncture Resistance: Less resistant to sharp objects compared to metal.
Laminated Tubes (Lamitubes)

Laminated tubes emerged in the mid-20th century as an improved alternative to flexible aluminum tubes, addressing limitations like cost, reactivity, and printability.
Their development was driven by the need for lightweight, flexible, and cost-effective packaging that could protect products from environmental factors. By the 1970s, advancements in material science introduced multi-layer laminates combining plastic and aluminum with enhanced barrier properties and more design flexibility.
The 21st century prioritized sustainability in laminated tubes, adopting recyclable mono-material PE, bio-based PLA, and EVOH barriers.
Use Cases
- Personal Care and Cosmetics: Creams, lotions, toothpaste, and shampoos benefit from airtight seals and aesthetic appeal.
- Pharmaceutical Products: Ointments, gels, and oral care products rely on tamper resistance and extended shelf life.
- Food & Industrial: Condiments, sauces, powdered beverages, and small hardware use laminated tubes for barrier protection and dispensing convenience.
Advantages
- Barrier Protection: Multi-layer design blocks moisture, oxygen, and light, extending shelf life.
- Customisation: Available in diverse sizes, shapes, and prints for brand differentiation.
- Squeezable for Easy Use: Designed to dispense products smoothly with minimal effort, ensuring precise control and less waste.
- Vibrant Branding: High-resolution printing on a smooth surface showcases logos and graphics sharply, boosting shelf appeal.
- Lightweight Efficiency: Compact shape slashes shipping costs and optimises storage, both in transit and on retail displays.
Disadvantages
- Recycling Challenges: Mixed materials (plastic/aluminum) complicate recycling processes.
- Higher Production Cost: Complex layering and adhesives increase expenses compared to single-material packaging.
- Heat Sensitivity: Deforms under high temperatures, limiting use for hot-fill products.
- Permeability Issues: Some chemicals or oils (e.g., citrus oils, acetone, oily pharmaceuticals) penetrate non-specialized barriers like basic aluminum/EVOH layers. Specialised barriers (high-barrier EVOH, metallised films) prevent leakage but cost 20–50% more.
- Delamination Risk: Poor manufacturing or handling can separate layers, compromising integrity.
Glass Containers, Jars, and Bottles
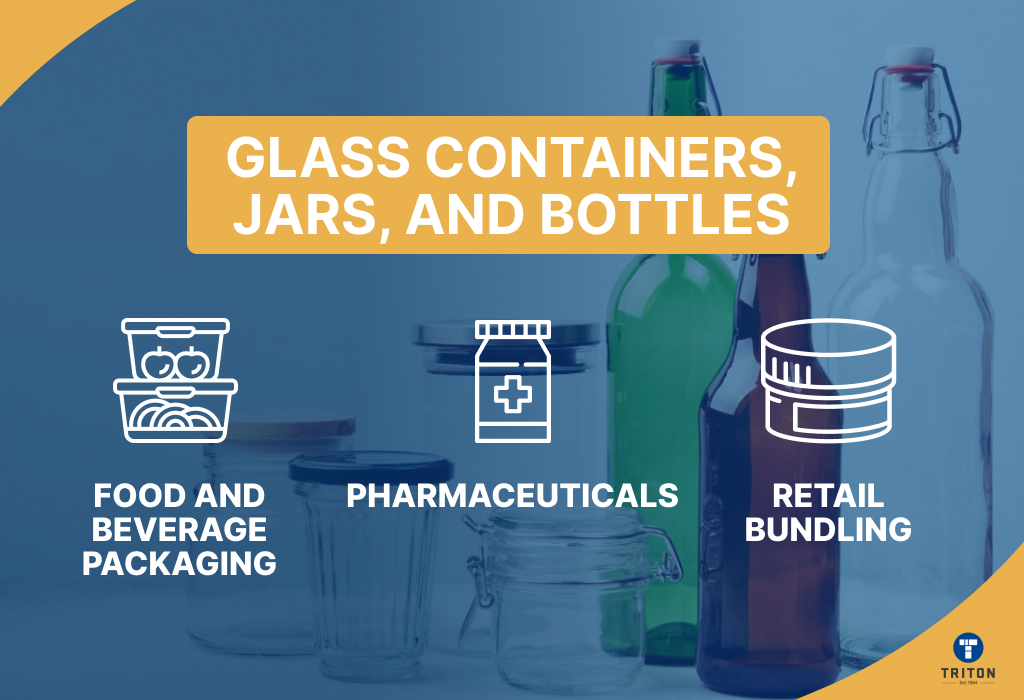
Glass containers—jars and bottles—are durable, reusable, and recyclable, valued for their premium appearance and strong barrier properties. Made from silica (sand), sodium carbonate (soda ash), and calcium carbonate (limestone), glass is non-porous and chemically inert. It blocks oxygen and moisture, maintains product integrity, and prevents chemical leaching or flavor changes, making it ideal for preserving food, beverages, cosmetics, and pharmaceuticals.
Use Cases
- Food and Beverage: Jams, sauces, oils, carbonated drinks, and acidic foods (e.g., vinegar). Glass prevents flavor transfer, resists corrosion, and withstands high-temperature processing.
- Cosmetics and Skincare: Creams, serums, oils. Glass blocks UV light, ensures chemical stability, and supports premium branding.
- Pharmaceuticals: Medicines, supplements, vaccines, injectables. Glass provides sterile, tamper-evident packaging compatible with sterilisation (e.g., autoclaving).
Advantages
- Barrier Protection: Blocks oxygen, moisture, and contaminants; impermeable to gases and vapors.
- Endless Recyclability: Can be recycled repeatedly without quality loss; reduces energy use with recycled cullet.
- Chemical Stability: Non-reactive (FDA GRAS-approved); prevents flavor/chemical transfer in food, beverages, and pharmaceuticals.
- Transparency: Allows product visibility; enhances consumer trust and premium branding.
Disadvantages
- Weight and Fragility: Modern glass bottles are 40% lighter today (averaging 350–450 grams) compared to their 1990s counterparts (550–900 grams), with innovations like chemical-strengthened ultrathin walls slimming champagne bottles from 900g to 800g. Lightweighting reduces CO2 emissions by 5–7% per 10% weight cut, slashing shipping costs by millions annually. Industry targets aim for standard bottles below 420 grams by 2026, nearing 300g using ion-exchange technology. Despite thinner designs, breakage rates remain stable, demonstrating how advanced engineering resolves the fragility-function tradeoff.
- Energy-Intensive Production: Requires temperatures up to 2,800°F (1,538°C); contributes to higher carbon footprint.
- Rigid Design Constraints: Limited to rigid shapes; unsuitable for squeezable or flexible packaging needs.
Aluminum Cans and Foil
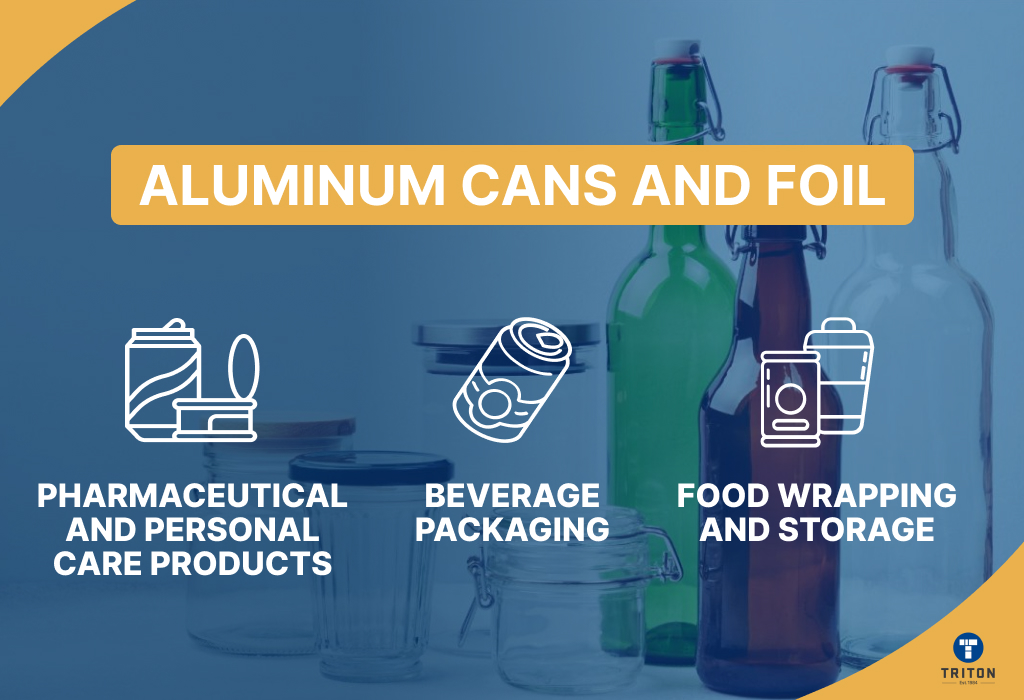
Aluminium cans and foil are lightweight, corrosion-resistant, and versatile packaging materials used across food, beverage, and pharmaceutical industries. Aluminum provides an excellent barrier against light, moisture, and oxygen, preserving product freshness and quality. Cans are commonly used for beverages, while foil is ideal for food wrapping, cooking, and insulation. Both are infinitely recyclable, though production and recycling processes are energy-intensive.
Use Cases
- Beverage Packaging: Aluminum cans hold 25% of the global beverage packaging market, primarily for sodas, beer, and energy drinks.
- Food Wrapping/Storage: Aluminum foil is used in ~60% of perishable food packaging and 40% of shelf-stable products (e.g., soups sauces).
- Pharmaceutical/Personal Care Products: 70% of global pill packaging uses aluminium blister packs, while creams and ointments rely on foil tube seals.
Advantages
- Excellent Barrier Properties: Blocks 100% of light/oxygen; extends shelf life by 2–3 years for oxygen-sensitive products.
- Lightweight and Strong: Cans weigh 40% less than glass, reducing global shipping emissions by 15–20%.
- Recyclable and Eco-Friendly: 69% of aluminium cans are recycled globally, saving 95% energy vs. primary production.
- Heat Resistant: Withstands temperatures up to 660°C, enabling use in cooking, sterilisation, and ready-meal trays.
Disadvantages
- Energy-Intensive Production: Producing 1kg of aluminium emits 11.5kg CO2 (global average), with smelting consuming 5% of global electricity.
- Dents Easily: Rough handling damages 10–15% of cans during transit.
- Design Limits for Foil: Limited to wraps, seals, and laminates; lacks structural complexity compared to plastics.
Wooden Crates
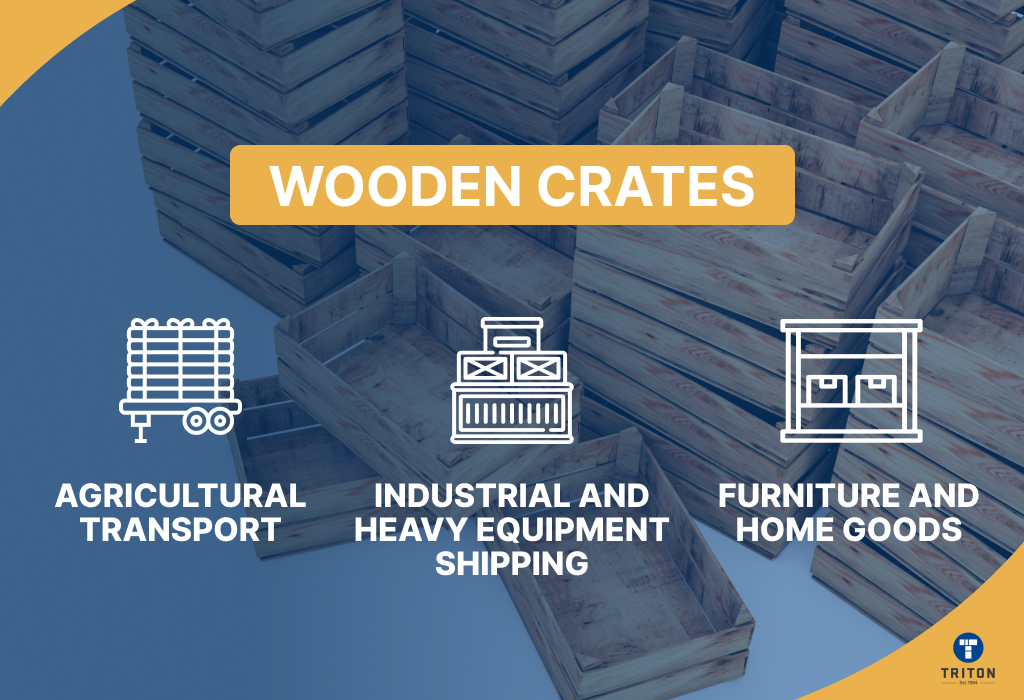
Wooden crates are durable, reusable containers made from pine, plywood, or hardwood. Depending on design and reinforcement (e.g., steel bracing), they support loads from 75 kg (standard crates) to 1,800 kg (heavy-duty variants). Widely used in agriculture, manufacturing, and shipping, their biodegradable and reusable nature aligns with sustainability goals, while their strength ensures safe transport of heavy machinery, perishables, and industrial goods.
Use Cases
- Agricultural Transport: Slatted designs provide ventilation for fruits, vegetables, and perishable goods.
- Heavy Equipment Shipping: Reinforced wooden crates with steel bracing or metal supports protect machinery and tools during transport.
- Furniture and Home Goods: Ensure structural integrity for large items during long-distance shipping.
Advantages
- High Durability and Strength: Sustain heavy loads and rough handling; automotive industries use them for machinery parts.
- Reusable and Eco-Friendly: Reduce energy use by 95% compared to new crate production.
- Customizable and Stackable: Built in multiple sizes with stackable designs; optional handles, hinges, or foam inserts.
- Natural Ventilation: Slatted gaps reduce spoilage in produce by enabling airflow.
Disadvantages
- Weight: Add 20–30% higher airfreight costs compared to plastic or aluminium.
- Moisture Sensitivity: Untreated wood warps or rots; requires water-resistant coatings for wet environments.
- Cost: Higher initial cost than plastic or cardboard, offset by reuse potential.
- Regulations: Require ISPM-15 compliance (heat treatment) for international shipping.
Wooden Pallets
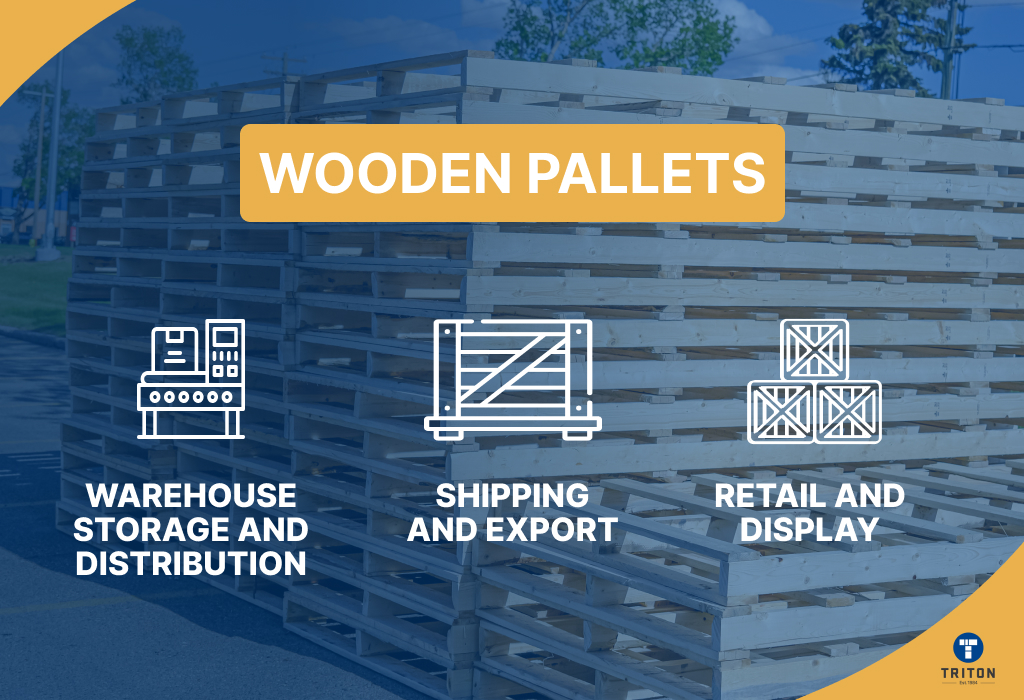
Wooden pallets are flat, sturdy platforms made primarily from pine or hardwood, designed for stacking, storing, and transporting goods. They are widely used in logistics, retail, and manufacturing due to their strength, reusability, and compatibility with forklifts and pallet jacks. Wooden pallets are eco-friendly, as they are recyclable and biodegradable, aligning with sustainability goals.
Use Cases
- Automotive and Heavy Industry: Used to transport engine parts, machinery, and bulk components due to high load-bearing capacity.
- Pharmaceuticals: Serve as hygienic, heat-treated platforms for transporting medical supplies (compliant with GMP standards).
- Reverse Logistics: Facilitate recycling/returns management by enabling efficient handling of bulk goods.
Advantages
- High Load Capacity: Static loads up to 4,000 kg, dynamic loads up to 1,500 kg (vs. plastic pallets’ 800–1,200 kg).
- Energy-Efficient Recycling: Repurposing saves 75% energy vs. new pallet production.
- Reusable and Eco-Friendly: Can be reused multiple times and are recyclable, supporting sustainable practices.
- Low-Cost Repairs: Damaged boards can be replaced cheaply, extending lifespan by 3–5 years.
Disadvantages
- Moisture Sensitivity: Untreated wood absorbs water, risking mold; ISPM-15 compliance (heat treatment) adds $3–5 per pallet.
- Weight Penalty: Avg. 15–25 kg/pallet increases fuel costs by 5–8% vs. plastic alternatives.
- Maintenance Costs: Require regular inspection for splintering/cracks; lifespan reduced to 2–3 years in high-humidity regions.
- Chemical Treatments: Fungicides/pesticides used for pest resistance may leave residues, limiting reuse in food/pharma.
Woven Sacks
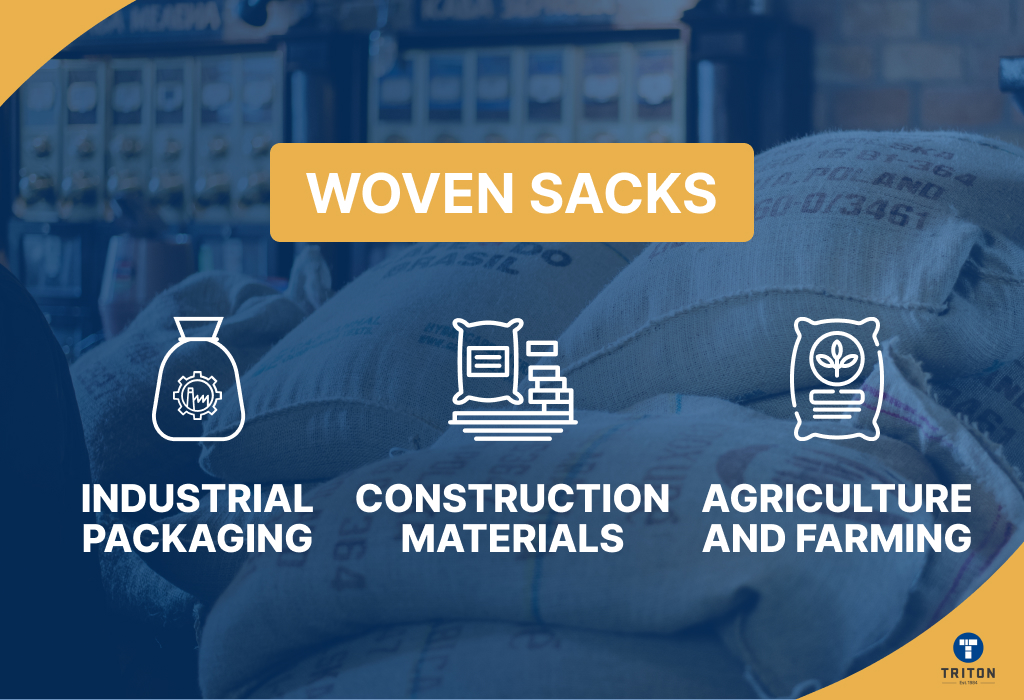
Woven sacks are manufactured using circular looms that interlock polypropylene (PP) or polyethylene (PE) tapes into a crosshatched pattern, achieving tensile strengths of 20–30 MPa.
Load capacity ranges from 25 kg (standard) to 100 kg (reinforced seams), outperforming paper sacks by 3x.
Designed for bulk material handling, they balance durability, breathability, and cost-efficiency, making them indispensable in agriculture (grains, seeds), construction (sand, cement), and industrial sectors (fertilisers, chemicals). Their lightweight design reduces shipping costs, while UV-resistant variants extend usability in harsh environments. Yet strong enough to withstand heavy loads, making them a reliable option for high-volume transport.
Use Cases
- Agriculture and Farming: Woven sacks are used to store and transport grains, rice, seeds, and fertilisers. Their breathable design allows airflow, preventing mold and spoilage, while protecting contents from contamination.
- Construction Materials: Ideal for carrying sand, gravel, cement, and other construction aggregates. Their durability and flexibility make them a cost-effective solution for heavy-duty applications.
- Industrial Packaging: Industrial Packaging: Used for chemicals, minerals, and bulk industrial goods. Woven sacks with laminated liners or UV-resistant coatings provide additional protection for sensitive materials.
- Mining: Transport minerals like coal and gypsum in UV-stabilized sacks (up to 1,000 cycles of reuse).
Advantages
- High Strength and Durability: Woven sacks can support heavy loads (up to 50 kg or more) and withstand rough handling, making them ideal for bulk products.
- Breathable Material: Allows airflow, preventing moisture buildup, which is essential for perishable goods like grains and seeds.
- Lightweight and Cost-Effective: Reduces overall shipping weight, lowering transport costs. A typical woven sack costs.
- Recyclable and Reusable: Many woven sacks are reusable and recyclable, supporting sustainability initiatives. Some manufacturers use recycled polypropylene to produce new sacks, reducing environmental impact. Recycling 1 ton of PP woven sacks saves 5.7 barrels of oil and reduces CO2 emissions by 1.5 tons.
Disadvantages
- Limited Moisture Resistance: While breathable, woven sacks are not fully waterproof unless laminated or coated. This makes them unsuitable for wet environments or moisture-sensitive goods.
- Prone to UV Degradation: Prolonged exposure to sunlight can weaken the material, reducing lifespan. UV-resistant coatings are available but add to costs.
- Limited Customization: Typically available in basic designs with limited printing options, which may not meet branding needs for retail packaging. Custom designs often require higher minimum order quantities.
Jute Bags
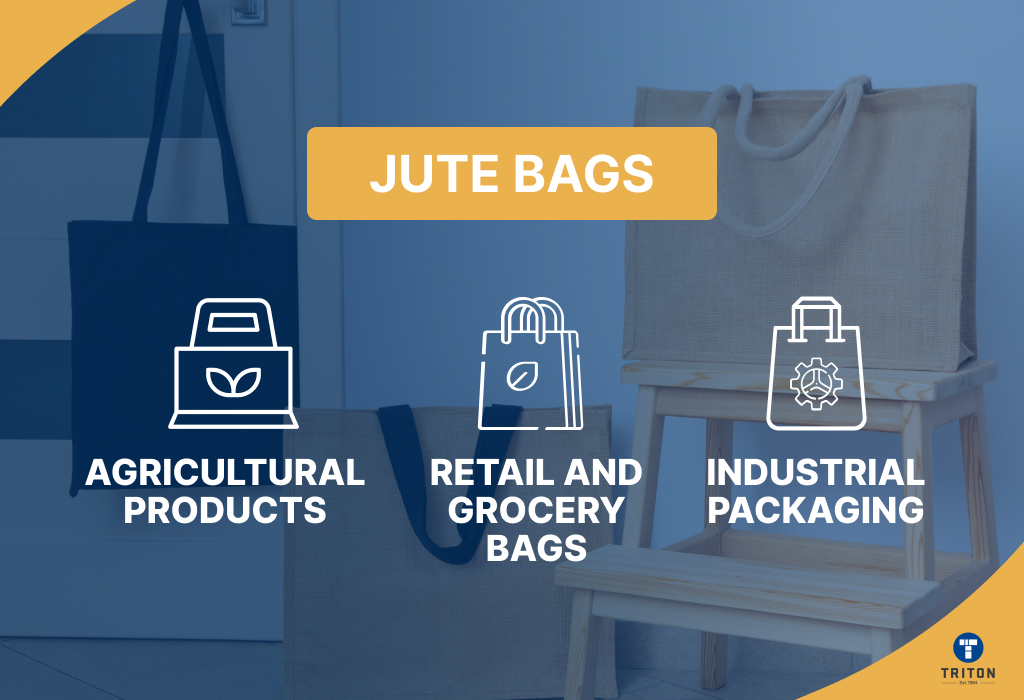
Jute bags are manufactured from natural jute fibers (Corchorus spp.), composed of ~65% cellulose, ~22% hemicellulose, and ~10% lignin. These fibers provide a tensile strength of 200–400 MPa, enabling load capacities up to 50 kg. The open-weave structure (5–10 threads/cm) allows airflow (permeability: 50–100 cm³/cm²/s) critical for perishable goods like grains.
Jute cultivation requires 8–12 tons/hectare of biomass, absorbs 15 tons CO2/hectare, and grows in 120 days. Bags are produced via ISO 9001-certified processes, meeting standards for bulk packaging (ISO 21898:2004).
Use Cases
- Agricultural Products: Jute bags are used to store and transport grains (wheat, rice), coffee beans, and potatoes in tropical climates like India and Bangladesh. Their breathability reduces spoilage rates by 10–15% compared to plastic bags in these regions.
- Retail and Grocery: Jute bags are used to replace single-use plastics in the EU and Canada, where 30% of supermarkets utilise them for fresh produce like fruits and vegetables.
- Industrial Packaging: Jute sacks are used to ship bulk materials (e.g., sand, cement) in 50 kg loads, particularly in eco-conscious markets. For example, India’s construction sector employs 4 million jute sacks annually for cement transport.
- Geotextiles: Jute mesh is used to control soil erosion in agriculture (with a permeability rate of 50–100 cm³/cm²/s) and stabilize embankments in civil engineering projects like road construction.
Advantages
- Biodegradability: Decomposes in 1–2 years (vs. 500+ years for plastic) with zero microplastic residue; compostable under ASTM D6400.
- Tensile Strength: 200–400 MPa fiber strength supports loads up to 50 kg; outperforms cotton bags by 3x.
- Carbon Sequestration: Jute cultivation absorbs 15 tons CO2/hectare and requires 8x less water than cotton.
- Cost-Efficiency: Raw jute costs 0.30 – 0.30–0.50/kg vs. $1.20/kg for organic cotton.
Disadvantages
- Moisture Absorption: Untreated jute absorbs 30–40% moisture by weight, weakening fibers. Laminated liners add 20–30% cost.
- UV Degradation: Loses 50% tensile strength after 6 months of sun exposure; UV-resistant coatings increase costs by 15%.
- Print Limitations: Screen printing on jute achieves 72 dpi resolution (vs. 300+ dpi on polyester), limiting brand visuals.
- Hygiene Constraints: Cannot be washed with water; microbial growth risks in humid storage.
Bubble Wrap
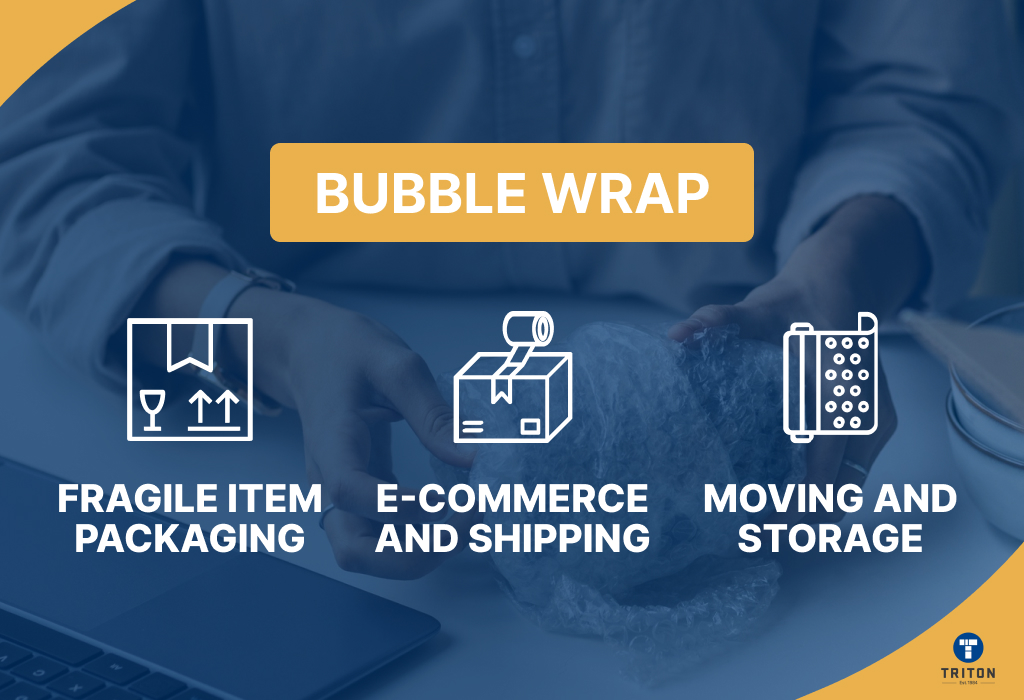
Bubble wrap is made from low-density polyethylene (LDPE) or linear low-density polyethylene (LLDPE), forming air-filled bubbles (6–40mm diameter) that absorb shocks and vibrations. Alfred Fielding and Marc Chavannes invented it in 1957 as textured wallpaper, but after failing in that market, IBM repurposed it in the 1960s to protect computer components during shipping.
Today, industries like e-commerce and logistics rely on its lightweight cushioning for safe transport. However, polyethylene’s non-biodegradable nature poses environmental challenges, prompting innovations like biodegradable PLA blends and recycled-content variants.
Use Cases
- Protect Fragile Items:Used for securing glassware, electronics, and ceramics during transit, minimising damage from impacts and vibrations.
- E-commerce: Reduce breakage in shipments, with 70% of bubble wrap sales driven by online retail logistics.
- Relocations: Safeguard household or industrial items during moves using adaptable cushioning.
- Safeguard Industrial Components: Protect automotive parts, machinery, and sensitive equipment in transit.
Advantages
- Shock Absorption: Air-filled bubbles withstand 20–50 kPa pressure, shielding items from drops and vibrations.
- Lightweight: Rolls weigh 1–2 kg, reducing shipping costs and handling effort.
- Customisable: Bubbles range from 6–40mm diameter to accommodate irregularly shaped items.
- Reusability: Undamaged wraps can be reused, lowering short-term packaging waste.
Disadvantages
- Environmental Persistence: Traditional LDPE takes 10–1,000 years to decompose in landfills.
- Aesthetic Limitations: Lacks visual appeal for consumer-facing packaging, requiring secondary branding materials.
- Storage Challenges: Bulky design occupies 2–3x more space than flat alternatives like air pillows.
- Carbon Footprint: Production emits 11.5 kg CO₂ per kilogram of polyethylene, contributing to climate impact.
Cushioning Materials
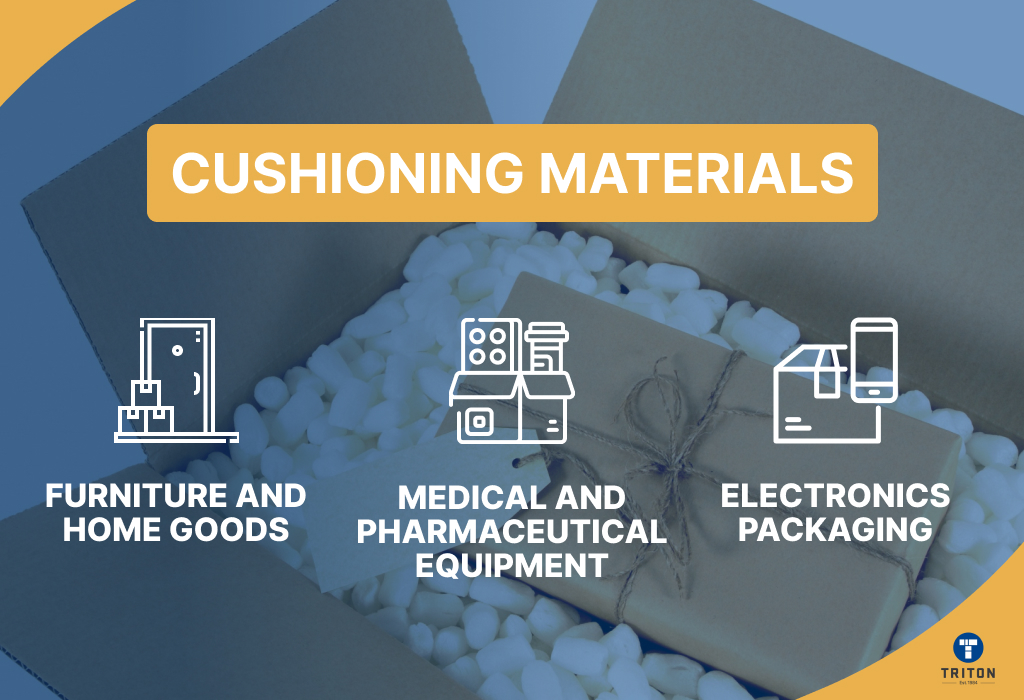
Cushioning materials absorb shocks, vibrations, and impacts during shipping, storage, and handling, safeguarding products from damage.
Common variants include polyethylene foam, air-filled plastics, paper-based fillers, and molded pulp, each offering tailored protection based on product fragility and logistical requirements.
Industries such as electronics, pharmaceuticals, and e-commerce rely on these materials to protect high-value and fragile items. Sustainable options like biodegradable PLA foam and recycled paper fillers decompose within 1–2 years, while traditional plastics like EPS foam persist in landfills for centuries, with only 10% recycled globally.
Use Cases
- Electronics Packaging: Protects delicate devices like smartphones, laptops, and cameras from impact during transit. For example, 30% of electronics manufacturers use foam inserts for shock absorption.
- Furniture and Home Goods: Cushions large items like furniture or glassware, preventing scratches, dents, or breaks. Corrugated cardboard wraps and air pillows are popular choices.
- Medical and Pharmaceutical Equipment: Safeguards sensitive instruments and devices from shock and vibration. Molded pulp trays and anti-static foam are commonly used.
- E-commerce: Accounts for 60% of cushioning material demand, driven by the need to protect goods during last-mile delivery.
Advantages
- Impact Absorption: Reduces shock by 60–80%, lowering damage rates during transit.
- Versatility: Available in multiple forms – foam inserts, bubble wrap, paper fillers, and air pillows—to suit diverse packaging needs.
- Customisation: Materials like die-cut foam and molded pulp can be tailored to fit specific product shapes, minimising movement.
- Sustainability: Paper-based fillers and PLA-based biodegradable foams are recyclable and compostable, supporting eco-friendly practices.
Disadvantages
- Environmental Impact: Plastic-based materials like EPS foam and bubble wrap are non-biodegradable, contributing to landfill waste. Only 10% of EPS foam is recycled globally.
- Storage Space: Bulky materials like foam and bubble wrap occupy 2–3x more space than flat alternatives.
- Higher Costs: Sustainable options, such as molded pulp and biodegradable foam, cost 20–50% more than traditional plastics.
- Messy Handling: Loose-fill materials like packing peanuts scatter easily, complicating cleanup and reuse.
Plastic Pallets
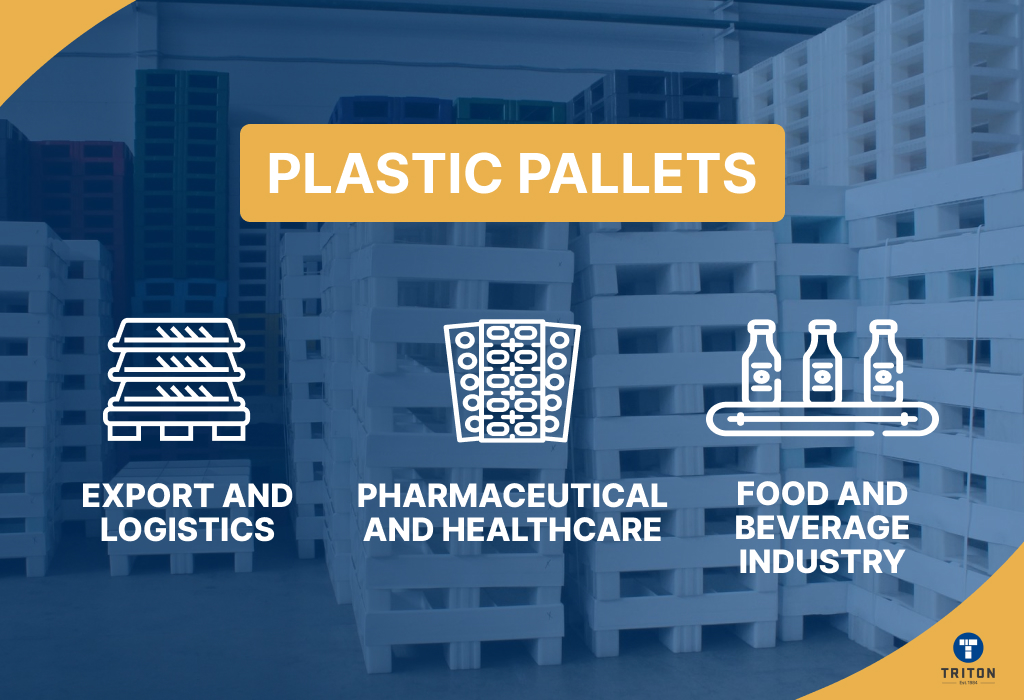
Plastic pallets are platforms made from high-density polyethylene (HDPE) or polypropylene (PP). They resist moisture, chemicals, and extreme temperatures, making them suitable for industries like food, pharmaceuticals, and manufacturing.
Unlike wooden pallets, plastic pallets do not splinter, absorb moisture, or require ISPM-15 treatments for international shipping. They are reusable, with a lifespan of 5–10 years, and some variants include 30–50% recycled material.
Use Cases
- Food and Beverage: Used in food handling and storage due to their non-porous surface, which prevents contamination. They can withstand -40°C to 80°C, making them ideal for cold chain logistics.
- Pharmaceuticals: Meet GMP standards for hygiene, allowing repeated sanitisation in sterile environments.
- Export and Logistics: Comply with ISPM-15 standards without requiring heat or chemical treatments, reducing costs for international shipping.
- Automotive and Manufacturing: Support heavy loads (up to 2,500 kg) and resist oil, grease, and chemicals common in industrial settings.
Advantages
- Durability: Resistant to wear and tear, with a lifespan of 5–10 years (vs. 3–5 years for wood).
- Hygiene: Non-porous surface resists moisture, chemicals, and bacteria, making them easy to clean and sanitise.
- Lightweight: Weigh 15–25 kg (vs. 20–40 kg for wood), reducing shipping costs and handling effort.
- Recyclability: Many pallets use 30–50% recycled materials and are fully recyclable at end-of-life.
Disadvantages
- Higher Upfront Cost: Cost $ 50–100 per pallet (vs. $10–20 for wood), though long-term savings offset initial expenses.
- Non-Biodegradable: Despite recyclability, improper disposal contributes to plastic waste. Only a small percentage of plastic pallets are recycled globally.
- Slippage Risk: Smooth surfaces reduce friction, increasing the risk of load slippage during transport.
- UV Degradation: Prolonged sun exposure weakens plastic, reducing lifespan in outdoor storage.
Wooden Containers

Wooden containers are durable and sturdy packaging solutions made from plywood, hardwood (e.g., oak, maple), or softwood (e.g., pine).
They are ideal for heavy-duty applications, particularly for transporting large machinery, industrial equipment, and fragile items. Their rigid structure and resilience ensure high-level protection during transit.
Wooden containers are eco-friendly, as they are reusable, biodegradable, and often made from sustainably sourced materials. They comply with ISPM-15 standards for international shipping, requiring heat treatment or fumigation to prevent pest infestations.
Use Cases
- Industrial and Heavy Equipment Shipping: Transport large, heavy items like machinery, tools, and automotive parts. Wooden containers can handle loads up to 4 metric tons, making them suitable for heavy-duty applications.
- Fragile or High-Value Goods: Protect delicate items like glassware, artwork, and antiques. Their robust construction minimises damage from impacts and vibrations during transit.
- Export Packaging: Ideal for international shipping due to their durability and compliance with ISPM-15 standards. Treated wooden containers prevent pest infestations and meet global shipping regulations.
- Agricultural Products: Designed with ventilation gaps, wooden containers are used for transporting perishable goods like fruits and vegetables, ensuring airflow and reducing spoilage.
Advantages
- High Durability and Strength: Handle heavy loads (up to 4 metric tons) and protect contents during rough handling and long-distance transport.
- Reusable and Eco-Friendly: Can be reused multiple times, and wood is biodegradable and recyclable. Recycling wooden containers saves 95% of the energy required to produce new ones.
- Customizable and Stackable: Built to various specifications, including custom sizes and designs. Stackable designs optimise storage and shipping efficiency.
- Natural Ventilation: Ventilation gaps in wooden containers make them suitable for agricultural products, reducing spoilage by maintaining airflow.
Disadvantages
- Heavy and Bulky: Wooden containers weigh 20–40 kg, increasing shipping costs and making handling more labor-intensive .
- Moisture Sensitivity: Untreated wood absorbs moisture, leading to warping or rot. Proper treatment (e.g., waterproof coatings) is required for humid environments.
- Higher Upfront Cost: Initial costs range from $ 60–200 per container, higher than lightweight alternatives like plastic or cardboard. However, reusability offsets long-term costs.
- Pest Vulnerability: Untreated wood is susceptible to pests like termites, requiring ISPM-15 compliance for international shipping.
Conclusion
Packaging materials protect products, but efficient workflows require more. Thermal printers, barcode scanners, and label applicators ensure accuracy in tracking, shipping, and inventory management.
At Triton Store, we equip businesses with tools to simplify logistics—no packaging sold, just the tech to make it smarter.
Need durable printers or scanners that keep up? We’ve got you covered. Cut errors, save time, and focus on what matters. Visit the Triton Store today.