Manual labelling machines create production bottlenecks, reduce throughput, and increase the chance of human error in high throughput environments.
Keeping up with large-scale orders? Forget about it if you are using manual weighing and labelling.
As industries increasingly turn to automation to stay competitive, the automatic weigh labelling machine market is projected to reach US $ 635.3 million by 2034.
If you are unfamiliar with automatic weigh labelling machines, this article explains how they work. We will explore the components and operating principles of these machines.
Components and Functioning of Automatic Weigh Labelling Machines
Automatic weigh-labelling machines are tightly coupled components for accurate, consistent, and fast product labelling. The core components include conveyor systems, scales, print-and-apply systems, and data management solutions.
Let’s look at these components one by one.
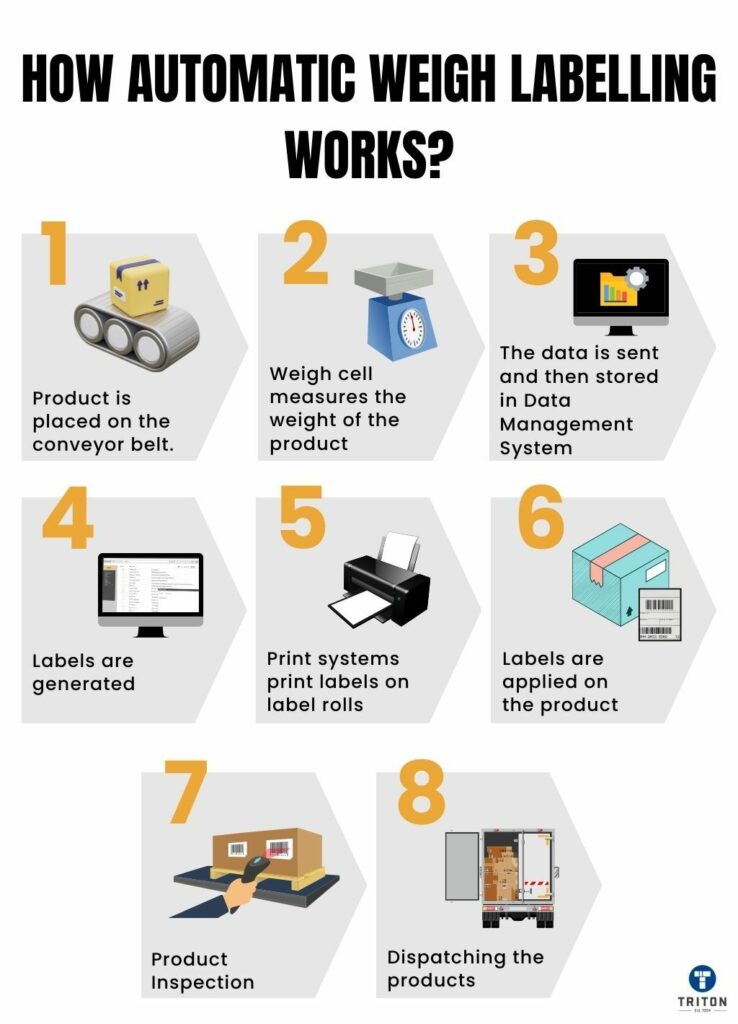
Conveyor System
The conveyor system handles the movement of products and usually includes three belts:
- In-feed conveyor
- Conveyor scale
- Out-feed conveyor
This section will explain the in-feed conveyor.
Products are placed on the in-feed conveyor, which uses adjustable guides and sensors to centre and space them based on product size. Sensors detect the product position, and the system adjusts the conveyor speed dynamically to maintain proper spacing between products.
Dynamic speed control creates a smooth flow for subsequent operations like weighing and labelling.
Conveyor Scale
In a conveyor scale system, the product is weighed while moving, using in-motion weighing technology.
The weighing belt passes the product over a sensitive load cell, such as an electromagnetic force compensation (EMFC) load cell. These load cells can capture precise weight measurements even when the product is in motion.
The conveyor scale system relies on sensors placed along the conveyor. These sensors detect the product position and synchronise the load cell to capture the weight when the product is over the scale.
The load cell continuously tracks the force applied to it, even when no product is present, and immediately records the weight when a product passes over it. |
This method eliminates the need for stopping the conveyor to weigh.
Connectivity and Data Management
Data management in automatic weigh labelling machines is handled by industrial PCs with Windows-based, often Windows 10, operating systems and solid-state drives (SSDs). Other commonly used systems include embedded Linux platforms and custom-built, real-time operating systems.
These systems collect weight data, product details, and other relevant information.
TCP/IP Ethernet and Serial RS232 connections handle the data transfer between subsystems. Once processed, the data is sent to the printer for label generation and stored for later use.
Print System
The print system receives data from the database and prints it onto labels using a specific digital printing technique, such as thermal printing, continuous inkjet printing, or laser printing. Each labelling system typically has only one printing technology based on the application requirements.
Some weigh-labelling systems have a modular design, allowing the printing technology to be swapped.
Labels are printed directly onto the label roll as it moves through the labeller. Thermal transfer and direct thermal printing are the most common printing technologies in automatic weight labelling systems.
The main components of the print system are the label dispenser, labelling head, and label sensor.
Once the label design is finalised, the print system prints labels directly on the label roll as it passes through the labeller. Depending on the application, printing technologies, such as thermal transfer or direct thermal printing, can be used.
The label dispenser separates individual labels from the continuous roll with peelers or vacuum systems.
The label sensor detects the presence of a label and ensures the dispenser is in position. It also stops the system from starting without the label.
The labelling head picks up the label from the unwind stand with vacuum pads or belt systems. Common techniques for applying the label on the product are as follows:
- Blow Application: Transfers the label using air pressure without contact, which is ideal for fragile or irregular items.
- Stamp Application: A mechanical arm presses the label onto the product surface.
- Vacuum Belt Application: Applies the label smoothly with suction and pressure, suited for larger products.
Label Verification System
After labelling, products move to the out-feed conveyor, where sensors verify that the labels are correctly positioned and the information is accurate and readable.
The rejection system is activated when a product’s weight or label falls outside the required standards. The rejection system uses air jets or pneumatic pushers to remove defective items from the production line.
Unused labels are collected by a label rewinder, which processes them for reuse or disposal.
The label verification system stops any product with incorrect weight or labelling from continuing on the production line.
Benefits of Automated Weigh Labelling Machines Over Manual & Semi Automatic Weigh Labelling Machines
Throughput
Automatic weigh labelling machines can process up to 150 items per minute. Their speed is significantly faster than manual (c. 5 per minute) or semi-automatic systems (c. 30 per minute).
Accuracy
Automatic weight labelling systems provide precise weight measurements with an error margin as low as ±1-5 grams. Load cell technology such as electromagnetic force compensation (EMFC) load cells, achieves this accuracy. Combined with advanced sensors, these systems ensure that labels are applied correctly.
These systems ensure that only products meeting the required weight range continue down the production line, improving quality control and reducing risk.
Flexibility & Features
Automatic check weighing systems are versatile and can accommodate different product shapes, sizes, and weights. They adjust easily to specific production needs and can be integrated into existing lines.
Features like a colour screen HMI allow operators to monitor processes, make adjustments, and save settings for easy access, enhancing overall operational flexibility.
A Note on HMI A Human-Machine Interface (HMI) in automatic weigh labelling systems allows operators to monitor and control the labelling process. It displays real-time data, enables adjustments, and alerts for issues. In Automatic Weigh Labeling Machines, Panel-Mount HMIs are commonly used for on-site control. They have touchscreen or keypad interfaces for real-time monitoring and adjustments. Touchscreen HMIs, either capacitive or resistive, allow operators to input commands directly and control the labelling process. Industrial Panel PCs HMI combine machine control and data processing. Industrial Panel PC HMI are used in complex systems. Finally, Web-Based or Remote HMIs enable operators to monitor and control the system from devices like laptops or smartphones, providing flexibility for remote operation. |
Challenges in implementing automatic weigh labelling systems in existing production lines
The high initial costs of purchasing and installing these systems can be a financial strain for small businesses. To overcome this obstacle a solid business case needs to be established factoring in such things as labour replacement, fewer product rejections, higher accuracy of label placement and more. Business cases can often repay the system implementation in 18 months or less.
Other considerations when implementing these systems are training and adaptation are necessary, as employees need time to learn the new equipment, which can temporarily impact productivity.
Maintenance needs also increase with these systems, as regular upkeep is required to avoid breakdowns and reduce downtime.
Integrating these systems with Product Information Management (PIM) software may disrupt current workflows initially, requiring close coordination between IT and operations teams.
Spreading the initial investment, scheduling phased training sessions, and establishing regular maintenance schedules can mitigate these challenges. Careful planning of PIM integration, with proper collaboration between IT and production teams, can ensure a smoother transition and long-term benefits.
The Bottom Line
Automatic weigh labelling machines have made the labelling process much simpler and faster. These machines improve efficiency by being more accurate, increasing output, and reducing wasted time, making the entire process more effective.
By automating the labelling process, these machines eliminate human error, ensure consistent label application, and maintain high production speeds. This reduces labour costs and creates a safer working environment by minimising the need for manual work.
As more industries start using these specialised machines, their benefits will become even more significant. This will lead to higher productivity and efficiency. Adopting this technology transforms business operations, preparing them to compete better in the market.