Packaging serves as the critical interface between a product and its consumer, pivoting in branding, protection, and the overall user experience. As such, the evolution of packaging print technologies has been instrumental in elevating product presentation and market differentiation.
This guide explores the range of printing technologies available for packaging, highlighting how each method can be leveraged to meet specific marketing and functional demands.
Flexography Printing
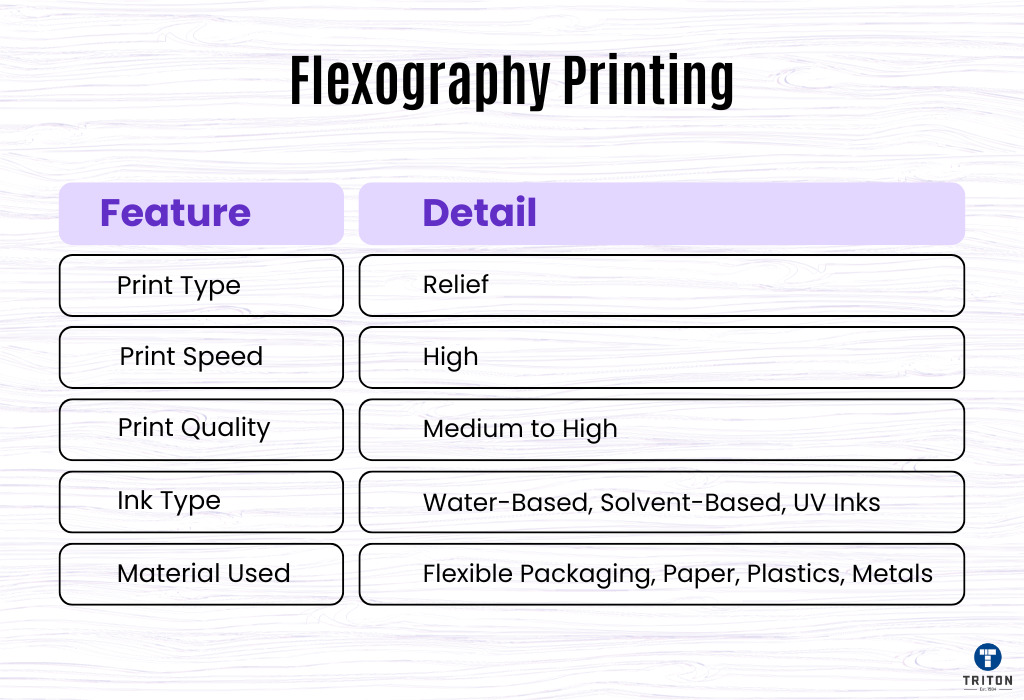
Feature | Details |
---|---|
Print Type
| Relief |
Speed | High |
Quality | Medium to high
|
Ink Type
| Water-based, solvent-based, UV inks
|
Materials Used
| Flexible packaging, paper, plastics, metals
|
Flexography, often abbreviated as flexo, is a highly versatile printing technique. This method uses a flexible relief plate to print on various substrates, including plastics, metallic films, cellophane, and paper.
Flexography’s adaptability makes it ideal for decorating and labelling everything from food packaging and beverage containers to wallpaper and gift wrap.
How Does Flexography Work?
The flexographic printing process involves fast-drying, low-viscosity inks applied to a flexible photopolymer plate mounted on a rotating cylinder. As the substrate passes through the press, it contacts the inked plates, which transfer the design directly onto the material.
Using rotary die-cutting within the same equipment allows simultaneous printing and cutting, greatly enhancing production efficiency.
Common Uses in the Industry
Flexography is predominantly used for large-scale printing projects such as shopping bags, food and beverage containers, and corrugated cardboard boxes. It can print on a wide range of materials and is characterised by rapid-drying inks.
Advantages
- Speed: Flexography machines operate at high speeds, making them suitable for large runs.
- Cost Efficiency: The process is cost-effective for large volumes due to the minimal downtime and rapid production rates.
- Versatility: It can print on various substrates, including non-porous materials that are challenging for other printing techniques.
- Quality and Durability: Flexographic inks are durable and resistant to fading, which is crucial for products exposed to various environmental conditions.
Disadvantages
- Setup Cost: Initial setup costs are high due to the need for custom printing plates.
- Graphic Detail: While improvements have been made, flexography traditionally does not match the high detail achievable with other printing methods, such as thermal printing.
Lithography Printing
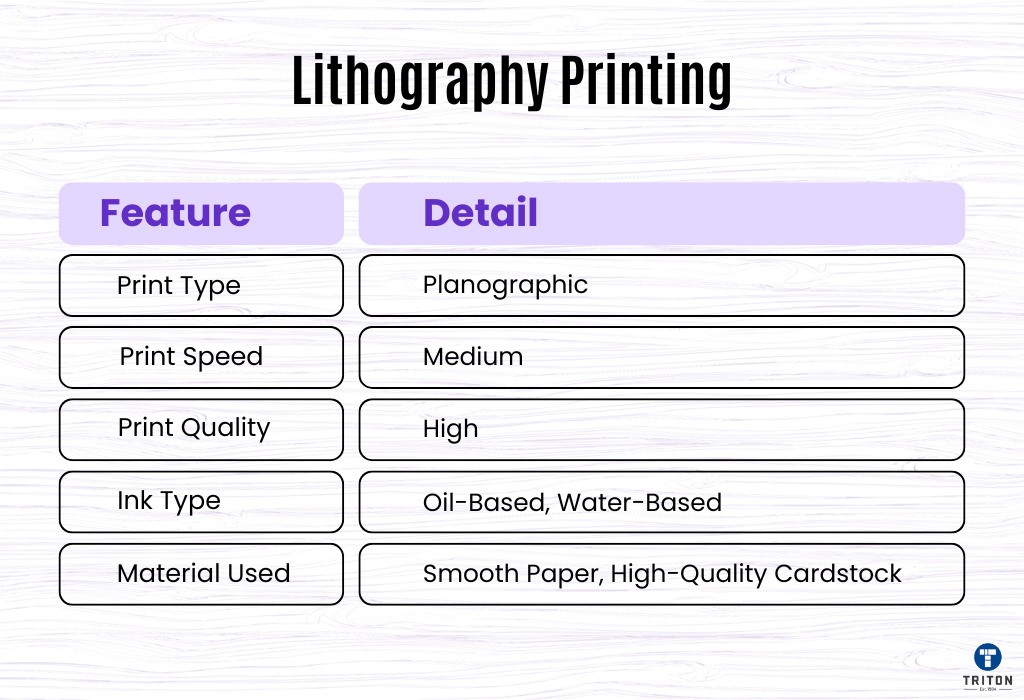
Feature | Details |
---|---|
Print Type
| Planographic |
Speed | Medium |
Quality | High |
Ink Type
| Oil-based, water-based
|
Materials Used
| Smooth paper, high-quality cardstock
|
Lithography is a distinguished planographic printing method known for its high-quality output. It excels at printing detailed graphics on packaging materials, making it ideal for premium products. This technique uses a flat plate that is chemically treated to interact differently with inks and water.
How Does Lithography Work?
Lithography involves creating an image on a flat plate, usually made of aluminium. This aluminium plate is then treated chemically so that the image areas attract oily inks while non-image areas attract water.
Water rollers moisten the plate during printing, repelling ink from the non-image sections. Following this, ink rollers coat the image areas with ink. The inked image is then transferred—or “offset”—from the plate to a rubber blanket and finally onto the printing surface, such as paper or cardboard.
Common Uses in the Industry
Lithography is widely used for printing detailed graphics on cartons, books, newspapers, and high-quality labels. It is particularly effective for packaging products that require vibrant, full-colour images, like cosmetic boxes, pharmaceutical packaging, and food packaging with appealing visual designs.
Advantages
- Image Quality: Offers exceptional print quality with rich, precise colours and fine details.
- Efficiency: Suitable for high-volume printing as the plates last for millions of impressions.
- Material Flexibility: Can print on metal, plastic, and other materials.
Disadvantages
- Setup Time and Cost: The process requires extensive setup with plate creation, making it less economical for short runs.
- Maintenance: The complexity of the machinery requires regular maintenance and skilled operators.
Gravure Printing
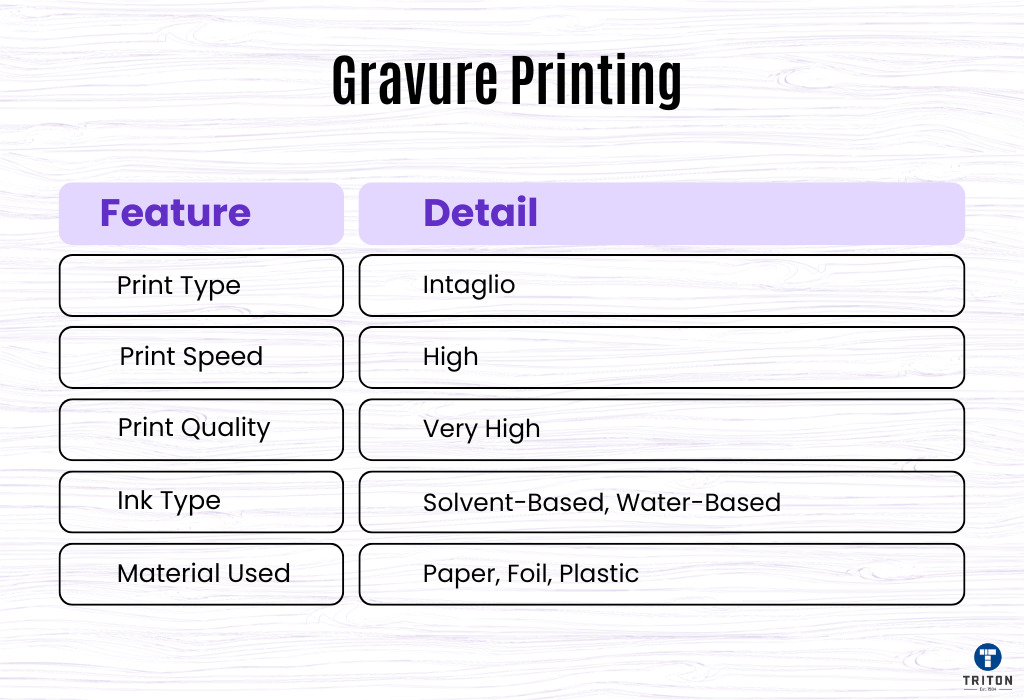
Feature | Details |
---|---|
Print Type
| Intaglio |
Speed | High |
Quality | Very high
|
Ink Type
| Solvent-based, water-based
|
Materials Used
| Paper, foil, plastic, and more
|
Gravure printing, also known as rotogravure, is a type of intaglio printing. It involves engraving an image onto a cylinder, making it highly effective for large-volume and high-quality print runs. This technique is praised for its precision and ability to produce rich, vibrant prints.
How Does Gravure Work?
In gravure printing, an image is etched into the surface of a metal cylinder, forming tiny cells that capture ink. The cylinder is immersed in ink, and a doctor’s blade wipes away the excess, ensuring ink remains only in the etched cells. As the substrate moves between the cylinder and a pressure roller, ink from the cells transfers to the substrate, producing the printed image.
Common Uses in the Industry
Gravure printing is preferred for a wide range of packaging needs, especially for high-volume products like wallpaper, gift wrap, and various types of food packaging. It is also extensively used to produce decorative laminates and high-quality magazines.
Advantages
- Image Quality: Offers exceptional clarity and detail, ideal for intricate graphic designs.
- Speed and Efficiency: Suitable for long runs due to the fast operating speeds and continuous printing capability.
- Durability: Prints are highly durable and resistant to smudging and fading, making them ideal for packaging that faces environmental stressors.
- Ink Consistency: Achieves consistent colour and ink distribution, critical for brand consistency across batches.
Disadvantages
- High Initial Costs: The cost of engraving cylinders is significant, particularly for custom designs.
- Flexibility: Less adaptable to changes once the cylinder is engraved, making it less suitable for short runs or variable data.
- Environmental Concerns: Uses a considerable amount of ink and solvent, which may raise ecological issues if not appropriately managed.
Screen Printing
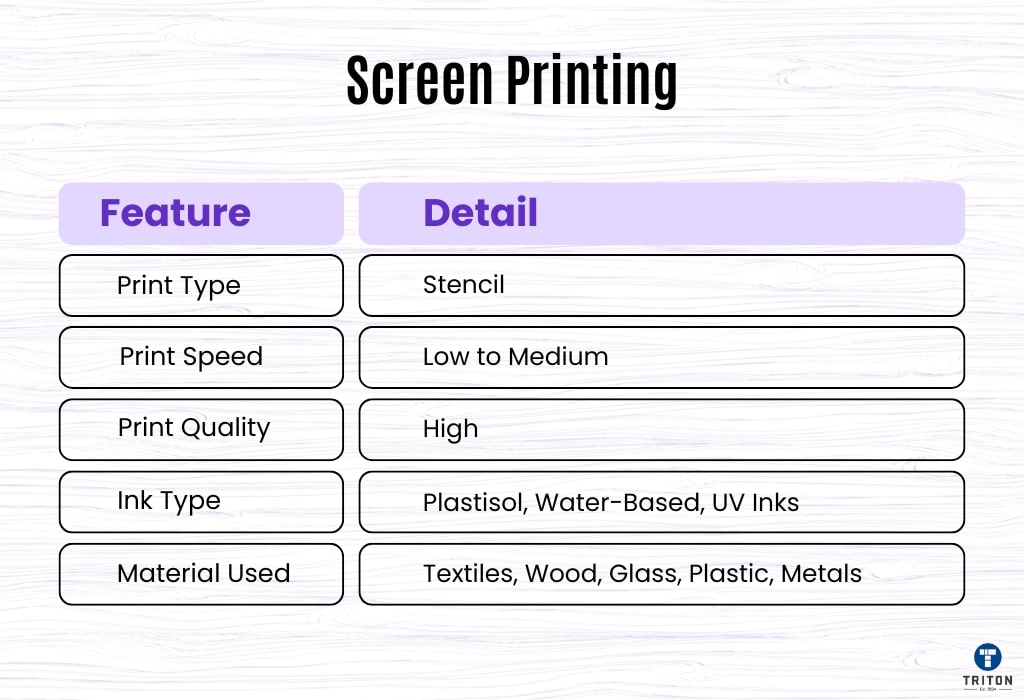
Feature | Details |
---|---|
Print Type
| Stencil |
Speed | Low to Medium
|
Quality | High |
Ink Type
| Plastisol, Water-based, UV
|
Materials Used
| Textiles, wood, glass, plastic, metals
|
Screen printing, also known as silk screening, is a popular method for applying vivid, durable designs to various substrates. It is known for its robustness and adaptability across different materials, making it ideal for artistic and industrial applications.
How Does Screen Printing Work?
The process of screen printing involves creating a stencil (or a screen) and using it to apply layers of ink on the printing surface. Each colour is applied using a different stencil, one at a time, to achieve the final design. The ink is pushed through the stencil mesh onto the substrate below using a squeegee. After each application, the ink is cured or set by heat.
Common Uses in the Industry
Screen printing is extensively used for textiles, decals, product labels, and warehouse signage. It is particularly favoured for bold graphic designs on T-shirts, balloons, and retail packaging.
Advantages
- Colour Vibrancy: Delivers rich, vibrant colours that are more opaque, allowing for greater colour contrast and brightness.
- Versatility: Can be used on various materials, including fabric, wood, glass, and plastic.
- Durability: Produces long-lasting prints that are resistant to harsh environmental conditions.
- Cost-Effective for Large Runs: Becomes more economical at higher volumes, with costs decreasing as quantity increases.
Disadvantages
- Setup Time: Requires considerable setup for creating stencils, especially for multi-colour designs.
- Complexity with Details: While excellent for vibrant designs, achieving fine detail with screen printing can be challenging.
- Cleanup and Space: This printing technique requires ample space for equipment and for the drying process. Additionally, cleanup is labour-intensive, largely due to the types of inks involved.
Offset Printing
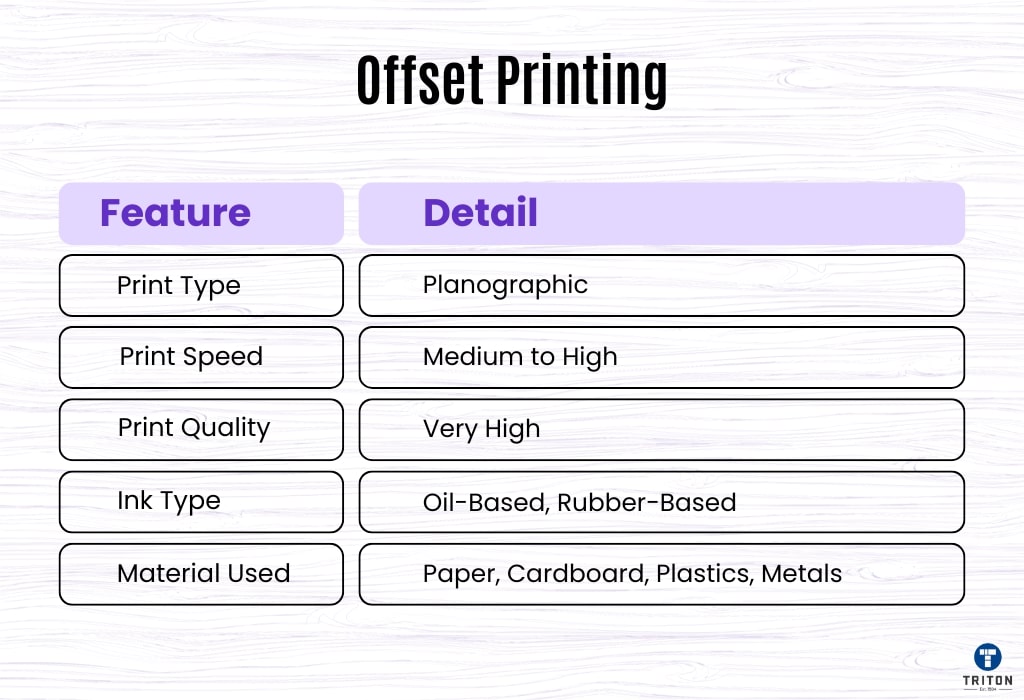
Feature | Details |
---|---|
Print Type
| Planographic |
Speed | Medium to high
|
Quality | Very high
|
Ink Type
| Oil-based, rubber-based
|
Materials Used
| Paper, cardboard, plastics, metals
|
Offset printing is a highly efficient method known for its exceptional image quality and precision. It is particularly favoured for producing large quantities of prints with consistent colour and detail.
How Does Offset Printing Work?
Offset printing operates on the principle of indirect image transfer. Images are first transferred from a plate to a rubber blanket and then to the printing surface. This method uses plates made typically from aluminium, which are chemically treated to attract ink to image areas and repel it from non-image areas.
Common Uses in the Industry
Offset printing is extensively used for printing books, newspapers, stationery, and packaging, such as boxes and cartons. Its precision and quality make it ideal for detailed graphic designs on consumer goods packaging, especially where brand image consistency is crucial.
Advantages
- Consistency and Quality: Delivers sharp and clean images due to the rubber blanket’s even ink transfer, making it excellent for detailed graphic work.
- Cost-Effectiveness: Highly cost-effective for large print runs as the unit cost decreases with volume.
- Material Versatility: Can print on various substrates, including paper, cardboard, plastic, and metal sheets.
Disadvantages
- Initial Setup Costs: High initial setup costs due to the need for producing plates and setting up the press.
- Turnaround Time: Longer setup times lead to slower turnaround for smaller print runs.
- Waste: Early prints often serve as tests to adjust colour and registration, leading to material waste.
Difference Between Different Label Printing Techniques
The following table compares key aspects of packaging printing methods.
Feature | Flexography | Lithography | Gravure Printing | Screen Printing | Offset Printing |
---|---|---|---|---|---|
Print Type
| Relief printing
| Planographic printing
| Intaglio printing
| Stencil printing
| Planographic printing
|
Material Compatibility
| Flexible packaging, paper, plastics, metals
| Smooth paper, high-quality cardstock
| Paper, foil, plastic, and more
| Textiles, wood, glass, plastic, metals
| Paper, cardboard, plastics, metals
|
Common Uses
| Packaging, labels, wallpaper, plastic bags.
| Artistic prints, boutique packaging, high-end products.
| High-volume production like magazines and laminates.
| Textiles, retail packaging, promotional items.
| Books, newspapers, high-quality packaging.
|
Advantages | High speed, cost efficiency, versatile substrate compatibility.
| High detail and texture quality, suitable for complex designs.
| High-quality detail, durable prints, consistent colour.
| Vibrant colours, durability, and broad material compatibility.
| Consistent quality, cost-effective for large runs, versatile materials.
|
Disadvantages
| High initial setup cost, lower detail capability.
| Higher cost, slower than some modern methods.
| High initial costs, less flexible for short runs.
| Setup time for stencils, less detail in prints.
| High setup costs, and potential for material waste.
|
The Bottom Line
In conclusion, understanding the various types of packaging printing techniques is essential for selecting the right approach to meet specific branding and functional requirements. Each method offers unique benefits and challenges, from the precision of lithography and the versatility of digital printing to the durability of gravure and the vibrancy of screen printing.
Businesses must consider detail complexity, setup time, and operational demands to select the optimal printing technique. Ultimately, the choice of printing technology will significantly influence the final product’s aesthetic and functional quality.
We hope this article was useful.
Thanks for reading!