LPN labels, short for License Plate Number labels, are essential tools used across industries to streamline inventory tracking and management processes. These labels offer a unique identification system for items and assets, significantly improving accuracy and visibility in logistics, manufacturing, and supply chain management.
This article aims to provide a comprehensive understanding of LPN Labels, illuminating their importance, real-world applications, and the substantial benefits they offer to contemporary businesses. Additionally, we will explore the processes involved in creating and printing these labels and discuss best practices to optimise their use in various operational environments.
What are LPN Labels?
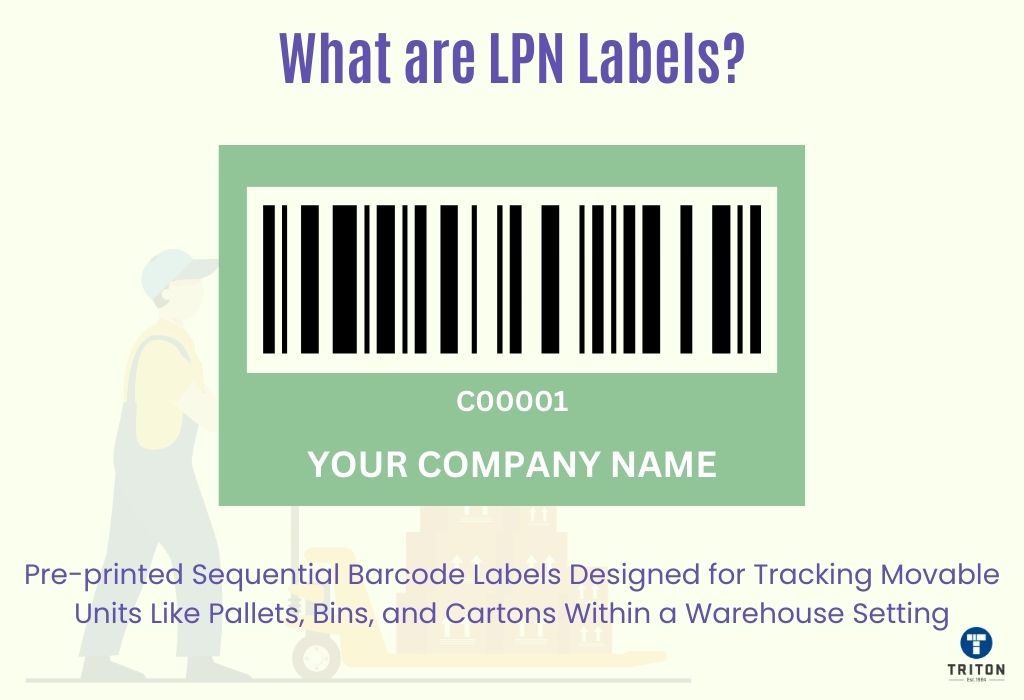
Licence Plate Number labels are pre-printed sequential barcode labels designed for tracking movable units like pallets, bins, and cartons within a warehouse setting. Each label uniquely identifies items, linking them to specific data such as product details and handling instructions. When scanned, they provide immediate information about the item’s contents and logistics.
LPN labels are made from polypropylene or polyester, known for their durability against moisture, abrasion, and temperature changes. They often use strong, permanent acrylic-based adhesives, ensuring they firmly stick to various surfaces, including plastics, metals, and cardboard.
LPN sequential labels are crucial for reducing errors and speeding up operations. They enable real-time tracking and quick inventory status updates. This efficiency is vital in large-scale logistics for maintaining smooth workflows and timely deliveries.
Why are LPN Labels Important?
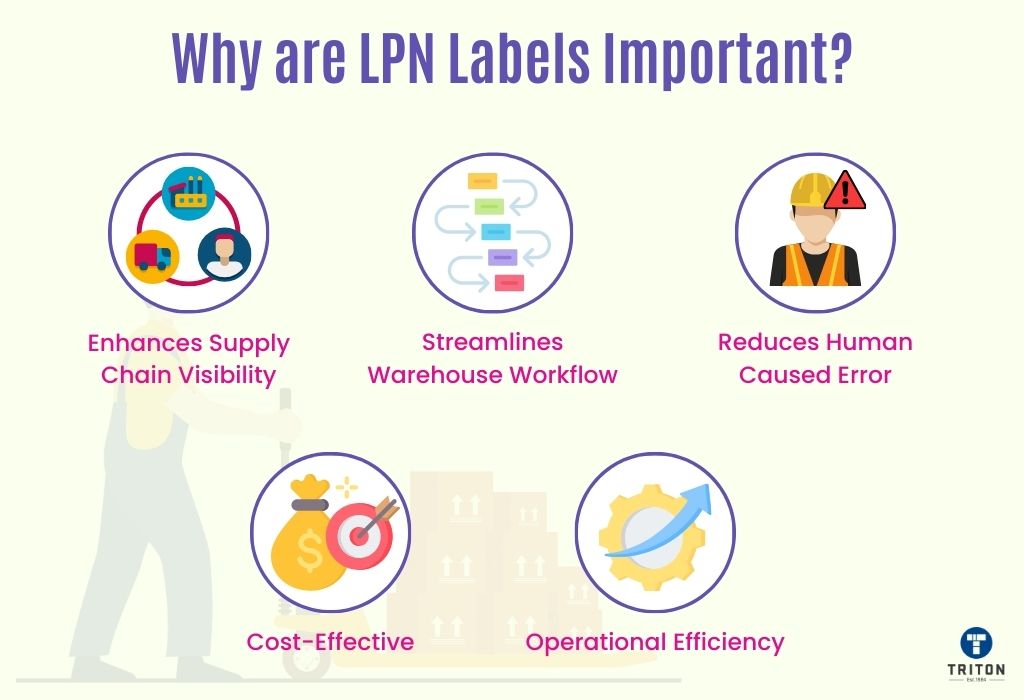
LPN labels play a crucial role in modern logistics and distribution centres. They provide a systematic approach to tracking and organising warehouse items, enhancing operational efficiency and accuracy.
Here are some benefits of LPN labels.
Enhanced Supply Chain Visibility
LPN labels significantly improve the visibility of products throughout the supply chain. By using sequential barcodes, these labels enable precise tracking of items as they move in and out of warehouses, facilitating a clear view of the product journey.
This enhanced visibility not only speeds up operations but also ensures the accuracy of shipments, contributing to the overall efficiency of the supply chain. The ability to track products in real-time allows for more informed decision-making and better management of resources.
To delve deeply into the world of barcodes, visit our dedicated Barcode Learning Centre. This resource is designed to enrich your knowledge, whether you’re just starting out or looking to expand your understanding of barcode technology.
Streamlined Warehouse Workflow
Implementing LPN labels in warehouse operations simplifies the tracking process considerably. With a single scan, warehouse staff can access a wealth of information about an inventory group, including order data, customer information, product contents, part numbers, and more.
This consolidation of data into one accessible point saves considerable time and effort, reducing the need for multiple checks and manual data retrieval. The result is a more streamlined workflow that enhances productivity and reduces the potential for bottlenecks in the supply chain.
Reduction in Human Error
LPN labels play a crucial role in minimising human errors in warehouse operations. By automating the tracking and identification process, these labels significantly reduce the likelihood of mistakes typically occurring during manual data entry or product handling.
This precision in tracking ensures that each item is accurately accounted for, leading to a more reliable and error-free inventory management system. The reduction in errors enhances operational accuracy and contributes to maintaining the integrity and reliability of the entire supply chain.
Cost-Effectiveness
The adoption of LPN labels leads to substantial cost savings for businesses. By streamlining processes and reducing the frequency of errors, these labels minimise the financial losses often associated with manual tracking systems.
Efficient processes mean fewer delays and a reduced need for corrective actions, which in turn translates into lower operational costs. Additionally, the time saved through efficient tracking can be redirected to other productive activities, further enhancing the cost-effectiveness of warehouse operations.
Operational Efficiency in Warehouses
Incorporating LPN labels into warehouse and fulfilment centre operations optimises key processes like receiving, picking, and shipping. These labels enable quick identification and tracking of containers, reducing the time spent on data entry and manual record-keeping.
LPN labels help maintain a smooth workflow by simplifying these processes, minimising potential delays and improving overall operational efficiency. They also play a crucial role in proactive inventory monitoring, allowing for early detection and resolution of any issues.
What Information is Present on LPN labels?
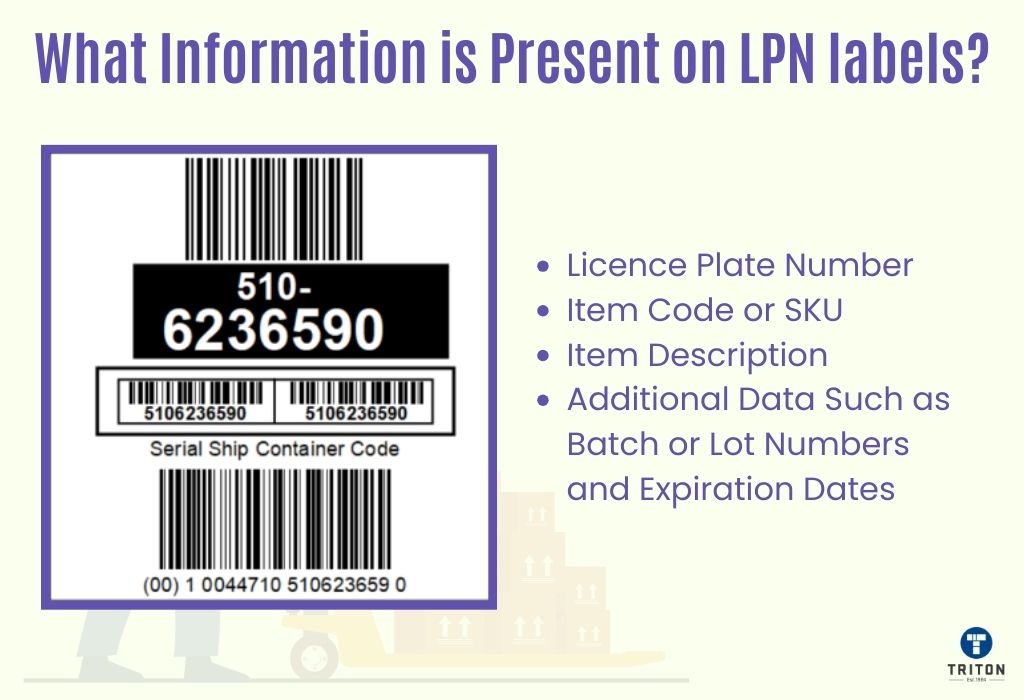
LPN labels, designed for effective inventory management, contain key elements that provide a detailed overview of each item. These components ensure accurate tracking and efficient handling within warehouse environments.
Each LPN label usually has the following information.
Licence Plate Number (LPN)
Each LPN label carries a unique License Plate Number, akin to a digital fingerprint for warehouse items. This number, typically encoded as a barcode, QR code, or RFID tag, is assigned to individual items, cartons, pallets, or containers. It serves as the primary identifier, allowing for seamless item tracking throughout its lifecycle.
For example, a pallet of goods might have an LPN that uniquely identifies it from arrival to dispatch.
For a deeper understanding of barcodes, QR codes, and RFID tags, please consult the following comprehensive guides:
Additionally, to explore how these technologies compare with one another, refer to these insightful comparisons:
Item Code or SKU
Item code or SKU is specific to the item or product on the label. It aids in precise identification and is linked to the LPN, ensuring that each item is accurately tracked and managed.
For an in-depth exploration of SKUs, including their definition, significance, creation methods, and best practices, visit our detailed guide at What is a SKU?
Item Description
Beyond just identification, LPN labels include a brief yet informative description of the item. This description offers additional details for easy recognition.
For example, a label might describe an item as “Red Cotton T-Shirt, Size M,” providing quick, at-a-glance information about the product without needing to access additional records.
Additional Data
Depending on the requirements of the specific inventory management system, LPN labels can also feature other critical information. This might include batch or lot numbers, essential for tracking production runs; expiration dates, crucial for perishable goods; or specific storage locations within the warehouse, aiding in efficient space management.
Where are LPN Labels Used?
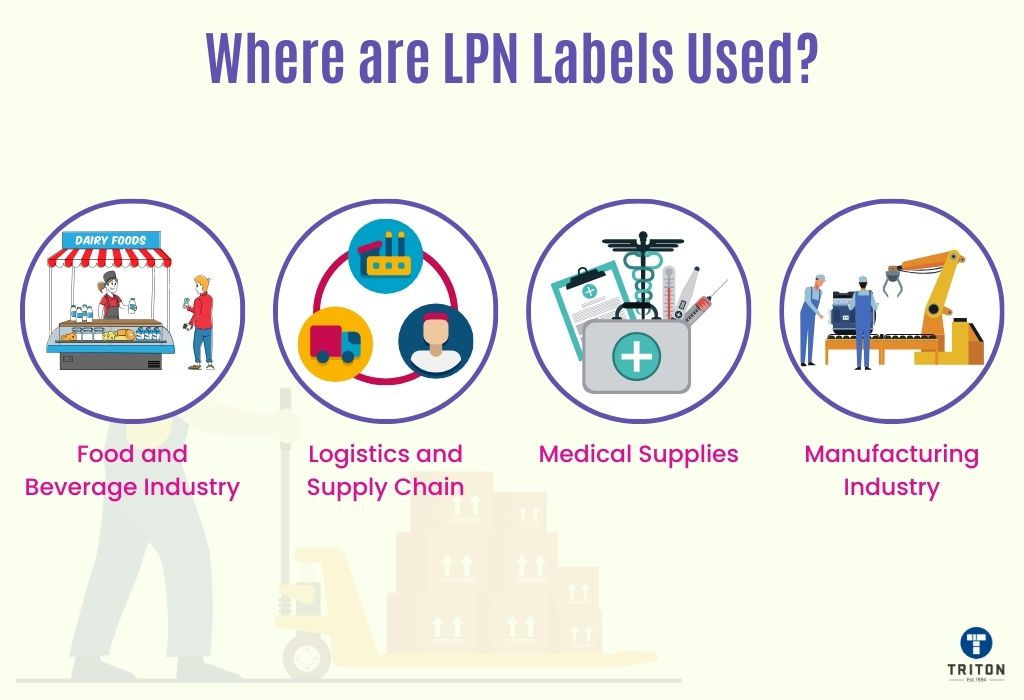
The convenience of accessing crucial data with LPN labels and their durability renders them perfect for various warehouse settings. Their multiple functionality has led to their widespread adoption across multiple sectors, such as:
- Food Industry: This industry relies on LPN labels to monitor product freshness and safety, essential for quality assurance.
- Beverage Sector: The beverage industry shares the same benefits from LPN labels as the food industry.
- Logistics and Supply Chain: LPN labels enhance supply chain management by accurately tracking goods and ensuring efficient inventory control.
- Medical Supplies: LPN labels ensure the traceability of vital healthcare products, supporting patient safety and regulatory compliance.
- Manufacturing Industry: LPN labels optimise the tracking of components and finished products, which is crucial for maintaining production schedules.
LPN labels have become essential tools for maintaining product quality and streamlining inventory management in these fields. In all these sectors, they are vital in tracking goods and managing businesses’ inventories.
How to Create an LPN Label?
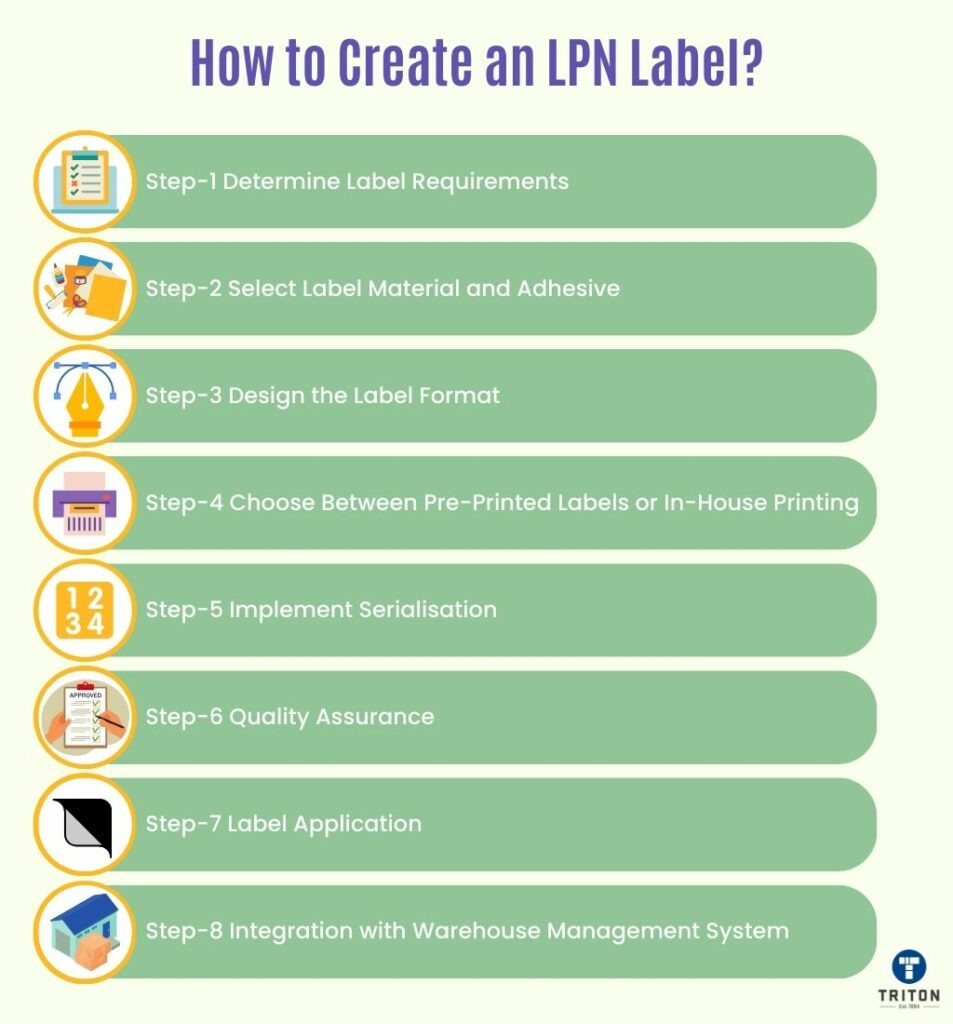
To create your own LPN label, you need to follow some simple steps.
Step-1 Determine Label Requirements
Assess the specific needs of your warehouse or logistics operation. Consider the size of labelled items, environmental conditions (like temperature and humidity), and the type of surfaces the labels will adhere to.
Step-2 Select Material and Adhesive
Choose durable materials like polypropylene or polyester for harsh warehouse environments. Use strong, permanent acrylic-based adhesives to securely attach to various surfaces, including plastics, metals, and cardboard.
Step-3 Design the Label Format
LPN labels typically include the License Plate Number, item code or SKU, a brief item description, and other relevant data like batch numbers, expiration dates, or storage locations.
Ensure the design is clear and easily scannable.
Step-4 Choose Printing Method
Decide between in-house printing and outsourcing.
In-house printing offers flexibility and control but requires investment in printers and supplies.
Outsourcing to a professional label company can ensure high-quality, durable labels with accurate barcodes.
Pre-Printed Labels or In-House Printing? - What to Choose?
Organisations across various sectors might consider managing their label printing needs internally. However, this approach can bring hidden expenses and risks, particularly in environments sensitive to temperature fluctuations. The cumulative costs of printer upkeep, consumables, and the wear and tear of equipment can be substantial.
On the other hand, opting for pre-printed LPN labels, which are adaptable to various conditions, presents a viable alternative. This choice offers greater versatility in selecting label types that more effectively fulfil specific requirements.
By adopting this method, businesses can significantly lower their expenses related to materials and equipment while ensuring they are equipped to handle diverse labelling tasks.
Working with a label supplier opens up additional customisation possibilities, including various colours and sizes and even incorporating company logos for enhanced branding. Pre-printed labels also mitigate the risk of generating confusion due to number duplication, ensuring a smoother operation.
Step-5 Implement Serialisation
Use a database management system to serialise LPN labels correctly, avoiding duplicate barcode labels. This is crucial for maintaining uniqueness in each label, especially in large operations with multiple warehouses.
Step-6 Quality Assurance
Ensure that the barcodes on the LPN labels are scannable and the information is printed clearly. This might involve testing different printers, label materials, and barcode formats to find the most reliable combination.
Our guides, Mistakes to Avoid When Designing Barcodes and Best Practices for Barcode and Label Designing, are essential resources for ensuring the highest quality in barcode design. They provide expert advice and practical tips to help you excel in this field.
Step-7 Label Application
Apply the labels to the designated items, pallets, or containers. Ensure that the labels are placed in a standardised, easily accessible location for scanning.
Step-8 Integration with Warehouse Management System
Integrate the LPN labels with your warehouse management system for real-time tracking and inventory management. This allows for efficient retrieval of information upon scanning the LPN labels in the warehouse.
Make LPN Label Designing and Printing Easy With BarTender Software
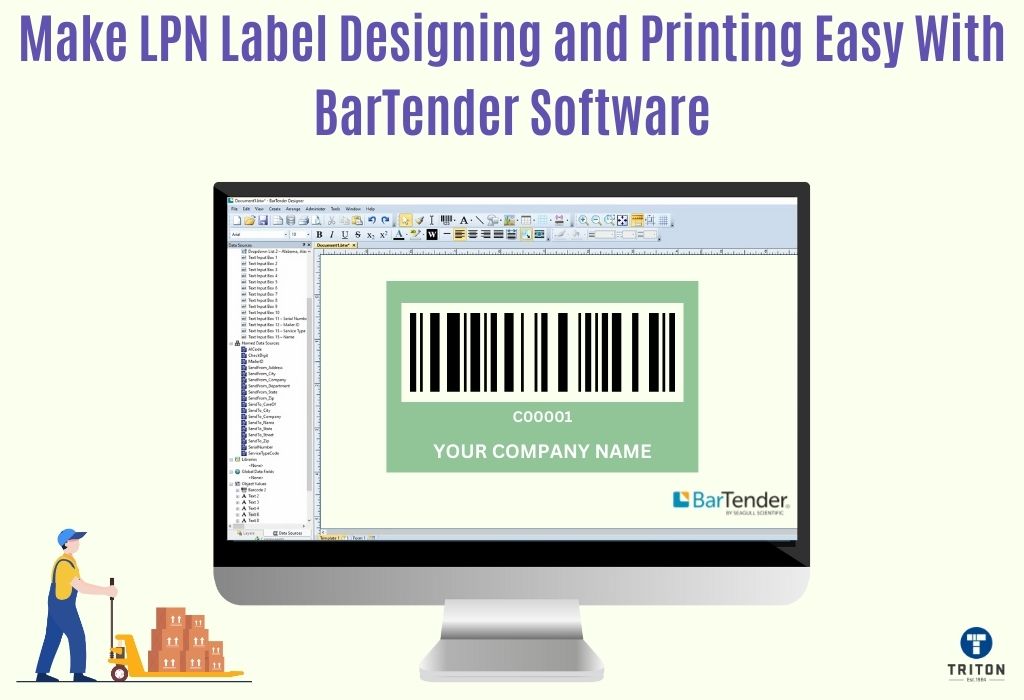
Seagull Scientific’s BarTender software stands as the premier choice for label design and printing worldwide. This solution streamlines the creation, management, automation, and printing of barcodes, labels, and tags, ensuring speed, accuracy, and efficiency.
BarTender’s seamless integration with existing business systems and infrastructure simplifies the label design and printing process. Its ability to connect with multiple data sources simultaneously, including databases, CSV files, and date/time serialisation, makes it a versatile tool for creating diverse barcodes and labels.
The software boasts an extensive library of over 400 preformatted barcode components, compatible with 105 barcode symbologies and adhering to more than a dozen barcode standards. Additionally, BarTender offers ready-to-use, editable templates, including License Plate Number and LPN Container ID, to streamline your workflow further. Learn more about the software’s features by reading our detailed article: What is BarTender Software?
At Triton Store, we offer BarTender software at competitive prices to meet various business needs. Our selection encompasses all four editions of BarTender: Starter Edition, Professional Edition, Automation Edition and Enterprise Edition, each tailored to varying degrees of labelling complexity and automation needs.
For those seeking a cutting-edge solution in label management, BarTender Cloud is the latest offering. This cloud-based platform enables remote management of label printing and design, bringing the power of BarTender to your fingertips, regardless of location.
To understand how BarTender Cloud compares with the on-premise version, refer to our comprehensive guide: BarTender Cloud vs BarTender Software Guide.
Opting for BarTender from Triton Store is more than just acquiring software; it’s a step towards enhancing your labelling and inventory management processes. With its flexibility, robust security features, and extensive support, BarTender elevates your business’s operational efficiency and effectiveness.
Discover how BarTender Software can transform your label printing experience. Connect with us via our live chat widget below, or fill out a form here.
Label Formats of LPN Labels
LPN labels are available in various roll formats, each designed to cater to different operational needs in warehouse and logistics environments. These formats offer flexibility in application and scanning, ensuring efficient inventory management.
Here’s a closer look at each LPN label type.
Printed Rolls
Below is a list of printed roll-type LPN labels.
- Singles: These are standard rolls of sequentially numbered labels. They are tailored to specific size requirements and are ideal for general warehouse labelling needs. Their simplicity makes them suitable for various applications, from small item tracking to larger pallet labelling.
- Single Twins: This format features two identical labels printed next to each other or sequentially on the roll. They are particularly useful for operations handling smaller pallets, crates, or cartons, allowing for consistent labelling of multiple items with the same identification number.
- Single Dual Labels(Corner Labels): Designed for high visibility, these labels have two sets of information on a single label with a die-cut notch. This design allows the label to be easily folded over the corner of a case or pallet, making it visible from two directions. This format is highly effective for quick identification in busy warehouse settings.
- Dual Twins: Ideal for large distribution centres, these labels have two sets of content, with an exact copy side by side on the roll. This design is particularly beneficial for labelling all four sides of large pallets, ensuring that identification information is accessible from any angle.
Sheeted Rolls
Sheeted LPN labels provide an alternative to roll formats, offering unique advantages for certain warehouse and logistics applications. These labels are supplied as pre-cut, individual pieces, making them distinct in their use and storage.
Sheeted LPN labels come in various layouts, such as Single layout, Dual layout, and Twin layout. This variety allows for customisation based on the specific needs of the inventory or packaging.
The size of sheeted LPN labels is typically limited to an 11″ x 17″ sheet. While this size range might seem small, it can accommodate large labels with ample space for additional information such as branding, critical dates, and handling instructions. This makes them suitable for applications like pallet labels where more detailed labelling is necessary.
Sheeted LPN labels offer variable colour options, allowing for customisation and easy visual differentiation. Additionally, blank stock material is available for operations that prefer to print their labels using office printers, providing flexibility and control over the labelling process.
LPN Label Best Practices
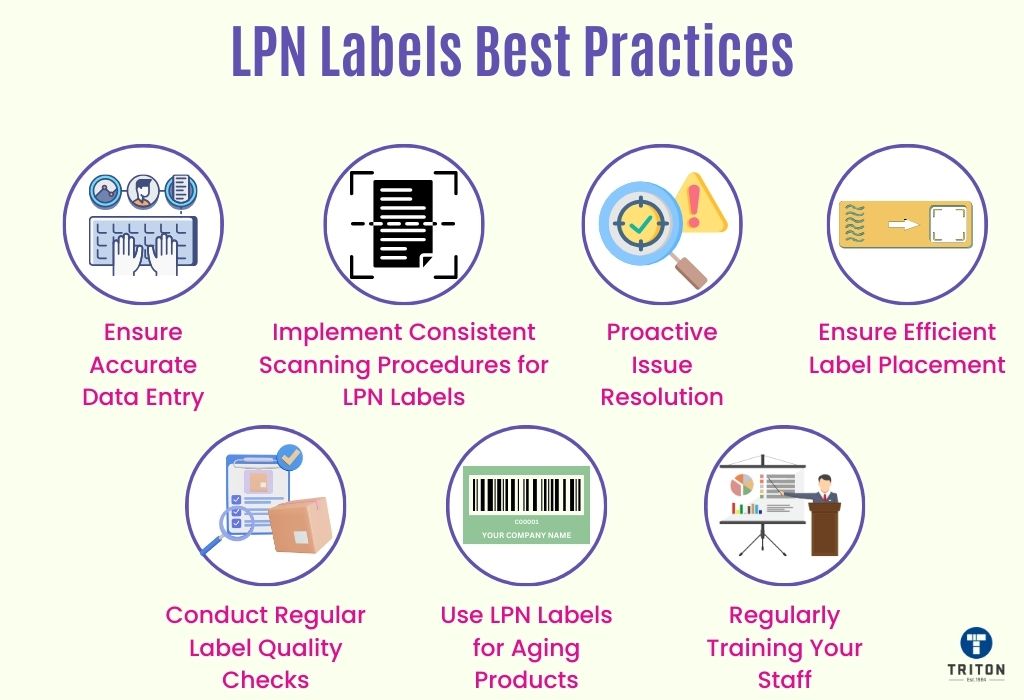
Implementing LPN labels in warehouse and logistics operations requires a strategic approach to maximise efficiency and accuracy. Here are some best practices to ensure optimal use of LPN labels:
Implementing Consistent Scanning Procedures for LPN Labels
Establishing consistent scanning procedures is crucial to maximising the efficiency and accuracy of LPN labels. This practice ensures that every item, pallet, or container in your supply chain is accurately tracked and managed, reducing the likelihood of errors and improving overall workflow.
The steps listed below must be taken to establish these procedures.
- Standardise Scanning Protocols: Develop clear, standardised protocols for scanning LPN labels. This should include specific guidelines on the distance, angle, and sequence of scanning to maintain uniformity across all operations.
- Invest in Quality Barcode Scanners: Utilise high-quality scanning equipment that reliably reads LPN labels under various conditions. Efficient scanners reduce errors and enhance the speed of operations.
- Seamless Data Integration: Ensure that the data from LPN label scans is integrated smoothly with your warehouse or inventory management systems. This facilitates real-time tracking and efficient inventory control.
- Feedback Mechanism: Encourage feedback from employees on the scanning process. Their insights can lead to practical improvements and more streamlined procedures.
To further enhance your LPN label scanning process, Triton offers a comprehensive range of advanced barcode scanning solutions. Our selection includes top-tier products from industry leaders like Honeywell and Zebra, tailored to integrate seamlessly into your logistics workflow.
Our diverse product range caters to various business needs, featuring mobile terminals, general-purpose barcode scanners, rugged barcode scanners, fixed scanners & sensors, USB barcode scanners, wireless barcode scanners, 2D barcode scanners, and Bluetooth barcode scanners.
Beyond barcode scanners, Triton is committed to boosting your operational efficiency with a wide array of barcode scanner accessories and spare parts and cables. These are carefully selected to ensure your equipment consistently performs at its best.
Choosing Triton means opting for unmatched quality and exceptional support. Our expert team is readily available through the live chat widget below, offering personalised assistance and guiding you through our extensive product range.
Accurate Data Entry
Minimise human error in data entry by training staff on the correct methods of labelling and scanning. Accurate data entry is crucial for maintaining the integrity of the tracking system.
To guarantee accurate data entry:
- Implement Error-Tracking Software: Use software that identifies and reports scanning and data entry errors in real-time. This allows staff to correct mistakes immediately, reinforcing proper techniques.
- Regular Data Accuracy Audits: Schedule frequent audits to review the accuracy of the data captured through LPN labels. These audits help identify common errors and areas needing improvement.
- Feedback and Continuous Improvement: Establish a system for regular feedback, where staff can learn from errors and refine their skills. Encourage a culture where feedback is seen as an opportunity for growth.
- Update Procedures Based on Technological Advances: As new scanning technologies and data entry systems are introduced, update operational procedures accordingly. This ensures the data entry process remains efficient and aligned with the best available tools.
- Cross-Training: Cross-train staff in different LPN label handling and data entry aspects. This enhances overall team skills and ensures operational continuity in case of staff absence.
Regular Label Quality Checks
Maintaining the quality of LPN labels is essential for accurate tracking and inventory management. Regular inspections should be part of the operational routine. These inspections involve checking the labels for clarity, scannability, and correct application.
Additionally, updating label material advancements and specifications can further enhance their durability and readability, especially in varying warehouse environments.
Efficient Label Placement
Efficient placement of LPN labels is crucial for streamlining warehouse operations. Standardise label placement across all items, ensuring they are easily visible and accessible for scanning.
This involves determining optimal locations on pallets or containers where labels are least likely to be damaged or obscured. Training staff on these standardised placement guidelines ensures consistency and speed in scanning processes.
Additionally, considering the ergonomic factors in label placement can significantly reduce the time and physical effort required for scanning, thereby increasing overall efficiency. Inventory Grouping
Proactive Issue Resolution
Effective use of LPN labels involves proactive strategies to identify and resolve inventory issues promptly. This approach centres around vigilant monitoring of inventory data, facilitated by regular scanning and analysis. By doing so, potential problems such as stock discrepancies, misplacements, or nearing expiration dates can be identified and addressed before they escalate into larger operational challenges.
Utilisation for Aging Products
LPN labels are highly effective for managing ageing products, especially in industries dealing with perishables or items with expiration dates. Implementing them involves setting up a system where LPN labels are encoded with manufacture and expiration dates. This setup allows for automated tracking of product life cycles.
Utilise warehouse management software that can sort and prioritise items based on these dates, enabling easy identification of products that need to be moved quickly. This practice helps reduce waste and ensures compliance with safety standards, as it facilitates the timely sale or disposal of products nearing their expiration.
Training Staff
Regular training sessions for staff on the correct scanning procedures are essential. This training should cover the basics of scanning and any updates or changes to the protocols. Refresher courses help maintain high levels of accuracy and efficiency in label scanning.
Conclusion
LPN labels represent a pivotal advancement in warehouse and logistics management, offering a blend of accuracy and efficiency. These serialised or sequential labels transcend traditional tracking methods, which is crucial in modern inventory management.
As supply chain demands evolve, the significance of LPN labels grows, making them indispensable in the landscape of efficient warehouse operations. Adopting LPN labels streamlines current processes and sets the stage for future technological integrations, ensuring businesses stay at the forefront of inventory and supply chain management.
Frequently Asked Questions
Can LPN Labels be Customised?
Yes, LPN labels can be customised in size, material, and design to meet specific warehouse needs. They can include various data points like item codes, descriptions, and other relevant information for efficient tracking.
Are LPN Labels Durable?
LPN labels are made from durable materials like polypropylene or polyester, suitable for harsh warehouse environments. They often use strong, permanent adhesives to ensure longevity and readability under various conditions.
How Do LPN Labels Integrate with Warehouse Management Systems?
LPN labels integrate seamlessly with Warehouse Management Systems, enabling efficient tracking, inventory management, and real-time data access, which enhances decision-making and operational workflows.
What Types of Information Can be Included in LPN Labels?
LPN labels can include information like License Plate Numbers, item codes, descriptions, batch numbers, expiration dates, and storage locations, providing comprehensive details for inventory management.
What Equipment is Needed for LPN Labelling?
Implementing LPN labelling requires barcode scanners, RFID readers, label printers, and compatible software for label generation and integration with existing inventory management systems.
How Are LPN Labels Applied in Different Industries?
LPN labels are versatile and used across various industries like food, beverages, logistics, medical supplies, and manufacturing. They aid in tracking, quality control, and ensuring compliance with industry-specific requirements.
Why Does the Warehouse Need to Generate LPN for Returned Products?
Mainly, the purpose of licence plating in the warehouse is to keep track of inventory by grouping and managing all of the items and pallets via Licence Plate Numbers throughout the warehouse process.