Warehouse management, at its core, grapples with the dual challenge of ensuring precise inventory accuracy and maximising operational efficiency against the complexity of modern logistics. Conventional tracking methods often fall short of meeting stringent requirements, often resulting in significant inventory mismanagement and inefficiencies.
RFID technology emerges as a transformative solution, offering the ability to streamline warehouse operations through enhanced accuracy and real-time inventory visibility. This approach addresses the prevailing challenges head-on and sets the stage for a more efficient, reliable, and cost-effective warehouse management system.
This guide delves into the mechanics, benefits, and practical applications of RFID within warehouse environments, offering a comprehensive understanding for those eager to master its implementation.
Understanding RFID Technology
What is RFID?
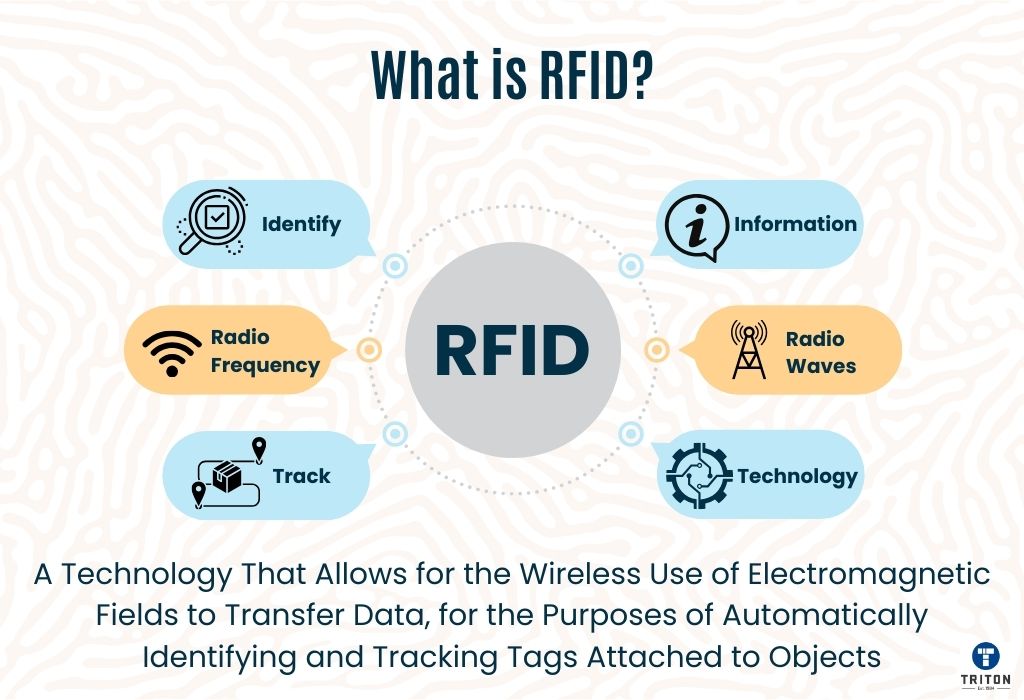
RFID, short for Radio Frequency Identification, is a technology that uses electromagnetic fields to automatically identify, track and manage assets. This technology operates on a defined protocol that enables the storage and retrieval of information remotely via tags, cards, and similar devices.
RFID operates by sending a signal to a microchip, which then sends back information to a receiver, allowing for easy and fast identification of items. This technology allows for the wireless retrieval of data, enabling objects to be tracked and managed without direct contact or line-of-sight scanning.
RFID technology has found applications in a wide array of areas, such as RFID asset tracking, RFID inventory management, access control, supply chain optimisation, personal identification, and security.
Components of an RFID System
An RFID system consists of three critical components:
- RFID tags (also known as transponders)
- RFID readers (also known as interrogators)
- Antennas
RFID Tags
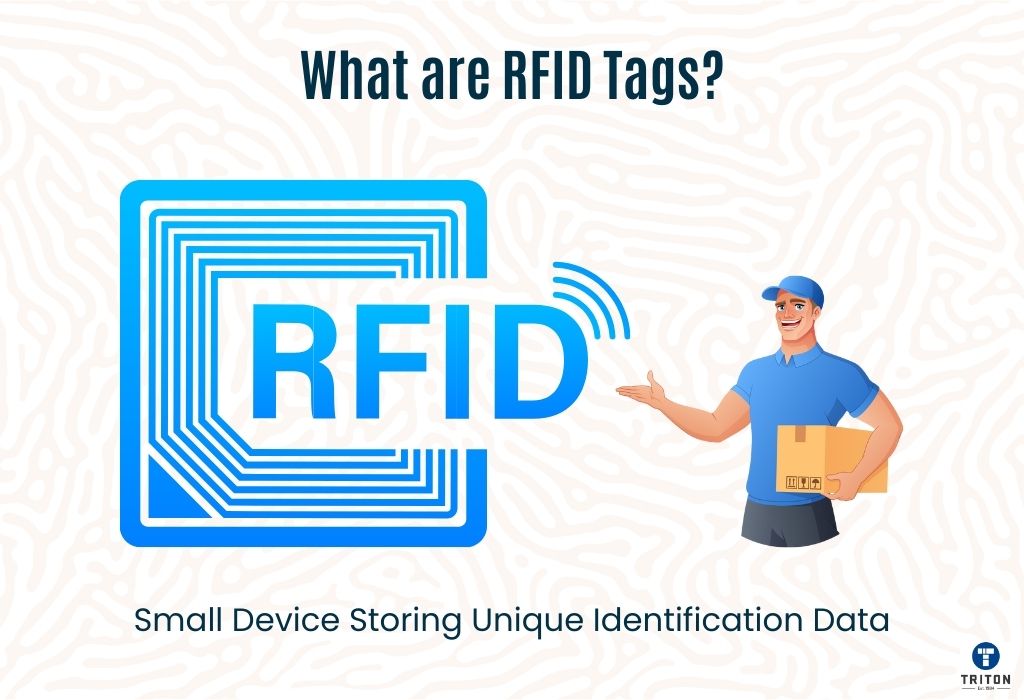
RFID tags are small devices embedded with a microchip and an antenna designed to store data about the item to which they are attached.
RFID tags can be classified into three types based on their power source:
- Passive RFID tags – They have no internal power supply and are activated by the reader’s electromagnetic field.
- Active RFID tags – They contain a battery that allows them to communicate with the reader over greater distances.
- Semi-Passive RFID tags – They use a battery to power the microchip while still requiring an external source to initiate communication.
RFID Readers
RFID readers are devices that communicate with the tag to read or write data. It sends out a radio frequency signal that activates the tag, allowing data to be transmitted back to the reader through the same radio frequency wave. The reader then decodes this information and passes it to a computer system for processing.
RFID readers can be handheld, mobile terminals, wireless, Bluetooth or stationary units, depending on the application needs.
RFID Antennas
Antennas are crucial components of RFID readers and tags that emit and receive radio waves. The antenna’s design, including its shape and size, influences the effective range and directionality of the RFID system.
What is an RFID Warehouse Tracking System?
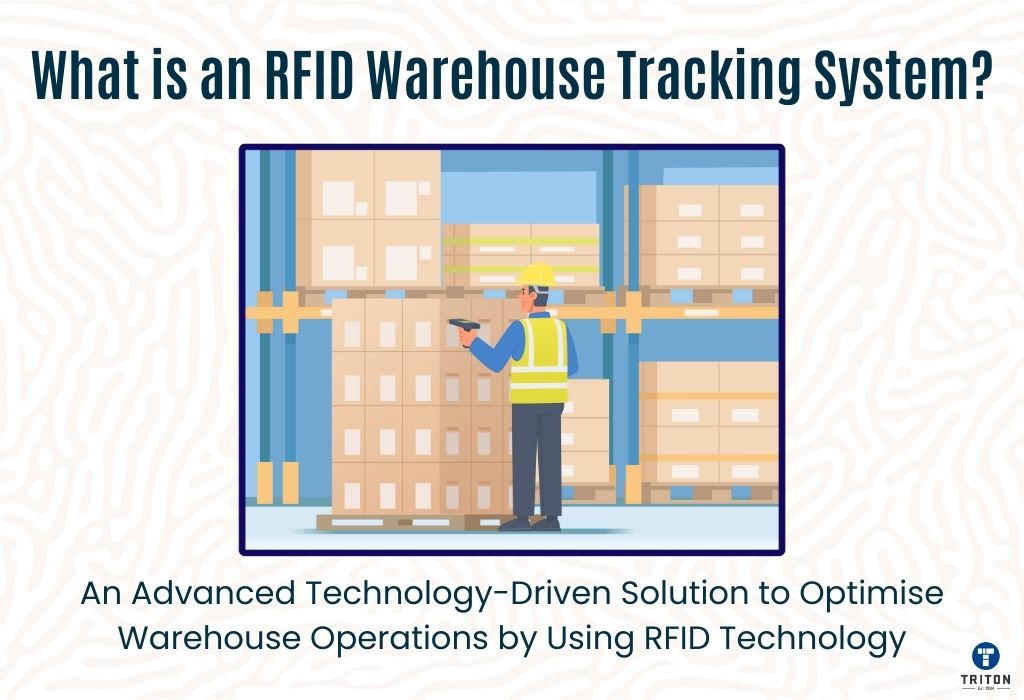
An RFID warehouse tracking system is an advanced technology-driven solution to optimise warehouse operations by using RFID technology to accurately track and manage inventory and assets. This system comprises an integrated network of RFID tags, readers, and antennas that work in concert to automate the identification, location tracking, and management of items throughout a warehouse environment.
At its core, the system uses RFID to provide real-time visibility into the status and whereabouts of goods from the moment they enter the warehouse until they are dispatched. Unlike traditional barcode-based tracking systems, RFID warehouse tracking systems stand out for their ability to read multiple tags simultaneously without needing direct line-of-sight scanning.
How is RFID Used in Warehouse Management?
RFID technology enhances warehouse management by enabling comprehensive tracking and management of assets both inside and outside the warehousing environment. Here are the applications of RFID in warehouse management.
Common Uses for RFID Tagging Outside of Warehousing
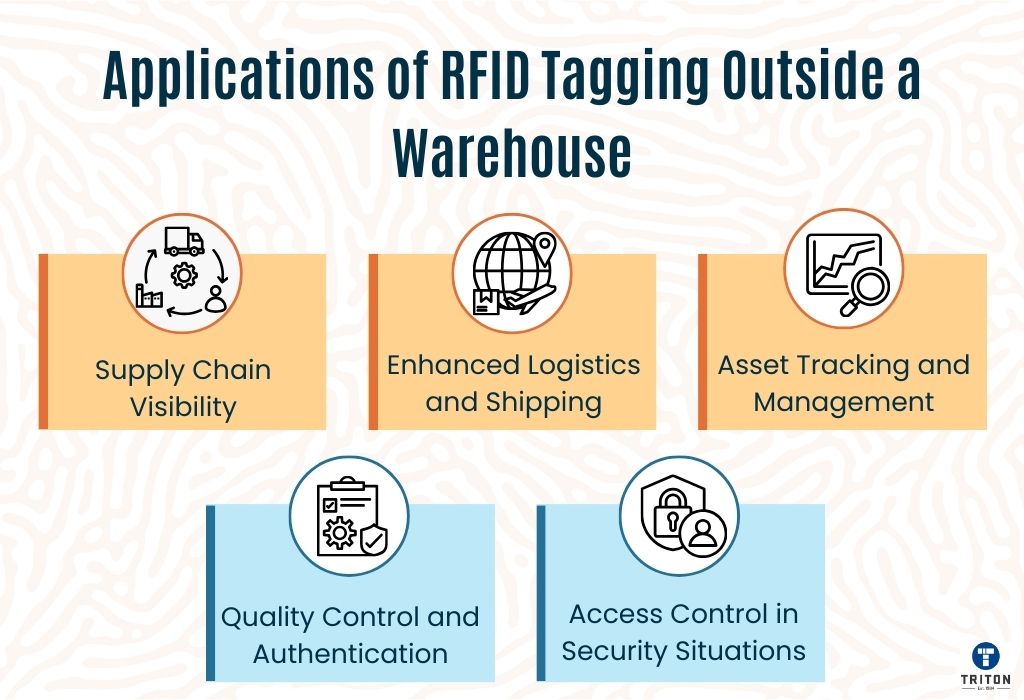
RFID technology significantly enhances operational efficiency, transparency, and security beyond the warehouse. Here’s an in-depth look at its applications.
Supply Chain Visibility
RFID technology revolutionises supply chain management by providing unparalleled visibility at every stage. By embedding RFID tags on products and pallets, businesses can track the journey of goods in real-time from production through to delivery.
This advanced tracking facilitates precise monitoring of product locations and status, enabling proactive supply chain operations management. RFID technology also helps identify bottlenecks, predict potential delays, and ensure that the supply chain operates as a cohesive unit, significantly reducing the risk of lost or misplaced items.
Enhanced Logistics and Shipping
In logistics and shipping, RFID tags streamline operations by automating the identification and tracking of shipments as they move through various checkpoints. This automation is critical for coordinating the loading and unloading of goods, ensuring that the correct items are shipped and received, and, ultimately, reaching the destination on time.
Asset Tracking and Management
Outside the warehouse, RFID technology also plays a crucial role in asset tracking and management, particularly for high-value items that move between locations.
Attaching RFID tags to these assets enables companies to monitor their location in real-time, whether they’re in transit, on loan to another business, or at a client site. This constant visibility helps optimise asset utilisation, schedule maintenance, and even prevent theft.
Quality Control and Authentication
RFID technology is instrumental in maintaining quality control, especially for products that require specific transportation conditions, such as food, pharmaceuticals or perishable goods.
RFID tags with built-in sensors. These sensors can record and transmit data on temperature, humidity, and other environmental factors, ensuring that conditions remain within prescribed limits throughout the journey. This real-time monitoring capability allows for immediate corrective action if conditions deviate, safeguarding the integrity of sensitive products.
Additionally, RFID tags act as security labels and serve as powerful tools against counterfeiting, providing a secure, tamper-proof method for authenticating products.
Access Control in Security Situations
In security-sensitive situations, RFID technology offers a sophisticated solution for access control. RFID tags can be used as secure identifiers for personnel or vehicles, granting access only to authorised individuals or assets in restricted areas.
This system operates by setting up RFID readers at entry points to scan tags and verify credentials automatically. The advantage of RFID in access control is its ability to manage permissions dynamically. It can log entry and exit activities in real-time, enhancing security measures while streamlining access procedures.
RFID in access control is particularly valuable in logistics hubs, manufacturing plants, and other critical infrastructures where controlling access is paramount.
Common Uses for RFID Tagging Inside of Warehousing
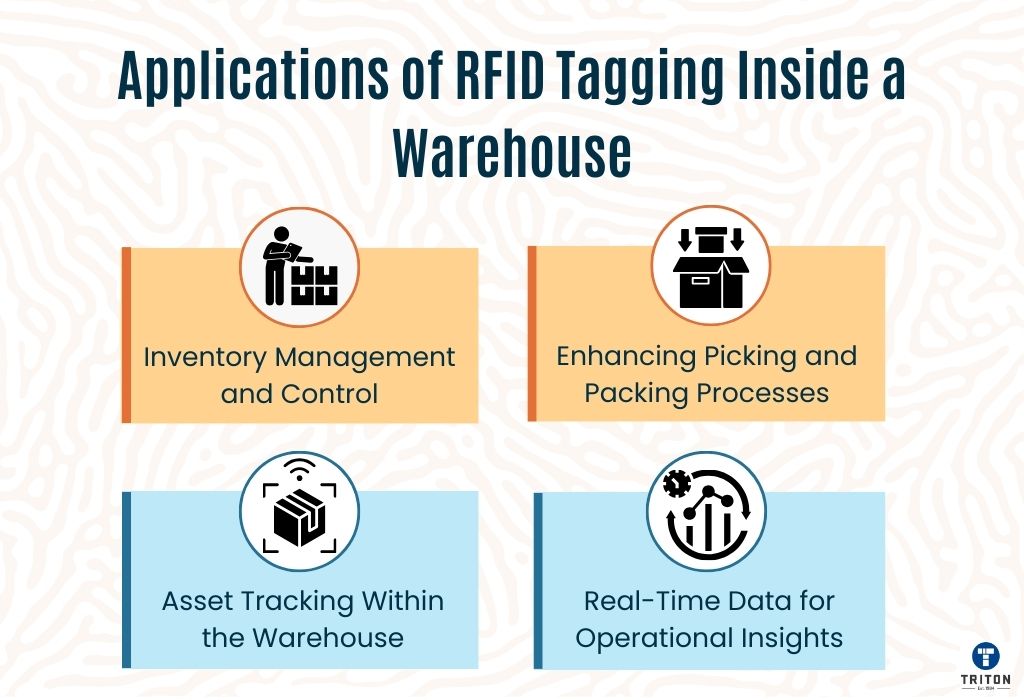
RFID technology revolutionises traditional practices within the warehouse, from inventory management to enhancing operational workflows. Here are key areas where RFID tagging significantly impacts internal warehousing operations.
Inventory Management and Control
RFID systems automate inventory tracking, providing real-time stock level and location data. This technology eliminates manual counting errors and ensures accurate inventory records, facilitating efficient stock management.
RFID’s ability to scan multiple items simultaneously also dramatically speeds up inventory audits and checks, enabling more frequent and accurate inventory updates.
Enhancing Picking and Packing Processes
RFID technology streamlines the picking and packing process by guiding warehouse staff to the exact location of items. It reduces the time spent searching for products, increasing order fulfilment speed and accuracy.
Asset Tracking Within the Warehouse
Beyond tracking products, RFID tags are instrumental in managing warehouse assets such as equipment, tools, and machinery. Monitoring the usage and location of these assets helps optimise their utilisation and schedule timely maintenance, thereby reducing downtime and extending asset lifespan.
Real-Time Data for Operational Insights
The data collected through RFID tagging offers valuable insights into warehouse operations, enabling managers to identify inefficiencies and make informed decisions. Analysing this data can reveal patterns, such as peak operational times or frequent bottlenecks, leading to strategic workflow and resource allocation improvements.
How Do RFID Warehouse Tracking Systems Work?
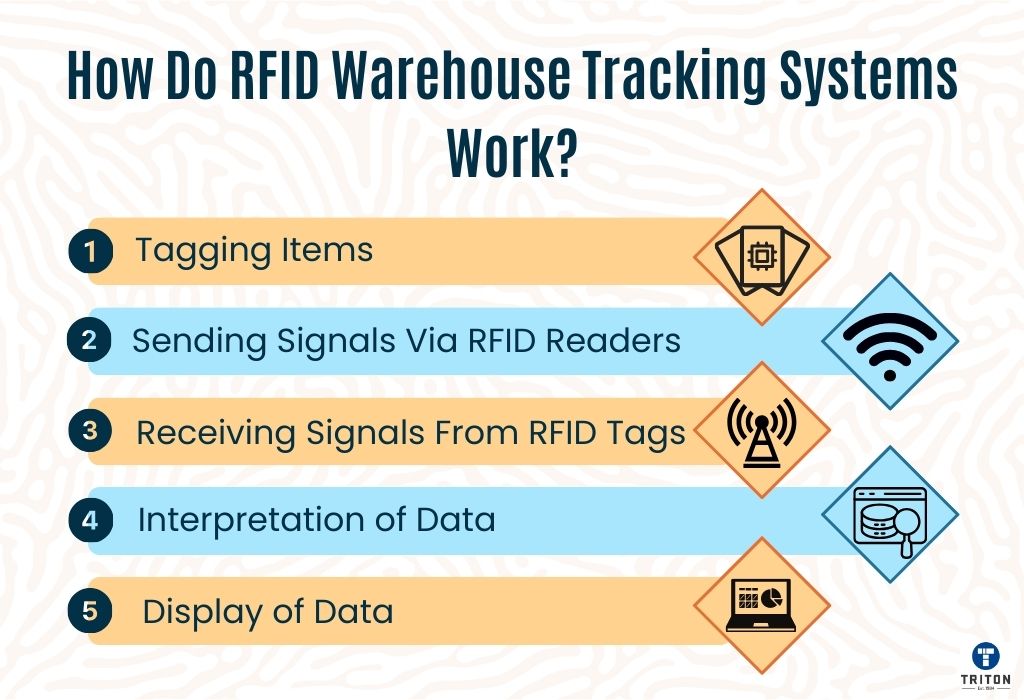
RFID warehouse tracking systems harness the power of Radio Frequency Identification technology to create a highly efficient, automated system for tracking inventory and assets within a warehouse. This sophisticated system operates through a seamless interaction between its core components: RFID tags, readers, and antennas.
Here’s a step-by-step breakdown of how RFID warehouse tracking works.
- Tagging Items: Each item or asset in the warehouse is equipped with an RFID tag. These tags contain a microchip and antenna, storing unique identification data about the item they are attached to. Depending on the requirements, tags can be passive (no internal power source), active (powered by a battery), or semi-passive (battery-powered but activated by reader signals).
- Sending and Receiving Signals: RFID readers are strategically placed throughout the warehouse to communicate with these tags. When an item comes within the reader’s range, the reader emits a radio frequency signal that activates the tag.
- Data Transmission: Once activated, the RFID tag sends back data to the reader via radio waves. This data includes the unique identification information of the tag and potentially additional data stored on it, such as the item’s origin, expiration date, or batch number.
- Processing Information: The reader captures and sends this data to a central database or Warehouse Management System via a connected network. This system processes and interprets the data, updating inventory levels, tracking item locations in real-time, and providing actionable insights into warehouse operations.
- Actionable Insights: With this information, warehouse managers can make informed decisions about inventory management, such as optimising stock levels, streamlining the picking and packing process, or enhancing overall operational efficiency.
- Integration with Other Systems: RFID warehouse tracking systems are often integrated with other operational systems, such as supply chain management, procurement, and sales platforms. This integration ensures that information flows seamlessly between different parts of the business, improving overall efficiency and responsiveness.
How to Implement RFID in Warehouse Management?
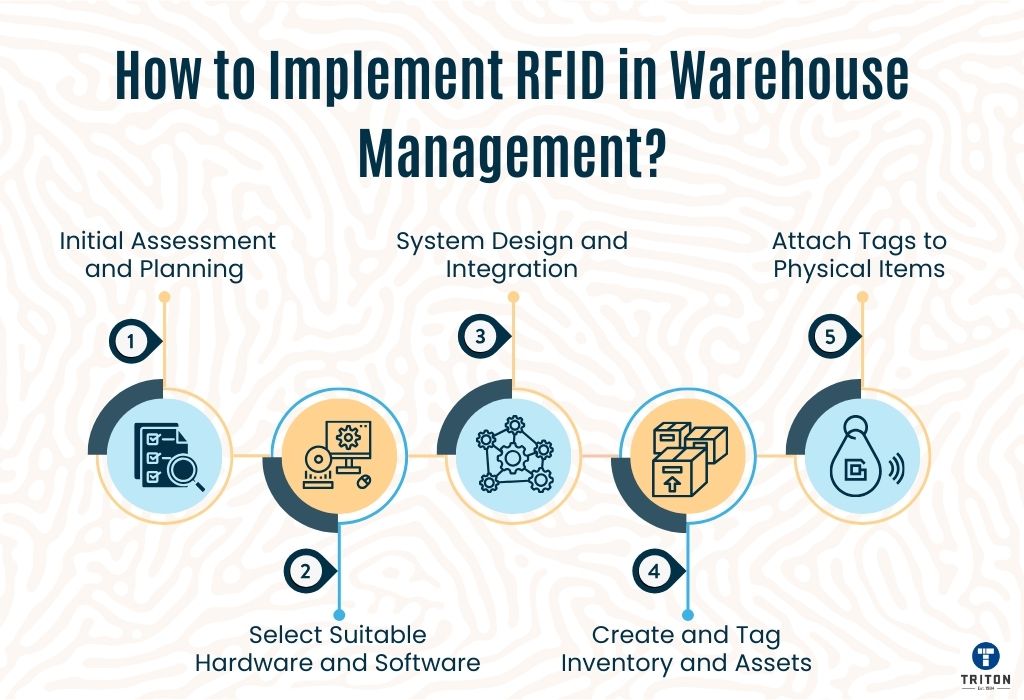
Implementing RFID technology within warehouse operations requires a structured approach to ensure seamless integration and optimal functionality. Below are the steps, divided into equipment requirements and the implementation process.
Equipment Required
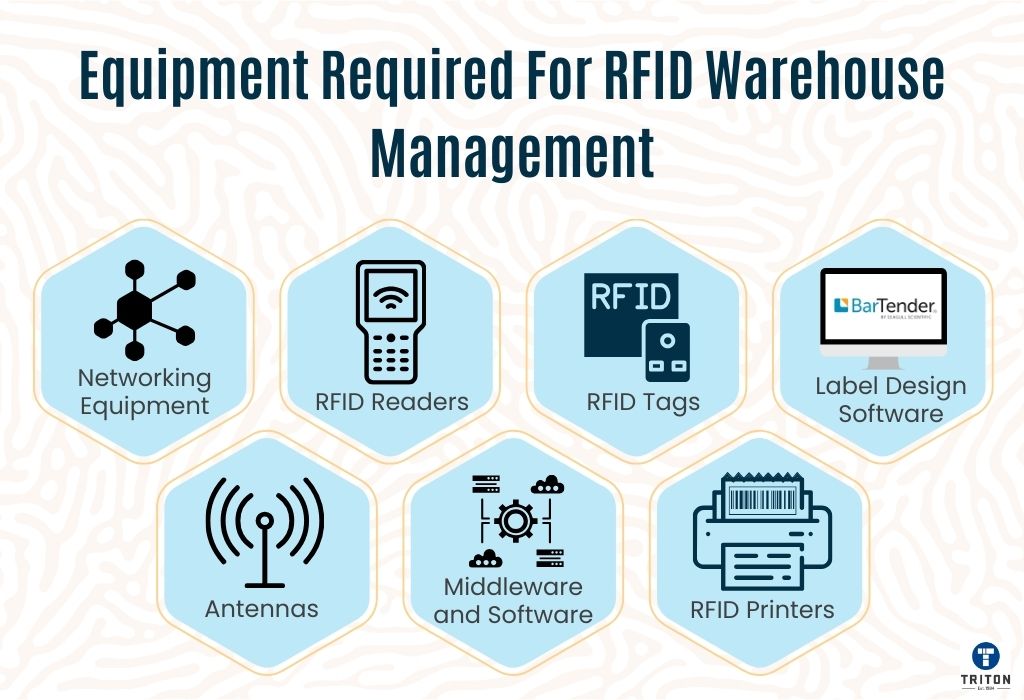
Implementing an RFID system in warehouse management involves several vital pieces of equipment. Each plays a critical role in the functionality of the system. Understanding what these components are and their importance will ensure a smoother implementation process.
RFID Tags
RFID tags are at the heart of any RFID system, serving as the critical link between the physical item and its digital representation in the warehouse management system. These tags store data about the item, such as its ID, status, and history, enabling seamless tracking and management.
RFID Readers
RFID readers are devices that send radio wave signals to tags and receive data back. They are available in various types to suit different operational needs within a warehouse setting. The selection of RFID readers is crucial for the effectiveness of the RFID system, influencing its range, accuracy, and reliability.
Antennas
Antennas are essential for transmitting signals between tags and readers. They can be integrated into the reader or connected externally. The warehouse’s physical layout and the desired read zones will dictate the appropriate type and placement of antennas.
RFID Printers
RFID printers are essential for encoding data onto RFID tags while simultaneously printing human-readable information on the tag’s label.
Top brands like Honeywell, Zebra, and TSC offer a wide range of RFID printers designed to meet the varied demands of warehouse management systems. These printers come in various models, including desktop printers for small-scale operations, industrial printers for heavy-duty use in harsh environments, and mobile printers for the flexibility to print and encode RFID tags directly on the warehouse floor.
Such a broad range ensures that businesses can select the most appropriate printer type to meet their operational needs and enhance efficiency.
Label Design Software
Label design software like BarTender Software allows for customising RFID tag labels, enabling businesses to include logos, barcodes, QR codes and other relevant information alongside the RFID encoding. The software ensures that labels are informative and, compliant with industry standards and tailored to the aesthetic branding requirements of the business.
Middleware and Software
The middleware acts as a bridge between the RFID hardware and the warehouse management software (WMS), filtering raw RFID data into actionable information. This software component is crucial for integrating RFID data into the warehouse’s existing IT infrastructure, allowing for real-time inventory updates, alerts, and analytics.
Networking Equipment
Networking equipment is vital for ensuring that all components of an RFID system are connected and communicate effectively with the central warehouse management system. This includes routers, switches, and hubs that facilitate the seamless data flow across the warehouse operations.
Implementation Process
A successful RFID implementation in warehouse management follows a structured approach. Here’s a step-by-step guide to navigate through the process:
Step 1: Initial Assessment and Planning
Begin by thoroughly assessing your current warehouse operations, inventory management systems, and technological infrastructure. This step involves identifying the specific challenges and inefficiencies that RFID technology can address.
With this insight, define clear, measurable objectives for what the RFID system needs to achieve, such as enhanced inventory accuracy, streamlined order processing, or improved asset management. This phase is crucial for laying the foundation of a tailored RFID solution that aligns with your warehouse’s unique requirements.
Step 2: Technology Selection
Choose the appropriate RFID tags, readers, printers, warehouse software and antennas that best suit your operational needs and environment. This step involves selecting between different types of RFID tags based on the required read range, memory capacity, and resistance to environmental conditions.
Similarly, decide on the RFID readers and antennas to ensure optimal coverage and data capture efficiency across your warehouse. Consideration of compatibility with existing systems and future scalability is paramount during this phase.
Step 3: System Design and Integration
Design the RFID system layout, strategically placing readers and antennas to cover key areas in the warehouse where inventory tracking and management occur. Make sure to integrate your Warehouse Management System (WMS) with readers and antennas.
Step 4: Create and Tag Inventory and Assets
After designing and integrating the RFID system with your Warehouse Management System, the next crucial step is creating and assigning RFID tags to your physical inventory.
This process involves several key actions:
- Designing RFID Tags: Utilise label design software to create RFID tags that serve the technical purpose of tracking and identification, align with your branding, and contain any necessary human-readable information. This step also involves encoding the tags with specific data crucial for inventory management, such as item IDs, descriptions, and other relevant metadata.
- Printing and Encoding Tags: With the design in place, use an RFID printer to produce the tags. The printing process includes encoding the digital data onto the RFID chips embedded within the tags. This dual function ensures that each tag carries the correct information and can be read by RFID readers while being visually identifiable.
- Assigning Tags to Inventory: Once the tags are printed and encoded, the next step is physically attaching them to your inventory items. The attachment method may vary depending on the type of item and the operational environment. Nonetheless, it’s crucial to ensure that tags are securely affixed and positioned for optimal readability.
- Updating the WMS: As tags are assigned to items, update your Warehouse Management System with the new RFID data. This synchronisation ensures that the physical tagging of items corresponds accurately with your digital inventory records, allowing for real-time tracking and management.
Advantages of RFID in a Warehouse
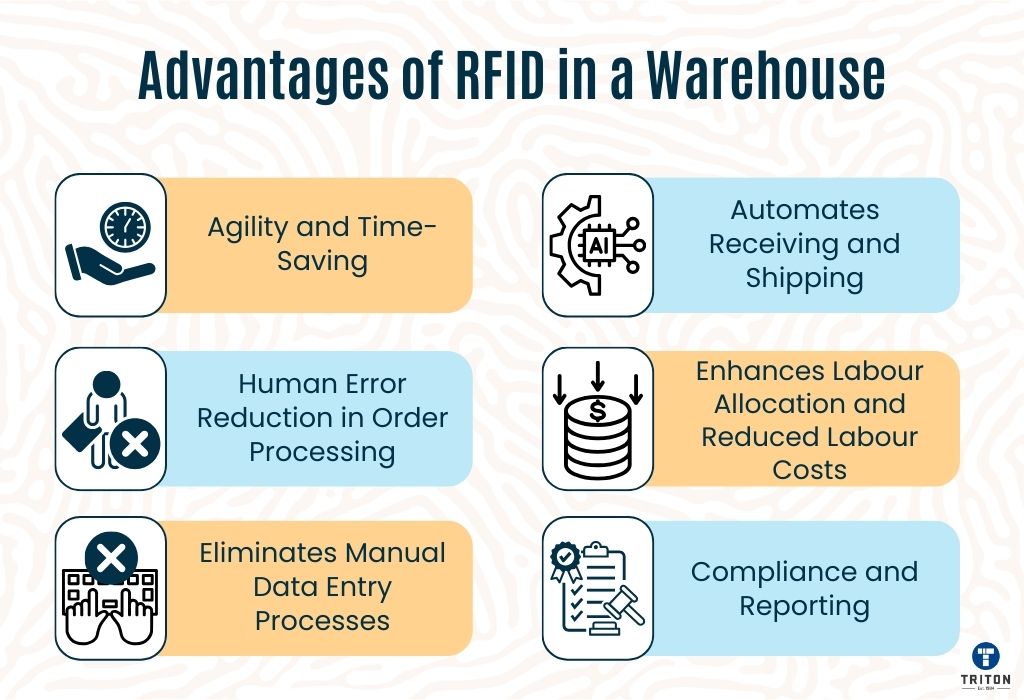
Here are some benefits of using RFID in warehousing.
Agility and Time-Saving
RFID systems impart unprecedented agility to warehouse operations. They furnish up-to-the-minute data regarding the location and condition of inventory, thereby facilitating prompt decision-making and necessary adjustments.
This agility is crucial for responding to market demands, handling urgent orders, and optimising the supply chain. The time saved in locating and processing items directly translates into faster order fulfilment cycles and the ability to handle higher volumes of business without additional strain on resources.
Human Error Reduction in Order Processing
RFID technology significantly reduces human errors in order processing, enhancing accuracy and efficiency. Traditional manual processes are prone to errors, leading to incorrect orders, returns, and dissatisfied customers.
RFID automates this process, ensuring the right products are always selected and shipped. This accuracy improves customer satisfaction and reduces the costs associated with returns and exchanges.
Automated Receiving and Shipping
Another standout advantage of RFID technology is the automation of receiving and shipping processes. Upon arrival and departure, goods equipped with RFID tags can be instantly scanned and registered by the system without manual intervention.
This automation speeds up the process and minimises the waiting time for trucks at docks, enhancing throughput and operational efficiency. It streamlines workflows, allowing for quicker inventory turnover and better use of warehouse space.
Eliminate Manual Data Entry Processes
The introduction of RFID technology eliminates the need for manual data entry, one of the most time-consuming and error-prone aspects of warehouse management.
With RFID, data about inventory movement is captured automatically and synced with the Warehouse Management System in real-time. This elimination of manual entry not only speeds up operations but also ensures that data is up-to-date and accurate, providing a reliable basis for inventory and logistical decisions.
Enhanced Labour Allocation and Reduced Labour Costs
RFID technology optimises the use of human resources in warehouse operations. By automating tasks such as inventory counts, order picking, and item tracking, RFID frees up staff to focus on more complex or customer-focused activities.
This optimisation leads to significant savings in labour costs, as less time is needed for routine tasks, and workforce productivity is maximised. Furthermore, the detailed insights RFID provides into operational workflows help managers deploy their teams more effectively, ensuring that labour is used efficiently across all warehouse areas.
Compliance and Reporting
RFID technology significantly enhances a warehouse’s ability to comply with industry regulations and standards. The technology automates the tracking and documentation of inventory movements. This automated data collection provides a detailed, accurate historical record, essential for regulatory compliance, especially in industries with stringent tracking requirements, such as pharmaceuticals, food and beverage, and electronics.
Furthermore, RFID simplifies reporting processes, offering immediate access to data for inventory audits, compliance reports, and performance analysis. This capability ensures adherence to regulatory standards and provides insights into operational efficiency and inventory accuracy, supporting continuous improvement initiatives.
With RFID, warehouses can maintain high standards of compliance and transparency, fostering trust with partners and regulatory bodies alike.
Potential Challenges and Disadvantages of RFID in a Warehouse
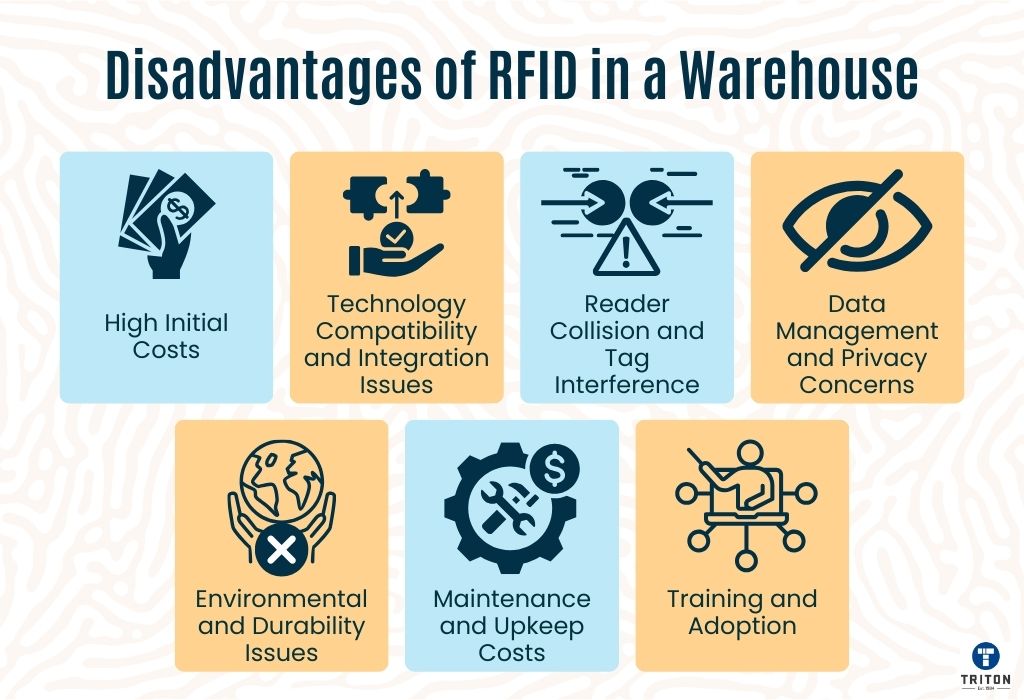
While RFID technology offers significant advantages for warehouse management, it’s essential to consider the potential challenges and disadvantages that may arise during its implementation and operation.
High Initial Costs
One of the primary challenges of implementing RFID technology in a warehouse is the high initial cost. The investment included purchasing RFID tags, readers, RFID printers and sophisticated software solutions required to integrate RFID data with existing warehouse management systems.
These upfront costs can be a significant barrier for many businesses, especially small to medium-sized enterprises.
Technology Compatibility and Integration Issues
Integrating RFID technology with the existing Warehouse Management System can present compatibility challenges. Many warehouses operate on legacy systems that do not readily support RFID technology, necessitating either substantial modifications to existing systems or a complete overhaul.
This process can be both time-consuming and costly, potentially leading to operational disruptions during the transition period. Ensuring that the RFID system seamlessly communicates with current inventory and tracking systems is crucial for maximising the benefits of RFID technology.
Reader Collision and Tag Interference
RFID systems can encounter operational challenges such as reader collision and tag interference.
Reader collision occurs when the signals from multiple RFID readers overlap, causing interference and potentially leading to inaccurate data capture. Tag interference, on the other hand, is often experienced in environments containing materials that obstruct RFID signals, such as metal or liquid, making it difficult for the system to read tags accurately.
These issues necessitate careful planning and system testing to identify and mitigate potential interference problems.
Data Management and Privacy Concerns
Adopting RFID technology in warehouses significantly increases the volume of data generated. Managing this influx of information requires robust data processing and storage solutions, raising concerns over data management and privacy.
Ensuring the security of RFID-generated data, mainly when it involves tracking information that could be considered sensitive, is paramount. Businesses must implement stringent data protection measures to safeguard against unauthorised access and ensure compliance with privacy laws and regulations.
Environmental and Durability Issues
Environmental factors and the need for durable equipment can significantly impact the effectiveness of RFID technology in a warehouse setting. RFID tags and readers must be resilient enough to withstand the demanding conditions often found in warehouses, such as temperature fluctuations, high humidity levels, and exposure to dust, chemicals, and physical impacts.
Choosing RFID components that are not suited to these conditions can lead to system failures, with tags becoming unreadable and readers unable to operate efficiently.
Maintenance and Upkeep Costs
Beyond the initial setup costs, RFID systems incur ongoing maintenance and upkeep expenses. Hardware components such as readers and antennas require repairs and replacements. Software systems need regular updates to remain effective and secure.
These ongoing costs can add up, affecting the overall return on investment for RFID implementation.
Training and Adoption
Implementing RFID technology requires comprehensive training for warehouse staff to ensure they are proficient in using the new system. Resistance to change is a common human factor that can hinder the adoption of new technologies.
Overcoming this challenge involves not only providing adequate training but also addressing any concerns and demonstrating the tangible benefits of the RFID system to encourage buy-in from all levels of the organisation.
Barcodes vs RFID - What to Use in Warehouse Management?
When it comes to optimising warehouse management, the decision between leveraging barcode technology and RFID systems is critical. This choice significantly affects various operations aspects, such as efficiency, cost management, data handling capabilities, and more.
Below, we explore the key factors influencing this choice, guiding the selection of the most appropriate technology based on specific warehousing needs and operational considerations.
Cost Considerations
Initially, barcodes present a more cost-effective option compared to RFID.
The cost of barcode labels and scanners is significantly lower than that of RFID tags and an RFID reader. For smaller operations or businesses prioritising budget constraints, barcodes offer an affordable way to improve inventory and asset tracking.
For detailed insights on deploying barcode technology, consider exploring our comprehensive guides, Mastering Barcode Asset Tracking and Mastering Barcode Inventory Systems. These guides offer step-by-step advice on implementation and optimisation within your operations.
However, it’s crucial to consider long-term operational costs. RFID’s higher initial investment will be offset by its efficiency gains and labour savings over time, making it a viable option for operations looking to scale or automate further.
Operational Efficiency
RFID technology enhances operational efficiency by enabling the simultaneous scanning of multiple items, even without direct line-of-sight. This feature drastically reduces the time needed for inventory counts and asset tracking, providing real-time visibility into warehouse operations.
In contrast, barcode systems require individual scanning of each item, which is more time-consuming and labour-intensive.
For warehouses processing high volumes of goods or requiring frequent inventory audits, RFID may offer significant operational advantages.
Data Capacity and Accessibility
RFID tags can store a wealth of information beyond a simple identification number, including the item’s history, handling instructions, and more. They also allow for real-time updates and data retrieval, enhancing inventory management’s dynamic nature.
Barcodes, while effective for basic tracking needs, offer limited data capacity and lack the ability to be updated once printed.
Warehouses needing detailed item-level information or real-time data access might find RFID more aligned with their operational goals.
Implementation and Integration
Integrating either technology into existing warehouse operations and IT systems requires careful planning.
Barcodes are more accessible to implement due to their simplicity and widespread usage across various industries. RFID, while potentially more complex to integrate, offers greater automation and efficiency gains.
The decision between RFID and barcode should consider the existing technological infrastructure and the ease with which the new system can be adopted without disrupting operations.
Durability and Reliability
RFID tags are more durable and reliable in challenging environments than barcodes, which can suffer from wear, tear, and environmental damage that render them unreadable.
For warehouses operating in harsh conditions or requiring the tracking of items prone to dirt, moisture, or other damaging factors, RFID provides a more robust solution.
Scalability
Both RFID and barcode technologies can scale with your business. However, the scalability offered by RFID is particularly notable for its ability to handle increased volume and complexity without a proportional increase in labour or time.
This makes RFID an attractive option for growing operations looking to maintain or enhance efficiency levels.
Guidance on Selecting the Most Appropriate Technology
Choosing between RFID and barcodes depends on various factors, including budget constraints, operational needs, and future scalability.
For businesses seeking cost-effective solutions for basic tracking needs, barcodes offer a proven, reliable option.
However, operations prioritising efficiency, detailed data management, and scalability will find the initial investment in RFID technology justified by its numerous benefits.
Wrapping Up
Implementing an RFID tracking system in warehouse management marks a significant step towards operational efficiency and accuracy. The transition to RFID brings challenges, such as initial costs and integration hurdles. However, its advantages, like improved order accuracy and automated operations, make it a worthwhile investment.
When weighing RFID against traditional barcode systems, businesses must consider their specific needs and capabilities. As businesses strive to meet the demands of an increasingly fast-paced and data-driven marketplace, RFID stands out as a critical tool in the arsenal of warehouse management technologies.
We hope this article was helpful.
Thanks for reading!