Many businesses struggle to strike a balance between efficiency and accuracy when dealing with the complexities of inventory management. Mismanaged inventory can lead to delayed orders, lost sales, and unsatisfied customers, directly impacting a company’s reputation and profitability.
The solution to this pervasive problem lies in the adoption of barcode inventory systems.
A barcode inventory system is a technology-driven method that uses barcodes to identify and track products throughout the supply chain. This innovative approach streamlines the entire management process, from receiving and storing to distributing products, ensuring accuracy and efficiency at every step.
This guide delves into the intricacies of barcode inventory systems, offering a comprehensive understanding of their functionality, benefits, and implementation strategies. Whether you’re a small business owner or a manager in a large corporation, understanding the dynamics of barcode inventory systems is crucial in optimising inventory management and enhancing overall operational efficiency.
So, without further ado, let’s get started!
What are Barcodes?
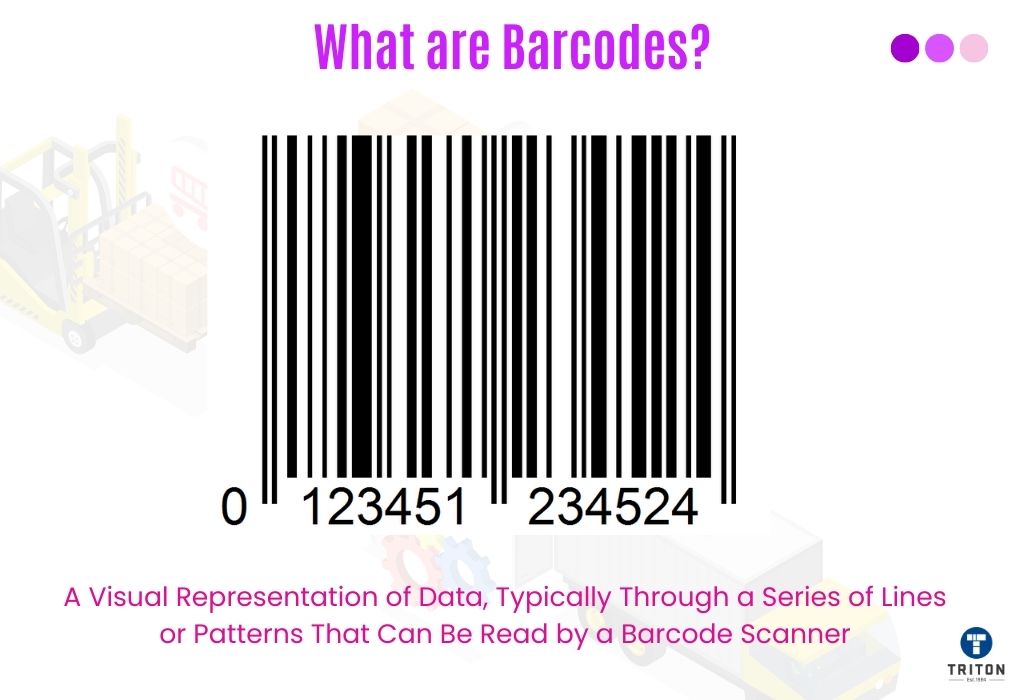
Before delving into the specifics of a barcode inventory system, it’s essential to have a clear understanding of barcodes themselves.
A barcode is a visual representation of data, typically through a series of lines or patterns that can be read by machines. These patterns encode information such as product type, price, and origin, which can be quickly scanned and interpreted by barcode readers.
There are primarily two types of barcodes used in inventory systems: 1D (one-dimensional) and 2D (two-dimensional) barcodes.
1D barcodes, also known as linear barcodes, are the traditional type you often see on retail products. They consist of a series of vertical lines of varying widths and spacings. They can encode information such as product numbers or inventory codes. The Universal Product Code (UPC), a staple in retail, is a classic example of a 1D barcode.
2D barcodes, on the other hand, are more complex and can hold a more significant amount of data. They appear as squares or rectangles containing an array of black-and-white patterns. Unlike 1D barcodes, which can only be read horizontally, 2D barcodes can be scanned both horizontally and vertically. This allows them to contain information like URLs, images, or other significant data. QR codes, known for their storage capacity and versatility, are a popular type of 2D barcode.
Building on the foundation of 1D and 2D barcodes, various barcode symbologies have been developed, each tailored for specific uses and industries. Among the most common are the European Article Number (EAN), GS1 DataBar, Data Matrix, and PDF 417. For a comprehensive list of different barcode types, please refer to our detailed article – Barcode Types.
For an in-depth guide on barcodes, their workings, and more, we highly recommend reading our dedicated guide – What is a Barcode? Before proceeding further in this article, familiarise yourself with barcoding technology, as it is essential for understanding barcode inventory systems and their impact on efficient inventory management and tracking.
What is the Best Barcode for Inventory Management?
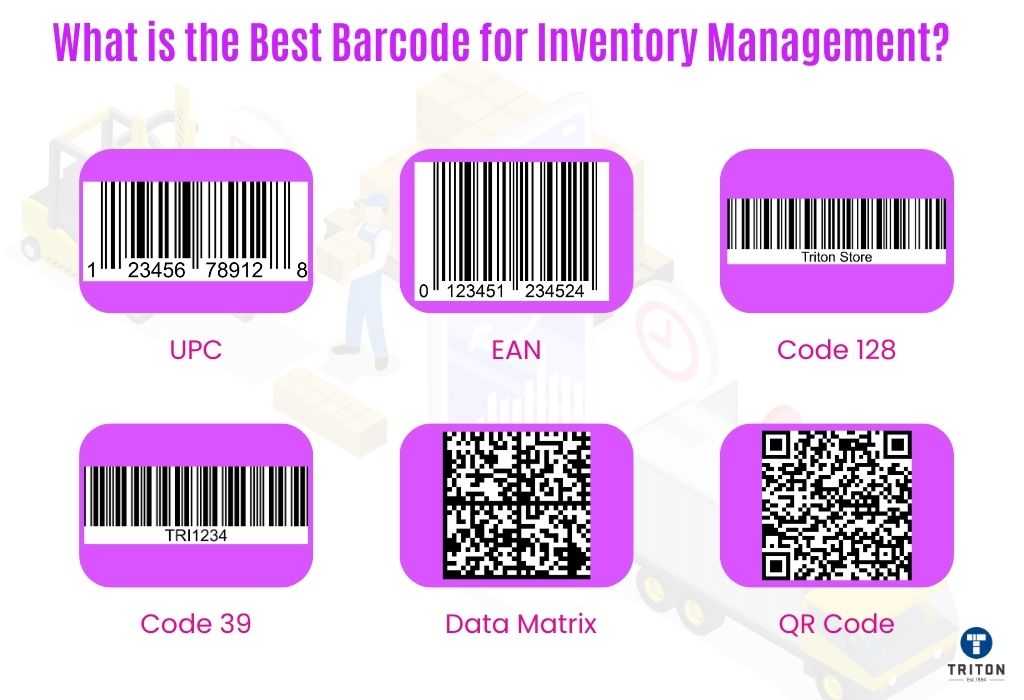
Selecting the appropriate barcode for inventory management is a decision influenced by various factors, including the type of information needed, the volume of items to be tracked, inventory scale, specific requirements and the operational environment.
While there is no one-size-fits-all answer, understanding the strengths and applications of different barcode types can guide you in making an informed decision.
1D Barcodes: Commonly used in general retail and for small to medium-sized inventory systems, 1D barcodes such as UPC and EAN are favoured for their simplicity and efficiency. They excel in tracking standard retail items, capturing basic information like product ID and price. For more specialised needs, Code 39 and Code 128 are alternatives, offering alphanumeric formats ideal for barcoding smaller items.
For a detailed comparison and a better understanding of the differences between Code 39 and Code 128, please refer to our Code 39 Vs Code 128 Comparison Guide.
2D Barcodes: When dealing with complex inventory systems that require detailed product information such as manufacturer details, batch numbers, and expiration dates, 2D barcodes like QR codes and Data Matrix are the preferred options. This makes 2D barcodes especially beneficial in pharmaceuticals, electronics, and food industries, where detailed tracking is paramount.
To compare and learn the differences between a QR Code and a Data Matrix code, refer to our QR Code vs Data Matrix Comparison Guide.
In environments with high-volume inventory or a need for tracking items through complex supply chains, 2D barcodes are advantageous. They store a wealth of information in a minimal space. They can be scanned from any angle, enabling faster processing—a critical factor in dynamic and fast-paced settings.
Ultimately, the best barcode for inventory management is the one that aligns with your specific business needs. For businesses with diverse needs, a combination of 1D and 2D barcodes might be the most effective solution.
What is a Barcode Inventory System?
A barcode inventory system is a comprehensive framework that synergises advanced hardware and software to revolutionise inventory management. At the heart of this system are specialised printers designed for creating barcode labels, the labels themselves, barcode scanners, and robust inventory management software. These components work in unison to form an integrated infrastructure.
This system is driven by sophisticated inventory management software, which seamlessly binds these elements together. It enables the efficient tracking, recording, and analysis of inventory data using barcodes.
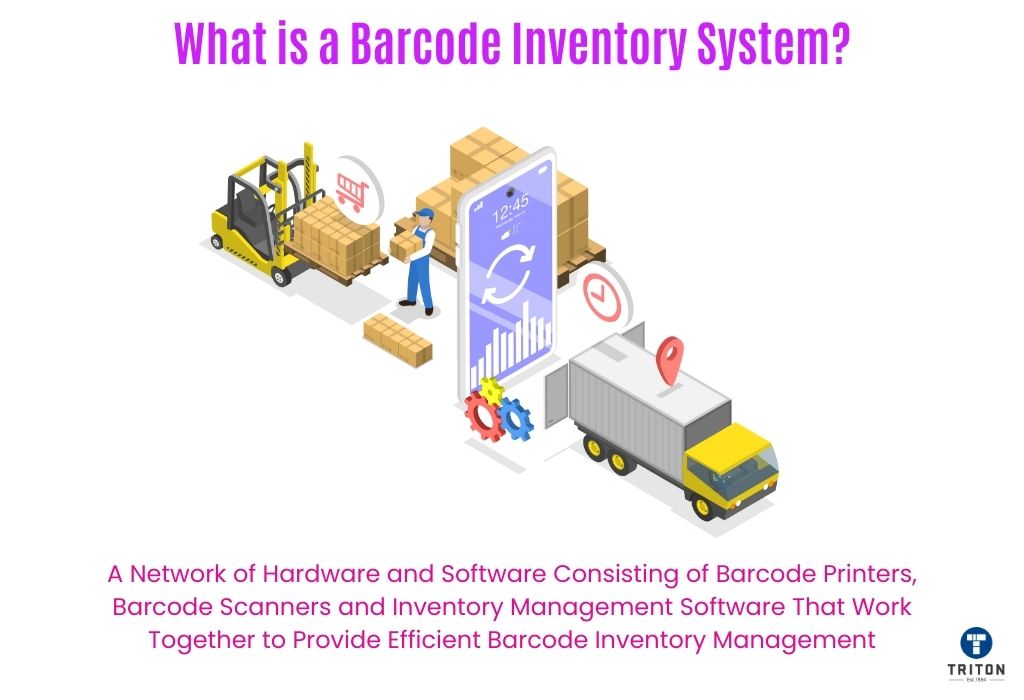
When Do You Need a Barcode Inventory System?
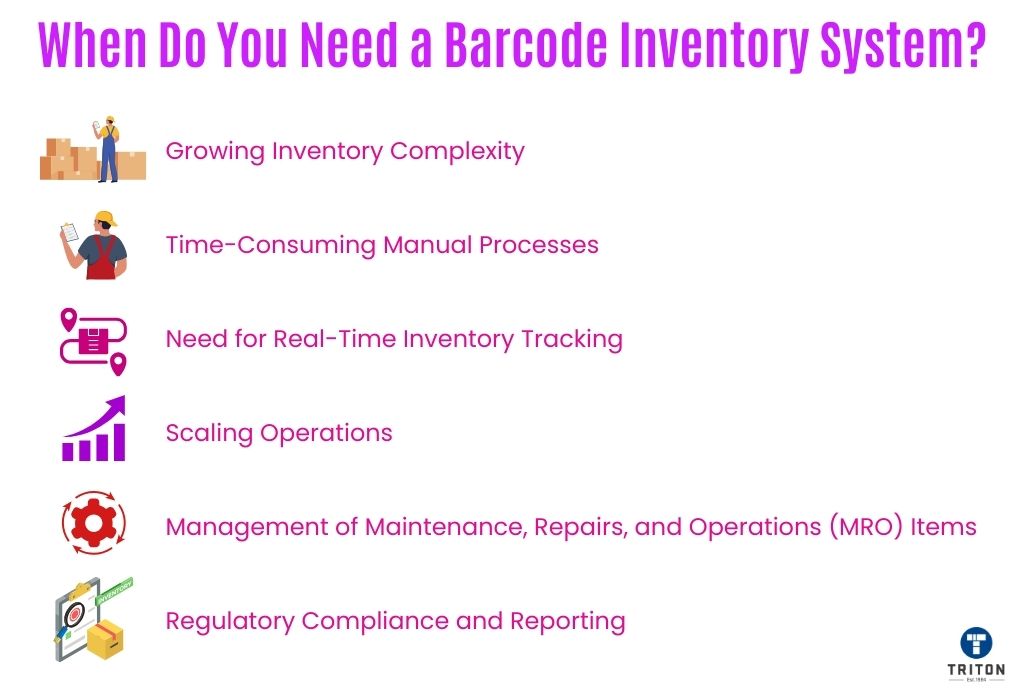
Identifying the right time to implement a barcode inventory system is key for businesses aiming to improve their inventory management. Here are some scenarios where adopting a barcode system is particularly beneficial.
- Growing Inventory Complexity: As your business expands, so does the complexity of managing your inventory. If tracking a wide range of items or managing large volumes is becoming challenging, a barcode system can introduce the necessary efficiency and accuracy.
- Time-Consuming Manual Processes: If your current inventory management involves extensive manual work, leading to high time consumption and error rates, it’s time to consider a barcode system. Automating inventory processes with barcoding can significantly reduce manual data entry and its associated errors.
- Need for Real-Time Inventory Tracking: If your business requires up-to-the-minute inventory information to make informed decisions, a barcode inventory system can provide this level of immediacy.
- Scaling Operations: If your business is expanding, opening new locations, or increasing product lines, a barcode inventory system can integrate these changes smoothly, ensuring consistent inventory management across your entire operation.
- Management of MRO Items: For businesses that keep items for maintenance, repairs, and operations (MRO), managing these items efficiently is crucial. A barcode inventory system can effectively track MRO items, ensuring their availability when needed and reducing downtime in operations.
- Regulatory Compliance and Reporting: Certain industries, such as pharmaceuticals, healthcare, and food and beverage, have stringent regulatory requirements for inventory tracking and reporting. If your business is in such a sector, implementing a barcode inventory system can help in maintaining compliance more effectively.
A barcode inventory system becomes a necessity when your business seeks to optimise inventory management, reduce errors, save time, and adapt to growth and market demands. It’s a strategic investment that can transform your inventory management from a potential liability into a critical asset for business success.
How Does a Barcode Inventory System Work?
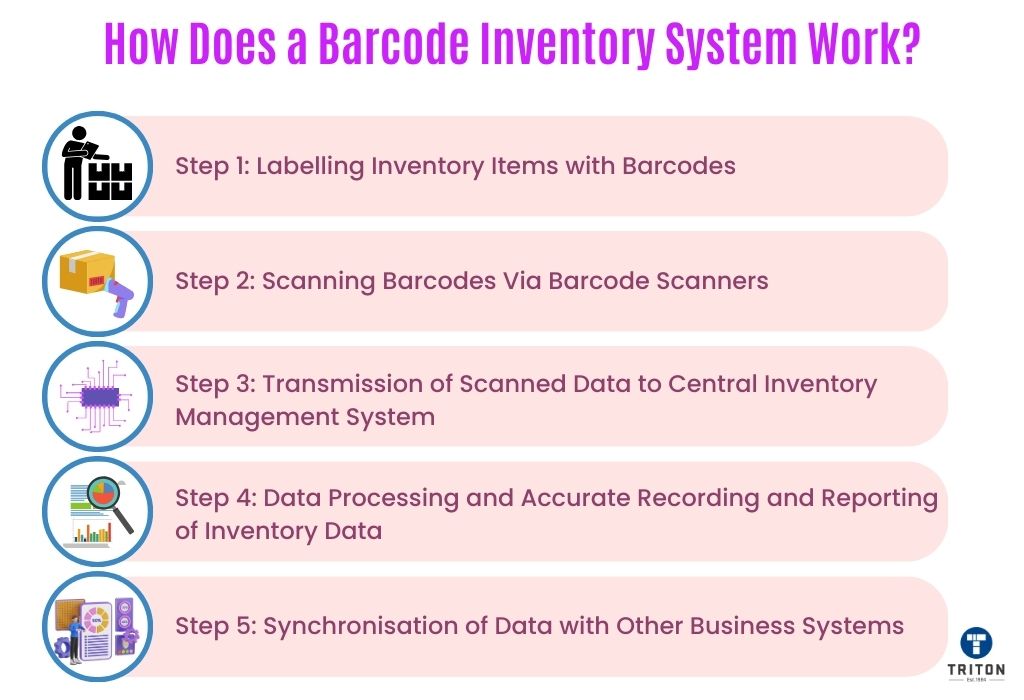
Understanding the mechanics of a barcode inventory system is key to appreciating its efficiency and effectiveness in inventory management. This system operates through a series of coordinated steps involving hardware and software components working together to track and manage inventory.
Step 1: Barcode Labelling
The process begins with barcode labelling. Each item in the inventory is assigned a unique barcode label. These labels contain encoded information about the product, such as its ID, type, or price.
The information encoded can vary depending on the business’s needs and the inventory’s complexity.
To learn about labelling in general, refer to our guide – What is Labelling?
Step 2: Barcode Scanning
Once labelled, items are scanned using a barcode scanner. These scanners use laser or imaging technology to read the barcode and decode the information. The scanner then converts this data into a digital format that can be processed by the inventory system’s software.
If you’re interested in understanding the science behind barcode scanners, our article “How Do Barcode Scanners Work?” will provide valuable insights.
Step 3: Data Processing
Once scanned, the data is transmitted to the central inventory management system. This software is the backbone of the barcode inventory system, where the data is processed and logged. It updates inventory levels, tracks the location of items, and records changes or movements within the inventory.
Step 4: Inventory Management and Reporting
With the data collected and processed, the inventory management software provides a comprehensive view of the inventory. It allows for real-time tracking, automated reordering, and detailed reporting.
Businesses can monitor stock levels, track sales trends, and generate analysis reports, helping make informed decisions.
Step 5: Integration with Other Systems
Often, barcode inventory systems are integrated with other business systems, such as point-of-sale (POS) systems, supply chain management, or enterprise resource planning (ERP) software. This integration ensures a seamless data flow across different business functions, enhancing overall operational efficiency.
What are the Benefits of a Barcode Inventory System?
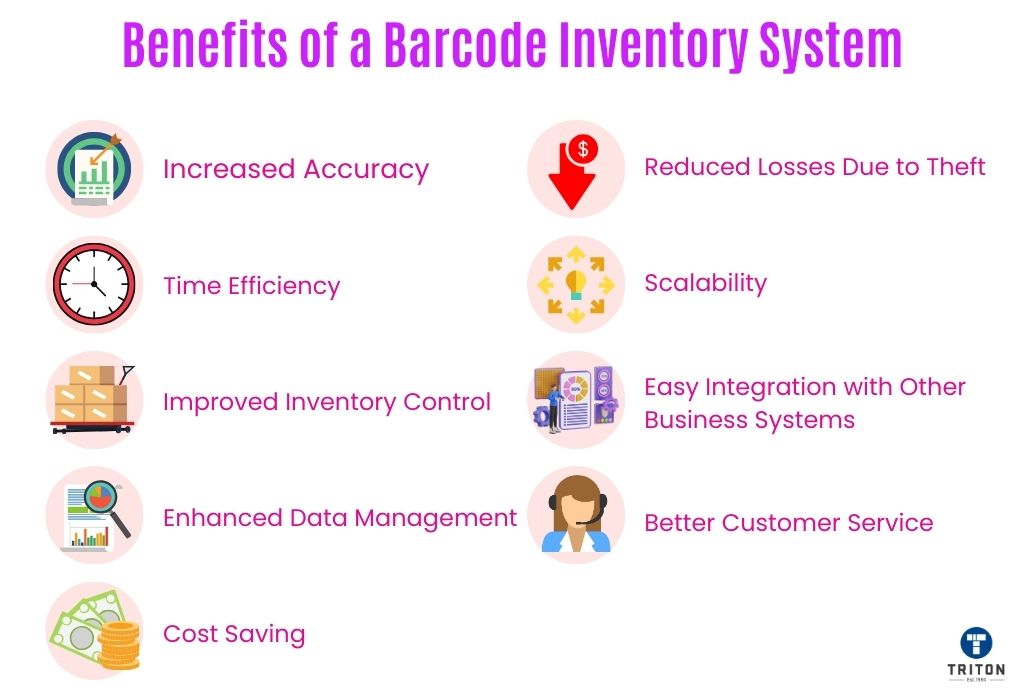
Implementing a barcode inventory system brings a multitude of benefits to businesses, streamlining operations and enhancing overall efficiency.
Here are some of the key advantages of a barcode inventory system.
- Increased Accuracy: One of the most significant benefits of using a barcode inventory system is the drastic reduction in human errors. Manual data entry is prone to mistakes, but scanning barcodes is quick and accurate, ensuring that inventory records are precise.
- Time Efficiency: Barcode systems speed up the inventory management process. Scanning barcodes is much faster than manually entering data, which means inventory can be tracked and updated in real-time, saving valuable time for businesses.
- Improved Inventory Control: With real-time tracking capabilities, businesses have a clearer understanding of their inventory levels. This improved visibility helps maintain optimal stock levels, reducing instances of overstocking or stockouts.
- Enhanced Data Management: Barcode inventory systems enable better data organisation and analysis. Businesses can easily track inventory trends, monitor sales patterns, and make data-driven decisions to optimise their operations.
- Cost Savings: By improving accuracy and efficiency, barcode systems can significantly reduce costs associated with inventory errors and time-consuming processes. These savings can be substantial over time, contributing to the overall profitability of the business.
- Reduced Losses: Barcode systems help minimise losses due to theft or errors. By keeping precise track of inventory, discrepancies can be quickly identified and addressed.
- Scalability: As businesses grow, their inventory management needs become more complex. Barcode systems are scalable, meaning they can easily adapt to increased product ranges and higher volumes of stock.
- Easy Integration with Other Systems: Barcode inventory systems can seamlessly integrate with other business systems, such as point-of-sale (POS), enterprise resource planning (ERP), and supply chain management, creating a unified operational framework.
- Better Customer Service: Accurate and efficient inventory management leads to quicker order fulfilment and fewer errors in customer orders, resulting in improved customer satisfaction.
What are the Drawbacks of Using a Barcode Inventory System?
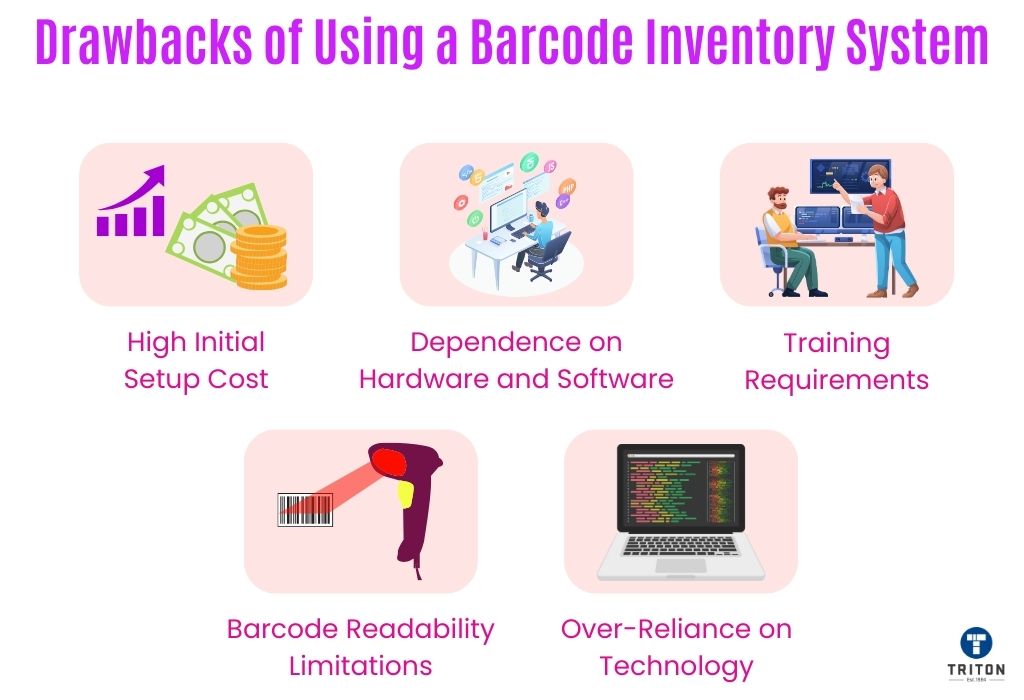
While barcode inventory systems offer numerous benefits, it’s also important to consider their potential drawbacks. Understanding these limitations can help businesses prepare and address them effectively.
- Initial Setup Cost: Implementing a barcode inventory system involves significant upfront costs. This includes the purchase of scanners, printers, and software, as well as potential training expenses for staff.
- Dependence on Hardware and Software: The effectiveness of a barcode system heavily relies on the software and hardware, such as scanners and printers. Malfunctions or technical issues with this equipment can disrupt the inventory process.
- Training and Adaptation: Employees need to be trained to use barcode systems effectively. This learning curve can initially slow down operations and requires time and resources for proper training.
- Barcode Limitations: Barcodes have limitations; they can be damaged, become unreadable, or fail to scan correctly, leading to potential errors or delays in inventory management. Our comprehensive guides, Common Mistakes to Avoid When Designing Barcodes and Best Practices for Designing Perfect Labels and Barcodes, provide valuable insights and tips to help you navigate these limitations effectively
- Over-Reliance on Technology: Heavy reliance on technology can be a double-edged sword. While it offers efficiency, it also creates a dependency, where system failures or outages can significantly impact operations.
How to Implement a Barcode Inventory System?
Implementing a barcode inventory system is a strategic process that involves careful planning and the right set of tools. This section provides an overview of the necessary steps and equipment to successfully set up a barcode inventory system.
Equipment Required
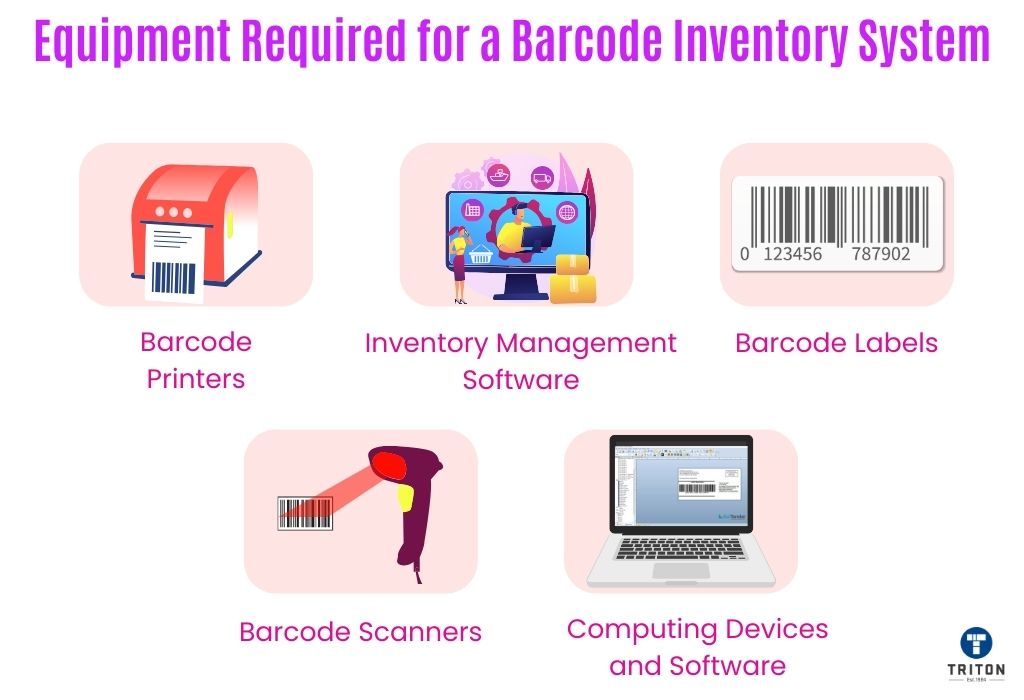
To effectively implement barcode inventory procedures, certain hardware and software are essential.
Barcode Printers
Barcode printers are specifically designed to produce barcode labels that are clear, durable, and adhere to products or packaging.
While various technologies are available for printing barcodes, not all are equally suited for this purpose.
- Thermal Printers: The most commonly used technology in barcode printing is thermal printing, which includes both direct thermal and thermal transfer printers. These printers are ideal for barcode printing because they produce high-quality, durable labels resistant to fading, smudging, and scratching.
- Inkjet Printers: While inkjet printers are common in many office environments, they are less suitable for barcode printing. The main issue is the ink quality, which can lead to smudging and blurring of barcodes. This smudging can affect the barcode’s readability and scan accuracy, especially under handling or exposure to moisture. To compare inkjet printers with thermal printers, refer to our Thermal Printer vs Inkjet Printer Guide.
- Laser Printers: Laser printers, another everyday office staple, also have limitations when it comes to barcode printing. The challenge with laser printers lies in their resolution capabilities. For barcodes that require high precision and detail, especially in smaller sizes, laser printers do not provide the necessary clarity, leading to scanning difficulties. Refer to our Thermal Printer vs Laser Printer Guide to compare laser printers with thermal printers.
In light of the importance of choosing the right printer for barcode applications, the Triton Store emerges as a reliable destination for your thermal printing needs. We offer an extensive selection of thermal printers, including models from renowned brands like Epson, Element, Senor, Honeywell, Zebra, and TSC, as well as colour label printers from OKI.
Our range is diverse, covering industrial printers, desktop printers, direct thermal printers, thermal transfer printers, barcode label printers, mobile printers and receipt printers, catering to various business requirements.
Alongside printers, Triton Store provides a wide array of essential accessories and high-quality thermal print heads from top brands such as Zebra, Honeywell, TSC, Intermec, Datamax, SATO, and Bizerba. These accessories, including spare printer parts and accessories, waterproof printer enclosures, cables and cleaning wipes, are designed to enhance your printing experience and ensure your equipment maintains consistent, high-quality performance.
Whether you’re looking to upgrade your existing setup or start anew, the Triton Store is your go-to source for all things related to thermal barcode printing.
Barcode Scanners
Barcode scanners are devices used to read the barcode labels. They come in various types, including handheld, stationary, and mobile scanners, each suited for different operational environments. To learn more about different barcode scanner types, refer to our article – Types of Barcode Scanners.
In the realm of barcode scanning technology, Triton stands out with its comprehensive range of advanced solutions. We proudly offer a selection of top-tier barcode scanners from industry leaders like Honeywell and Zebra, each designed to integrate seamlessly into diverse logistics workflows.
Our product range is extensive, catering to a variety of business needs with options like mobile terminals, general-purpose barcode scanners, rugged barcode scanners, fixed scanners & sensors, USB barcode scanners, wireless barcode scanners, 2D barcode scanners, and Bluetooth barcode scanners.
But our commitment to enhancing your operational efficiency doesn’t stop at scanners. Triton also provides a wide array of essential barcode scanner accessories and spare parts and cables, ensuring that your equipment consistently delivers optimal performance.
Our expert team is always ready to assist, available through our live chat widget to offer personalised guidance and help you navigate our extensive product range to find the perfect fit for your business needs.
Barcode Labels
Barcode labels are the medium on which barcode data is printed and then attached to inventory items. They vary in size, material, and adhesive quality.
Triton provides a selection of thermal printer consumables essential for creating high-quality barcode labels. We offer products like thermal transfer ribbons, thermal labels, thermal carton labels, thermal carcase tags, food-compliant thermal inserts, receipt rolls and shipping & freight labels. Each product in our lineup is carefully chosen to meet the demands of businesses of all sizes, ensuring reliability and quality in every item.
Inventory Management Software
Inventory management software is the central system that processes and stores all the data collected from the barcode scans. It should be capable of tracking inventory levels, generating reports, and integrating with other business systems if necessary.
Computing Devices and Software
Computers or mobile devices are needed to operate the inventory management software and to manage the data collected from the barcode scanners. Equally important is a label design and print software streamlines label creation, offers customisation options, and enables efficient batch printing.
Seagull Scientific’s BarTender software is a prime example of label design and print software. Its seamless integration with existing business systems simplifies the label design and printing process. BarTender’s ability to connect with various data sources, including databases and CSV files, and its date/time serialisation capabilities make it a versatile tool for producing diverse barcodes and labels.
With over 400 pre-formatted barcode components, BarTender supports 105 barcode symbologies and adheres to numerous standards. It offers a range of pre-formatted label templates that can be used directly. Discover more about BarTender’s features in our article: What is BarTender Software?
At Triton Store, we offer BarTender software tailored to various business needs, featuring all four editions: Starter Edition, Professional Edition, Automation Edition and Enterprise Edition. Each edition is designed to cater to different levels of labelling complexity and automation requirements.
Seagull Scientific has also introduced BarTender Cloud, a cloud-based solution that allows for remote label printing and design management. This innovation brings BarTender’s robust features to your fingertips, accessible from anywhere. Learn about the differences between BarTender Cloud and its on-premise version in our guide: BarTender Cloud vs BarTender Software.
Experience the transformative impact of BarTender Software on your label printing process. For more information or to discuss your specific needs, reach out to us through our live chat widget or by filling out a form here.
Implementation Process
Implementing a barcode inventory system is a structured process that requires careful planning and execution. Here’s a step-by-step guide to implementing a barcode inventory system.
- Assessment and Planning: Begin by assessing your current inventory management system. Identify the specific needs, challenges, and goals of your business. This step involves determining the scale of the system, the types of products to be tracked, and the key objectives you aim to achieve with the inventory barcode system.
- Selecting the Right Equipment: Choose the appropriate hardware and software based on your assessment. This includes selecting suitable barcode scanners, printers, labels, and inventory management software that align with your business requirements.
- System Setup and Integration: Install the inventory software system and integrate it with your existing business systems, such as POS, ERP, or supply chain management systems. Ensure the software is configured correctly to meet your specific inventory tracking needs.
- Labelling Inventory: Generate and print barcode labels for your inventory items. Ensure each item is accurately labelled with its unique barcode. This step is crucial for the system’s accuracy and efficiency.
- Training Staff: Train your employees on how to use the new system, including how to operate the scanners, printers, and software. Effective training ensures all staff members are comfortable and proficient with the system.
- Testing the System: Conduct thorough testing before fully implementing the system to ensure everything works as intended. This phase helps identify and rectify any issues or glitches, ensuring the system is reliable and ready for full-scale operation.
- Going Live: Launch the barcode inventory system once testing is complete, and any issues have been addressed. Start using it for daily inventory management tasks.
- Monitoring and Adjusting: After implementation, continuously monitor the system’s performance. Gather user feedback and make necessary adjustments to optimise the system’s functionality and efficiency.
How Expensive is an Inventory Management System?
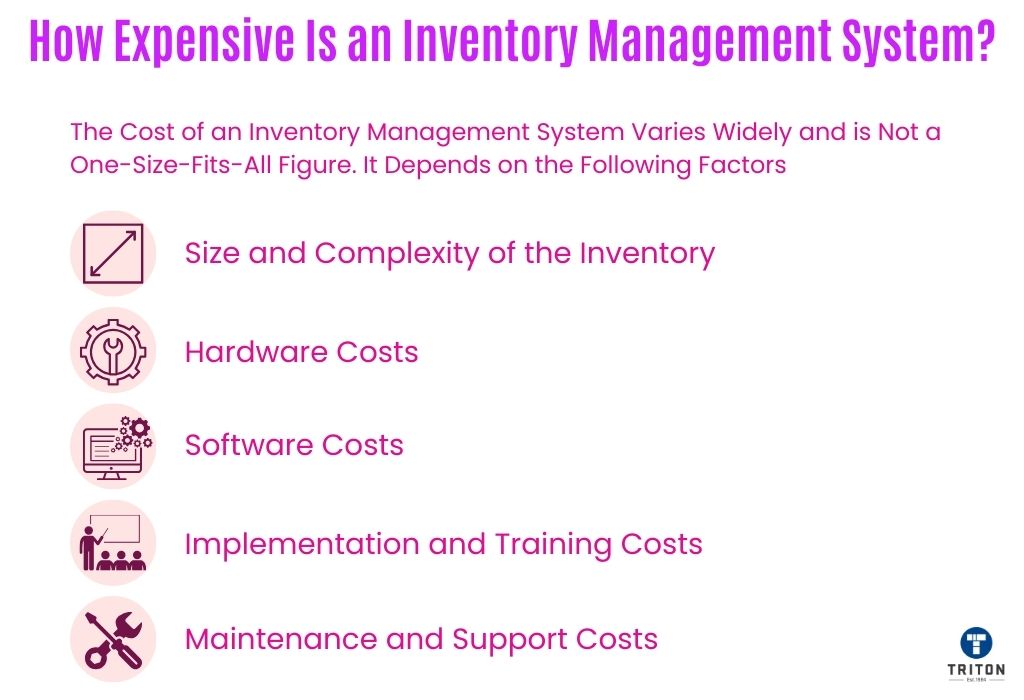
Understanding the cost implications of implementing an inventory management system is crucial for businesses planning to adopt this technology. The expense can vary widely depending on several factors:
- Size and Complexity of the Inventory: The cost is significantly influenced by the size of your operation and the complexity of your inventory. Larger businesses with extensive inventory might require more sophisticated systems, which are more expensive.
- Hardware Costs: This includes the price of barcode scanners, printers, and any other necessary hardware. The cost can vary based on the type and quantity of equipment needed. For instance, rugged scanners for industrial environments are more costly than basic models used in a retail setting.
- Software Costs: The price of inventory management software can range from affordable cloud-based solutions to more expensive, comprehensive systems. The cost often depends on the features, scalability, and level of customisation required.
- Implementation and Training Costs: Implementing the system and training staff are often overlooked costs. These can include the expense of hiring external consultants for implementation and dedicating time to employee training.
- Maintenance and Support Costs: Ongoing maintenance, software updates, and technical support can incur additional costs. Some vendors offer these services as part of a subscription fee, while others may charge separately.
To sum it up, the cost of an inventory management system is not a one-size-fits-all figure.
The cost depends on a variety of factors, including the scale of your business, the complexity of your inventory needs, the type of hardware and software you choose, and the scope of implementation and ongoing support. Carefully evaluating these aspects will help you determine a budget that aligns with your business objectives.
Best Practices for Optimising Barcode Inventory Systems
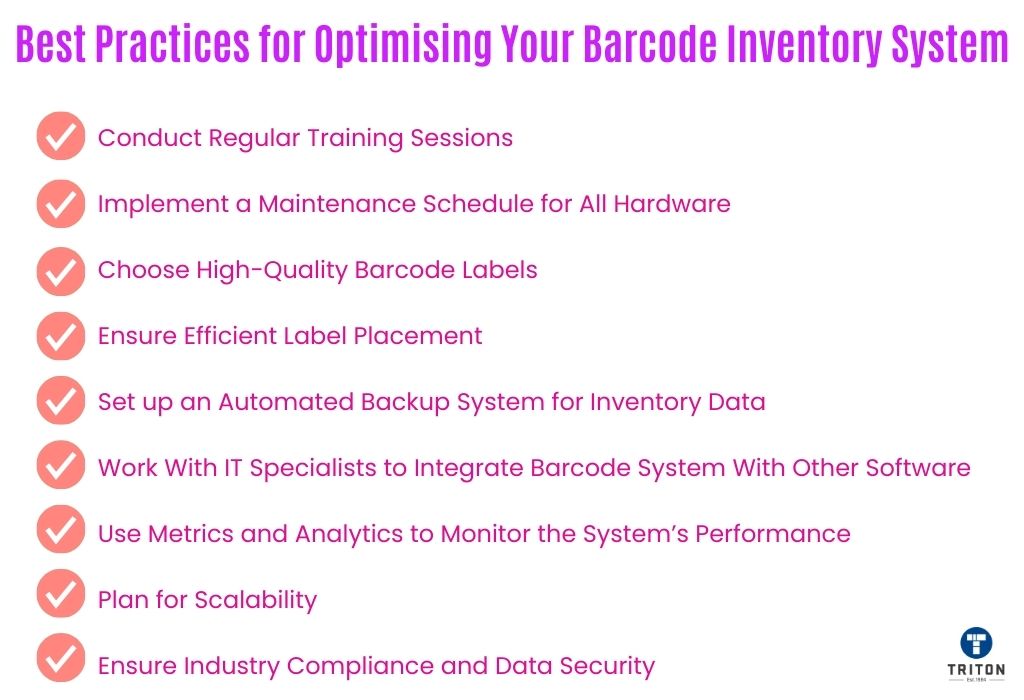
To maximise the efficiency and effectiveness of your barcode inventory system, it’s essential to implement best practices that delve into the specifics of operation and maintenance.
- Regular Training and Updates: Conduct ongoing training sessions focusing on practical, hands-on experience with the system. Update training materials regularly to reflect system upgrades or procedure changes, ensuring staff is always knowledgeable about the latest functionalities.
- Maintain Equipment Properly: Implement a maintenance schedule for all hardware. This includes cleaning barcode scanners and printers regularly, checking for software updates, and promptly addressing any technical issues to prevent disruptions in operations. Our Thermal Printer Maintenance Guide and How to Clean Barcode Scanners Guide will come in handy.
- Quality of Barcode Labels: Choose labels that are resistant to environmental factors like moisture, heat, or abrasion, especially if items are stored in challenging conditions. Test different label materials to find the best fit for your products and storage environments.
- Efficient Label Placement: Place labels on a consistent part of the item, ideally where they can be easily seen and scanned without needing to move the item. For example, avoid placing labels on the bottom of products if they are stacked. Consider the ergonomics of scanning to speed up the process.
- Regular Data Backups: Set up an automated backup system for your inventory data. Schedule regular backups and ensure they are stored securely in cloud storage or on a separate physical server.
- System Integration: Work with IT specialists to integrate your barcode system seamlessly with other software. This might involve customising APIs or using middleware to ensure smooth data flow and accessibility across platforms.
- Continuous Monitoring and Improvement: Use metrics and analytics to monitor the system’s performance. Regularly solicit user feedback and conduct audits to identify areas for improvement or optimisation.
- Scalability Planning: Assess your system’s capacity for handling increased inventory or expansion. Plan for modular upgrades or additional modules that can be added as your business grows, avoiding the need for a complete system overhaul.
- Compliance and Security: Regularly review industry standards and update your system to ensure compliance. Implement robust cybersecurity measures, including encryption and access controls, to protect your inventory data.
Frequently Asked Questions
What Industries Can Use a Barcode Inventory System?
Barcode inventory systems are versatile and can be utilised across various industries.
Retail businesses use them for stock management and sales tracking. In manufacturing, they are essential for tracking parts and finished products.
Healthcare industries employ them for managing medical supplies and patient records. Logistics and warehousing rely on barcode systems for efficient inventory tracking and order fulfilment.
Barcode inventory systems are used in the food and beverage industry for tracking production and expiration dates.
How Secure is a Barcode Inventory System?
Barcode inventory systems are generally secure, but their security level depends on the accompanying software and internal protocols. Most systems use encrypted data transfer and secure databases to protect inventory information.
Can Barcode Inventory Systems Integrate With Other Business Software?
Yes, most barcode inventory systems are designed to integrate seamlessly with other business software, such as ERP (Enterprise Resource Planning), CRM (Customer Relationship Management), and accounting software.
What is the Learning Curve for Implementing a Barcode Inventory System?
The learning curve for implementing a barcode inventory management system varies depending on the system’s complexity and the users’ technical proficiency.
Generally, modern systems are user-friendly with intuitive interfaces. However, adequate training is essential to ensure all users are comfortable with the system.
Final Thoughts
In conclusion, barcode inventory management systems represent a pivotal advancement in inventory management, offering unparalleled efficiency, accuracy, and scalability across various industries.
These systems transform how businesses handle their inventory by reducing manual errors, saving time, enhancing data management, and facilitating informed business decisions. While considering the implementation of such a system, it’s important to weigh the initial costs, understand the potential drawbacks, and adhere to best practices for optimal results.
As technology continues to evolve, barcode inventory systems remain a crucial tool, enabling businesses to stay competitive, responsive, and efficient in today’s dynamic market landscape.
We hope this article was helpful.
Thanks for reading!