Managing a warehouse efficiently hinges on the ability to accurately track and manage inventory. Traditional methods, burdened by manual entries and ageing systems, lead to significant inaccuracies and inefficiencies. These issues escalate costs and severely impact productivity, creating a pressing need for a more reliable solution.
Deploying barcode systems emerges as a key solution, offering a significant leap in efficiency and accuracy. By simplifying inventory management, these systems enable precise tracking and faster operations across all warehouse activities, from receiving to dispatch.
This guide offers an in-depth exploration of integrating barcode technology into your warehouse operations. We’ll discuss the best barcodes for warehouses, outline the essential equipment required, and the step-by-step process for implementing the barcode inventory system. We’ll also share best practices followed by answers to frequently asked questions to clear any doubts you might have.
Before diving deeper, gaining a foundational understanding of barcode systems is crucial. We recommend starting with our What is a Barcode? guide to lay the groundwork for the insights and strategies discussed here.
What Is a Warehouse Barcode System?
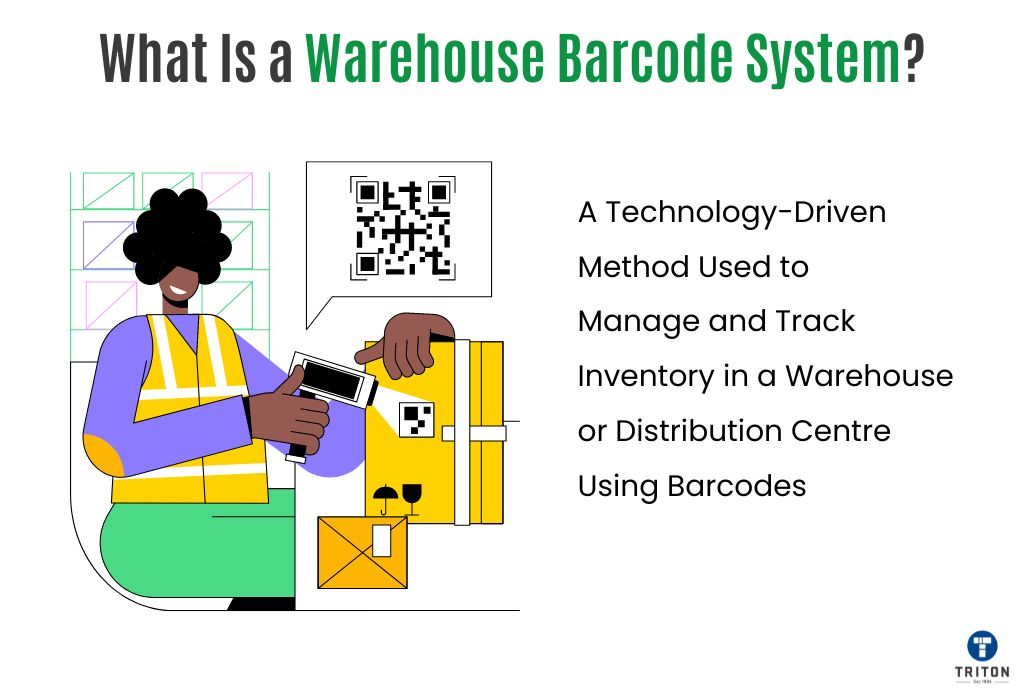
A warehouse barcode system is a technology-driven method used to manage and track inventory in a warehouse or distribution centre using barcodes.
At its core, a warehouse barcode system consists of several key components:
- Barcodes: These are printed labels with unique patterns representing information about the product, such as type, size, and colour, which can be read by scanners.
- Barcode Scanners: Devices used to read the barcode’s information, converting the patterns into digital data that can be processed by the warehouse’s management system.
- Warehouse Management Software (WMS) or Inventory Management Software: This software receives data from the barcode scanners and updates inventory records, providing accurate, real-time inventory levels and facilitating order processing and stock management.
Warehouses cater to a wide array of functions and requirements, necessitating different types of labels tailored to meet specific operational needs. To gain a thorough insight into these label varieties and discover how they can enhance your warehouse’s efficiency, delve into our detailed guide on Types of Warehouse Labels.
Additionally, for guidance on selecting the perfect labels for your setup, our article How to Choose Warehouse Labels will prove invaluable, providing you with expert advice and practical tips to make informed decisions.
What Is the Best Barcode for Barcoding Warehouses?
The best barcode for a warehouse depends on several factors, including the nature of the inventory, item or product size, the detail of information required, environmental conditions, and compatibility with the warehouse management system.
Barcodes fall into two main categories: 1D Barcodes (Linear Barcodes) and 2D Barcodes. 1D barcodes are the traditional barcodes that consist of parallel lines and spaces to represent data. In contrast, 2D barcodes use patterns and graphics for data representation, allowing for more information in a smaller space. For a comprehensive comparison of 1D and 2D barcodes, our 1D vs 2D Barcode Comparison Guide is an invaluable resource.
Here are the most commonly used warehouse barcode types and their ideal applications.
1D Barcodes:
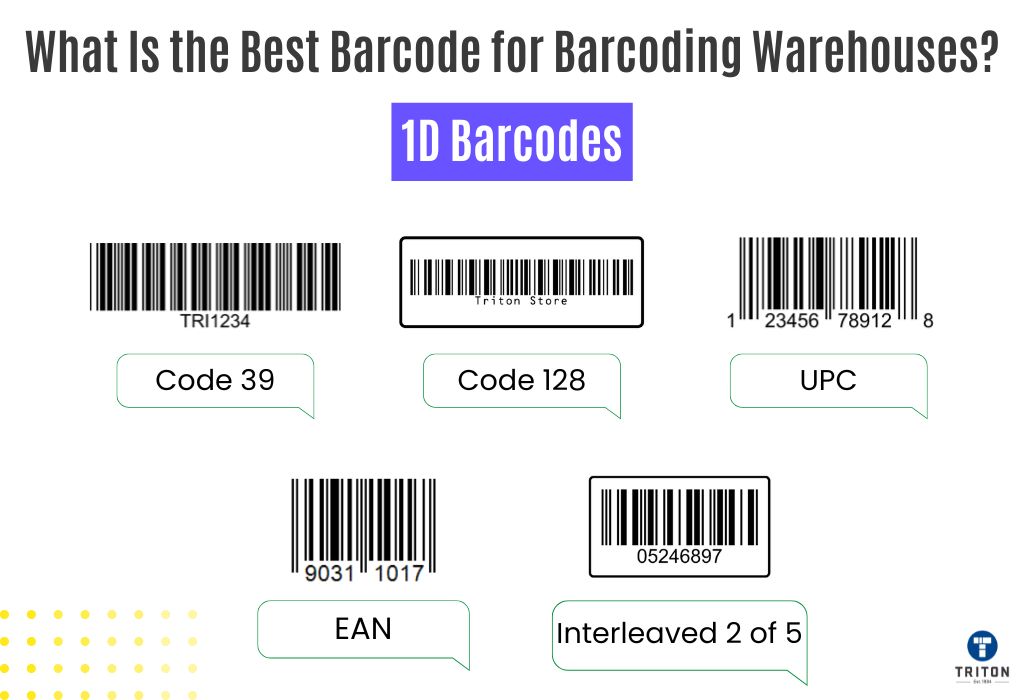
- Code 39: A versatile symbology that encodes letters, numbers, and a few special characters. Ideal for labelling goods that require alphanumeric data.
- Code 128: Known for its high-density data capacity and capability to encode all 128 ASCII characters. Suitable for packaging and shipping labels due to its compact size and high-density data capacity.
- UPC (Universal Product Code) and EAN (European Article Number): Predominantly used in retail for tracking store trade items. Its widespread adoption makes it useful for warehouses managing retail products.
- Interleaved 2 of 5: Best for numeric-only data, this symbology is highly efficient for encoding long sequences of numbers in a compact format.
2D Barcodes:
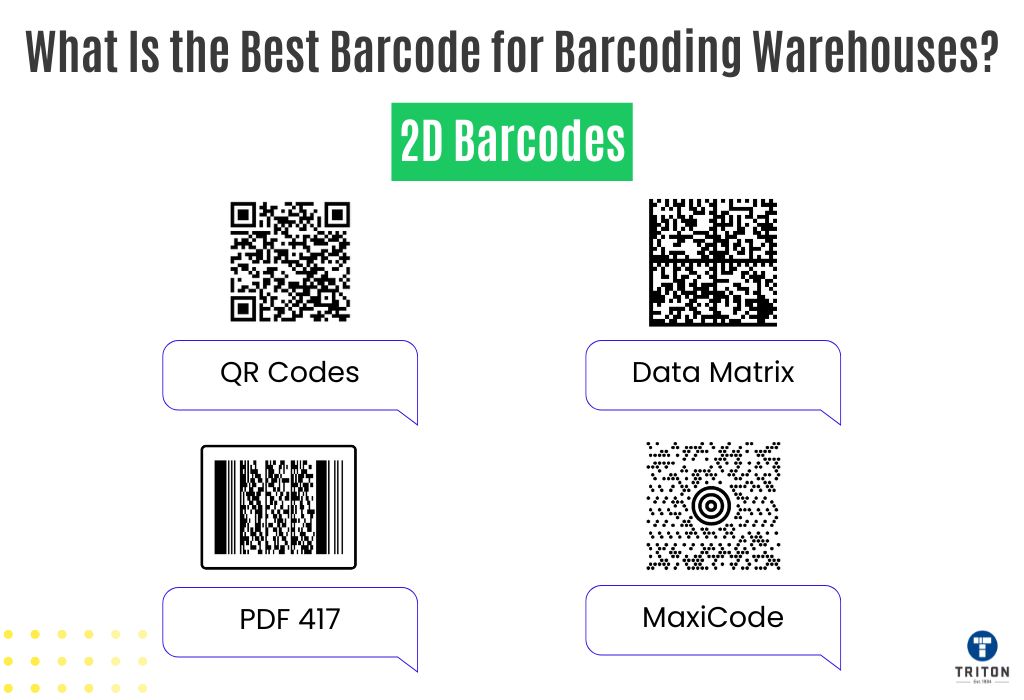
- QR Codes: Capable of storing a large amount of data, including URLs and graphics. Ideal for quick access to product information in dynamic barcode inventory systems.
- Data Matrix: Known for its small size and high data capacity. Ideally suited for space-constrained components or items that require detailed information like part numbers or manufacturing data.
- PDF 417: A stacked barcode that can encode large amounts of data, including text and numbers. Suitable for documents and identification cards in logistics.
- MaxiCode: Designed for high-speed sorting and tracking of packages. Used by major parcel delivery services, making it a good choice for warehouses involved in shipping and receiving tasks.
To sum it up, 1D barcodes are typically sufficient for basic inventory tracking. However, for more complex needs or to store additional information, 2D barcodes are necessary. The choice between 1D and 2D barcodes should be guided by your specific warehouse needs, considering current operations and future scalability.
For a more detailed exploration of the various barcode symbologies available and how they can be effectively utilised in different settings, refer to our comprehensive article, Barcode Types.
Use BarTender to Create Warehouse Barcodes!
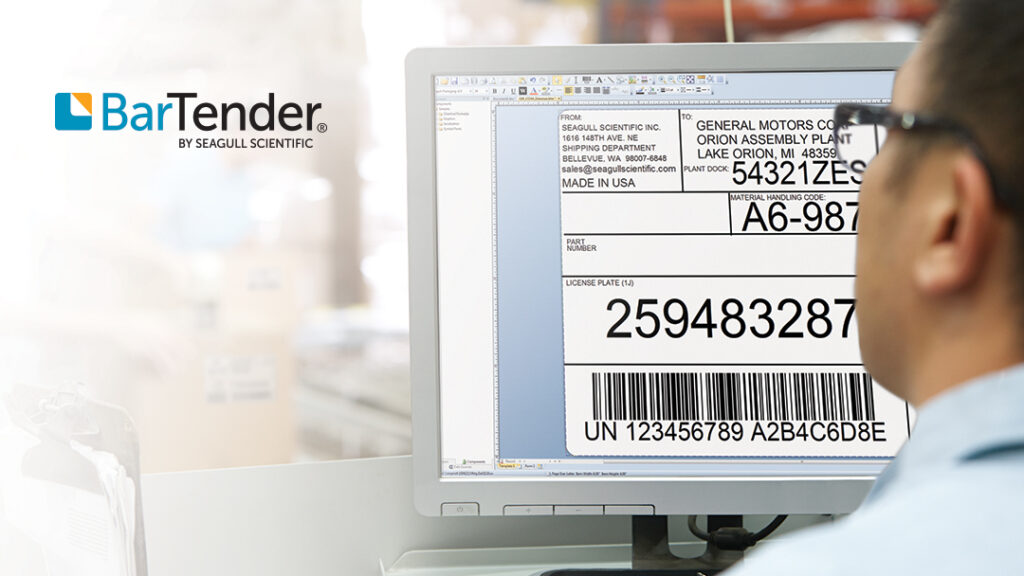
Efficient warehouse management starts with creating accurate and reliable barcodes. While free barcode generators offer a no-cost solution, they fall short in robustness, reliability, and support needed for professional operations.
BarTender by Seagull Scientific emerges as a superior solution, offering capabilities far exceeding free barcode generators. This comprehensive label designing and printing software facilitates the creation of labels, barcodes, RFID tags, and more, ensuring seamless integration into your warehouse operations.
BarTender’s standout feature is the ability to integrate smoothly with systems like ERP and WMS, making barcode generation a seamless part of your workflow. Its intuitive design tools allow for easy label and barcode creation, requiring no prior programming knowledge.
Offering over 400 pre-formatted barcode components and supporting 105 symbologies, BarTender meets a broad range of standards It also offers a variety of pre-formatted label templates ready for immediate use. The software’s capability to connect with various data sources, including databases and CSV files, along with its date/time serialisation capabilities, underscores its versatility for producing a wide array of barcodes and labels.
For more on BarTender’s features, see our What is BarTender? guide.
At Triton Store, we offer all four editions of BarTender software, namely, Starter Edition, Professional Edition, Automation Edition and Enterprise Edition. We also provide BarTender Cloud, a cloud-based solution for remote label printing and management, accessible from anywhere.
To explore the differences between BarTender Cloud and its on-premise counterpart, refer to our BarTender Cloud vs BarTender Software guide.
If you’re ready to elevate your warehouse’s labelling system or have specific inquiries, reach out to us through our live chat widget or by filling out a form on our website. Experience the difference with BarTender, and let Triton Store guide you to the ideal labelling solution for your business needs.
What Equipment Is Required for Implementing Barcode Systems in a Warehouse?
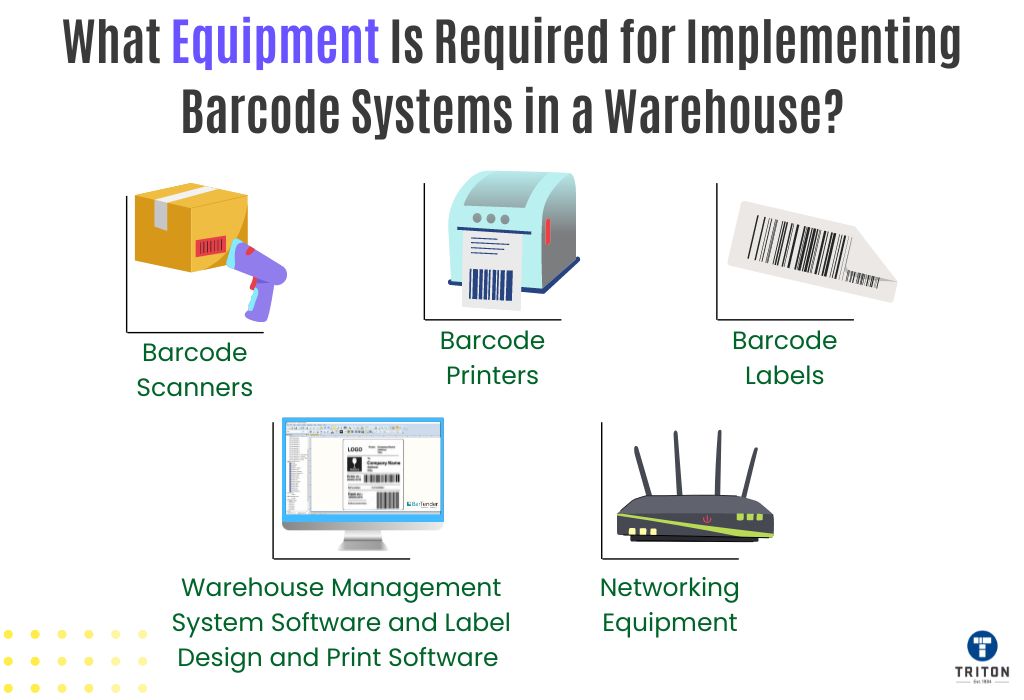
Implementing a barcode system in a warehouse requires a combination of hardware and software to ensure efficient and accurate inventory tracking. Here’s a breakdown of the essential equipment needed to set up a barcode system in a warehouse setting:
Barcode Scanners
A barcode scanner is a device that reads the information encoded within a barcode and translates it into a format that can be understood and processed by a computer system. It uses light sensors to detect the dark and light elements of a barcode—the bars and spaces—converting them into electrical signals that are then decoded into data. To better understand how barcode scanners work, consider exploring our detailed article, How do Barcode Scanners Work?
There are different types of barcode scanners. However, in a warehouse environment, the following types are best suited.
- Handheld Scanners: These are the most common type of barcode scanners used in warehouses. They are portable, easy to use, and can be wired or wireless, offering flexibility in various operational scenarios.
- Stationary Scanners: These are strategically placed at fixed points like entry and exit gates or along conveyor belts to automatically capture barcode data from passing items. These scanners are best suited for automated high-volume scanning.
- Mobile Computers: These devices combine a scanner with a mobile computing device and facilitate real-time updates to the WMS from the warehouse floor.
At Triton, we offer an extensive selection of scanners from leading brands such as Honeywell and Zebra. Our range is tailored to meet diverse warehouse requirements, featuring:
- Mobile terminals for on-the-go data access
- General-purpose scanners for a variety of applications
- Rugged scanners for demanding environments
- Fixed scanners and sensors for automated scanning
- USB scanners, wireless scanners, and Bluetooth scanners for connectivity flexibility
- 2D scanners for advanced barcode reading
Committed to the smooth running of your operations, Triton also supplies an extensive range of accessories and spare parts, and cables to ensure your equipment remains at peak performance.
Contact us via our live chat widget for expert advice tailored to the unique needs of your business.
Barcode Printers
Barcode printers are specialised devices designed to print readable barcodes on labels or tags that can be attached to warehouse inventory. These printers are essential for producing physical barcodes. The choice of a barcode printer depends on your specific needs, such as print volume, operational environment, and the type of labels required for your inventory.
Among the various technologies available for barcode printing, thermal printing stands out for its widespread adoption in warehouse settings. This preference is attributed to thermal printing’s ability to quickly produce high-quality barcodes that withstand fading, smudging, and scratching.
There are two primary thermal printing techniques: direct thermal and thermal transfer.
Direct thermal printers create images directly on heat-sensitive material, making them well-suited for short-term applications where the labels are not exposed to extreme light or heat. On the other hand, thermal transfer printers use a thermal ribbon to print on a wider variety of materials, offering labels that can endure longer storage periods and harsher conditions.
To compare and learn more about these two thermal print technologies, consider referring to our article, Direct Thermal vs Thermal Transfer Printers.
Recognising the critical role of the right printing technology in barcode applications, Triton Store stands as a trusted provider for all your thermal printing needs. Our comprehensive lineup includes thermal printers from leading manufacturers such as Epson, Element, Senor, Honeywell, Zebra, and TSC, alongside colour label printers from OKI.
Our inventory comprises various thermal printer models, including industrial printers, desktop printers, direct thermal printers, thermal transfer printers, barcode label printers, mobile printers and receipt printers.
Along with printers, Triton Store offers comprehensive, high-quality thermal print heads from leading brands such as Zebra, Honeywell, TSC, Intermec, Datamax, SATO, and Bizerba. We also have spare printer parts and accessories, waterproof printer enclosures, cables and cleaning wipes, all designed to optimise your printing operations and guarantee sustained high performance from your equipment.
Whether upgrading your current setup or starting from scratch, rely on Triton Store to provide the expertise and resources necessary for a seamless and efficient barcode printing experience.
Barcode Labels
Barcode labels are the physical medium that carries the barcode itself. These labels are affixed to items, shelves, or pellets within a warehouse, enabling the efficient tracking and management of inventory through barcode scanning systems. The effectiveness of a barcode system hinges on the quality and suitability of its labels, which come in diverse sizes, materials, and adhesives to match specific operational needs.
At Triton, we also supply thermal printer consumables. Our comprehensive range includes thermal transfer ribbons, thermal labels, thermal carton labels, thermal carcase tags, food-compliant thermal inserts, receipt rolls and shipping & freight labels. Each product in our selection meets the high standards required for effective barcode labelling.
Software
The software serves as the brain of the warehouse barcode system, essential for orchestrating the seamless operation of barcode scanning, printing, and data management. These software include.
- Warehouse Management System (WMS) Software: This software is the operational core of a warehouse, managing all aspects of inventory control. The WMS uses the data collected by barcode scanners to update inventory records, track product locations, and manage orders in real time. This software can also generate reports and analytics, helping managers make informed decisions about inventory levels, warehouse operations, and logistics.
- Label Design and Print Software: This software is crucial for creating and printing the barcode labels. This software allows for the customisation of barcode labels to meet specific requirements, including incorporating company logos, compliance with industry standards, and generating various barcode symbologies. Advanced label design software like BarTender can automate the label creation process by pulling product information directly from the WMS or other databases, ensuring labels are accurate and up-to-date. To find the best label printing software click here.
Networking Equipment
A robust wireless network infrastructure is foundational for the seamless operation of wireless barcode scanners, mobile computers, and other connected devices within a warehouse. This infrastructure ensures that devices can communicate with the WMS and each other, facilitating real-time data exchange and timely updates.
Key components include.
- Wireless Access Points (WAPs): These devices provide the wireless coverage needed for barcode scanners and mobile computers to connect to the network from anywhere in the warehouse.
- Routers and Switches: Routers direct data traffic, ensuring information flows between the warehouse network and external networks, including the Internet and other corporate networks. Switches connect multiple devices on the same network within a building, allowing them to communicate directly with each other.
- Network Security Solutions: Protecting the data transmitted across a warehouse’s network is paramount. Implementing robust network security measures, such as firewalls, encryption, and secure access protocols, is critical to prevent unauthorised access and protect sensitive information from cyber threats.
How to Implement a Barcode System in the Warehouse?
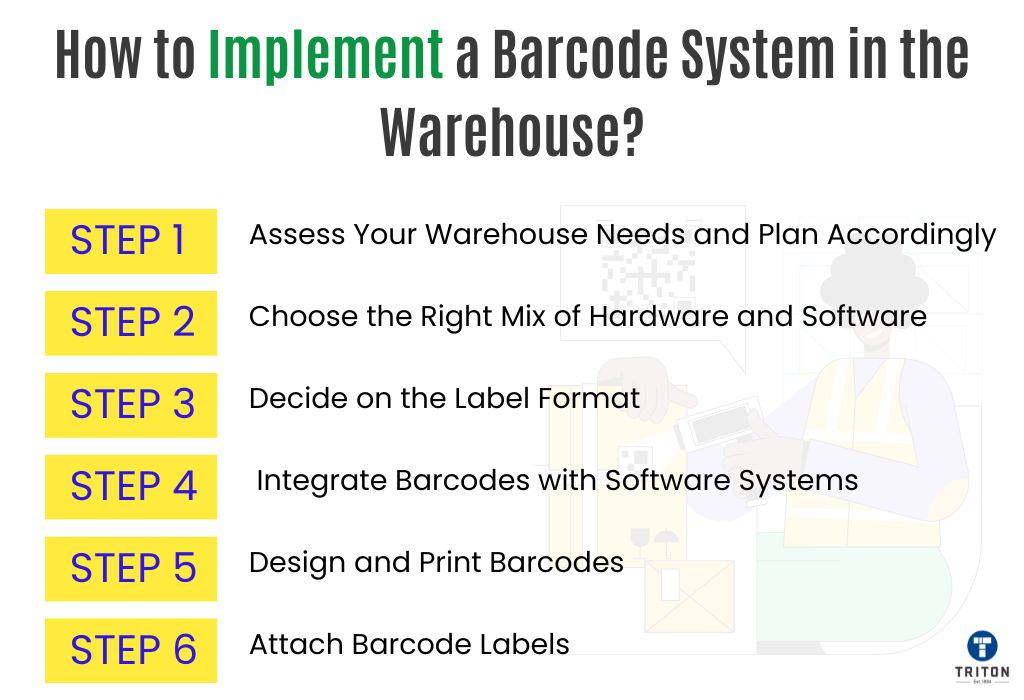
Implementing a barcode system in your warehouse is a strategic move towards enhancing efficiency, accuracy, and visibility. This process, while straightforward, requires careful planning and execution to ensure success.
Here’s a step-by-step guide on how to use barcodes for warehouse management.
Step 1: Assess Warehouse Needs and Plan Accordingly
Start with a thorough evaluation of your warehouse’s specific needs. Analyse the size and variety of your inventory, transaction volumes, warehouse layout and special conditions like cold or outdoor storage. Also, evaluate your existing inventory management practices, tracking mechanisms, and the overall movement of goods within your facility.
This assessment should also identify logistical inefficiencies and technological gaps that barcode implementation could address. For instance, manual data entry points prone to error, areas where product retrieval times are slow, or processes that lack real-time tracking capabilities are key candidates for improvement.
Step 2: Choose Your Technology
Selecting the right mix of hardware (barcode scanners, printers, and mobile computers) and software (WMS and label design software) is crucial. Your choices should align with the operational demands identified in Step 1.
For hardware, consider factors like mobility needs, scanning distance, and environmental conditions.
For software, prioritise compatibility with your hardware, ease of integration with existing systems, and support for the barcode standards relevant to your industry.
Step 3: Decide on Your Label Format
Define the information to be included on each barcode label, such as.
- Product name
- Product description
- Stock Keeping Unit Number (SKU)
- Lot Number
- Quantity
- Expiry Date
This decision influences the choice of barcode symbology (e.g., Code 128 for versatility, QR codes for larger data capacity).
Consider the physical constraints of where labels will be placed (e.g., small bins require smaller labels) and ensure the label material suits the warehouse environment (e.g., water-resistant labels for damp areas).
Step 4: Integrate with Software Systems
Configure your centralised software platform to work with your new barcode system. This integration is crucial for real-time inventory updates and data accuracy. The software should support your chosen barcode symbologies and facilitate easy data capture and retrieval.
This step may involve customising the software to fit your workflow and training staff on new procedures. Work closely with IT specialists to ensure a smooth data flow between barcode scanners and your software.
Step 5: Designing and Printing of Barcodes
Utilise software like BarTender for label creation, steering clear of overly customised designs that could hinder scanning efficiency. Focus on creating well-sized, easily scannable barcodes, with readability as the top priority.
Print labels at 300 dpi for the sharpest clarity. However, 203 dpi is also suitable for applications where high resolution is not critical.
For further insights into crafting effective barcode labels and avoiding common pitfalls, explore our articles on Mistakes to Avoid When Designing Barcodes and Best Practices for Barcode and Label Designing.
Step 6: Attachment of Barcodes
The final step is strategically placing barcode labels on inventory items, shelves, and bins. Ensure labels are affixed in easily accessible and visible areas to facilitate quick, accurate scanning.
For guidance on effectively attaching barcodes to racks, delve into our comprehensive article, How to Label Warehouse Racking. This resource provides detailed instructions and best practices for labelling warehouse racking, ensuring your setup is optimised for efficiency and accuracy.
Other Considerations
Train Your Team
Conduct comprehensive training sessions for your staff, covering how to use the barcode scanners, printers, and any software changes. Training should include best practices for scanning, label handling, and troubleshooting common issues. Ensure that all users are comfortable with the new system before full implementation.
Test and Adjust
Conduct a pilot test of the barcode system in a controlled section of your warehouse before full implementation. This testing phase will allow you to identify and resolve any issues with scanning accuracy, label quality, or software integration.
Gather feedback from staff and make necessary adjustments.
Full Implementation and Continuous Improvement
Roll out the barcode system across your entire operation, closely monitoring any issues and making adjustments as needed. After implementation, regularly review the system’s performance and seek ways to optimise further.
Continuous improvement will help you adapt to changing business needs and leverage new technologies as they become available.
Why Should You Use a Barcode System for a Warehouse?

Implementing a barcode system in a warehouse significantly enhances operations across various fronts. Let’s delve into the benefits of using barcodes in a warehouse setting.
Enhanced Accuracy and Efficiency
Barcode systems drastically reduce human errors linked to manual data entry. Scanning barcodes, as opposed to typing information, minimises the risk of errors. This method ensures more accurate inventory records and speeds up operations such as receiving, sorting, and shipping, thereby boosting overall productivity.
Streamlined Receiving and Sorting Processes
With barcode technology, the receiving and sorting of goods become more organised and less time-consuming.
Scanning barcodes on arrival automatically updates inventory levels and assists in immediately categorising products for storage or further processing. This streamlined process reduces bottlenecks at the receiving dock, ensuring products are quickly available for sale or dispatch.
Real-Time Inventory Management and Data-Driven Decision Making
Barcodes provide real-time visibility into inventory levels, enabling warehouses to manage stock more effectively. This immediate access to data supports data-driven decision-making, allowing managers to respond swiftly to stock needs, predict ordering requirements, and optimise inventory turnover rates.
Real-time data supports a lean inventory approach, optimising stock levels to meet customer needs without overinvesting inventory.
Seamless Integration
Barcode systems can seamlessly integrate with Warehouse Management Systems (WMS) and other enterprise resource planning (ERP) tools. This integration allows for the automatic update of inventory records upon scanning, ensuring that all systems reflect current data.
Such cohesion between systems enhances data accuracy and streamlines operations. It provides a unified overview of warehouse activities, facilitating better strategic planning and resource allocation.
Faster Inventory Audits
Inventory audits with a barcode system are significantly faster and more accurate than manual counts.
Scanners quickly capture product information, making verifying stock levels and identifying discrepancies easier. This efficiency reduces the downtime and labour costs associated with manual inventory checks, allowing for more frequent audits and consistent inventory accuracy.
Increased Visibility and Reduction of Ghost Inventory
Barcode systems enhance inventory visibility, addressing issues like ghost inventory—items listed in the inventory system but not physically present in the warehouse.
Barcodes track every item’s movement through the warehouse and update records in real time. This visibility helps identify discrepancies early, preventing the financial and operational issues associated with unaccounted-for stock.
Compliance and Traceability
Barcodes provide a traceable record of product movement from receipt to dispatch in regulated industries such as food and beverage. This traceability is crucial for compliance with safety standards, managing recalls, and ensuring products meet industry requirements.
Barcodes also make retrieving historical data for audits easy, demonstrating compliance and safeguarding against legal or financial penalties.
Scalability
As business grows, so does the complexity of managing inventory. Barcode systems can scale to accommodate increased volume without a proportional increase in errors or inefficiencies. Whether adding new products or expanding operations, barcode systems adjust seamlessly, supporting growth with minimal additional cost or complexity.
Cost Savings
While implementing a barcode system requires an initial investment, the long-term savings are substantial.
Reduced errors, decreased labour costs, improved inventory management, and faster processing times all contribute to significant cost reductions. These savings contribute to a healthier bottom line, allowing for reinvestment in growth and innovation.
Best Practices for Barcoding in a Warehouse Setting
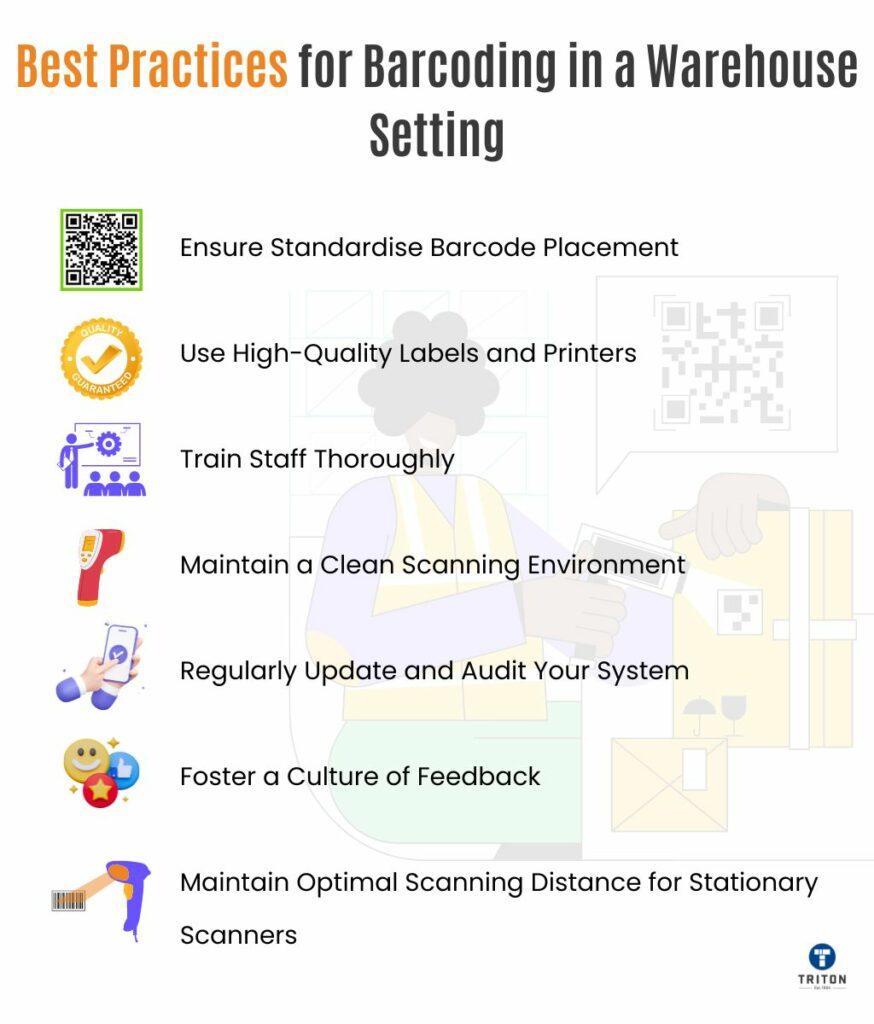
To maximise the efficiency and effectiveness of a warehouse barcoding system, it’s essential to implement best practices meticulously. Here’s how to ensure these practices are followed and optimised for your operations.
Standardise Barcode Placement
Achieve consistency in barcode placement on items, shelves, and bins to facilitate quicker scanning and reduce errors. Analyse your warehouse’s workflow to identify the most accessible points for barcode scanning.
For boxed items, place barcodes in locations that remain accessible when stacked. For irregularly shaped items, choose a flat surface that faces the user during scanning. On shelves or bins, position barcodes at eye level or just below and on the same side across all aisles.
Standardising barcode placement reduces the time spent by staff searching for barcodes, streamlining the scanning process across the warehouse.
Use High-Quality Labels and Printers
Select labels that are durable and suited to your warehouse environment. For instance, use laminated labels to prevent wear in areas prone to moisture or abrasion. Opt for printer models that support various label sizes and offer high-resolution printing to ensure clear and scannable barcodes.
Regular testing of printed barcodes against standard distances and angles can help maintain quality control, ensuring every printout meets readability standards.
Train Staff Thoroughly
Comprehensive training for all staff members who will interact with the barcode system is crucial. Training should cover scanning techniques, proper handling of equipment, and troubleshooting common issues. Incorporate regular refresher courses to keep staff up-to-date on barcode technology and warehouse process changes.
Well-trained employees are more likely to use the system efficiently, contributing to its overall success.
Maintain a Clean Scanning Environment
Ensuring that barcode labels and scanners remain clean and free from obstructions is vital for the smooth operation of your barcode system. Use electronic-safe cleaning solutions and soft cloths to avoid damaging sensitive components.
For areas exposed to high dust or debris, protective covers for scanners and regular cleaning intervals can prevent buildup that might obscure barcodes.
Encourage staff to report any damaged or unreadable labels immediately, ensuring maintenance or replacement can occur promptly to keep operations running smoothly.
Explore our resource on How to Clean Barcode Scanners and Thermal Printer Cleaning and Maintenance Guide for detailed guidance on keeping your equipment in top condition.
Regularly Update and Audit Your System
Barcode systems are not set-and-forget solutions. Regular updates to software and hardware, as needed, keep the system running smoothly and securely.
Periodic audits of barcode accuracy and inventory levels help identify any discrepancies early, allowing for timely corrections and updates to inventory records.
Foster a Culture of Feedback
Encourage staff to provide feedback on the barcode system’s usability and effectiveness. Frontline workers often have valuable insights into potential improvements or issues that may not be immediately apparent to management.
Actively listening and responding to this feedback fosters a culture of continuous improvement.
Maintain Optimal Scanning Distance for Stationary Scanners
For stationary or fixed barcode scanners, it’s crucial to maintain the correct distance between the scanner and the barcode to ensure accurate and efficient scanning. The optimal distance varies depending on the scanner’s specifications and the barcode size. However, typically, the scanning distance ranges from a few inches to a foot away (approximately 6 to 30 cm).
Consult your scanner’s manual for the manufacturer’s recommended scanning distance.
Frequently Asked Questions
What Is Barcoding in a Warehouse?
Barcoding in a warehouse involves using barcodes to identify and track inventory items, equipment, and storage locations. This system streamlines operations by automating data capture, enhancing accuracy, and speeding up processes like receiving, sorting, and shipping.
What Is Inventory Barcoding?
Inventory barcoding is the practice of attaching barcodes to inventory items to facilitate automated tracking and management. Each barcode uniquely identifies a product, containing data such as the product name, SKU, and quantity.
Check out our Mastering Barcode Inventory Systems Guide for a comprehensive understanding of barcoding inventory systems and how to effectively implement them.
How Does Barcoding Improve Warehouse Efficiency?
Barcoding improves warehouse efficiency by automating the tracking of inventory movements, reducing manual data entry errors, and speeding up the retrieval and storage of items. It enables quick and accurate inventory audits, facilitates faster decision-making through real-time data access, and streamlines the entire supply chain process from receiving to shipping.
Can Barcoding Systems Integrate With Existing Warehouse Management Systems?
Yes, barcoding systems can integrate with existing Warehouse Management Systems (WMS) to enhance functionality and data accuracy. This integration allows for seamless communication between the barcode system and the WMS, ensuring that inventory records are automatically updated upon scanning.
The Bottom Line
Adopting warehouse barcode solutions is not just about modernising operations; it’s about setting a foundation for streamlined efficiency, pinpoint accuracy and a dynamic inventory management system. Throughout this guide, we’ve detailed the crucial steps and best practices to navigate the implementation process effectively.
By embracing these strategies, warehouses can significantly minimise errors, accelerate processes, and ultimately, drive productivity to new levels. The journey to integrating barcoding into your warehouse operations is a strategic investment in your business’s future, promising a robust return through improved operational clarity and performance.
We hope this article was useful.
Thanks for reading!