Manufacturers often encounter significant hurdles in inventory and quality management due to the dual challenges of maintaining operational accuracy and boosting efficiency. Errors in these areas escalate costs and impact delivery timelines, affecting customer satisfaction and competitive standing.
Barcode systems emerge as a strategic solution to these issues. They provide a reliable mechanism for tracking products, components, and processes with unparalleled precision. Their implementation streamlines operations, minimising errors and enhancing visibility across the supply chain.
This guide explores the integration of barcode technology within manufacturing operations, demonstrating its significant influence on enhancing efficiency, accuracy, and cost savings. It outlines best practices and implementation strategies, providing manufacturers with a strategic framework to employ barcode systems effectively.
What are Barcodes and How Do They Work?
Barcodes are digital fingerprints for products and components, offering a unique identifier that can be read by barcode scanners. At their core, these systems encode information in visual patterns — either lines or graphics — that represent data such as SKU, product numbers, batch details, and more. The scanning process decodes this pattern back into digital data, facilitating rapid and accurate data entry.
There are two primary types of barcodes used in manufacturing: one-dimensional (1D) and two-dimensional (2D).
1D barcodes consist of a series of vertical lines of varying widths and spacings. These encode data horizontally and are limited in the amount of information they can hold.
In contrast, 2D barcodes encode data using complex patterns such as dots, squares, hexagons, and other shapes. These encode information both horizontally and vertically, allowing for a more substantial amount of data within a smaller space.
For a comprehensive understanding of barcodes and their operational principles, refer to our dedicated guide, What is a Barcode?
What Barcodes are the Best for Manufacturing?
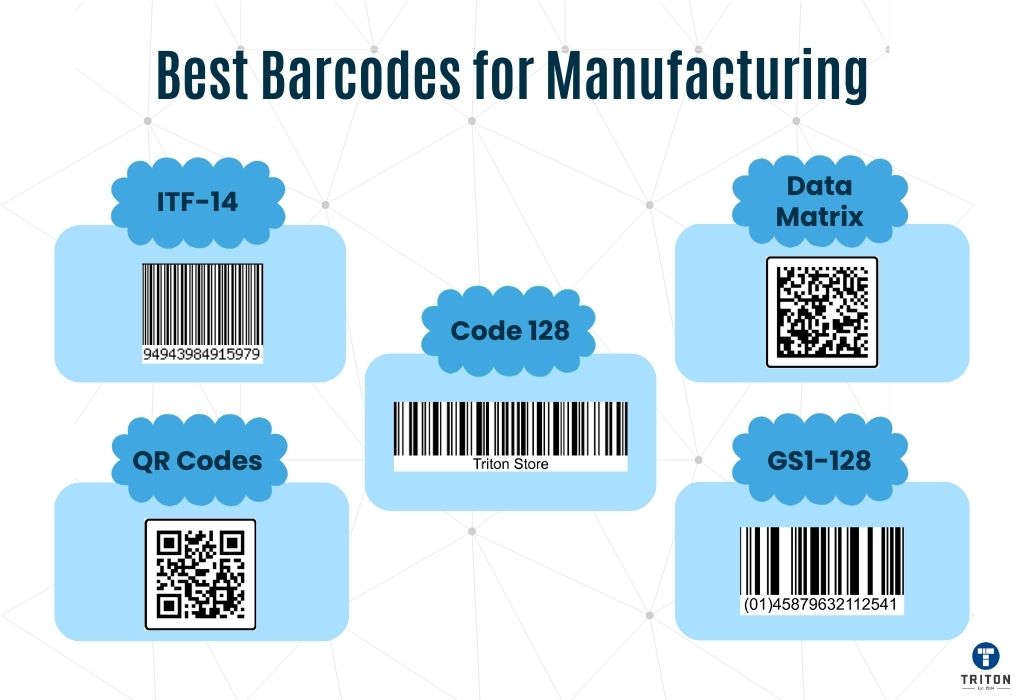
In the manufacturing sector, the choice of barcode symbology plays a crucial role in the efficiency and reliability of tracking and managing operations. Here are key barcode symbologies commonly utilised in the manufacturing industry:
- Code 128: Widely recognised for its high-density data capacity, Code 128 is versatile and can encode all 128 characters of ASCII. This makes it suitable for packaging, shipping, and tracking applications where a compact barcode with extensive information is necessary.
- Data Matrix: Preferred for its ability to encode large amounts of data into a small space, the Data Matrix code is often used for marking small items, components, and electronic parts. It’s robust, with error correction capabilities that allow readability even when damaged, making it ideal for challenging industrial environments.
- QR Codes: Known for quick scanning and high storage capacity, QR codes are used in manufacturing for inventory management, providing product information, and linking to digital content. Their ability to be scanned with smartphones facilitates easy access to data on the shop floor.
- GS1-128: This symbology is designed to provide a global standard for exchanging data between different companies. GS1-128 barcodes are used for logistical and shipping labels, enabling tracking from production through delivery with serialised shipping container codes.
ITF-14: The ITF-14 barcode is specifically designed to encode the Global Trade Item Number (GTIN) for products. It is typically used on shipping containers, cartons, and pallets, providing a standardised method for tracking products in large-scale distribution.
How are Barcodes Used in Manufacturing?
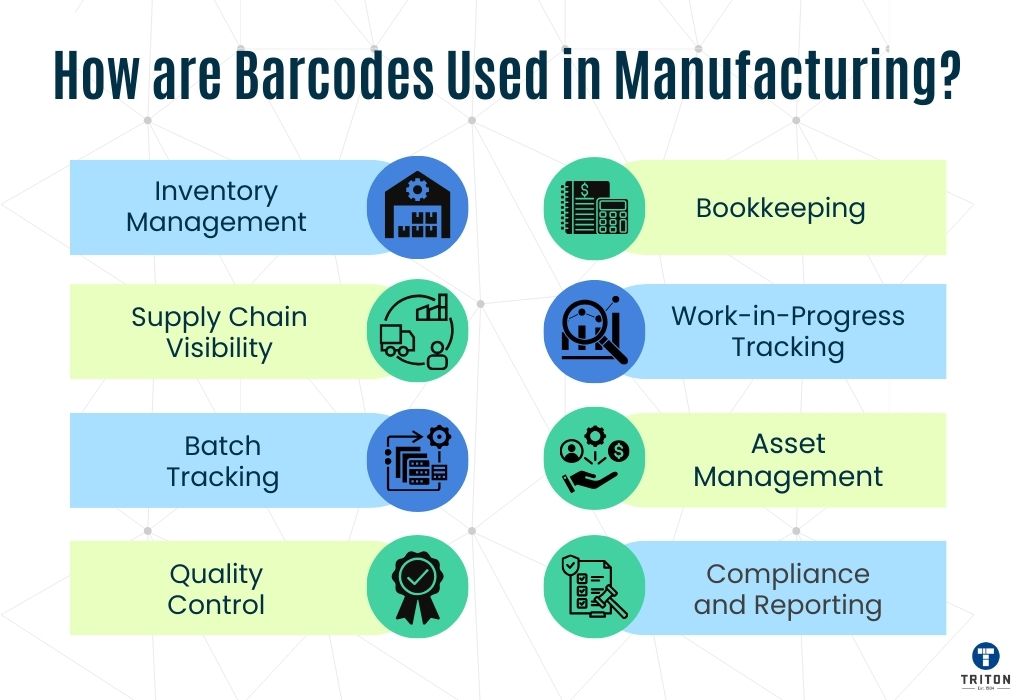
Barcodes are crucial in modern manufacturing processes, enhancing efficiency, accuracy, and traceability across various operations. Here’s how barcodes are utilised in the manufacturing industry.
Inventory Management
Barcodes streamline inventory management by allowing quick scanning of products and materials as they enter, move through, or leave a facility. This automation reduces manual data entry errors and provides accurate, real-time inventory counts.
Managers can instantly access inventory levels, facilitating better purchasing decisions and reducing the risk of stockouts or excess inventory. Refer to our Barcode Inventory System Guide to learn more about inventory barcoding.
Supply Chain Visibility
Barcodes enhance supply chain visibility by offering a clear view of the movement of goods from suppliers to the manufacturing floor and then to the customers. Each scan captures vital data such as location, movement dates, and handler details, enabling companies to track shipments, predict arrival times, and manage supply chain logistics efficiently.
Batch Tracking
Barcodes are essential for batch tracking in manufacturing, allowing companies to track the production, inspection, and distribution of batches. This capability is crucial for recalling specific batches if defects are discovered, understanding batch-related quality issues, and managing expiration dates for perishable goods.
Quality Control
Barcodes ensure that products and components are correctly identified and tracked through each stage of production and inspection. This system facilitates the tracing of quality issues to their source, enabling quick corrective actions and minimising the impact of defects.
Bookkeeping
Barcodes simplify the tracking of purchases, sales, and inventory adjustments. Scanning barcodes on invoices, orders, and inventory items automates the entry of this data into accounting systems, enhancing accuracy and saving time.
Work-in-Progress (WIP) Tracking
Barcode tracking helps monitor production flow, identify bottlenecks, and ensure efficient resource utilisation. Real-time visibility into WIP status aids in effectively scheduling and managing production timelines.
Asset Management
Using barcodes for asset management ensures accurate machinery, equipment, and tools tracking. Scanning assets for maintenance, usage, or location changes helps schedule preventive maintenance, reduce equipment downtime, and manage asset life cycles.
For an in-depth exploration of implementing barcodes in asset tracking, visit our comprehensive guide – Barcode Asset Tracking.
Compliance and Reporting
Barcodes are a powerful tool for automating data collection and reporting in sectors like chemical manufacturing, where regulatory compliance is critical. They meet traceability, safety, and quality standards, simplifying audits and reporting processes. This system supports adherence to industry regulations and standards, protecting companies from non-compliance risks.
When Do You Need a Barcode System in Manufacturing?
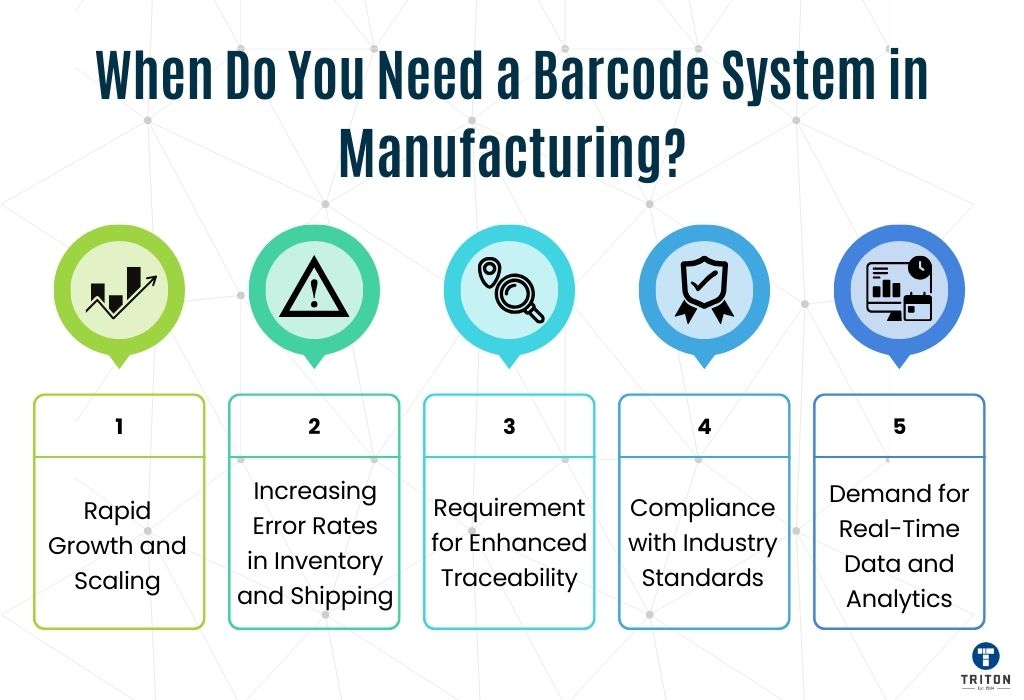
Deciding when to implement a barcode system in manufacturing hinges on recognising the signs that your current processes could significantly benefit from automation and improved tracking. Here are key indicators that it’s time to adopt a barcode system:
Rapid Growth and Scaling
As manufacturing operations expand, managing inventory, assets, and processes becomes exponentially more complex. A barcode system enables scalable growth by automating data collection and tracking, ensuring that operations remain streamlined despite increasing volume.
Increasing Error Rates in Inventory and Shipping
Manual data entry and tracking methods are prone to errors, leading to inventory discrepancies, shipping mistakes, and unhappy customers. Implementing a barcode system drastically reduces these errors, improving accuracy in every facet of the manufacturing process.
Need for Enhanced Traceability
In industries where product recall or tracing the origin of materials is essential—such as food, pharmaceuticals, and chemicals—barcodes provide the necessary level of detail for traceability. This ensures safety, compliance, and accountability across the supply chain.
Compliance with Industry Standards
Certain industries require adherence to specific standards and regulations that mandate using barcode systems for tracking and reporting. Integrating these systems ensures compliance and enhances operational transparency and efficiency.
Demand for Real-Time Data and Analytics
Manufacturers needing immediate access to data for decision-making, trend analysis, or operational adjustments will find barcode systems essential. These systems provide real-time insights into inventory levels, production progress, and more, facilitating informed decision-making.
How to Implement a Barcode System in Manufacturing?
Implementing a barcode system in manufacturing is a strategic process that involves careful planning, the right equipment, and a step-by-step approach to integration. Here’s a detailed look at the equipment required and the implementation process.
Equipment Required
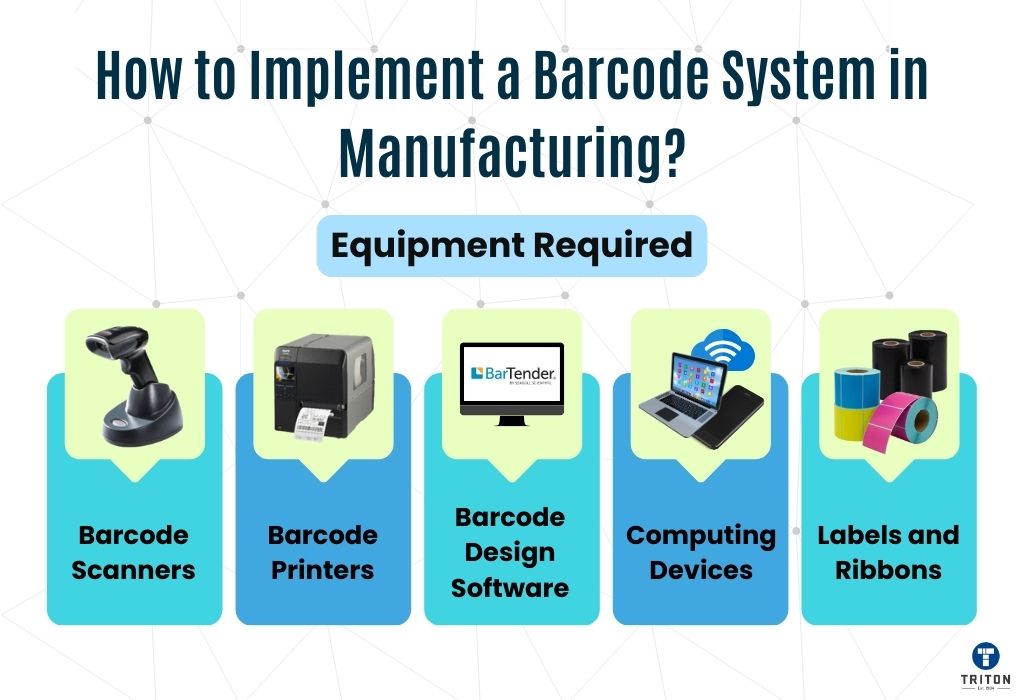
The successful implementation of a barcode system in manufacturing hinges on selecting the right equipment. Each piece is pivotal in ensuring the system’s overall efficiency and reliability.
Barcode Scanners
Barcode scanners are integral for reading the information encoded within a barcode. There are various types of barcode scanners, each suited to different operational needs.
- Handheld Scanners: Versatile and portable, ideal for use in warehouses and on the production floor where mobility is necessary.
- Stationary Scanners: Mounted in a fixed position, these are best for reading barcodes on items as they pass through a point in a conveyor system or entry/exit points.
- Wireless Scanners: Offer the flexibility of handheld scanners but without the constraints of cables, enhancing mobility and ease of use in large spaces.
- Imager Scanners: Capture images of the barcode and decode information from 2D barcodes like QR codes, ideal for environments where both 1D and 2D barcodes are in use.
- Rugged Barcode Scanners: Designed for harsh manufacturing environments, rugged scanners are built to withstand drops, dust, and water. Their durability makes them suitable for use in outdoor settings, around heavy machinery, or in any place where a regular scanner might be damaged.
- Mobile Terminals: These handheld devices combine a barcode scanner with a computer, allowing for direct interaction with your inventory management system. They are essential for applications requiring mobile data collection and processing.
- USB Barcode Scanners: Connect directly to a computer via a USB port, offering a simple and reliable scanning solution. They offer a plug-and-play solution and are ideal for stationary points like checkout counters or inventory stations where mobility is not a priority.
Bluetooth Barcode Scanners: Offer the flexibility of wireless scanning with the added benefit of Bluetooth connectivity, allowing them to pair with various devices, including tablets, smartphones, and Bluetooth-enabled computers. This type is best for environments where scanners need to be frequently moved between different workstations.
Barcode Printers
Choosing an appropriate barcode printer is crucial for generating scannable and durable labels for manufacturing operations. Here’s a detailed look at different types of barcode printers:
- Direct Thermal Printers: Use heat from the thermal printhead to create an image directly on heat-sensitive barcode labels. Ideal for applications where barcodes are used in the short term and not exposed to extreme conditions, such as indoor retail environments, receipts and temporary shipping labels. The lack of ink or toner makes them cost-effective for certain applications.
- Thermal Transfer Printers: Employ a thermal ribbon to print on various label materials, producing durable, long-lasting labels capable of withstanding harsh conditions. These printers are preferred in manufacturing for labelling products, inventory, and assets that may face exposure to elements like chemicals and heat.
- Inkjet Printers: Spray ink onto labels to generate barcodes and images. While less common for barcode creation due to durability concerns, recent advancements have broadened their application, especially where high-resolution labels are needed, such as on product packaging. They offer versatility with the ability to print on various materials.
- Laser Printers Attract toner to paper with static electricity, creating sharp and clear prints. Although they provide high-quality prints, laser printers are less favoured for barcode printing because the heat during the printing process can lead to barcode edge distortion, affecting scan reliability. They are suitable for office environments where high-volume barcode printing is not required.
In general, thermal printers stand out as the preferred option for manufacturing, given their robustness and flexibility. These printers are available in various models, including desktop printers, mobile printers, industrial printers, and dedicated barcode label printers, ensuring accessibility and suitability for a wide range of operational needs. This diversity allows businesses to select the perfect fit for their specific environment and printing volume requirements.
Labels and Ribbons
Labels and ribbons form the foundational elements of barcode printing, ensuring that the information encoded in barcodes is accurately represented and remains readable throughout the product’s lifecycle.
Labels serve as the physical medium that carries the barcode, while ribbons (in thermal transfer printing) provide the ink or substance that creates the barcode image on the label. Their quality and compatibility are essential for producing durable, scannable barcodes that can withstand the environmental conditions they are exposed to, from the manufacturing floor to the end user.
Computing Devices
Computing devices are essential in bridging the gap between the physical world of barcodes and digital data management. These devices process, store, and analyse the data captured by barcode scanners, integrating it into the broader manufacturing and business systems. Here are the devices you will need.
- Desktop Computers: Act as the central hub for barcode operations, handling tasks from label design to barcode system management. They are crucial for processing and analysing large volumes of data, interfacing with enterprise resource planning (ERP) systems, and other business software.
- Mobile Devices: Include tablets and smartphones equipped with barcode scanning capabilities either through built-in hardware or external attachments. These devices offer unparalleled flexibility and mobility, allowing for on-the-spot scanning and data entry on the manufacturing floor, in the warehouse, or during transportation.
- Internet Connectivity – Facilitates the immediate upload of barcode data to cloud-based systems and its distribution across various locations. It enables real-time data synchronisation, granting uninterrupted access to inventory statuses, tracking details, and analytics from any location.
Barcode Design Software
Barcode design software is an essential tool in the creation and management of barcodes for manufacturing operations. This software allows for the precise design of barcode labels, ensuring they meet industry standards and are optimised for scanning accuracy.
Key features and considerations include:
- Customisation: The software provides a range of design options, enabling the customisation of barcode labels to include not only the barcode itself but also text, logos, and other relevant information. This flexibility ensures that labels can be tailored to specific product requirements, branding, or regulatory compliance needs.
- Compatibility: The software must support the barcode symbologies and printing technologies used in your manufacturing processes. Compatibility with various barcode standards (e.g., UPC, EAN, QR Code, Data Matrix) and printer types ensures seamless design-to-print workflows.
- Integration: Advanced barcode design software can integrate with existing inventory management, enterprise resource planning (ERP), and supply chain management (SCM) systems. This integration allows for the automatic generation of barcode labels based on inventory data, streamlining the labelling process and reducing manual data entry errors.
- Ease of Use: While offering advanced features, the software should also be user-friendly, with an intuitive interface that allows for quick learning and adoption by staff. Ease of use reduces training time and supports efficient operations.
- Scalability: As manufacturing operations grow, barcode design needs may evolve. Software that can scale with your business, supporting an increasing volume of label designs or more complex labelling requirements, is a valuable asset.
Seagull Scientific’s BarTender Software emerges as a leading solution in label design and barcode generation, offering capabilities surpassing standard free tools. This comprehensive software facilitates the streamlined creation of various labels, including barcodes, RFID tags, and more.
Featuring an extensive library of over 400 pre-designed barcode components and supporting 105 symbologies, BarTender is adept at meeting various industry standards. Its rich assortment of label templates, combined with the capability to connect to multiple data sources such as databases and CSV files, enhances its adaptability for generating a diverse array of barcode and label types. The software’s advanced serialisation functions further attest to its versatility and efficiency in label creation.
Seagull Scientific has tailored BarTender to meet varying needs through four distinct editions: Starter, Professional, Automation, and Enterprise, as well as a cloud version called BarTender Cloud.
The Starter Edition caters to the needs of smaller teams requiring basic label design functionalities. The Professional Edition offers advanced features suitable for complex labelling requirements.
The Automation Edition is a perfect fit for organisations aiming to streamline operations through automation, whereas the Enterprise Edition is designed to serve the expansive needs of large-scale enterprises. Further enhancing its utility, BarTender Cloud introduces the flexibility of cloud-based label management and printing, accessible from any location.
For a detailed examination of BarTender’s extensive features and to discern the right edition for your business needs, consider exploring our article, What is BarTender? Furthermore, for insights into the comparative advantages of BarTender Cloud over its on-premise counterparts, our guide, BarTender Cloud vs BarTender Software, serves as a valuable resource.
Implementation Process
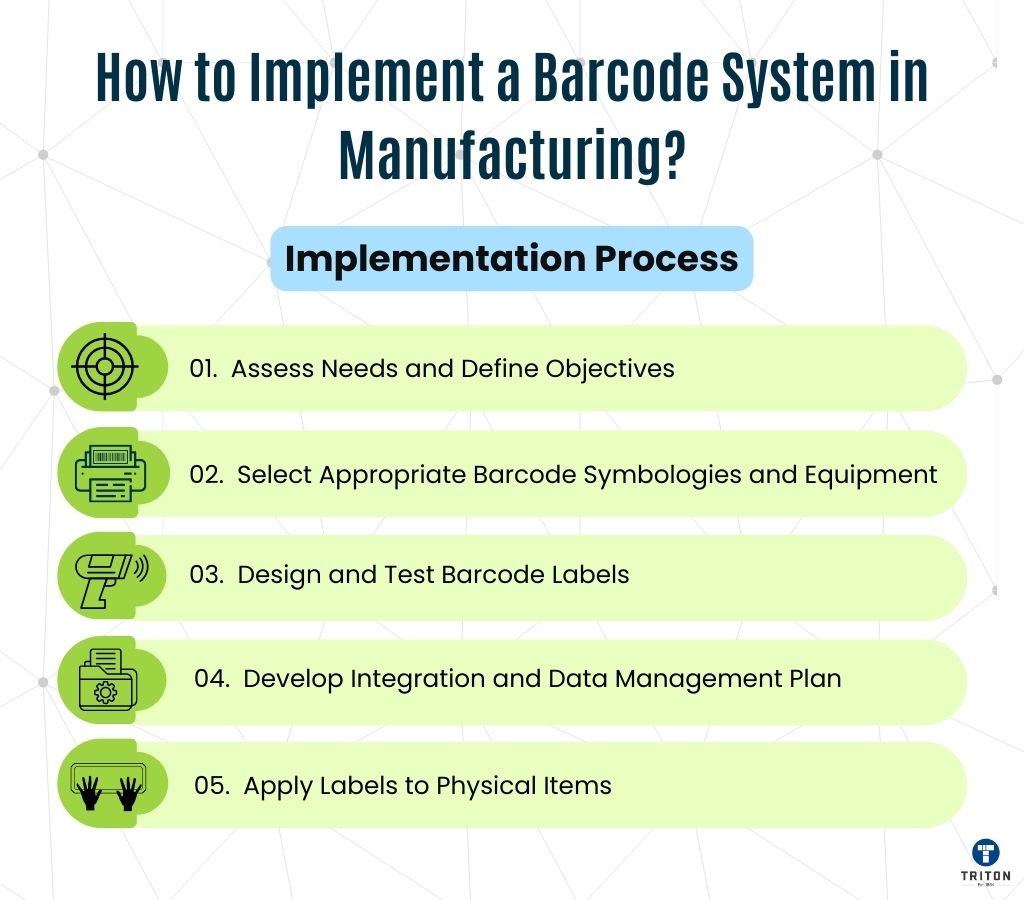
Implementing a barcode system in a manufacturing setting involves a series of well-defined steps, each critical to ensuring the system’s effectiveness and alignment with operational goals. Here is a step-by-step guide on how to implement a barcoding system in manufacturing.
Step 1: Assess Needs and Define Objectives
Begin by thoroughly analysing your current processes to identify areas where a barcode system can introduce improvements. Determine specific objectives such as increasing inventory accuracy, enhancing traceability, or streamlining production workflows.
Engage with people across departments to gather insights and define clear, measurable goals for the barcode implementation.
Step 2: Select Appropriate Barcode Symbologies and Equipment
Choose the barcode symbologies that best suit your product types, packaging, and information requirements. Then, based on the needs assessment, select the necessary equipment — scanners, printers, labels, ribbons, and computing devices — ensuring compatibility with the chosen symbologies and your operational environment.
Step 3: Design and Test Barcode Labels
Utilise barcode design software to create labels that meet your informational and regulatory needs while being easily scannable. Design labels with consideration for size, contrast, and placement on the product or packaging to ensure optimal readability.
Conduct testing in various operational conditions to validate the design’s effectiveness before full-scale production.
Step 4: Develop Integration and Data Management Plan
Outline how barcode data will integrate with your existing IT infrastructure, including inventory management, ERP, and SCM systems. Plan for data capture, storage, and analysis processes, ensuring security and compliance standards are met.
This step may involve customising software interfaces or developing middleware to facilitate seamless data flow.
Step 5: Applying Labels to Physical Items
After designing and testing barcode labels, the next crucial step involves systematically applying these labels to your products, components, or assets. This process requires careful planning to ensure labels are placed in positions that are both easily accessible for scanning and secure enough to remain attached throughout the product’s lifecycle.
Consider the following:
- Label Placement: Determine optimal placement for labels on each item, considering factors such as exposure to wear and tear, environmental conditions, and ease of scanning during various stages of handling and processing.
- Application Method: Depending on the volume of items and the nature of your operations, decide whether to apply labels manually or automate the process using label applicators or label dispensers. For high-volume environments, automated applicators can significantly increase efficiency and consistency.
- Quality Assurance: Implement a quality control procedure to check the legibility and adherence of labels after application. This step is crucial to prevent scanning issues arising from poorly applied labels.
- Record-Keeping: Ensure that the application of labels is logged and tracked within your management system software. This record-keeping supports traceability and inventory control, allowing for easy updates and audits.
Following these detailed steps ensures a comprehensive approach to implementing a barcode system, improving efficiency, accuracy, and decision-making within manufacturing operations.
The Bottom Line
The adoption of barcode systems in manufacturing heralds a significant shift towards more efficient, accurate, and responsive operations. From streamlining inventory management to enhancing traceability and compliance, barcode technology offers a suite of benefits that can transform the manufacturing landscape.
This guide has detailed essential steps and considerations for implementing barcode systems, from equipment selection to deployment, providing a blueprint for manufacturers to leverage this technology effectively. As the industry moves forward, the strategic adoption of barcode systems will be crucial in achieving operational excellence and meeting the increasing demands of production and supply chain management.
Thanks for reading!
Frequently Asked Questions
What Are the Benefits of Using Barcodes in Manufacturing?
The adoption of barcode technology in manufacturing offers numerous benefits, including:
- Enhanced Efficiency: Automates data collection and entry, speeding up processes and reducing manual labour.
- Improved Accuracy: Minimises human errors in inventory management and data recording, ensuring accurate tracking of materials and products.
- Increased Traceability: Allows for detailed tracking of products through the manufacturing process and supply chain, facilitating easier recalls and compliance with regulations.
- Cost Savings: Reduces operational costs by optimising inventory management and reducing errors and associated rework.
- Seamless Integration: Easily integrates with existing manufacturing and inventory management systems, enhancing data flow and accessibility.
What Are the Best Practices for Barcoding in Manufacturing?
Implementing barcoding in manufacturing effectively requires adherence to best practices, such as:
- Comprehensive Planning: Evaluate your operational needs and objectives to choose suitable barcode types and equipment.
- Quality Equipment Selection: Invest in reliable scanning and printing equipment that matches your manufacturing environment and volume needs.
- Effective Training: Ensure staff are adequately trained on barcode system usage, from scanning to data management.
- Regular Maintenance: Maintain equipment and update software regularly to ensure the system’s reliability and accuracy.
- Data Security Measures: Implement robust data security protocols to protect sensitive information captured and stored by the barcode system.
- Continuous Evaluation: Regularly assess the barcode system’s performance and adjust to address new challenges or improve efficiency.