Effective inventory management is a cornerstone of operational success for businesses across various industries. Central to this process are inventory tags, essential tools that provide a reliable means to track, manage, and optimise stock levels.
As the lifeline of order and efficiency, these tags serve as identifiers and critical components in a larger operational excellence system. They bridge the gap between physical inventory and digital data, ensuring that every item is accounted for from arrival to final sale. Their role extends beyond mere tracking; they are pivotal in forecasting, decision-making, and enhancing customer satisfaction.
In an era where speed and accuracy dictate market leadership, inventory tags stand out as silent sentinels, guarding against the chaos of mismanagement and loss. This guide aims to demystify inventory tags, comprehensively understanding their types, importance, and application.
Without further ado, let’s get started.
What is an Inventory Tag?
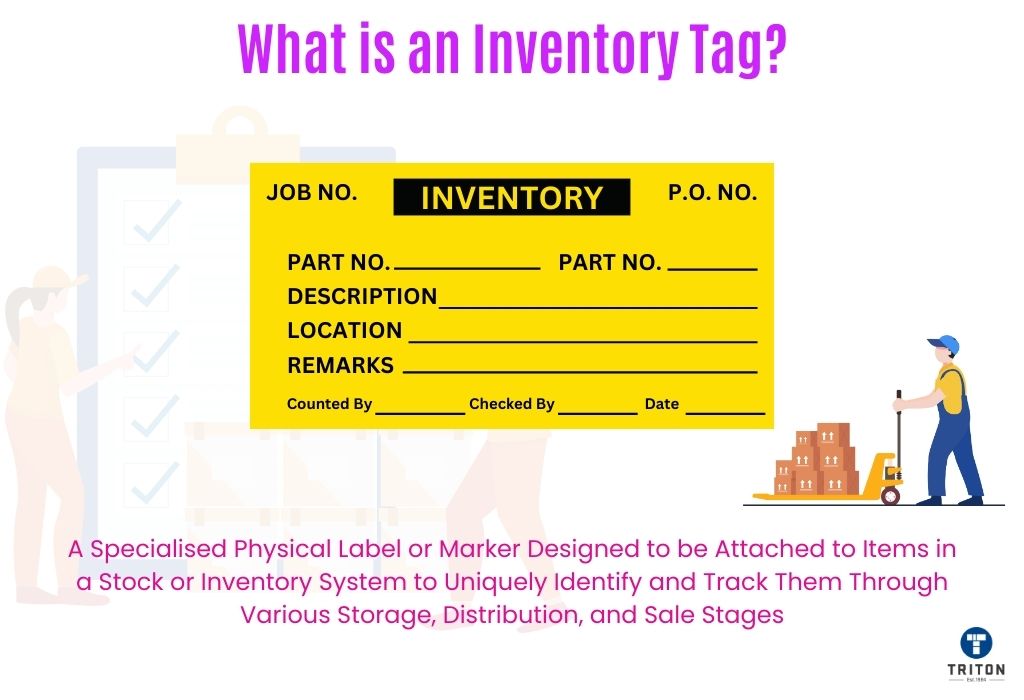
An inventory tag is a specialised physical label or marker designed to be attached to items in a stock or inventory system to uniquely identify and track them through various storage, distribution, and sale stages. The primary purpose of an inventory tag is to maintain a reliable link between the physical item and its digital record in an inventory management system.
Each inventory tag carries a unique code, often in the form of a barcode, QR code, or RFID chip, that can be read and interpreted by inventory management systems. This code is distinct to each item or batch, ensuring that no two items share the same identifier, which is crucial for precise tracking and inventory control.
Did you know that barcodes and QR codes are often mistaken for being the same but are actually two different technologies? Explore our guide on QR Code vs Barcode to learn more about their differences.
Beyond mere identification, these tags can store a wealth of information, including the item’s origin, product names, SKUs, product descriptions, batch number, production date, expiration date, and any other relevant data. SKUs also play a crucial role in inventory management, and to learn more about them, refer to our detailed article What is a SKU?
By providing an unambiguous way to identify each item in an inventory, inventory tag labels form the backbone of efficient inventory management. They act as a critical nexus point, bridging the tangible world of physical inventory with the intangible realm of data and analytics, enabling businesses to maintain accurate and efficient control over their stock.
Why are Inventory Tags Important? - The Benefits of Inventory Tags
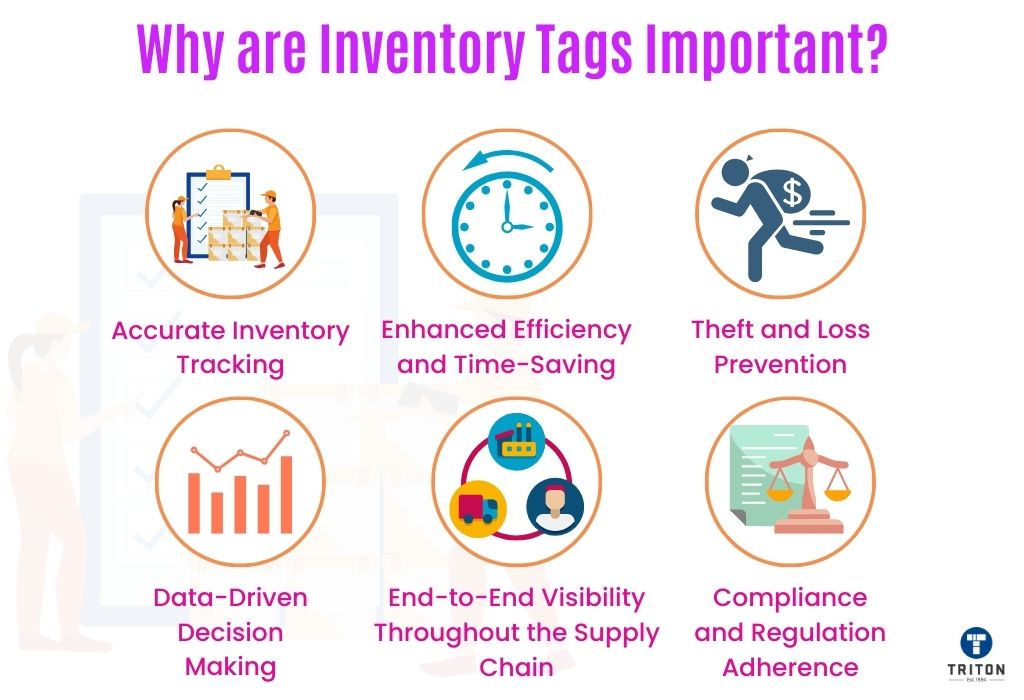
The importance of inventory tags spans across various aspects of business operations, offering benefits that significantly enhance efficiency, accuracy, and decision-making. Let’s take a look at the advantages of inventory tags.
Accurate Inventory Tracking
The primary benefit of inventory tags is their ability to facilitate precise tracking of every item in the inventory. With unique identifiers, businesses can monitor the movement and status of each item, reducing errors and discrepancies.
This level of accuracy is crucial for maintaining up-to-date stock levels, preventing overstocking or stockouts, and ensuring that inventory records reflect the true state of the warehouse or sales floor.
Enhanced Efficiency and Time-Saving
Inventory tags streamline the process of managing stock. By automating the tracking process, they significantly reduce the time and labour traditionally required for manual inventory counts.
Employees can quickly scan tags to update or retrieve information, allowing faster operations and freeing time to focus on other critical tasks. This efficiency extends to various processes, including receiving, storing, picking, and shipping items.
Theft and Loss Prevention
Inventory tags act as a deterrent to theft and help in quickly identifying any missing items. With each item tagged and accounted for, spotting discrepancies and investigating issues becomes easier.
In environments where theft or loss is a concern, inventory tags can be a powerful tool in maintaining stock integrity.
Data-Driven Decision Making
The wealth of information provided by inventory tags allows businesses to make informed decisions. By analysing data collected from tags, such as sales trends, stock movement, and product life cycles, managers can forecast demand, optimise stock levels, and plan for future purchases more effectively. This data-driven approach leads to more intelligent, more strategic decision-making.
End-to-End Visibility Throughout the Supply Chain
Inventory tags provide end-to-end visibility throughout the supply chain, from the manufacturer to the end consumer. This visibility is vital for tracking the progress of items, managing supply chain logistics, and responding quickly to any issues that arise. It gives businesses a comprehensive view of their inventory’s journey, enhancing control and responsiveness at every stage.
Compliance and Regulation Adherence
Maintaining accurate inventory records is a regulatory requirement in many industries. Inventory tags help businesses adhere to industry standards and legal requirements by providing a clear, auditable trail of inventory movement and history. This is particularly crucial in pharmaceuticals, food and beverage, and aerospace sectors, where inventory accuracy can have significant safety and legal implications.
Types of Inventory Tags
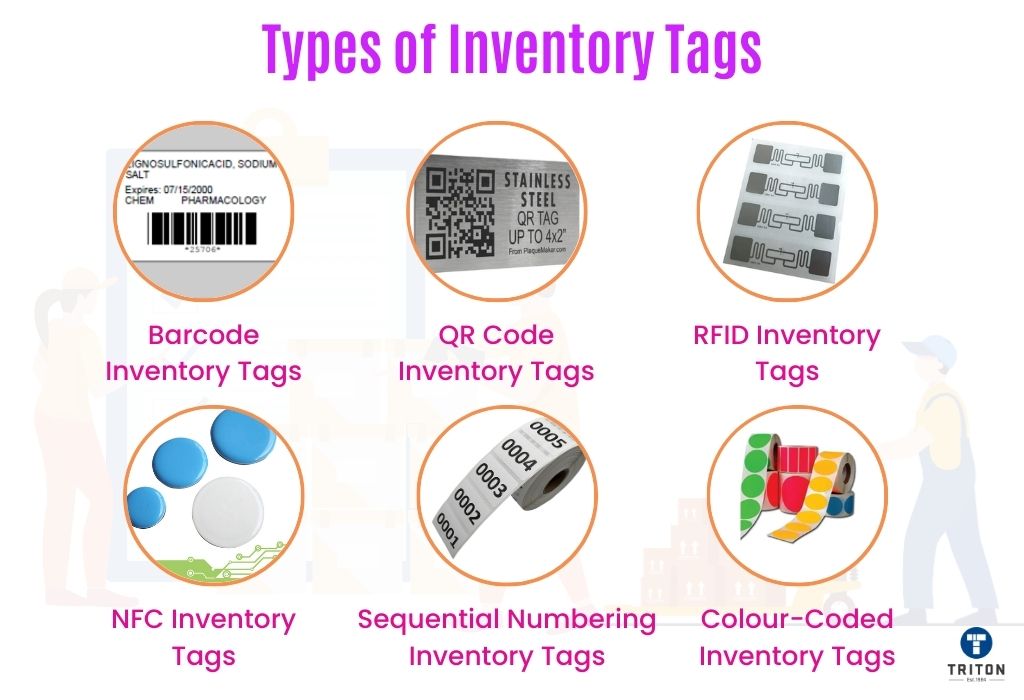
Inventory tags come in various forms, each suited to different needs and environments. Understanding the types of tags available is crucial for selecting the right one for your inventory management system. Here’s a look at the most common types of inventory tags:
Barcode Inventory Tags
Barcode tags are one of the most widely used inventory tagging systems. They consist of a series of vertical lines of varying widths representing numbers and other characters. These tags are scanned using a barcode scanner, translating the barcode into a readable format.
Barcode tags are ubiquitous in retail, warehousing, and distribution. They are ideal for environments where simple, cost-effective tracking is required.
To gain a deeper understanding of barcoding technology, we encourage you to explore our informative guides:
- Barcode 101: An introductory guide to the world of barcodes for beginners.
- Barcode Types: Discover various barcode symbologies and their applications.
- Discrete vs Continuous Barcodes: A comparative guide outlining the distinctions between 1D barcodes.
- 2D Stacked Barcodes vs 2D Matrix Barcodes: Examine the differences between different 2D barcode technologies.
For even more comprehensive knowledge about barcodes, please visit our dedicated Barcode Learning Centre.
QR Code Inventory Tags
QR codes are a type of two-dimensional barcode that can hold a significant amount of data compared to traditional barcodes. They can be scanned using smartphones and other camera-equipped devices, making them highly accessible.
QR code tags are used in various industries, including retail, marketing, and event management, where additional information like URLs, images, or text needs to be embedded within the tag.
If you’re contemplating the incorporation of QR codes into your inventory tag labels, our collection of guides offers valuable insights:
- What is a QR Code: A comprehensive guide explaining QR codes.
- How QR Codes Work: A detailed exploration of the inner workings of QR codes.
- QR Code Test: Guidelines to ensure the functionality and readability of your QR codes.
- QR Code Size: Understanding the ideal dimensions for various QR code applications.
- QR Code Alternatives: Exploring alternative technologies that may better suit your requirements.
- QR Code Best Practices: Essential guidelines to enhance the effectiveness of your QR code usage.
RFID Inventory Tags
RFID (Radio-Frequency Identification) tags use electromagnetic fields to automatically identify and track tags attached to objects. These tags can hold a wide range of information and can be read from several feet away, even without a direct line of sight.
RFID tags are prevalent in supply chain management, asset tracking, and access control. They are particularly useful in environments where quick, multiple-tag readings are necessary.
To delve deeper into RFID technology and its applications, we invite you to explore our comprehensive guides:
- What are RFID Tags?: Discover the various types of RFID tags and their applications for real-time tracking and data collection.
- QR Code vs RFID: Compare QR codes with RFID technology to determine which suits your company’s needs best.
- RFID vs Barcode: Contrast RFID with traditional barcodes to make informed decisions regarding technology adoption.
- What are RFID Printers?: Investigate the role of RFID printers in creating effective tracking and inventory management RFID tags
NFC Inventory Tags
NFC (Near Field Communication) tags are a subset of RFID technology. They allow two-way communication between the tag and the reader device when they are in close proximity, typically a few centimetres.
NFC tags are less common and usually used in interactive marketing and secure access controls.
Sequential Numbering Inventory Tags
Sequential numbering tags are simple tags that feature a unique number sequence. They don’t contain any encoded data but provide a straightforward way to identify and track items manually.
Sequential numbering tags are often used in quality control, repair services, and any situation where simple, manual tracking is sufficient.
Colour-Coded Inventory Tags
Colour-coded tags use colours to categorise and prioritise items. They are often used in conjunction with other tagging systems to provide at-a-glance information.
These tags are useful in warehouses, libraries, and retail environments where quick visual identification is beneficial.
Each type of inventory tag has its unique features and applications. The choice of tag depends on various factors, including the nature of the items being tracked, the environment they’re in, and the level of detail required for tracking. Understanding these options allows businesses to tailor their inventory management system to their specific needs, enhancing efficiency and accuracy.
How to Use Inventory Tags Effectively?
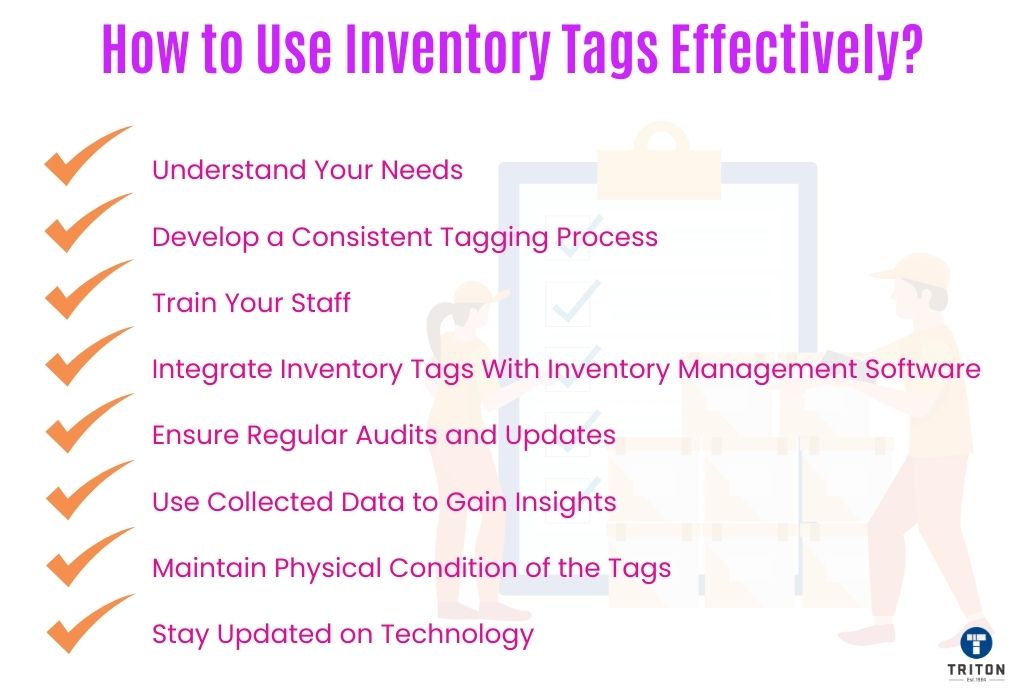
Implementing inventory tags is more than just attaching labels to items; it’s about integrating a system that enhances the accuracy, efficiency, and reliability of inventory management. Here’s how businesses can use inventory tags effectively:
Understand Your Needs
Before selecting a type of inventory tag, assess your business’s specific needs. Consider factors such as the size of your inventory, the complexity of your supply chain, the environment in which your items are stored and handled, and the level of detail you need to track inventory. This understanding will guide you in choosing the most suitable type of tag.
Consistent Tagging Process
Develop a standardised process for tagging items. This should include guidelines on what information to include and where and how tags should be placed, ensuring they are easily accessible and readable. Consistency in tagging ensures that all items are accounted for, and the system remains reliable.
Train Your Staff
Ensure that all staff members involved in inventory management are trained on how to use the tags and the related scanning equipment. They should understand the importance of the system and how to troubleshoot common issues. Proper training minimises errors and maximises the system’s effectiveness.
Integrate with Inventory Management Software
Inventory tags are most effective when integrated with inventory management software. This software can automatically update inventory levels as items are scanned, provide detailed reports, and alert you to issues like low stock or discrepancies. Ensure your tags are compatible with your software and that the system is set up to leverage the full capabilities of the tags.
Regular Audits and Updates
Even with an effective tagging system, regular audits are crucial. Periodically check your inventory to ensure all items are tagged correctly, and the data matches your physical stock. Update your tags as needed, especially if items are moved, sold, or disposed of.
Leverage Data for Insights
Use the data collected from your inventory tags to gain insights into your inventory management. Analyse trends, identify fast-moving items and understand seasonal variations. This data can inform your purchasing decisions, help optimise stock levels, and improve your overall inventory strategy.
Maintain Your Tags
Ensure that your tags remain in good condition and are always legible. Replace any damaged or worn-out tags promptly. For technology-based tags like RFID or NFC, perform regular checks to ensure they function correctly.
Stay Updated on Technology
Inventory management technology is continually evolving. Stay informed about new types of tags, software updates, and best practices. Being adaptable and open to innovation can further improve your inventory management system.
How to Create an Inventory Tag
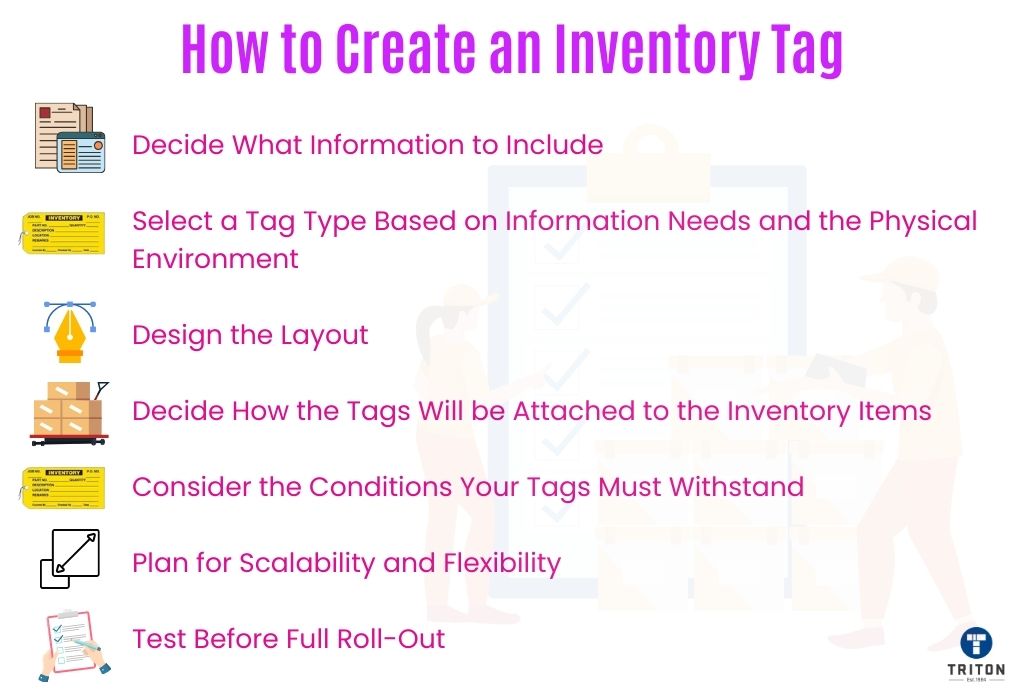
Creating an inventory tag involves several steps, from conceptualising the design to selecting materials and deciding on the technology to be used. Here’s a comprehensive guide to creating an inventory tag that meets your business requirements:
Determine the Information to Include
Start by deciding what information is crucial for your inventory management. Common details include unique identification numbers, product names, SKUs, and barcodes or QR codes. For more advanced systems, consider RFID chips. Consider the level of detail required and the ease of access to this information when scanned.
Tip: Create a hierarchy of information, placing the most critical details in the most prominent position on the tag.
Choose the Tag Type
Select a tag type based on your information needs and the physical environment where the tags will be used. Options include barcode tags, QR code tags, RFID tags, and NFC tags. Each has its advantages and suitability for different environments and purposes.
Tip: Consider using dual-technology tags (e.g., barcode and RFID) if your environment or processes vary significantly.
Design the Layout
Design the tag’s layout, ensuring it’s clear, readable, and accessible. If using barcodes or QR codes, ensure they comply with standards and are scannable. The design should also consider the size of the tags and how they will be attached to the inventory items.
Tip: Use contrasting colours and avoid cluttering the tag with too much information. Test the design under different lighting conditions and distances to ensure readability.
Consider the Attachment Method
Decide how the tags will be attached to the inventory items. Options include adhesive, ties, or sleeves.
Tip: For items handled frequently or in harsh environments, consider more durable attachment methods like metal ties or protective sleeves.
Factor in Environmental Conditions
Consider the conditions your tags must withstand, such as temperature extremes, moisture, chemicals, or rough handling. Use materials and protective coatings proven to withstand your specific environmental conditions.
Plan for Scalability and Flexibility
Your tagging system should be able to grow and adapt to your business. Design tags with future expansions in mind, such as additional fields or technology upgrades.
User-Friendly Design
Remember that your staff will be interacting with these tags daily. Involve end-users in the design process to get feedback on what works best for them regarding tag size, readability, and ease of scanning.
Test Before Full Roll-Out
Create prototypes of your tags and test them in real-life scenarios. Conduct a pilot program in one area of your inventory or with a small group of users before fully implementing the new tags.
Simplify Inventory Tag Creation with BarTender
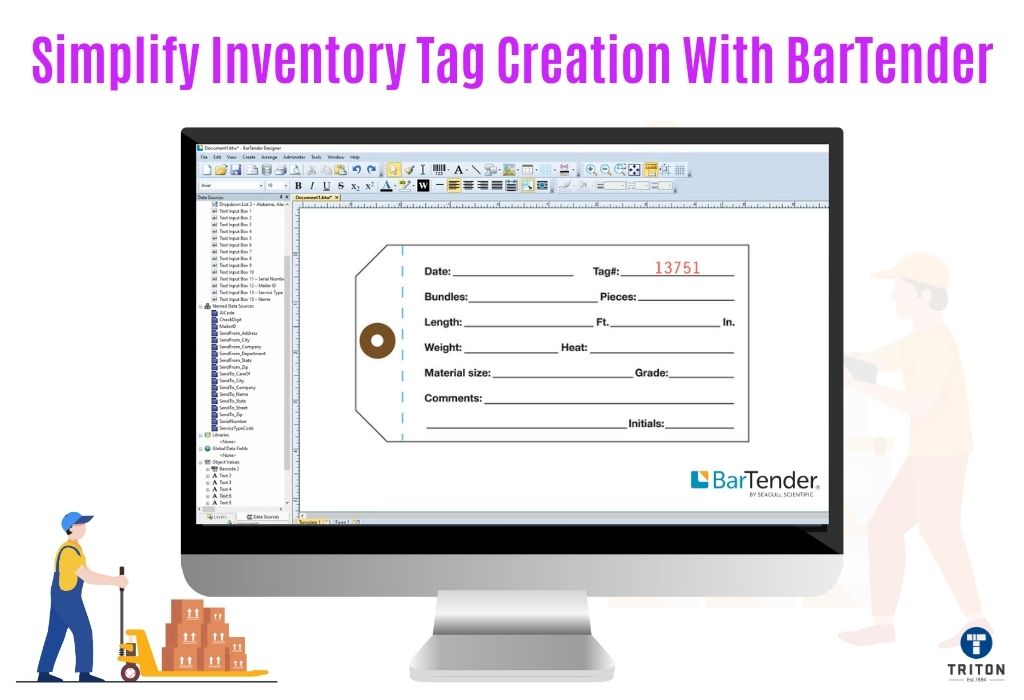
Creating effective inventory tags can be streamlined and simplified using the right tools. To facilitate this process, we at Triton Store recommend the industry-leading solution: Seagull Scientific’s BarTender Software. More than just a tool, BarTender is a comprehensive solution that transforms how businesses design and print their inventory tags.
BarTender sets itself apart with its robust label design capabilities. Whether you’re looking to include images, texts, barcodes, or RFID tags, BarTender does it all. Its intuitive interface and range of customisable templates, such as Inventory Stock labels, Inventory Location labels, and general Inventory labels, make professional tagging accessible to all.
A standout feature of BarTender is its seamless integration with nearly any database or business system. This integration allows you to effortlessly import product information, SKUs, and other vital data into your tag designs, ensuring accuracy and consistency across your inventory. Additionally, the software supports “smart” labels, which automatically update with changing data like expiration dates or lot numbers, significantly simplifying the label management process.
Triton Store offers all four editions of BarTender: Starter Edition, Professional Edition, Automation Edition and Enterprise Edition, each designed to meet varying levels of labelling complexity and automation requirements. BarTender Cloud introduces remote management capabilities for businesses looking for modern solutions, allowing you to manage label printing and design operations from anywhere.
For businesses aiming to modernise their label management, BarTender Cloud emerges as the latest innovation in the field. With BarTender Cloud, you gain the flexibility to design, manage, and print your inventory tags from anywhere, at any time, ensuring that your operations are as agile and adaptable as your market demands.
For a detailed comparison of how BarTender Cloud stands up against the traditional on-premise BarTender solution, we invite you to explore our in-depth guide: BarTender Cloud vs BarTender Software.
Choosing BarTender from Triton Store isn’t just about getting software; it’s about securing a comprehensive solution for your labelling and inventory management needs. With BarTender’s flexibility, robust security features, and support, your business can enhance its efficiency and effectiveness.
To explore how BarTender can revolutionise your label printing experience, connect with us via the live chat widget below or delve into the software’s capabilities through our informative article: What is BarTender Software?
How to Print an Inventory Tag?
Printing inventory tags is a crucial component of effective inventory management. The right printer can make all the difference in the quality, durability, and readability of your tags. Here’s a comprehensive guide on printing inventory tags, including factors to consider when choosing a printer.
Factors to Consider When Choosing a Printer
- Print Volume: Assess the number of tags you’ll need to print regularly. High-volume environments require industrial printers, while smaller operations will find desktop printers sufficient.
- Type of Inventory Label Printed: The type of printer you need depends on the kind of tags you’re printing. For basic barcode and QR code tags, a standard label printer might suffice. For more durable or specialised tags, such as those with RFID capabilities, you require a more robust industrial printer.
- Tag Material: Determine the type of material you’ll be printing on. Different printers accommodate different materials, from standard paper to durable synthetic options.
- Environment: The environment where the printer will be used can affect its performance and longevity. Industrial environments require printers to withstand dust, moisture, and temperature fluctuations.
- Print Resolution: Always choose high-resolution printers, which are essential for creating clear, scannable barcodes and detailed graphics. Look for at least 203 DPI print-resolution printers.
- Connectivity Options: Look for printers that easily integrate with your existing systems and offer connectivity options like USB, Ethernet, Wi-Fi, or Bluetooth for seamless operation.
- Ease of Use: User-friendly printers with intuitive interfaces reduce training time and increase productivity. Therefore, look for printers with displays and buttons.
Printing Your Tags
Once you’ve selected the right printer, follow these steps to ensure high-quality, reliable tags:
- Design with Detail: Use software like BarTender to design your tags. Ensure all necessary information is included and that barcodes or RFID elements are correctly formatted and placed. The design should be clear, readable, and scannable, with enough contrast between the text (or codes) and the tag background.
- Conduct a Test Run: Before printing the entire batch, do a test print to check the quality. Check for readability, scan the barcodes or RFID tags to ensure they work correctly, and make sure the tag adheres well to the item’s surface. This step helps avoid costly mistakes and wasted materials. Adjust the printer settings if necessary.
- Monitor the Print Quality: As you print your tags, periodically check the quality to ensure consistency. Look out for any signs of smudging, fading, or misalignment.
Thermal printers are often the preferred choice for printing inventory tags, particularly when it comes to barcode and QR code tags. They are renowned for producing sharp, high-contrast images crucial for accurate barcode scanning.
Not only are thermal printers fast and ideal for handling large volumes, but they also operate without ink or toners. Instead, they use labels and ribbons, significantly reducing the cost per label over time, which is especially beneficial for businesses with extensive printing needs. To learn how a thermal printer works, refer to our guide – How Does a Thermal Printer Work?
At Triton Store, we recognise the critical role of reliable and efficient tag printing in inventory management. That’s why we offer an extensive selection of thermal printers, consumables, and accessories designed to elevate your label printing process. Our collection features top-tier models from industry-leading brands such as Epson, Element, Senor, Honeywell, Zebra, and TSC and colour label printers from OKI, ensuring a fit for every business requirement.
Our inventory spans various types of thermal printers, including industrial printers, desktop printers, direct thermal printers, thermal transfer printers, barcode label printers, mobile printers, and receipt printers. This diversity ensures that every business can find the right tool for their operations.
To complement our printers, we provide an extensive range of essential accessories and high-quality thermal printheads from trusted brands like Zebra, Honeywell, TSC, Intermec, Datamax, SATO, and Bizerba. These accessories, including spare printer parts and accessories, waterproof printer enclosures, cables and cleaning wipes, are all curated to enhance and streamline your printing experience.
We also offer a wide selection of thermal printer consumables, catering to a broad spectrum of shipping and labelling needs. From thermal transfer ribbons and thermal labels to thermal carton labels, thermal carcase tags, food-compliant thermal inserts, receipt rolls and shipping & freight labels, each product is selected for its reliability and quality, ensuring your business’s operations run smoothly.
At Triton, we understand that every business is unique. Beyond providing products, we offer customised solutions and expert support to help you choose the ideal printer and accessories for your specific needs. Our team is dedicated to enhancing your printing and labelling efficiency, ensuring you maximise your investment.
Explore our extensive collection and connect with our professionals via the live chat widget for personalised assistance. Let Triton Store be your partner in achieving enhanced efficiency and quality in all your printing and labelling endeavours.
Best Practices for Inventory Tagging
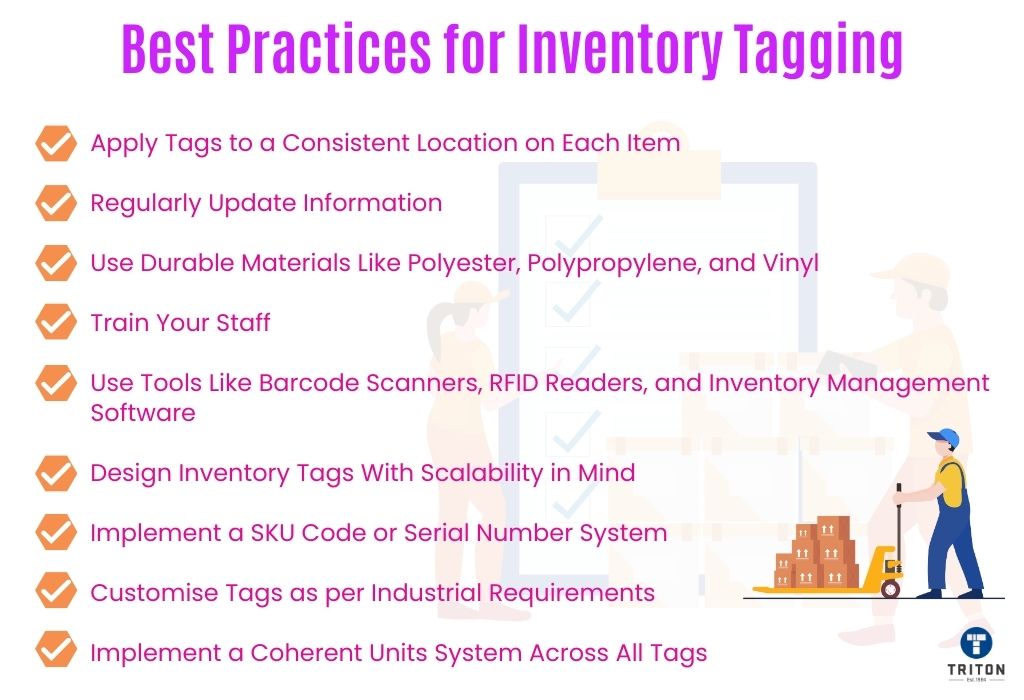
Effective inventory tagging is crucial for accurate and efficient inventory management. Here’s how to implement a system that enhances your inventory’s accuracy, efficiency, and traceability.
Consistent Placement
Apply tags to a consistent location on each item, considering accessibility, visibility, and lighting conditions. Choose a spot that’s easily accessible, visible under various lighting conditions, and where the tag remains unobstructed.
Consistent placement ensures that staff can quickly locate and scan tags, significantly reducing the time and effort required for inventory processes.
Regularly Update Information
Keep the information such as price, batch number, or expiration date change on your inventory tags up-to-date.
Regular updates prevent discrepancies between your physical inventory and database records. Implementing a system that automatically reflects updates on the tags, such as with “smart” labels in a digital system, can greatly enhance accuracy and efficiency.
The frequency of updates will depend on factors such as sales velocity, seasonality, and product lifecycle. For instance, perishable goods might require more frequent updates than non-perishable items.
Use Durable Materials
Select materials for your tags that can withstand the conditions they’ll be exposed to. For items in cold storage, use freeze-resistant labels; for outdoor items, choose UV-resistant materials. Durable tags like polyester, polypropylene, and vinyl, often with protective laminates, remain legible and intact over time, ensuring that your inventory remains correctly identified and trackable.
Train Your Staff
Ensure that all staff members involved in inventory management are trained on the tagging system. They should understand how to read and apply tags, as well as how to update and scan them.
Proper training reduces errors and ensures that everyone is proficient in using the tags as intended. Regular refresher courses can also help to keep everyone up-to-date on any changes or new technologies.
Leverage Technology
Utilise technology to enhance your tagging system. Tools like barcode scanners, RFID readers, and inventory management software can streamline applying, updating, and tracking tags. These technologies can also provide valuable data and insights, helping you to better understand and manage your inventory.
Triton offers a wide range of top-notch barcode scanning solutions from reputable brands such as Zebra and Honeywell for those seeking to elevate their barcode scanning capabilities.
Our comprehensive inventory features various barcode scanner models, such as mobile terminals, general-purpose barcode scanners, rugged barcode scanners, fixed scanners & sensors, USB barcode scanners, wireless barcode scanners, 2D barcode scanners, and Bluetooth barcode scanners. This diverse selection ensures that we can meet a wide range of operational needs, enhancing efficiency and accuracy in your inventory management.
But our commitment doesn’t end with scanners. At Triton, we’re dedicated to providing excellence in all aspects. We offer a carefully curated range of essential barcode scanner accessories and spare parts and cables to ensure that your equipment always performs at its best.
When you choose Triton, you’re not just selecting a product; you’re choosing a partner committed to quality and support. Engage with our experts via the live chat widget for personalised assistance and discover how our barcode scanning solutions can transform your inventory management.
Plan for Scalability
Design your inventory tagging system with scalability in mind. As your business grows, your inventory system should be able to accommodate increased volume and complexity. This involves choosing tags and technologies that can be easily expanded or updated and creating scalable procedures.
Use SKU Codes or a Serial Number System
Implement a system using SKU codes or serial numbers for unique identification. SKU codes are ideal for tracking product types at a glance, while serial numbers provide individual item tracking. This system enhances the accuracy of inventory tracking, aids in forecasting, and simplifies the process of stocktaking and order fulfilment.
For a deeper understanding of how SKU codes can transform your inventory management and contribute to a more efficient and profitable operation, consider reading this detailed article – What is a SKU?
Customisation for Specific Industries
Tailor your tags to meet the specific needs of your industry. For example, in healthcare, tags might need to be sterilisable, while in retail, they might need to include security features. Understanding and addressing your industry’s unique challenges and requirements ensures that your tagging system is as effective and compliant as possible.
Implement a Coherent Units System
Establish a coherent system for units of measure across all tags. Unit consistency helps avoid confusion and errors in stock levels and order, whether you’re using pieces, pounds, or pallets. This is particularly important for businesses dealing with diverse products or international operations.
FAQs on Inventory Tagging
What is an Inventory Tagging System?
An inventory tagging system is a method used to track and manage items within a business’s inventory. It involves attaching tags, usually with unique identifiers like barcodes or RFID chips, to each item or batch. These tags interact with inventory management software to provide real-time data on stock levels, location, and movement, enhancing the accuracy and efficiency of inventory control.
What are the Benefits of Using RFID Tags over Barcodes?
RFID tags offer several advantages over traditional barcodes. They can be read without a direct line of sight and from a greater distance, allowing faster and more efficient scanning.
RFID tags can store more inventory data and be updated with new information. They’re particularly beneficial in environments requiring quick, bulk reading of items, such as supply chain management and large retail operations.
What are Inventory Count Tags?
Inventory count tags are specific labels used during physical inventory counting to ensure accuracy and accountability. They typically include information like item descriptions, quantities, and location. As items are counted, details are recorded on these tags, which are then used to update inventory records, verify accuracy, and identify discrepancies.
How Do You Label Inventory Racks?
Labelling inventory racks involves placing clear, durable labels at each rack position. These labels usually include a unique identifier, often a barcode or alphanumeric code, indicating the specific section and shelf. The labels should be positioned at a consistent, easily visible height and angle. This system helps quickly locate items and maintain an organised warehouse or storage area.
These guides will prove invaluable if you’re seeking assistance with labelling your warehouse effectively.
- Types of Warehouse Labels: An exploration of various warehouse label types.
- Warehouse Rack Labelling Best Practices: Tips and practices for effective rack labelling in warehouses.
- The Ultimate Guide to Warehouse Signs: A comprehensive guide covering everything you need to know about warehouse signs.
- How to Choose Warehouse Labels: Insights on selecting the right warehouse labels for your needs.
How Often Should Inventory Tags Be Updated?
Inventory tags should be updated whenever there’s a significant change to the item, such as movement, sale, or adjustment in quantity or status. The frequency can vary based on factors like sales velocity, item type, and industry practices. High-turnover items may require daily updates, while less frequently moved items might be updated weekly or monthly.
Final Thoughts
In conclusion, inventory tags are more than mere labels; they are the linchpins of efficient inventory asset management, offering accuracy, control, and insight into every aspect of stock handling. From the simple barcode to sophisticated RFID tags, the right tagging strategy can transform your inventory management from a challenging task into a streamlined, data-driven process.
By understanding the various types of tags, implementing best practices, and leveraging the latest technology, businesses can keep track of their inventory in real-time and make informed decisions that drive growth and efficiency.
As we’ve explored, the world of inventory tags is vast and varied, and with the right approach, the benefits are substantial. Embrace the power of effective inventory tagging, and watch as it brings organisation, clarity, and success to your business operations.
We hope this article was useful.
Thanks for reading!